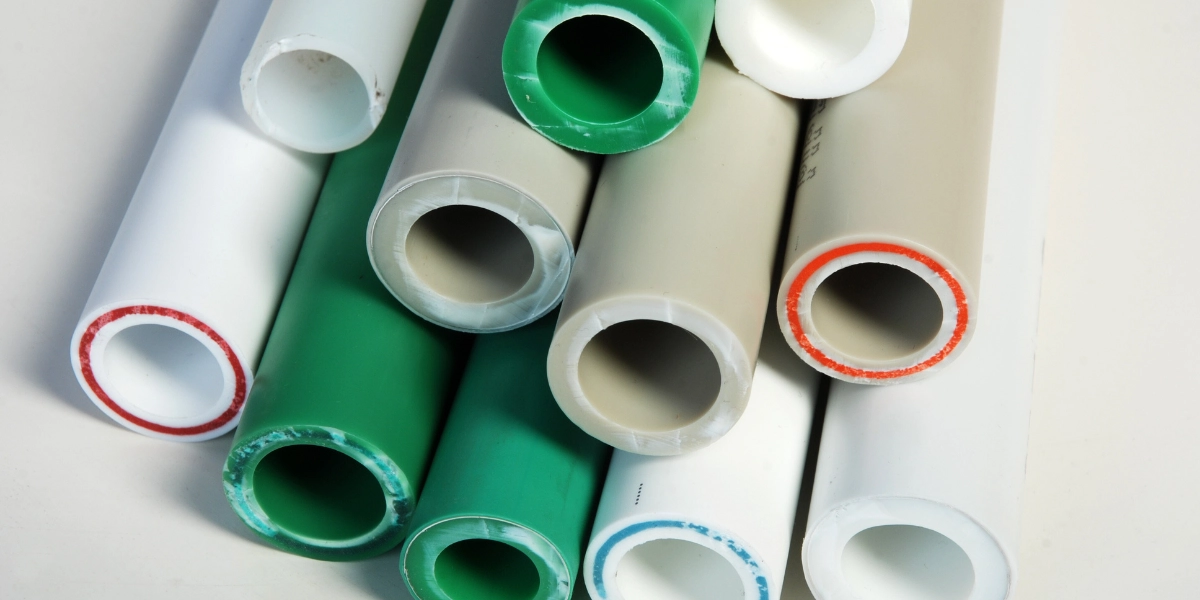
- Blog
- 6 Jan 2025
Exploring the Pultrusion Manufacturing Process
The pultrusion manufacturing process is a highly efficient method for creating composite materials that are lightweight, strong, and consistent in quality. By continuously pulling fibers and resin through a heated die, pultrusion produces structural components with uniform cross-sections. This technique is widely used across various industries, including construction, transportation, and electrical, due to its ability to create durable and reliable products. Understanding the pultrusion manufacturing process is essential for those interested in modern composite production techniques, as it provides valuable insight into the advantages and applications of this versatile manufacturing method.
Definition of Pultrusion
The pultrusion manufacturing process is a continuous production method used to create composite materials with a constant cross-sectional profile. The term “pultrusion” is derived from a combination of “pull” and “extrusion,” highlighting the key principle of pulling raw materials through a die to form the desired shape. This process is particularly well-suited for manufacturing long, straight products such as rods, beams, and channels that are used in various industrial and structural applications. Pultrusion is an efficient way to produce lightweight, high-strength components with consistent quality, making it a valuable technique in the field of composite manufacturing.
Key Steps in the Pultrusion Manufacturing Process
The pultrusion manufacturing process consists of several key steps that work together to create strong and durable composite products. By breaking down the pultrusion process into smaller steps, we can better understand how each phase contributes to the final result. Below, we discuss the primary stages of material preparation, the pulling mechanism, and the curing and cooling stages.
Material Preparation
The first step in the pultrusion manufacturing process is material preparation. Raw materials, such as glass fibers, carbon fibers, or other reinforcing fibers, are carefully aligned and impregnated with a resin matrix. Typically, epoxy resin is used in this process due to its excellent bonding properties and resistance to environmental degradation. The resin acts as a binding agent, ensuring that the fibers remain in place and are effectively bonded throughout the production process. Proper material preparation is crucial, as it sets the foundation for the quality and performance of the pultruded product.
