Core Materials
Core materials play a pivotal role in composite manufacturing, serving as the central layer sandwiched between layers of reinforcement material to form a composite structure. These materials are crucial for providing thickness and rigidity to composite panels without significantly increasing weight. Core materials are selected for their ability to improve the mechanical properties of composites, including their strength, stiffness, and impact resistance. By incorporating materials, manufacturers can create lightweight structures with high strength-to-weight ratios, essential for high-performance applications in industries such as aerospace, automotive, and marine.
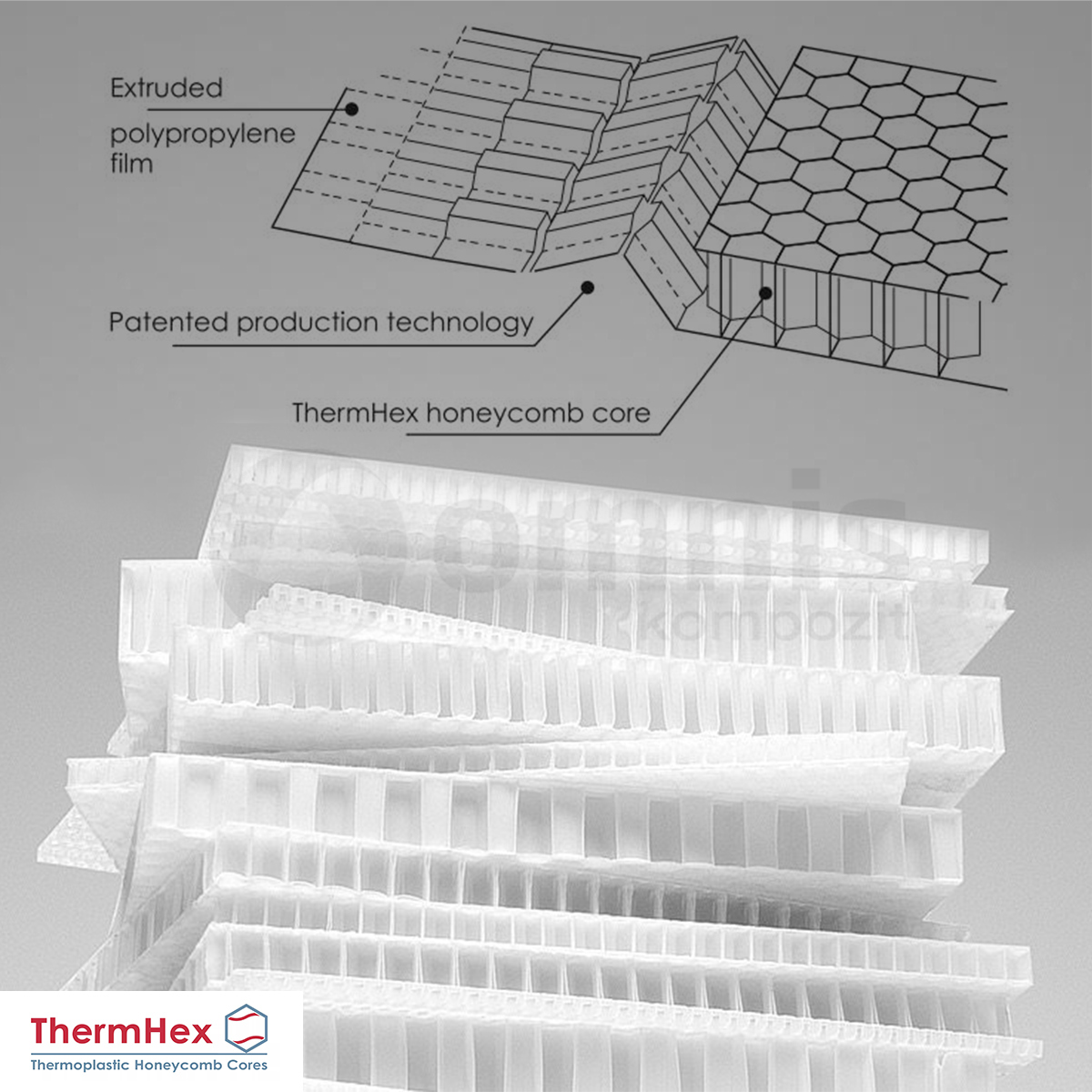
PP Honeycomb-Honeycomb Plate
Review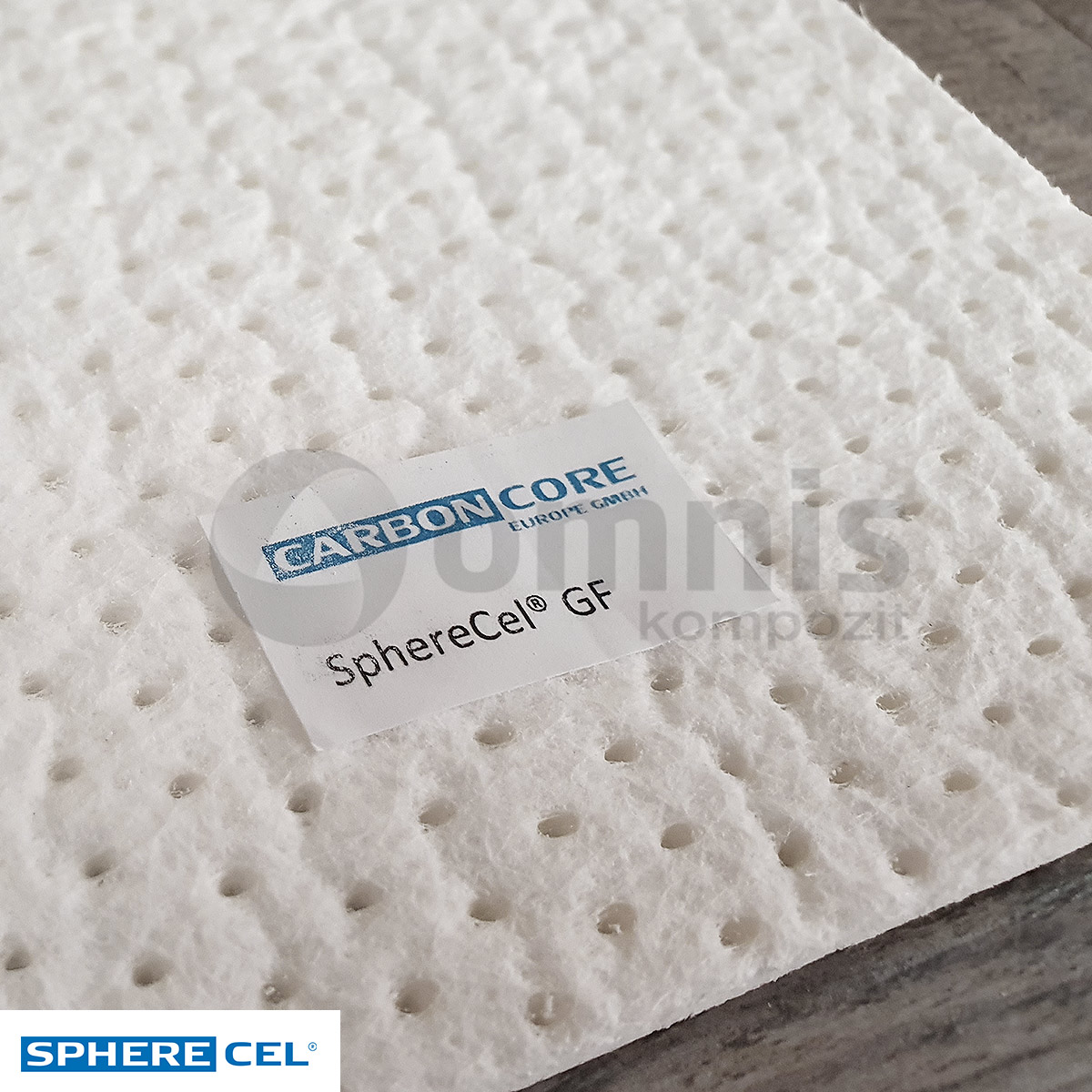
SphereCel GF Nonwoven Glass Fiber Core Felt
Review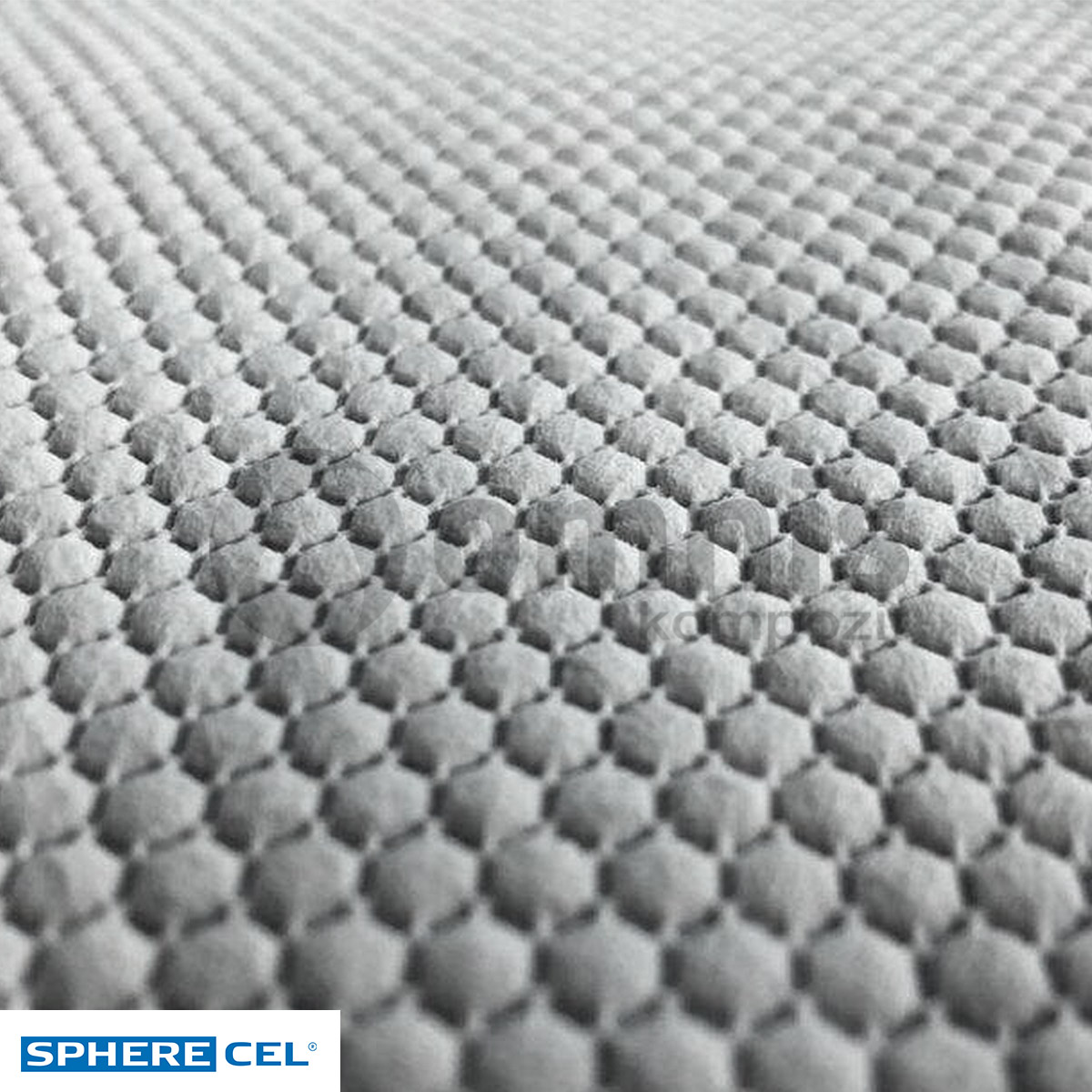
SphereCel PE Nonwoven Polyester Core Felt
Review
SphereCel SBF Sewn Glass Fiber Core Felt
Review
SphereCel PrintBlock Nonwoven Glass Fiber Core Felt
Review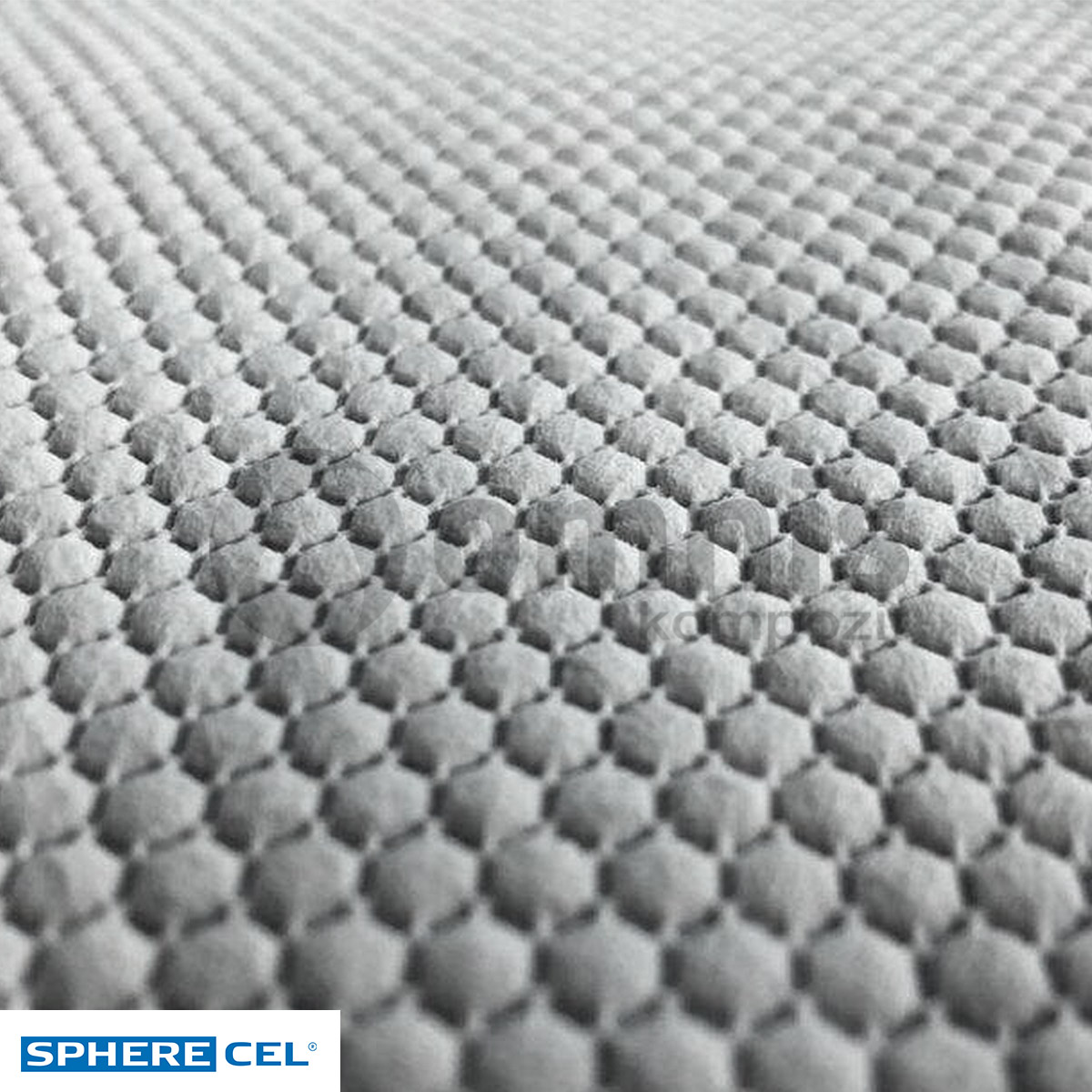
SphereCel HX-OM-CM Nonwoven Honeycomb Polyester Core Felt
