Composite Semi-finished Products
A semi-finished composite product is an intermediate material that has been partially processed but requires further fabrication or finishing before it can be used in the final application. These products leverage the unique properties of composites, such as high strength-to-weight ratio, corrosion resistance, and design flexibility, providing a versatile and efficient material solution across various industries. Semi-finished composite products are available in various forms, including sheets, tubes, rods, and profiles, each designed to reduce manufacturing complexity and improve performance in specific applications. By offering a balance between customization and convenience, semi-finished composite products enable manufacturers to achieve optimal results with reduced lead times and lower costs.
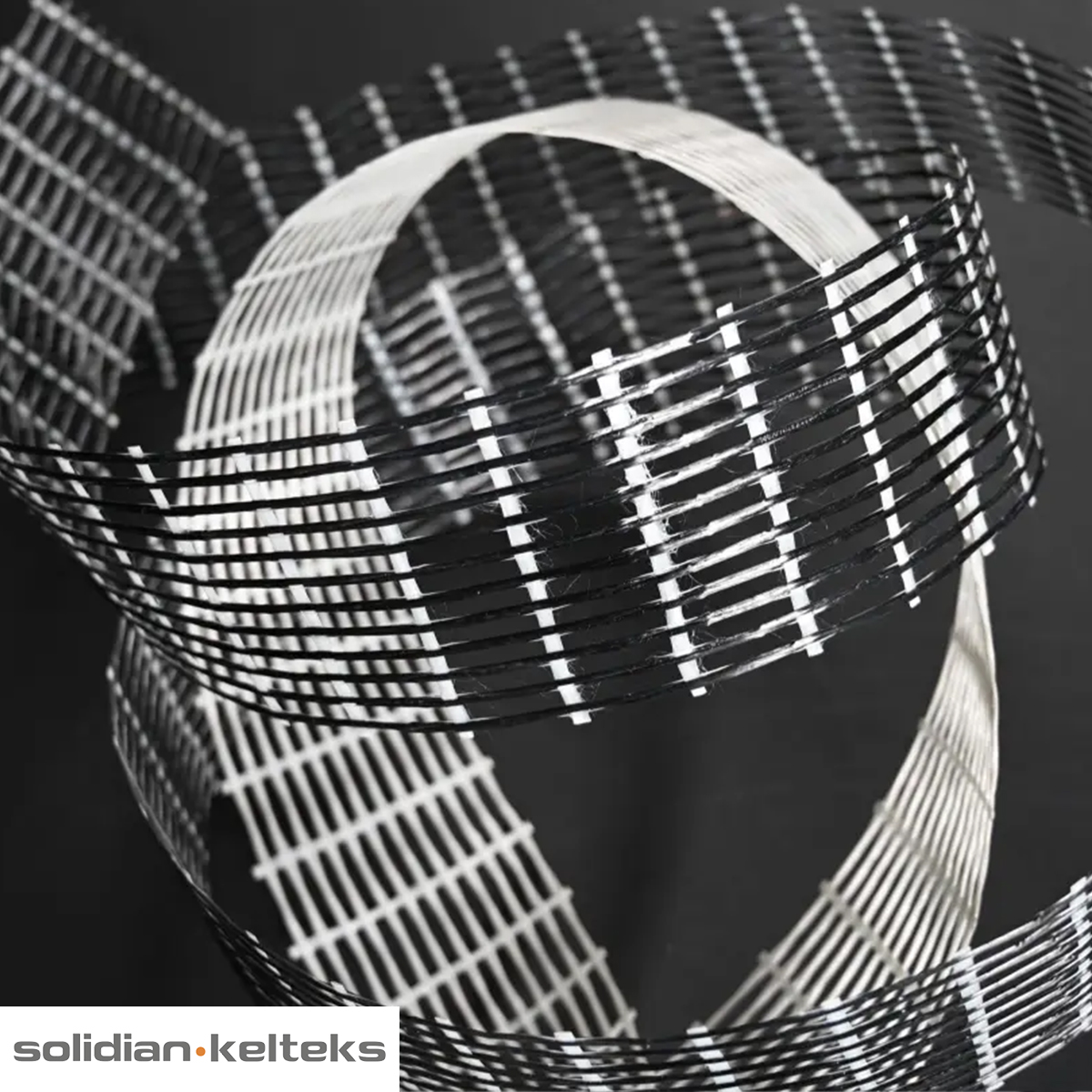
Briksy Glass-Carbon Reinforcement Brick Mesh
