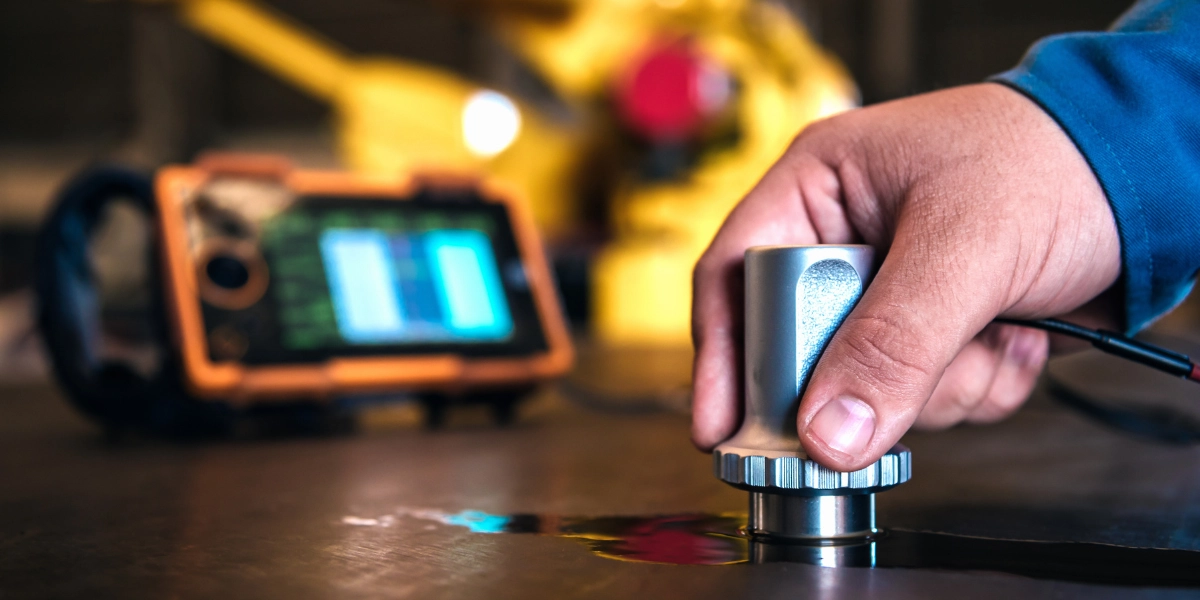
- Blog
- 27 Dec 2024
An In-Depth Guide to Composite Testing Methods and Applications
Composite testing plays a vital role in ensuring the quality and reliability of materials used in various industries. Composite materials are engineered to provide superior properties by combining two or more constituent materials, and these properties must be verified through rigorous testing. By understanding the different methods and their importance, engineers and manufacturers can make informed decisions and improve the safety and performance of their composite products. This guide will explore key aspects of testing, including methods, challenges, and standards, to provide a comprehensive understanding of this essential process.
Definition and Importance of Composite Testing
Composite testing refers to the various methods used to evaluate the properties and performance of composite materials. Composites, which are made from two or more constituent materials, are designed to achieve superior strength, stiffness, or other mechanical properties compared to their individual components. Composite testing is crucial because it ensures these materials meet the necessary performance standards for their intended use. By conducting this testing, manufacturers and engineers can verify the integrity, reliability, and safety of composite components in industries such as aerospace, automotive, and construction.
Key Methods of Composite Testing
Composite testing involves multiple methods to assess different aspects of the material. Each testing method provides valuable insights into how the composite behaves under specific conditions, helping engineers understand its suitability for various applications. Here, we’ll explore some of the key methods of testing and how they contribute to assessing the material’s overall quality and performance.
Mechanical Testing
Mechanical testing is a fundamental part of composite testing that evaluates the strength, stiffness, and other mechanical properties of a composite material. Methods such as tensile, compressive, and flexural tests fall under mechanical testing, and they help determine the performance limits of a composite under different loads. For example, FRP reinforcement materials, commonly used in construction, are subjected to these tests to ensure they can withstand the mechanical stresses they will encounter. Mechanical testing is vital for applications where the structural integrity of composites must be guaranteed.
