Carbon Fiber Pipes
A carbon fiber pipe is a high-strength, lightweight tube made from carbon fiber and resin. This cutting-edge material combines the durability and strength of carbon fiber with the versatility of a tube, making it an ideal choice for a wide range of applications. They offer exceptional rigidity and strength-to-weight ratios, outperforming traditional materials on many fronts. Ideal for applications requiring precision and endurance, a carbon fiber tube is not just a component; it's a revolution in material science, promising unparalleled performance and efficiency.
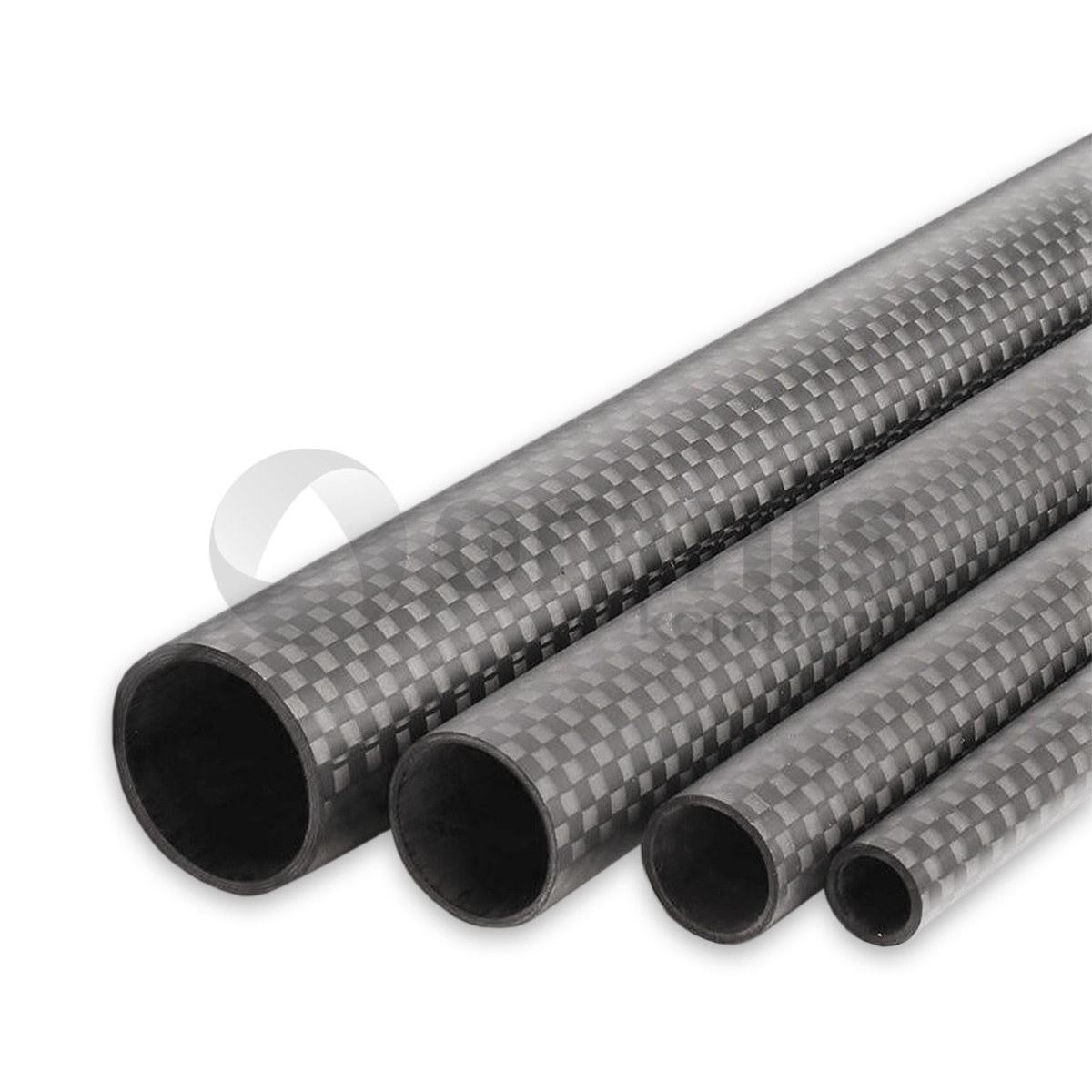
Carbon Fiber Pipe
ReviewHow are carbon fiber pipes manufactured?
The manufacturing process of carbon fiber tubes involves several sophisticated steps, starting with the winding of carbon fiber strands soaked in resin around a mandrel. This method, known as filament winding, allows for precise control over the fiber orientation, ensuring the carbon fiber tube achieves maximum strength and rigidity. After winding, the carbon fiber tube undergoes curing, where the resin hardens, bonding the carbon fibers together into a solid, robust structure. This meticulous process results in a carbon fiber pipe that offers unmatched performance and durability.
What are the main advantages of using carbon fiber pipes?
They are celebrated for their remarkable advantages, including superior strength-to-weight ratios, corrosion resistance, and durability. Unlike traditional materials, a carbon fiber tube provides the strength needed for demanding applications while being incredibly lightweight. This makes carbon fiber tubes an excellent choice for industries where performance and efficiency are paramount. Moreover, their resistance to corrosion extends their lifespan, ensuring that they remain a cost-effective solution over time.