Review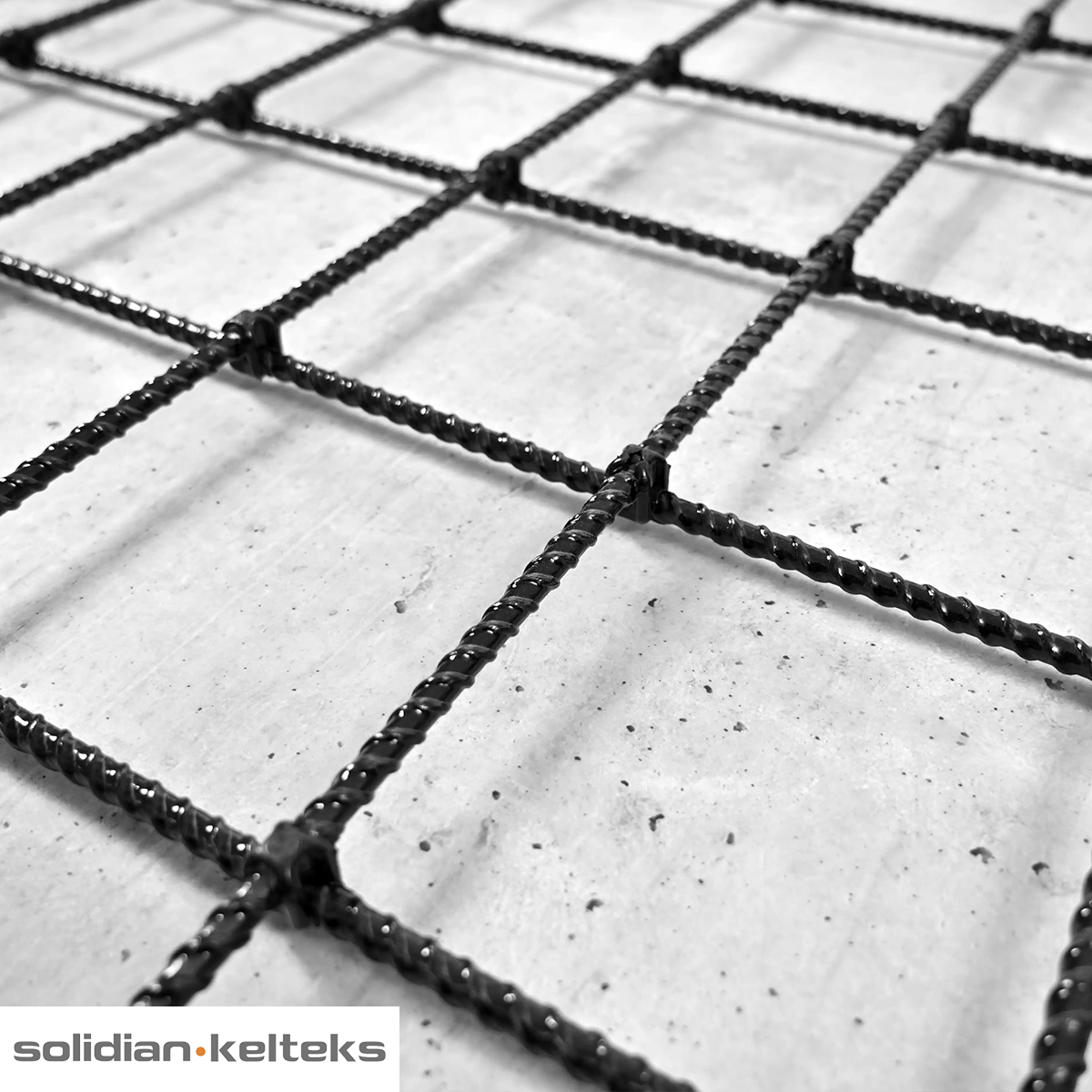
Rigid Mesh: REMAT carbon
Review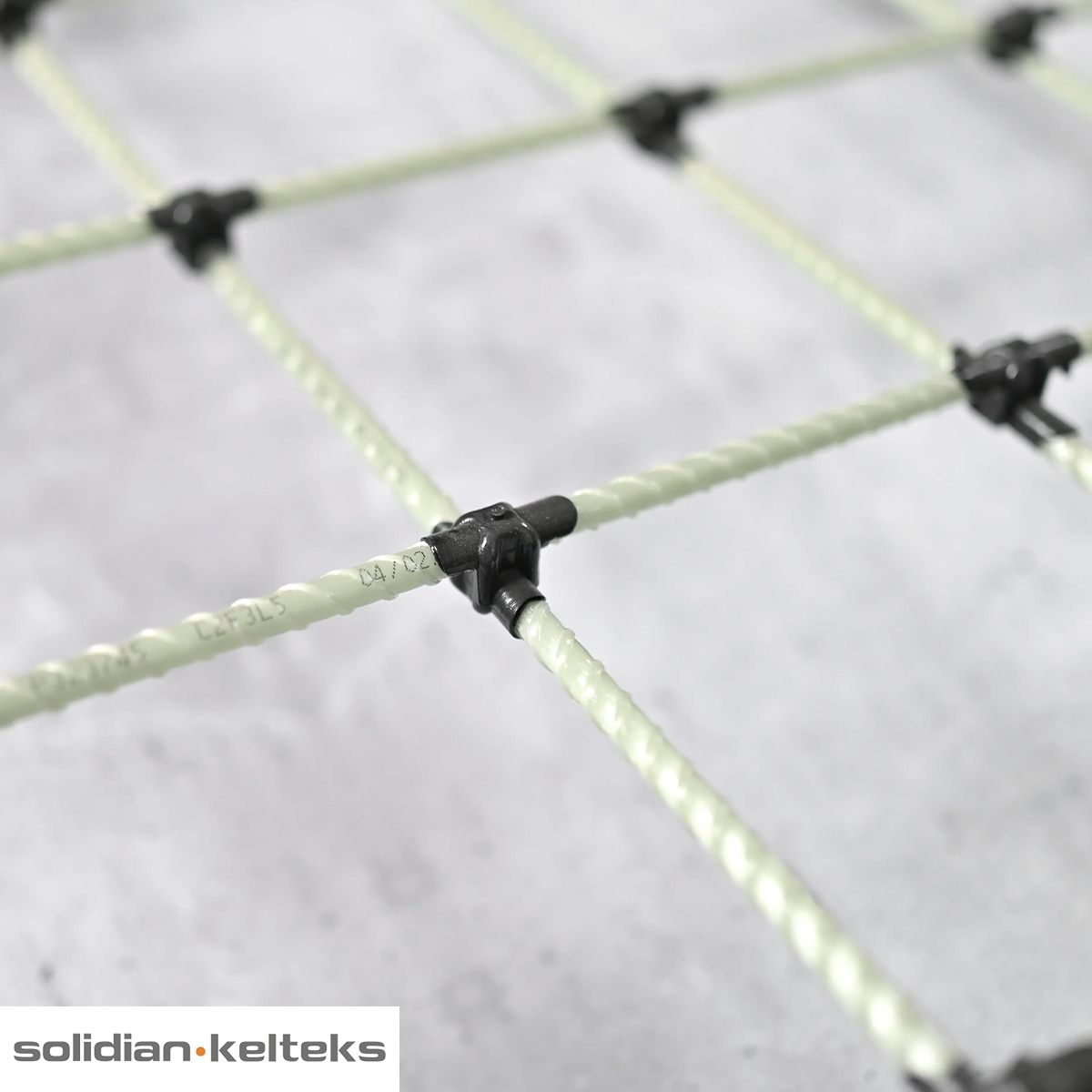
Rigid Mesh: REMAT glass
Review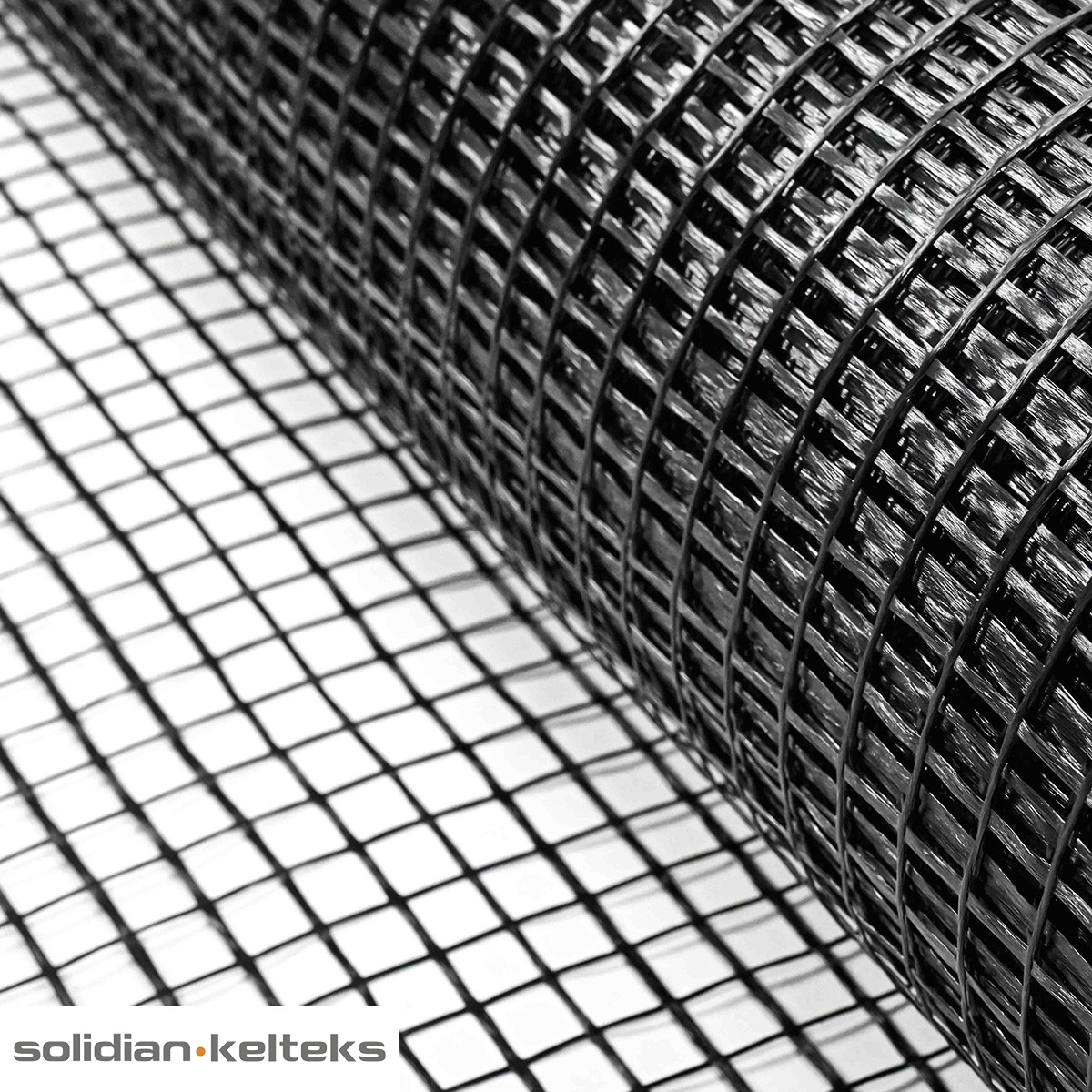
Primafloor
Review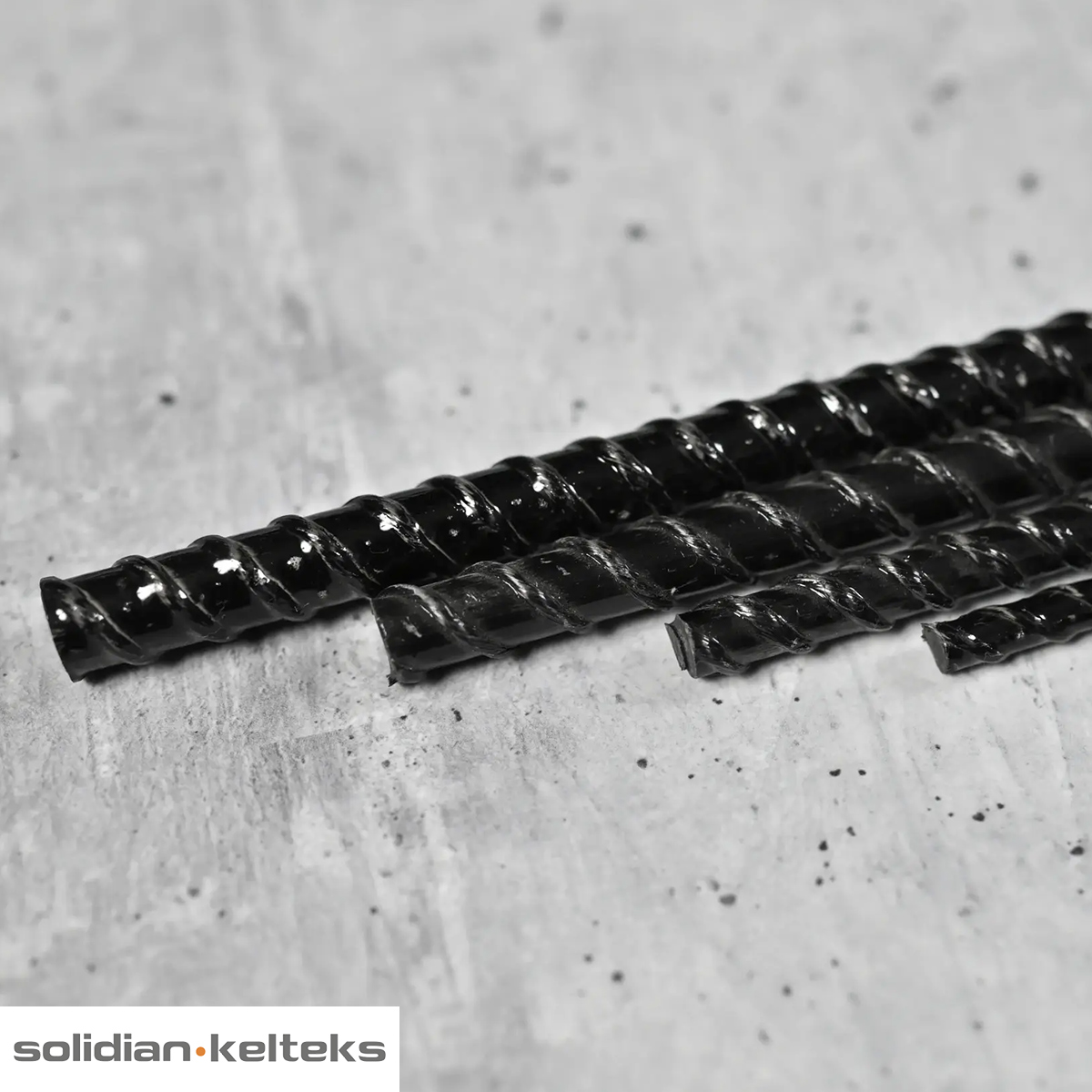
