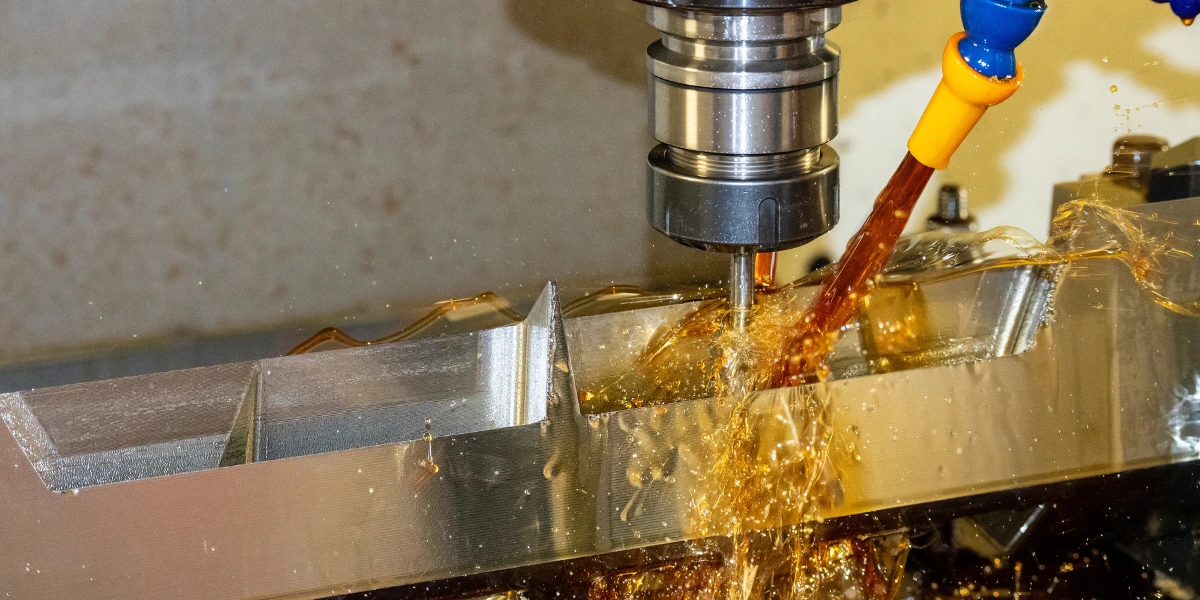
- Blog
- 14 Mar 2025
Closed Molding Process Explained
Closed molding process is a widely used manufacturing technique in the composite industry. It involves shaping composite materials inside a sealed mold, preventing direct exposure to the environment. This method is favored for its ability to produce high-quality, consistent parts while minimizing waste and emissions.
In this guide, you will learn what the closed molding process is, its types, materials used, benefits, and common applications in modern manufacturing.
What is the Closed Molding Process?
The closed molding process also known as sealed molding process is a composite manufacturing method where materials are placed inside a sealed mold cavity. Resin is introduced into the mold, and pressure or vacuum is applied to ensure the material takes the mold’s shape completely.
This process ensures precise control over resin distribution and fiber placement, leading to stronger and more durable finished parts. The closed mold design also reduces the emission of volatile organic compounds (VOCs), making it more environmentally friendly than open molding techniques.
Types of Closed Molding Processes
Several variations of the sealed molding exist, each tailored for specific manufacturing needs and material types.
1. Vacuum Infusion Process (VIP)
The vacuum infusion process (VIP) involves placing dry fibers into a mold and sealing it with a vacuum bag. A vacuum is then applied, drawing resin into the mold and saturating the fibers evenly.
Key Advantages:
Ideal for large, complex parts.
Reduced waste and resin consumption.
Compatible with high-performance materials like epoxy resin.
VIP often uses vacuum consumables such as peel ply, breather fabric, and flow media to assist in resin flow and ensure complete fiber saturation.
2. Resin Transfer Molding (RTM)
Resin Transfer Molding (RTM) involves placing reinforcement materials into a closed mold cavity. Resin is then injected under pressure, saturating the fibers.
Key Advantages:
- Suitable for medium to high production volumes.