Non-Destructive Testing (NDT)
Non-Destructive Testing (NDT) is another essential aspect of composite testing, allowing for the evaluation of material properties without causing any damage. Techniques such as ultrasonic testing, radiography, and thermography are widely used to detect flaws, cracks, or delaminations within the composite. NDT methods are invaluable in industries where safety is paramount, like aerospace and automotive, as they ensure the reliability of composite components without compromising their usability. By incorporating non-destructive testing, engineers can gain crucial insights into the condition of composite materials at any stage of production or during their service life.
Thermal Testing
Thermal testing is an important part of composite testing that helps evaluate how composites react to changes in temperature. Composite materials may undergo expansion, contraction, or even degradation when exposed to varying thermal conditions, and thermal testing allows engineers to determine these behaviors. The properties of materials like epoxy resin, which is often used as a matrix in composites, can change significantly under thermal stress. Thermal testing helps identify temperature limits and ensures that the composite will maintain its structural properties under extreme temperature conditions, making it crucial for applications in aerospace and automotive industries.
Why Composite Testing is Essential in Industries
Composite testing is an indispensable part of ensuring that materials used in critical applications are safe and reliable. For industries such as aerospace, automotive, and construction, composite materials are chosen for their unique properties, including high strength-to-weight ratios and resistance to environmental conditions. Conducting this testing provides manufacturers with the confidence that these materials will meet performance expectations. For example, using non-woven polyester in composites requires testing to confirm its ability to provide reinforcement without compromising flexibility. Proper testing helps industries avoid costly failures and guarantees long-term performance.
Challenges in Composite Testing
While testing is essential, it also comes with its challenges. The heterogeneous nature of composites, which involves combining materials like fibers and resins, often leads to complexities in testing. Unlike metals, composites can have highly anisotropic properties, meaning they behave differently depending on the direction of the load applied. This makes the interpretation of this testing results more complex. Additionally, testing methods must be carefully chosen to ensure they do not introduce defects into the material. Overcoming these challenges requires specialized knowledge, experience, and appropriate testing equipment to achieve reliable results.
Advanced Technologies in Composite Testing
Recent advancements in technology have significantly improved the capabilities of testing. One of the notable advancements is the use of digital image correlation (DIC), which allows for precise strain measurements and deformation analysis during mechanical testing. In addition, automated ultrasonic testing systems have enabled faster and more accurate non-destructive testing, particularly for large composite structures like wind turbine blades. The development of advanced simulation tools has also played a role in this testing, allowing engineers to predict material behavior under different conditions before conducting physical tests. By embracing these advanced technologies, industries can better ensure the quality and reliability of composite materials.
Standards and Certifications for Composite Testing
Composite testing is governed by various standards and certifications that ensure consistency, safety, and reliability. Organizations such as ASTM (American Society for Testing and Materials) and ISO (International Organization for Standardization) have established guidelines for this testing procedures. These standards cover mechanical, thermal, and non-destructive testing methods to provide a comprehensive framework for evaluating composite materials. Adhering to these standards helps manufacturers produce consistent products that meet industry requirements. For example, epoxy resin composites used in aerospace applications must meet stringent testing standards to ensure they can handle the demanding conditions of flight. Compliance with these certifications ensures that composite materials deliver reliable performance across diverse applications.
In conclusion, composite testing is a crucial process that guarantees the performance and reliability of composite materials used across different industries. By employing a range of testing methods—mechanical, non-destructive, and thermal—manufacturers can assess various properties and ensure their materials meet stringent requirements. Although challenges exist in this testing, advancements in technology and adherence to established standards have made significant strides in improving the accuracy and efficiency of these tests. Whether used in aerospace, automotive, or construction, proper composite testing ensures that composite materials can deliver the strength, durability, and safety needed for their intended applications.