REBAR carbon
Review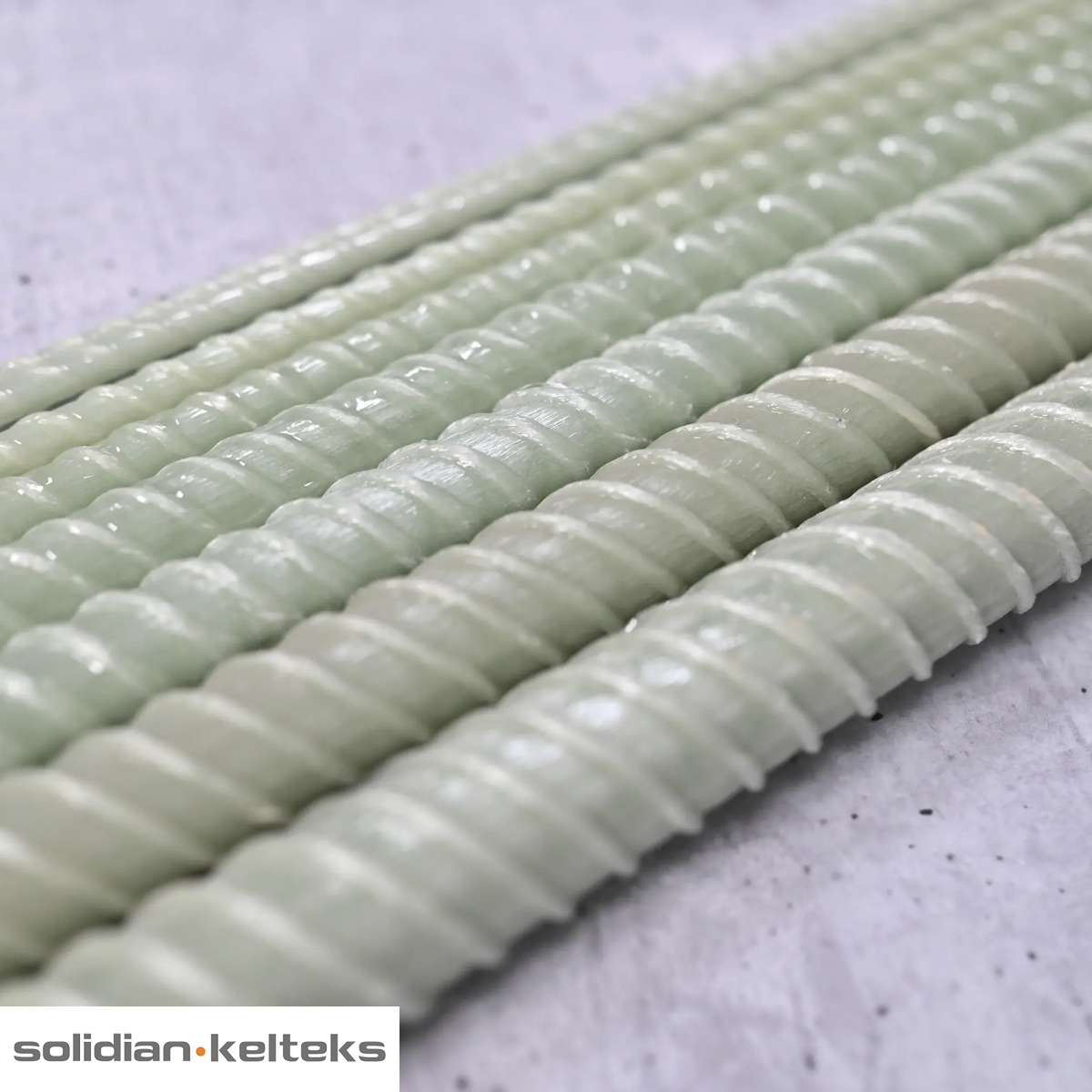
REBAR glass
Review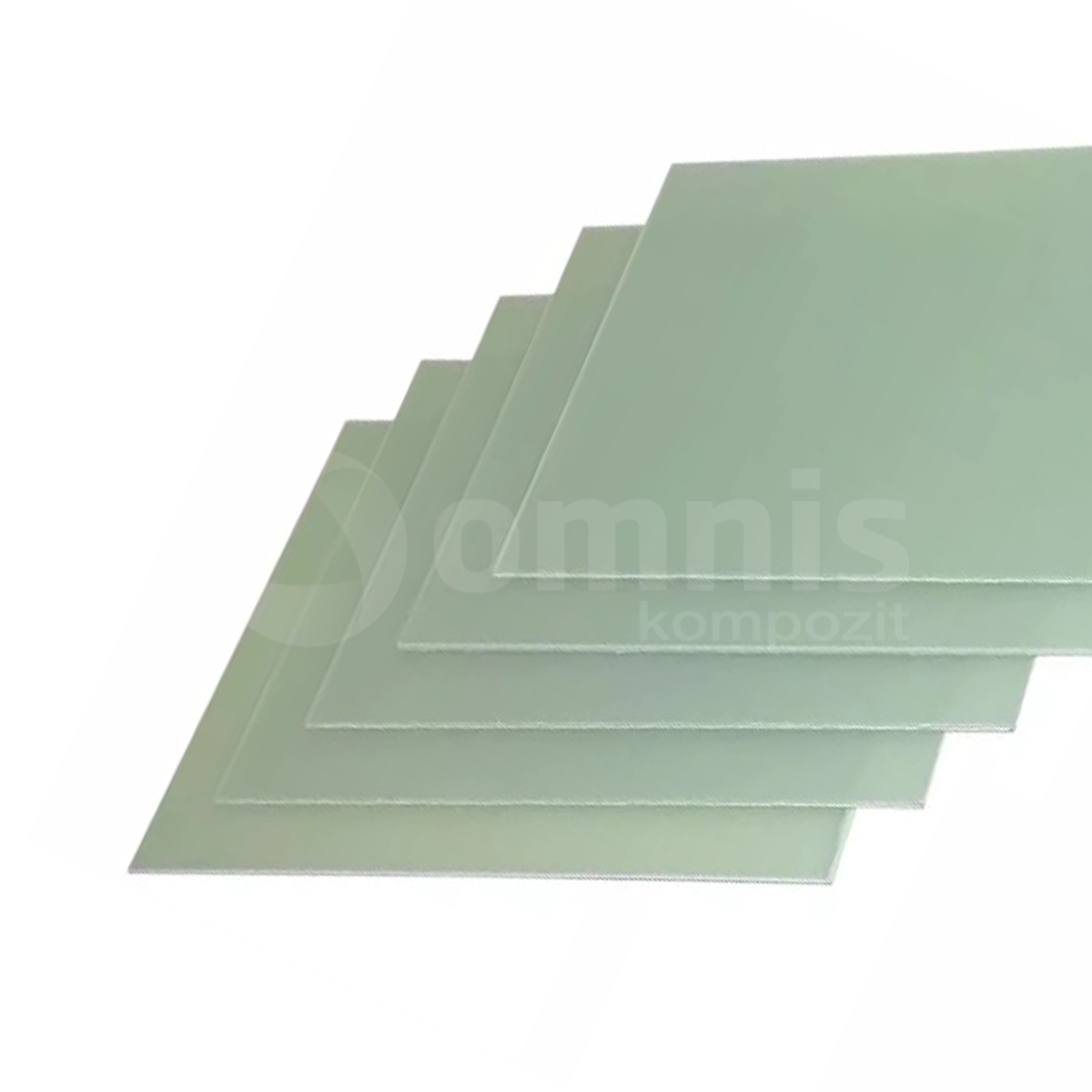
G-10 License Plate
Review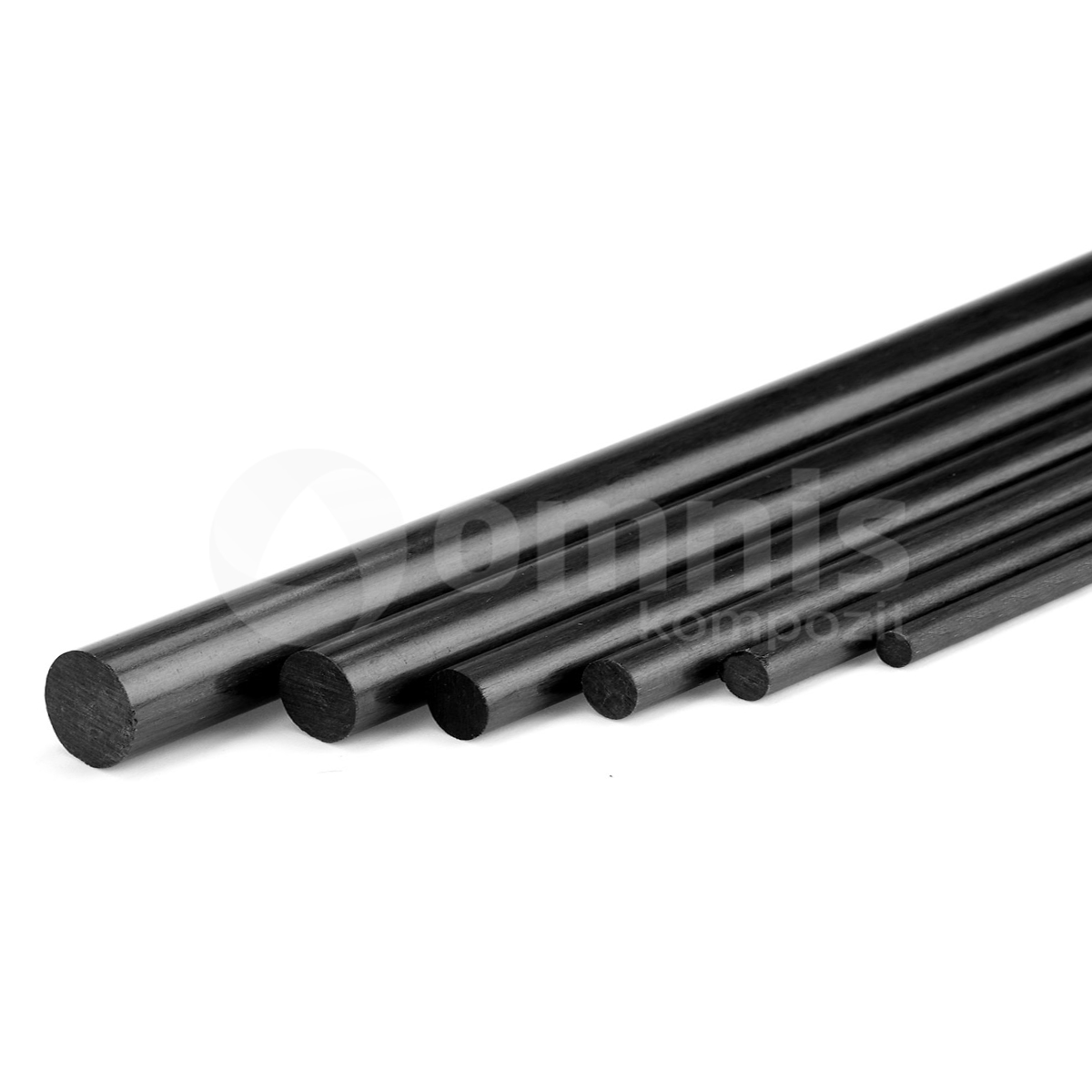
Carbon Fiber Rod
Review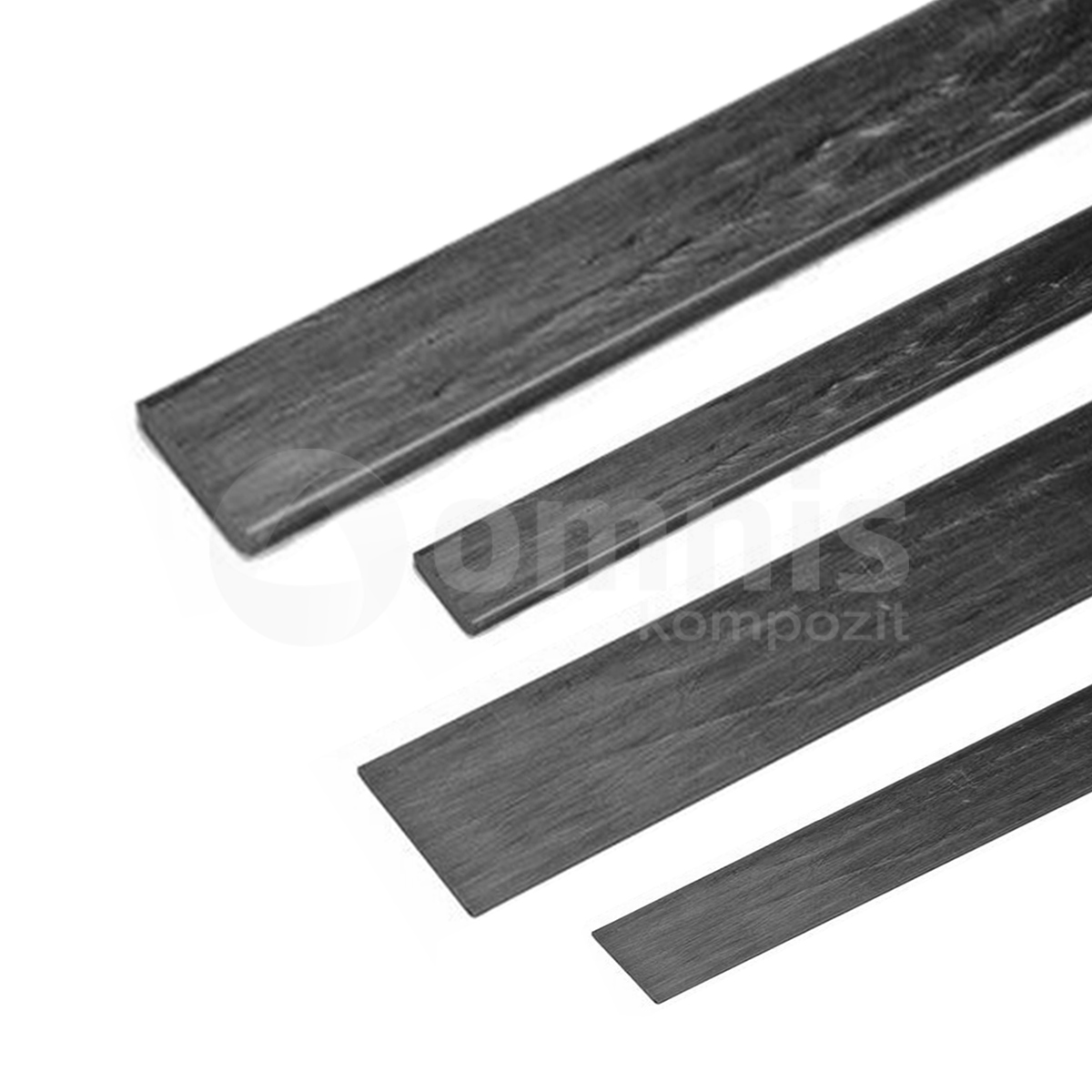
