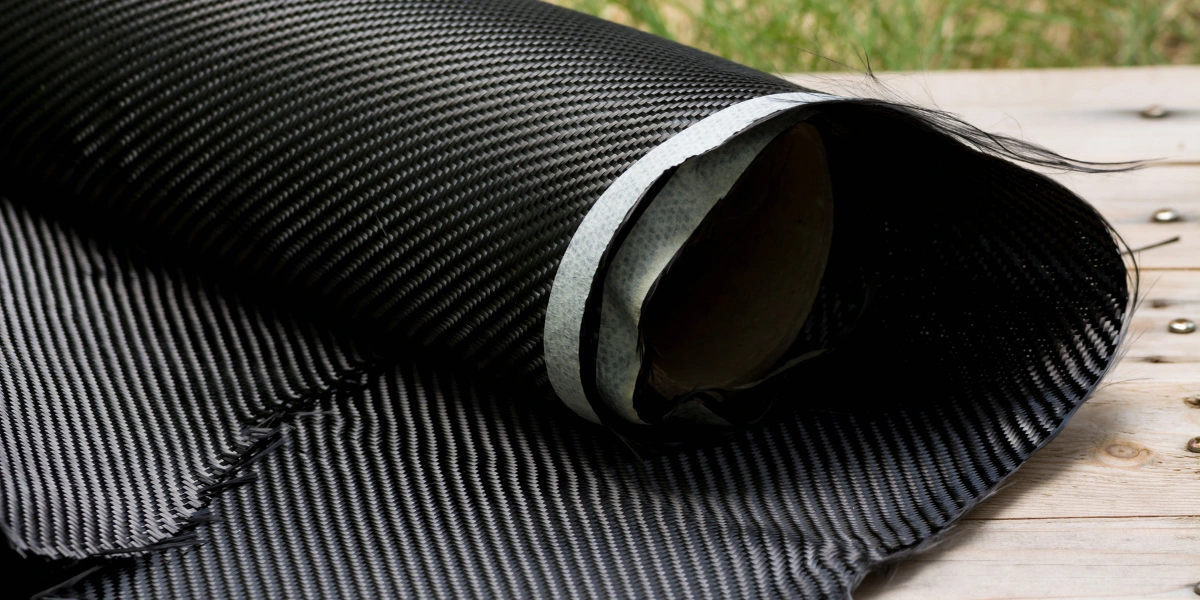
- Blog
- 25 Feb 2025
What is Automated Fiber Placement?
Automated Fiber Placement (AFP) is transforming the way composite materials are manufactured, offering unmatched precision and efficiency. This advanced technique uses robotic systems to place fiber materials like carbon fiber in carefully controlled patterns, creating lightweight yet strong components. Widely used in industries such as aerospace, automotive, and wind energy, AFP plays a vital role in producing durable and high-performance parts. In this blog, we’ll explore what Automated Fiber Placement is, how it works, its benefits, key applications, and the challenges faced when using this innovative technology.
What is Automated Fiber Placement?
Automated Fiber Placement (AFP) is an advanced manufacturing technique used in the composite materials industry for the precise placement of fiber materials, such as carbon fiber and glass fiber, onto a mold or tool. This process involves the use of a specialized machine to lay narrow, continuous strips of fiber material, called tows, in specific patterns to create strong, lightweight composite parts. AFP technology is widely used in industries requiring high-performance components, such as aerospace, automotive, and sports equipment manufacturing.
Key Components of the AFP Process
The Automated Fiber Placement process relies on several critical components working together to ensure accuracy and efficiency:
- AFP Machine: A robotic system equipped with a placement head designed to lay multiple tows of fiber material simultaneously. These machines can be programmed to control the speed, angle, and pressure for optimal fiber placement.
- Fiber Tow Supply: Rolls of carbon fiber, glass fiber, or other reinforcement materials, pre-impregnated with epoxy resin for easier bonding during the curing process.
- Tooling Surface: A mold or form where the fiber layers are applied. The tooling surface determines the final shape of the composite part.
- Compaction Rollers: These rollers press the fibers firmly onto the surface to eliminate gaps and ensure proper bonding between layers.