- Produces parts with smooth finishes on both sides.
- Reduces material waste compared to open molding.
To prevent sticking and ensure clean part removal, mold release agents are often applied to the mold surfaces before production begins.
3. Light Resin Transfer Molding (LRTM)
Light Resin Transfer Molding (LRTM) is a variation of RTM that uses a lighter mold and lower injection pressures. It’s ideal for medium-volume production and offers a balance between cost and quality.
Key Advantages:
- Cost-effective for medium production runs.
- Reduced equipment costs compared to standard RTM.
- Easier mold handling and setup.
4. Compression Molding in Closed Molding
Compression molding in a sealed molding involves placing a pre-measured amount of material into a heated mold. The mold is then closed, and heat and pressure are applied to shape the part.
Key Advantages:
- Ideal for high-volume production.
- Excellent for parts with consistent thickness.
- Suitable for both thermoset and thermoplastic materials.
Benefits of the Closed Molding Process
The sealed molding offers several advantages, making it a preferred choice in industries requiring precision and efficiency.
1. Enhanced Product Quality
Closed molds provide better control over fiber placement and resin flow, resulting in parts with improved strength, consistency, and surface finish.
2. Reduced Emissions
Since the mold is sealed, VOC emissions are significantly lower than in open molding, contributing to a safer work environment and better regulatory compliance.
3. Material Efficiency
The controlled resin flow minimizes waste, making sealed molding processes more cost-effective and sustainable compared to open molding methods.
4. Faster Production Times
The automation and control offered by sealed molding processes allow for faster curing and cycle times, making it ideal for medium to high production runs.
5. Compatibility with Composite Manufacturing Processes
The sealed molding process integrates seamlessly with other composite manufacturing processes, such as filament winding and pultrusion, enabling manufacturers to produce complex hybrid components efficiently.
Materials Used in Closed Molding
The sealed molding process can accommodate a wide range of materials depending on the application’s requirements for strength, flexibility, and heat resistance.
1. Reinforcements
- Carbon Fiber: Known for its high strength-to-weight ratio, often used in aerospace and sports equipment.
- Glass Fiber: Commonly used for automotive and construction applications due to its affordability and good mechanical properties.
- Kevlar: Offers excellent impact resistance, ideal for protective gear and aerospace parts.
2. Resins
- Epoxy Resin: Provides excellent strength, chemical resistance, and durability, making it a top choice for high-performance parts.
- Polyester Resins: More affordable and suitable for general-purpose composite parts, such as automotive panels.
- Vinyl Ester Resins: Known for their corrosion resistance, often used in marine and chemical storage applications.
3. Mold Release Agents
To prevent parts from sticking to the mold, mold release agents are commonly applied to the mold surface before production. These agents improve part removal, reduce defects, and extend mold life.
Applications of Closed Molding
The sealed molding process is widely used across various industries due to its ability to produce high-quality, durable parts with minimal waste.
1. Aerospace
Used for manufacturing lightweight yet strong components such as fuselage panels and structural reinforcements using epoxy resin.
2. Automotive
Common for producing car body panels, bumpers, and structural parts due to its efficiency and ability to handle polyester resins.
3. Marine
Ideal for boat hulls, decks, and structural components where corrosion resistance and durability are critical.
4. Wind Energy
Wind turbine blades are often made using sealed molding processes due to the need for large, strong, and aerodynamic components.
5. Construction
The closed molding process is used in sustainability in construction projects for producing eco-friendly structural elements with minimal material waste.
6. Sports and Recreation
Applications include bicycle frames, helmets, and protective gear where lightweight strength is essential.
To wrap up, the closed molding process plays a vital role in modern composite manufacturing, offering a balance of quality, efficiency, and environmental sustainability. Whether through vacuum infusion, resin transfer molding, or compression molding, this technique allows manufacturers to create strong, durable, and visually appealing parts across various industries.
By using materials like epoxy resin, polyester resins, and high-strength fibers, along with tools like mold release agents and vacuum consumables, the closed molding process continues to be a key method in advancing composite manufacturing processes.
As technology evolves, the closed molding process will likely become even more efficient, supporting industries focused on innovation and sustainability.