Carbon Fiber Reinforcement Strips
Review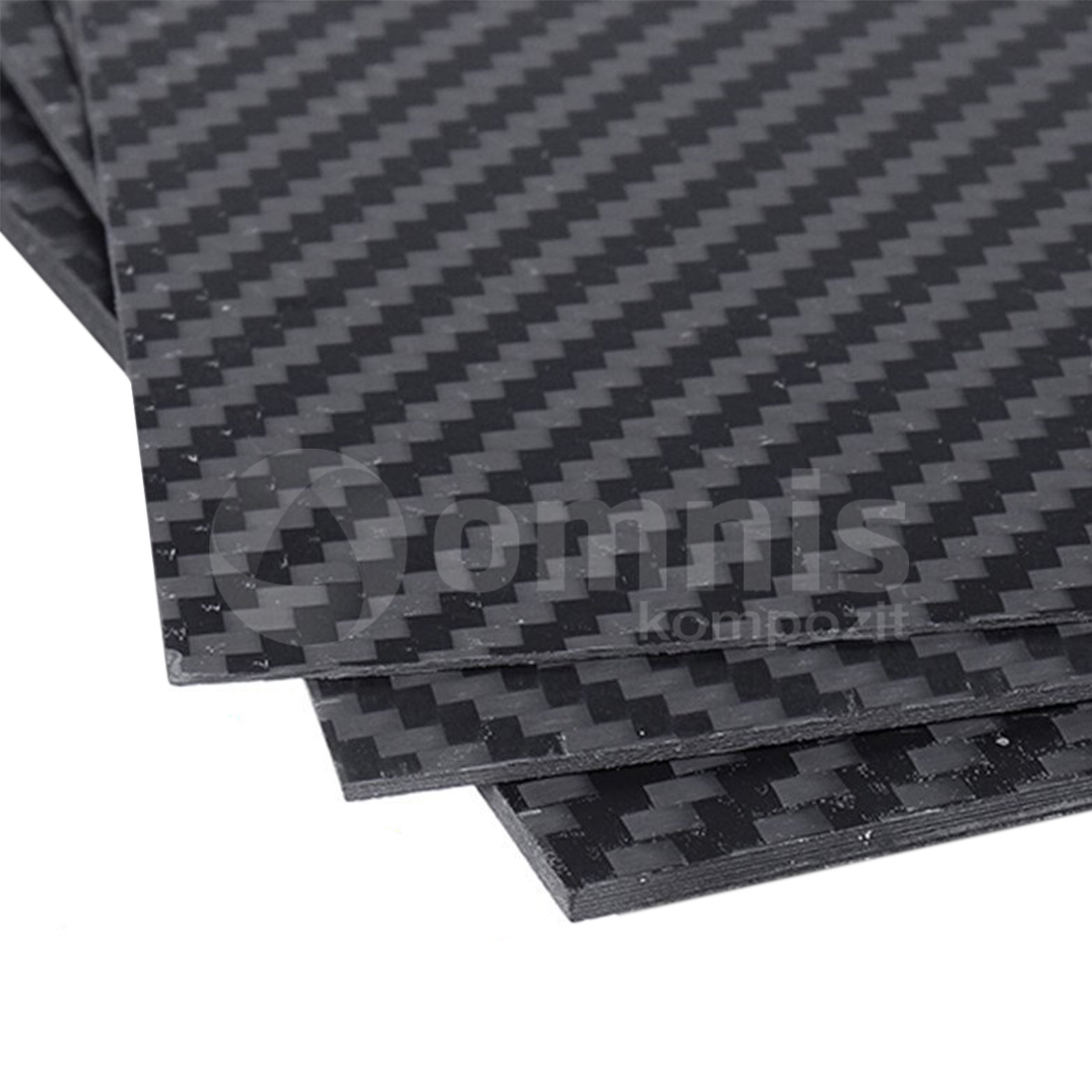
Carbon Fiber Plate
Review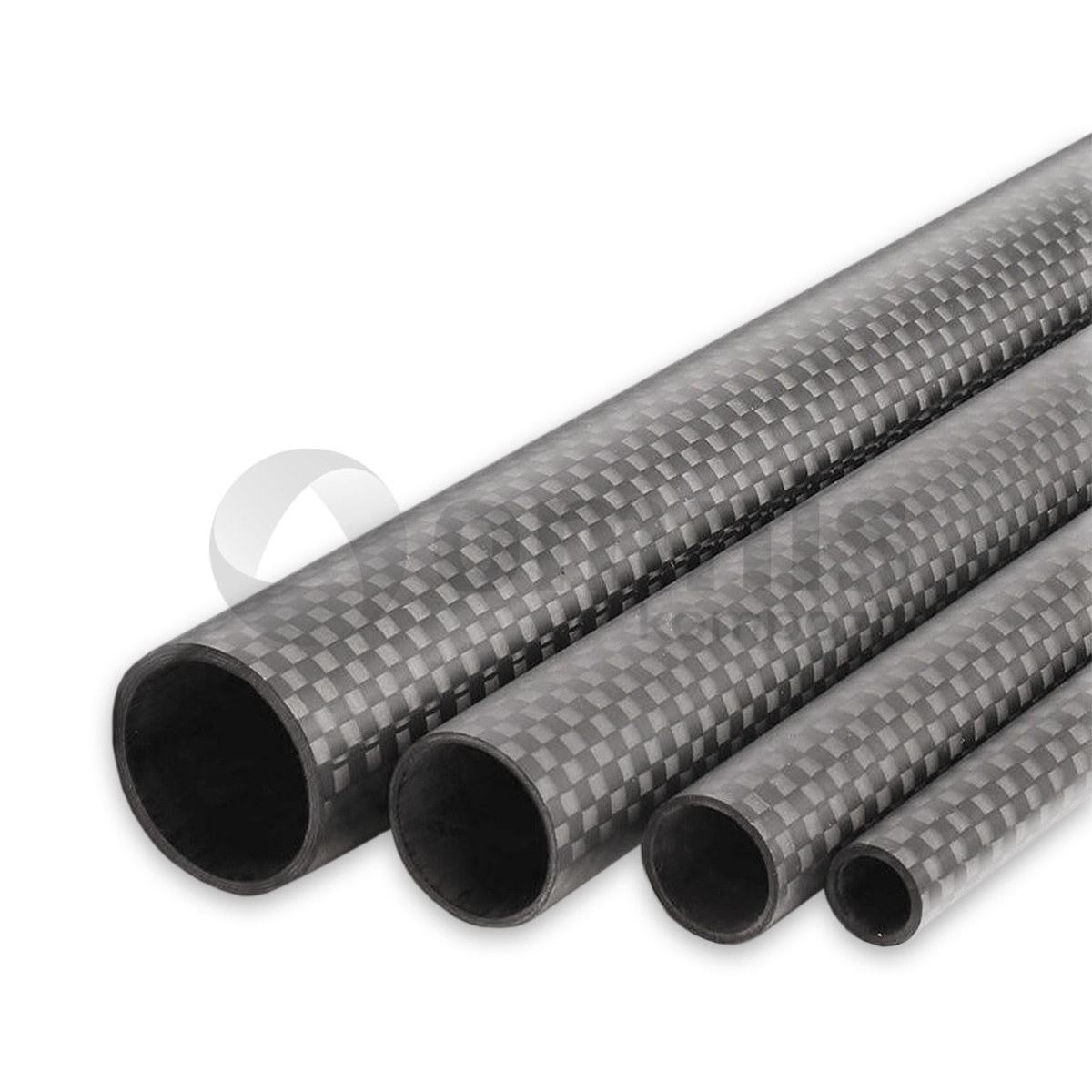
Carbon Fiber Pipe
ReviewHow are semi-finished composite products manufactured?