In what industries are carbon fiber pipes most commonly used?
They find extensive use across various industries, including aerospace, automotive, civil engineering, and sports equipment. In the aerospace and automotive sectors, the lightweight yet strong carbon fiber tube contributes significantly to fuel efficiency and performance. Civil engineering projects utilize carbon fiber tubes for their durability and resistance to environmental factors, while in sports, they are preferred for their ability to enhance the performance of equipment with their lightweight and strength characteristics.
Can carbon fiber pipes be customized in terms of length and diameter?
Absolutely! Carbon fiber tubes can be tailored to meet specific requirements in length and diameter, offering unparalleled flexibility for projects and applications. Whether for industrial use or bespoke projects, a carbon fiber tube can be manufactured to precise specifications, ensuring a perfect fit and optimal performance. This customizability opens up a world of possibilities, making carbon fiber pipes a versatile choice for diverse needs.
How do carbon fiber pipes compare to traditional metal pipes in terms of strength and weight?
They outshine traditional metal pipes by offering superior strength at a fraction of the weight. This remarkable strength-to-weight ratio means that a carbon fiber tube can bear significant loads while being light enough for easy handling and installation. Compared to metals, carbon fiber does not compromise on performance for the sake of weight, making it an ideal replacement in applications where both strength and weight are critical factors.
Are carbon fiber pipes resistant to corrosion?
Yes, they exhibit excellent resistance to corrosion, making them an ideal choice for environments where traditional materials may fail. Unlike metal pipes, which can corrode over time when exposed to certain chemicals or environments, a carbon fiber tube maintains its integrity, ensuring longevity and reliability in a wide range of applications. This resistance to corrosion not only extends the lifespan of carbon fiber pipes but also reduces maintenance costs.
Can carbon fiber pipes withstand high temperatures?
They are capable of withstanding high temperatures, thanks to the thermal stability of carbon fiber and the high-performance resins used in their manufacturing. While specific temperature tolerances can vary based on the resin system, a carbon fiber tube generally offers superior performance in high-temperature environments compared to many traditional materials, making them suitable for applications requiring thermal resistance.
How do carbon fiber pipes perform under high pressure?
Carbon fiber pipes excel in high-pressure environments due to their high tensile strength and stiffness. The unique properties of carbon fiber, combined with advanced manufacturing techniques, result in a tube that can withstand significant pressure without deformation. This makes carbon fiber pipes an excellent choice for applications involving high-pressure fluids or gases, offering safety and reliability where it matters most.
What types of fluids can be safely transported through carbon fiber pipes?
They are versatile in handling a wide range of fluids, including water, oils, gases, and some chemicals. The inert nature of carbon fiber, coupled with the choice of resin, can be tailored to resist the specific fluids in question, ensuring safe and efficient transport. Whether for industrial applications, chemical processing, or water treatment, a carbon fiber tube provides a reliable conduit for various fluids.
How do you connect or join sections of carbon fiber pipe?
Connecting or joining sections of carbon fiber pipe is a streamlined process that can be tailored to the specific requirements of your project. Methods such as adhesive bonding, mechanical fastening, or the use of specially designed connectors ensure a secure and robust joint. Adhesive bonding offers a seamless connection, preserving the sleek appearance and aerodynamics of the carbon fiber tube. For applications requiring modularity or frequent disassembly, mechanical fasteners provide flexibility and ease of use. Regardless of the method, joining carbon fiber pipes ensures a durable and reliable system, allowing you to harness the full potential of carbon fiber’s strength and lightweight properties. This adaptability makes carbon fiber pipes an excellent choice for a wide range of applications, from industrial piping systems to high-performance sporting equipment.
Can they be repaired if damaged?
Yes, they can be repaired if damaged, ensuring their longevity and durability even in the most demanding environments. Repair techniques vary depending on the extent of the damage but typically involve cleaning the damaged area, applying a carbon fiber patch with a compatible resin, and curing the repair to restore the structural integrity of the carbon fiber tube. Professional repair services can restore the pipe to near its original strength, making this a cost-effective alternative to replacement. This repairability, combined with the inherent durability of carbon fiber pipes, ensures that your investment continues to deliver performance and reliability, maintaining the operational efficiency of your systems or projects.
What maintenance is required for carbon fiber pipes?
Maintenance for carbon fiber tubes is remarkably minimal, reflecting the material’s exceptional durability and resistance to environmental factors. Regular inspections to identify any potential damage or wear and prompt cleaning to remove debris or chemicals are generally all that’s required to maintain the optimal condition of a carbon fiber tube. Unlike metal pipes, carbon fiber tubes do not corrode, significantly reducing the need for protective treatments or frequent replacements. This low maintenance requirement, coupled with the long service life of carbon fiber tubes, provides a cost-efficient solution that ensures continuous performance without the need for extensive upkeep. By choosing carbon fiber pipes, you’re investing in a solution that not only meets but exceeds the demands of your application, offering reliability, efficiency, and unparalleled performance.