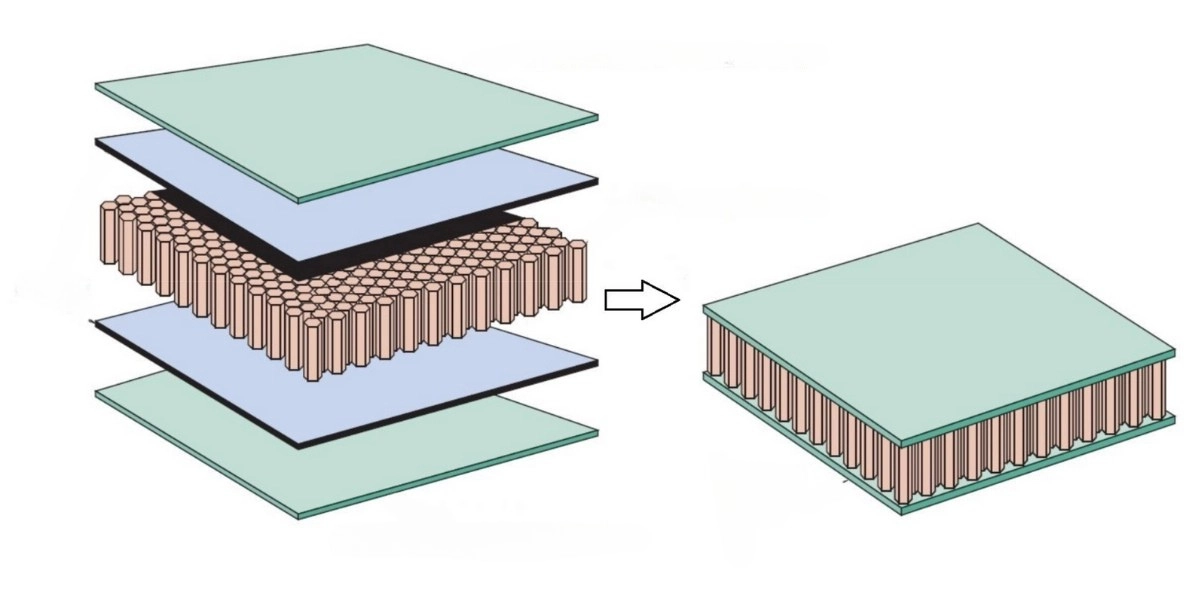
- Blog
- 28 Mar 2025
Top Benefits of Composite Sandwich Structures
In modern manufacturing, the demand for lightweight, durable, and high-performance materials continues to grow. Composite sandwich structures have become a popular solution across various industries due to their exceptional strength-to-weight ratio and design flexibility. By combining strong outer layers with lightweight core materials, these structures offer excellent mechanical properties while reducing overall weight. Their versatility makes them ideal for applications in aerospace, automotive, marine, and construction sectors. In this article, we will explore what sandwich composites are, their key benefits, and how they excel in today’s advanced manufacturing processes.
What Are Composite Sandwich Structures?
Sandwich composites are advanced materials made by layering two strong outer skins around a lightweight core. This design creates a structure that is both rigid and lightweight, offering high strength without adding extra weight. The outer skins are usually made from materials like fiberglass or carbon fiber structural reinforcement, which provide excellent durability and resistance to external forces.
The core materials play a crucial role in the overall performance of the structure. Common core options include PP honeycomb, known for its excellent impact resistance and lightweight properties, and PVC foam, which offers great insulation and moisture resistance. These cores help distribute loads evenly across the structure while preventing bending and deformation.
Key Benefits of Composite Sandwich Structures
Sandwich composites offer an outstanding balance of strength, stiffness, and lightweight performance, making them ideal for various industries. Their unique design, combining durable outer skins with lightweight core materials results in a high strength-to-weight ratio that enhances structural efficiency while reducing overall weight. This not only improves fuel efficiency in transportation applications but also lowers material costs. Additionally, these structures provide excellent impact resistance, thermal insulation, and corrosion resistance, ensuring long-lasting durability even in demanding environments. Their versatility and performance make them a preferred choice in aerospace, automotive, marine, and construction sectors.
Why Composite Sandwich Structures Excel in Modern Manufacturing
Sandwich composites excel in modern manufacturing due to their perfect blend of strength, lightweight properties, and design flexibility. Their high strength-to-weight ratio allows manufacturers to create durable yet lightweight components, which is essential in industries like aerospace and automotive for improving fuel efficiency and performance. The use of versatile core materials enable customized solutions for specific needs like impact resistance or thermal insulation. Additionally, incorporating carbon fiber structural reinforcement in the outer skins enhances durability and stiffness, making these structures ideal for complex, high-performance applications while also reducing production and operational costs.
Common Applications of Composite Sandwich Structures
Thanks to their lightweight, strength, and versatility, sandwich composites are used across a wide range of industries. Their ability to combine durability with reduced weight makes them ideal for applications where performance, efficiency, and longevity are essential.
Aerospace Components
In aerospace, sandwich composites are used in aircraft panels, flooring, and interior components. Their lightweight nature helps improve fuel efficiency while maintaining the strength needed to withstand high stress and pressure during flight.
Automotive Body Panels
Automotive manufacturers use these structures for body panels, hoods, and floors to reduce vehicle weight without compromising safety. This enhances fuel efficiency and performance while maintaining crash resistance.
Marine Structures
In marine applications, sandwich composites are used for hulls, decks, and bulkheads. Their resistance to moisture and corrosion makes them ideal for harsh marine environments, while their lightweight design improves buoyancy and fuel efficiency.
Wind Turbine Blades
Wind turbine blades benefit from the high strength-to-weight ratio of sandwich composites. This allows for longer, more efficient blades that can capture more wind energy without adding excessive weight, leading to better energy output.
Construction Panels and Architectural Uses
In construction, these structures are used for wall panels, roofing, and facades. They provide excellent insulation, strength, and durability while being lightweight, which simplifies installation and reduces structural load.
Composite sandwich structures have become essential in modern manufacturing due to their unique combination of strength, lightweight performance, and versatility. By integrating durable outer skins with lightweight core materials like PP honeycomb and PVC foam, these structures deliver high strength-to-weight ratios, improved energy efficiency, and long-lasting durability. Whether in aerospace, automotive, marine, wind energy, or construction, they offer tailored solutions that meet the demanding needs of each industry. With the added benefits of carbon fiber structural reinforcement, composite sandwich structures continue to push the boundaries of design and performance, making them a top choice for innovative and efficient engineering solutions.