Semi-finished composite products are manufactured using a range of processes tailored to the specific properties and applications of the composite material. Common methods include pultrusion, filament winding, resin transfer molding (RTM), and compression molding. Each process involves the combination of reinforcement fibers, such as carbon or glass, with a polymer matrix, such as epoxy or polyester, to form a composite material with targeted characteristics. The choice of manufacturing process depends on the desired shape, size, and mechanical properties of the semi-finished product. Advanced techniques and precision engineering are employed to ensure that these semi-finished products meet stringent quality standards, offering a reliable and efficient material solution for various applications.
What are the main advantages of using semi-finished composite products?
The main advantages of using semi-finished composite products include reduced manufacturing time and costs, enhanced material performance, and design flexibility. By providing materials that are closer to the final product form, semi-finished products minimize the need for extensive machining and processing, leading to faster production cycles and lower labor requirements. The inherent properties of composite materials, such as high strength, lightweight, and resistance to corrosion and wear, are fully leveraged in semi-finished products, offering superior performance over traditional materials. Additionally, the versatility of semi-finished composite products allows for customization to meet specific application needs, supporting innovation and design optimization in various industries.
In what industries are semi-finished composite products most commonly used?
Semi-finished composite products find widespread use across a variety of industries due to their versatile properties and performance advantages. Key sectors include aerospace and defense, automotive, construction, marine, sporting goods, and energy. In aerospace, they are used for lightweight structural components; in automotive, for high-performance parts with reduced weight; in construction, for durable and corrosion-resistant elements; in marine, for robust and lightweight boat components; in sporting goods, for high-strength and lightweight equipment; and in energy, for durable infrastructure in wind turbines and other renewable energy systems. The broad applicability of semi-finished composite products underscores their role in driving innovation and efficiency in industrial and consumer applications.
Can semi-finished composite products be customized for specific applications?
Yes, semi-finished composite products can be extensively customized for specific applications, offering manufacturers the ability to tailor material properties, shapes, and sizes to meet precise requirements. This customization can include the selection of fiber types, resin formulations, and manufacturing processes to achieve desired mechanical, thermal, and chemical resistance properties. Custom shapes and dimensions can be produced to fit unique design specifications, further enhancing the material’s utility in complex applications. The flexibility in customization allows for the development of optimized solutions that maximize performance and efficiency in the final product, showcasing the adaptability of semi-finished composite products to a wide range of industrial challenges.
How do semi-finished composite products compare to traditional materials?
Semi-finished composite products offer several advantages over traditional materials such as metals, wood, and concrete, including superior strength-to-weight ratios, improved corrosion resistance, and greater design flexibility. Unlike traditional materials, composites do not succumb easily to environmental degradation, ensuring longevity and reduced maintenance costs. Their lightweight nature leads to significant energy savings and performance improvements in applications such as transportation and aerospace. Furthermore, the ability to tailor the properties of composite materials allows for innovations that are not possible with conventional materials, providing solutions that meet the evolving demands of modern engineering and design.
What types of semi-finished composite products are available?
A wide range of semi-finished composite products is available, catering to diverse application needs and manufacturing processes. Common types include composite rods, tubes, sheets, profiles, and panels. Each type can be tailored in terms of material composition, dimensions, and mechanical properties to suit specific requirements. For example, rods and tubes are often used in structural applications for their strength and rigidity, while sheets and panels may be chosen for their surface area and ease of fabrication into complex shapes. The variety of available semi-finished composite products underscores the material’s versatility and adaptability to different industrial and consumer applications.
Can semi-finished composite products be further processed or machined?
Yes, semi-finished composite products can indeed be further processed or machined to achieve the desired final product specifications. This capability is one of the key advantages of using semi-finished products in composite manufacturing. Depending on the composite material’s composition and the semi-finished product’s form, various machining processes such as cutting, drilling, milling, and grinding can be applied. These processes allow for precise shaping and sizing to fit specific application needs, making semi-finished composite products highly versatile and adaptable to a wide range of industrial and commercial uses.
To ensure the best outcomes during machining, it’s important to use tools and techniques that are compatible with the composite material’s properties, as composites can be abrasive to cutting tools and may require special handling to prevent delamination or fraying. Furthermore, the ability to machine semi-finished composite products enables manufacturers to incorporate complex features and tolerances that are crucial for the performance and integration of the composite part within its application.
Manufacturers value semi-finished composite products for their ability to reduce production times and costs while still achieving high-quality, customized components. By starting with a semi-finished product, companies can streamline their manufacturing processes, focusing on the specific modifications needed to meet their unique requirements. This efficiency, combined with the performance benefits of composite materials, makes semi-finished products an attractive option for industries ranging from aerospace and automotive to construction and consumer goods.