Pulling Mechanism
After the materials are prepared, they are pulled through a heated die using a mechanical pulling system. This is where the term “pultrusion” comes into play, as the entire process revolves around pulling the fibers and resin combination through the die. The heated die gives the composite its specific shape, with the desired cross-section, and the temperature helps initiate the curing reaction of the resin. The pulling mechanism ensures that the composite materials are evenly distributed and correctly aligned, which is essential for the structural integrity of the final product. The pultrusion manufacturing process relies on this pulling action to achieve continuous and consistent production.
Curing and Cooling Stages
Once the material passes through the heated die, the curing stage begins. Curing involves hardening the resin to achieve the desired mechanical properties. During the curing stage of the pultrusion manufacturing process, the material is exposed to heat to ensure the resin sets properly and forms a rigid composite structure. Following the curing process, the composite is cooled down to stabilize its shape and properties. This cooling step is critical, as it allows the product to maintain its form and ensures that the final pultruded component is ready for use in various applications without any deformation or loss of structural integrity.
Materials Used in Pultrusion
The pultrusion manufacturing process utilizes a range of materials, each selected for its specific properties to enhance the final product. Common reinforcing fibers include glass fiber, carbon fiber, and aramid fiber, each offering unique characteristics in terms of strength and flexibility. For example, carbon fiber rod is often used when high stiffness and lightweight properties are required. The resin matrix, typically made of polyester, vinyl ester, or epoxy resin, plays a crucial role in binding the fibers together and protecting them from environmental exposure. The combination of reinforcing fibers and resins in the pultrusion process allows for the production of composite materials with excellent mechanical and chemical resistance properties.
Advantages of the Pultrusion Manufacturing Process
The pultrusion manufacturing process offers several advantages that make it an attractive choice for composite production. One of the main benefits is the ability to create lightweight yet highly durable components with a constant cross-sectional shape. Pultrusion is also highly efficient, allowing for continuous production with minimal waste. Another advantage is the ability to produce composites with tailored properties by selecting specific fiber and resin combinations. For instance, using FRP reinforcement allows for enhanced strength and rigidity, making pultruded products ideal for construction and infrastructure applications. Overall, pultrusion provides a cost-effective way to produce high-quality composite components with predictable performance.
Applications of Pultruded Products
Pultruded products find applications across a variety of industries due to their unique properties. In construction, pultruded beams, channels, and rods are used as structural components that require high strength-to-weight ratios. In the electrical industry, pultruded materials are often used for cable trays and ladder racks due to their excellent insulating properties. The transportation industry also benefits from pultruded products, especially when lightweight, corrosion-resistant components are needed for vehicles, trains, and ships. The versatility of the pultrusion manufacturing process makes it suitable for producing a wide range of products that meet specific industrial needs.
Challenges and Limitations in Pultrusion
While the pultrusion manufacturing process has many advantages, it also comes with certain challenges and limitations. One of the primary challenges is the limitation to producing parts with a constant cross-sectional profile, which restricts the shapes that can be produced. Additionally, the pultrusion process requires precise control of temperature and pulling speed to ensure consistent product quality. Any variation in these parameters can lead to defects, such as voids or incomplete curing of the resin. Furthermore, the initial setup cost for pultrusion equipment can be high, which may be a barrier for small-scale manufacturers. Despite these challenges, the benefits of the pultrusion manufacturing process often outweigh the limitations, particularly for large-scale production of high-quality composite materials.
In conclusion, the pultrusion manufacturing process is a highly efficient and effective method for producing composite materials with a consistent cross-sectional profile. By understanding the key steps involved, including material preparation, pulling, and curing, we can appreciate the complexity and precision required to create high-quality pultruded products. The combination of advanced materials like carbon fiber rod and epoxy resin makes pultrusion a versatile solution for numerous industrial applications. Despite some challenges, the advantages of the pultrusion process ensure its continued importance in the field of composite manufacturing, providing industries with lightweight, durable, and cost-effective solutions for a wide range of structural and functional needs.