Review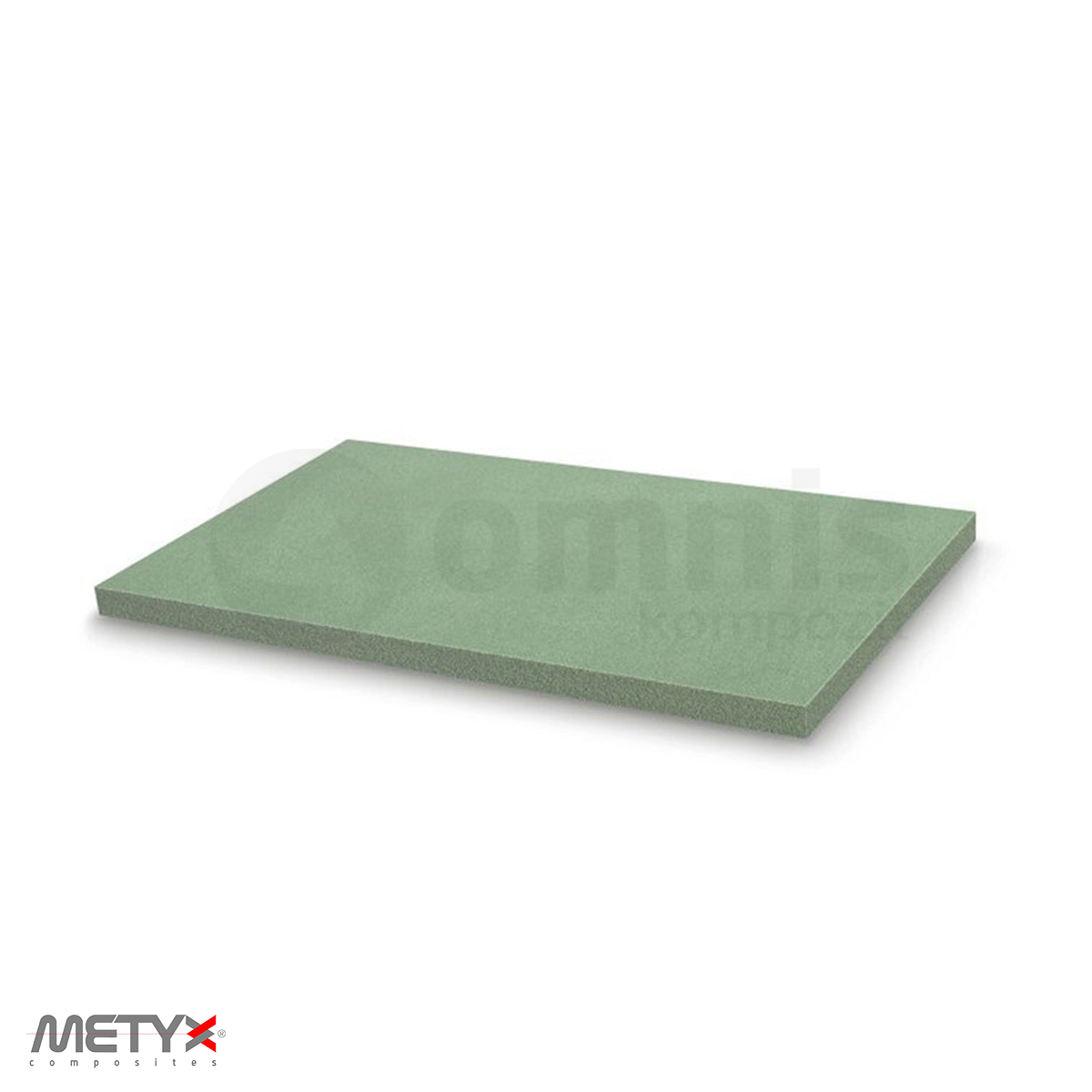
PVC Foam Plate
ReviewHow do core materials enhance the properties of composites?
Core materials enhance the properties of composites by significantly increasing the laminate’s stiffness and bending strength while adding minimal weight. They work by creating a larger distance between the composite’s outer skins, which dramatically increases the moment of inertia, leading to greater resistance to bending and deformation. This structural efficiency allows for the design of lighter, more energy-efficient vehicles and structures. Additionally, these materials can improve thermal and acoustic insulation properties, contributing to more comfortable and efficient operational environments. Their use is a key factor in the advanced performance of modern composite structures.
What are the main types of core materials available?
The main types of materials available for composite manufacturing include foam cores, honeycomb cores, and balsa wood cores, each offering unique properties and advantages. Foam cores, made from materials such as PVC, PET, or polystyrene, provide excellent strength-to-weight ratios and are easy to shape and process. Honeycomb cores, typically made from aluminum, aramid fiber, or thermoplastic materials, offer exceptional stiffness and low density, making them ideal for aerospace and transportation applications. Balsa wood cores are natural, renewable options that combine lightweight with high compressive strength and good thermal insulation. Selecting the right core material depends on the specific requirements of the project, including performance, weight, and environmental considerations.
How do I choose the right core material for my project?