Benefits of Automated Fiber Placement
Automated Fiber Placement (AFP) offers significant advantages over traditional manual layup techniques, making it a preferred choice for manufacturing high-performance composite parts. One of its key benefits is enhanced precision, as the automated process ensures accurate fiber alignment, which improves the mechanical properties of the final component. Additionally, AFP reduces material waste by placing fibers with minimal overlap or gaps, optimizing resource use. The technology also boosts production speed since AFP machines work faster than manual methods, making them ideal for producing large or complex parts efficiently. Consistent quality is another advantage, as automated control minimizes human error, ensuring uniformity across all manufactured components. Furthermore, AFP enables the creation of complex designs and custom fiber patterns that would be challenging to achieve manually, expanding design possibilities in composite manufacturing.
Applications of Automated Fiber Placement
Automated Fiber Placement (AFP) plays a crucial role in various industries, especially where strong, lightweight composite materials are essential.
In the aerospace sector, AFP technology is widely used in the production of composites in aviation, contributing to the manufacturing of critical structural components such as wings, fuselage panels, and engine casings. These parts must withstand extreme forces while remaining lightweight to improve fuel efficiency and overall aircraft performance. The precision of AFP ensures optimal fiber alignment, enhancing the strength and durability of these essential components while reducing weight, a critical factor in aviation engineering.
In the automotive industry, AFP is used to create lightweight composite components that help improve both fuel efficiency and vehicle performance. Parts like body panels, roof structures, and chassis reinforcements benefit from AFP’s ability to produce strong yet light materials, which reduces the overall weight of the vehicle. This weight reduction contributes to lower fuel consumption and better handling, making AFP especially valuable in the production of high-performance sports cars and electric vehicles.
Within the wind energy sector, AFP technology is essential for manufacturing large wind turbine blades, where strength and flexibility are key. These blades must endure constant exposure to wind forces while maintaining structural integrity. AFP allows for precise placement of fiber materials along the blade’s length, ensuring balanced weight distribution and minimizing stress points. This results in longer-lasting and more efficient turbines capable of generating sustainable energy.
Sports equipment manufacturers also leverage AFP for producing high-performance gear where strength, lightweight properties, and durability are critical. Products such as bicycles, tennis rackets, golf clubs, and skis benefit from AFP’s ability to create optimized composite structures. The process allows for customized fiber placement, enhancing impact resistance and performance while keeping the equipment as light as possible for athletes.
Across all these industries, AFP continues to revolutionize composite manufacturing by combining strength, precision, and efficiency to meet modern engineering demands.
How Automated Fiber Placement Works
The AFP process involves a series of carefully controlled steps to ensure optimal fiber placement and part quality.
Preparation of the Fiber Material
Before the AFP machine begins, the fiber material is prepared. The fibers, often carbon fiber, are pre-impregnated with epoxy resin to ensure strong adhesion during curing. These materials are loaded onto the AFP machine in the form of narrow tows, each carefully aligned to avoid tangling or twisting.
Programming the AFP Machine
A critical step in the AFP process is programming the machine for the desired fiber placement pattern. Engineers create a digital model of the part and determine the optimal fiber orientation for strength and performance. Software controls the speed, angle, and pressure of the tows being placed, ensuring minimal waste and maximum efficiency.
Laying the Fibers with Precision
The AFP machine’s robotic arm lays the fibers onto the mold with exceptional precision. The compaction rollers ensure the fibers stay in place and adhere well. Each layer builds upon the previous one to create the composite part. Once the layers are complete, the part is prepared for curing, often using a vacuum bag process to remove air pockets and apply uniform pressure during the hardening phase.
Challenges in Implementing AFP Technology
While AFP offers significant advantages, it also presents certain challenges:
- High Initial Investment: The cost of FRP machines and advanced robotics can be substantial, limiting access for smaller manufacturers.
- Skilled Workforce Requirement: Programming and operating AFP machines require specialized training and experience.
- Material Handling: Proper storage and handling of fiber tows, especially carbon fiber supplements, are crucial to prevent contamination and ensure material integrity.
- Process Monitoring: Real-time quality control systems are necessary to detect issues like fiber misalignment or incomplete bonding.
Automated Fiber Placement continues to revolutionize the composite manufacturing industry with its precision, efficiency, and ability to produce high-performance parts across various sectors. As the technology evolves, it is expected to become more accessible, driving further innovations in lightweight, durable composite materials.