Choosing the right core material for your project involves considering several key factors, including the mechanical performance requirements, weight constraints, environmental conditions, and cost. Evaluate the specific strength, stiffness, and impact resistance needed for the application, as well as the compatibility of the core material with the chosen reinforcement and resin systems. Consideration of the operating environment is crucial, as factors such as moisture exposure, temperature extremes, and chemical resistance can significantly influence material selection. Consulting with material specialists and conducting tests with potential materials can help ensure the optimal choice for your composite project.
What are the benefits of using carbon core materials in composites?
Using carbon core materials in composites offers significant benefits, including unparalleled strength-to-weight ratios, superior stiffness, and excellent thermal and electrical conductivity. Carbon core materials, such as carbon foam or carbon-reinforced honeycomb structures, provide exceptional structural integrity, enabling the design of lightweight yet highly durable components. These properties make carbon core materials particularly suitable for high-performance applications in aerospace, automotive racing, and sporting goods, where minimizing weight without sacrificing strength or stiffness is crucial. Additionally, carbon core materials can contribute to energy efficiency and performance enhancements in various applications.
Can core materials be used in both aerospace and marine applications?
Yes, core materials can be used in both aerospace and marine applications, offering tailored solutions to meet the distinct requirements of each industry. In aerospace, core materials are valued for their high strength-to-weight ratios, contributing to the efficiency and performance of aircraft and spacecraft. Marine applications benefit from core materials’ buoyancy, impact resistance, and resistance to water absorption, enhancing the durability and performance of boats and marine structures. The selection of core materials for these applications depends on specific performance criteria, including mechanical properties, environmental resistance, and weight considerations.
How do core materials contribute to the strength and stiffness of a composite?
Core materials contribute to the strength and stiffness of a composite by increasing the moment of inertia of the structure, which significantly enhances its resistance to bending and deformation. This is achieved through the sandwich construction, where the core material is placed between two stiff and strong skins. The core supports the skins, keeping them separated and stable under load, which effectively increases the composite panel’s stiffness without adding substantial weight. This structural principle allows for the creation of lightweight yet strong and stiff composite structures, optimizing performance across a wide range of applications.
What are the differences between foam cores, honeycomb cores, and carbon cores?
Foam cores, honeycomb cores, and carbon cores differ primarily in their structure, material properties, and application suitability. Foam cores are solid, lightweight materials with uniform properties that provide good strength, thermal insulation, and impact resistance. Honeycomb cores feature a unique cellular structure that offers exceptional stiffness-to-weight ratios and is ideal for applications requiring high strength with minimal weight. Carbon cores, made from carbon fiber materials, provide the highest strength and stiffness among core types, along with excellent thermal and electrical conductivity, making them suitable for high-performance and demanding applications. Each core type has its specific advantages, making them suitable for different composite manufacturing needs.
How are core materials integrated into composite structures?
Core materials are integrated into composite structures through a process known as sandwich construction. In this process, the core material is placed between layers of reinforcement fabric impregnated with resin. The assembly is then subjected to heat and pressure, either through vacuum bagging, autoclaving, or press molding, to cure the resin, bonding the core to the skins firmly. This creates a lightweight, rigid panel that combines the strength and stiffness of the outer layers with the lightweight, structural properties of the core. Proper integration techniques are crucial to ensure the performance and integrity of the composite structure.
What are the environmental impacts of using different core materials?
The environmental impacts of using different core materials vary based on the material composition, production processes, and end-of-life recyclability. Natural materials like balsa wood have a lower environmental impact due to their renewable nature and biodegradability. Synthetic foam and honeycomb cores, while offering superior performance characteristics, may have higher environmental footprints due to the energy-intensive production processes and challenges in recycling. Efforts are being made to develop more sustainable core materials and recycling methods to reduce the environmental impact of composite manufacturing. Selecting core materials with a lower environmental footprint without compromising performance is increasingly important in sustainable design and manufacturing practices.
Can core materials be recycled or reused in any way?
Recycling or reusing core materials depends on the type of material and the availability of recycling processes. Some foam and honeycomb materials can be difficult to recycle due to their composite nature and the adhesives used in sandwich panels. However, efforts are underway to develop more sustainable materials and recycling techniques. For example, thermoplastic materials offer better prospects for recycling compared to thermoset-based cores. Additionally, some core materials, like balsa wood, can be more easily repurposed or biodegraded. The industry is increasingly focusing on circular economy principles, aiming to improve the recyclability and reusability of core materials to minimize environmental impact.