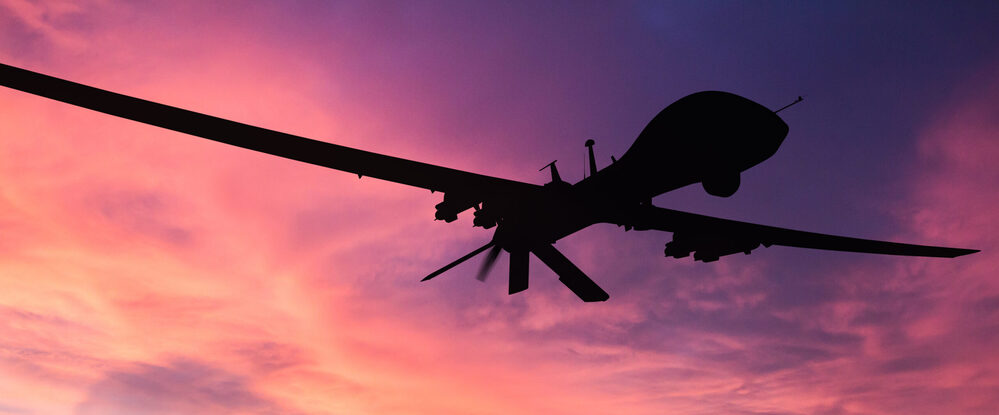
Aviation
The aviation industry has experienced a remarkable transformation in aircraft construction materials, shifting from traditional aluminum structures to advanced composites. This change has been driven by the limitations of aluminum, such as weight, strength, and corrosion resistance.
The advent of advanced composites, including carbon fiber reinforced polymers (CFRP) and fiberglass composites, has revolutionized the aerospace industry. These composites provide superior strength-to-weight ratios and enhanced performance compared to aluminum. The transition from metal to composite structures is motivated by the need for improved fuel efficiency, increased range, and reduced maintenance and operating costs in the composites in the aviation sector. The advantages of using composites in aircraft design are significant and far-reaching.
Evolution of Aviation Materials: From Aluminum to Advanced Composites
The odyssey from heavy, metal-laden airframes to sleek, composite-based structures marks a pivot in the annals of aviation history. This remarkable transition is not merely a story of material substitution but a revolution, propelled by relentless innovation in synthetic materials in aviation and engineering breakthroughs.
The Shift from Metal to Composite Structures
Tracing its lineage back to the gleaming bodies of aluminum that dominated the 20th-century skies, the aviation industry’s material paradigm has undergone a tectonic shift. Structural composites, championed by their superior mechanical properties, have edged out metals in a multitude of applications, forever altering the landscape of aircraft design. Pioneers in aerospace materials science have successfully leveraged the chemistry and physics of synthetic resins and fibers, giving birth to an era where lightweight aircraft materials reign supreme.
Impact of Composites on Aircraft Performance and Efficiency
This embrace of advanced composites has ushered in a new epoch characterized by improved flight dynamics and operational efficiency. The superior strength-to-weight ratios of composite materials afford considerable weight reductions, which in turn cascade into manifold performance enhancements. Modern aircraft, with bones of carbon fiber and sinews of polymer matrices, soar higher, faster, and longer – all the while sipping fuel with greater parsimony. The resulting leap in fuel economy and payload capacity reflects the profound impact high-performance, synthetic aviation materials have imprinted on the aerospace sector.
Advantages of Using Composites in Aircraft Design
Using composites in aircraft design offers numerous advantages that contribute to improved performance, reduced costs, and enhanced safety. Two key benefits of utilizing composites in aviation are weight reduction and fuel efficiency. Composites are significantly lighter than traditional materials, such as aluminum, resulting in reduced overall aircraft weight. This reduction in weight translates to improved fuel efficiency, as lighter aircraft require less power to propel and operate. As a result, operators can achieve cost savings through reduced fuel consumption and lower emissions, contributing to a more sustainable aviation industry.
In addition to weight reduction and fuel efficiency, composites also offer exceptional corrosion resistance and durability. Traditional aluminum structures are susceptible to corrosion, requiring frequent inspections and repair to maintain structural integrity. However, composites possess inherent corrosion resistance properties, eliminating the need for regular inspections and resulting in significant maintenance cost savings in the composites in aviation industry. Moreover, composites exhibit high durability and resistance to fatigue, ensuring extended service life for aircraft structures. This durability factor enhances the overall reliability of the aircraft, reducing the need for frequent repairs and replacements.
By leveraging composites in aircraft design, manufacturers and operators can benefit from the weight reduction, fuel efficiency, corrosion resistance, and durability of these advanced materials in composites in aviation. These advantages not only improve operational efficiency but also contribute to a more sustainable and cost-effective aviation industry.
Weight Reduction and Fuel Efficiency Benefits
The adoption of composites in aircraft construction has led to an impressive reduction in overall weight, a triumph of lightweight design that transcends traditional capabilities. This weight savings translates directly into fuel efficiency, a cornerstone of sustainable aviation. Not only does this mean that aircraft can now fly further on less fuel, but it also results in lower emissions and operational costs, aligning with the ever-growing environmental awareness and the need for greener solutions within the industry.
Corrosion Resistance and Durability Considerations
Beyond the benefits of weight and efficiency, composite materials stand tall against the harsh conditions faced in aviation. The innate corrosion resistance of composite structures showcases one of their strongest composite material advantages over metal alloys traditionally used in the aerospace sector. This resistance extends the lifespan of aircraft components and decreases the need for frequent maintenance, contributing to more sustainable operational practices and reinforcing the role of composites in fostering a new era of durable and resilient aircraft designs.
Types of Composites Utilized in Aircraft Construction
In aircraft construction, various types of composites are utilized to achieve optimal performance and efficiency. These composites offer a range of characteristics that make them suitable for different applications within the aircraft structure.
One of the most widely used composites in aviation is carbon fiber composites. These composites in aviation are renowned for their exceptional strength-to-weight ratio, making them ideal for critical load-bearing structures such as wings and fuselages. The high tensile strength and low weight of carbon fiber composites contribute to improved fuel efficiency and overall aircraft performance.
Fiberglass composites are another commonly employed option in aircraft construction. These composites in aviation strike a balance between cost, strength, and weight, making them suitable for secondary structures and fairings. Fiberglass composites offer good impact resistance and can withstand the environmental challenges faced by aircraft in operation.
Aramid fiber composites, such as Kevlar, find application in the construction of impact-resistant components and ballistic protection. These composites in aviation have excellent strength and stiffness properties, providing enhanced protection against impacts and ensuring the safety of critical areas within the aircraft.
By utilizing these different types of composites strategically, aircraft manufacturers can optimize the strength, weight, and durability of their products, ultimately improving the safety and performance of aircraft in operation.
Manufacturing Processes for Aviation Composites
Resin Transfer Molding (RTM) and its Applications
Resin Transfer Molding (RTM) is a widely used manufacturing process in the production of aviation composites. RTM involves injecting resin into a preform under controlled pressure, resulting in a high-quality composite structure with exceptional surface finish. This process in composites in aviation is particularly suitable for manufacturing complex shapes, making it an ideal choice for producing aircraft components such as wing skins and fairings.
Automated Fiber Placement (AFP) Technology
Automated Fiber Placement (AFP) technology plays a significant role in the manufacturing of aviation composites. This advanced technique allows for precise placement of carbon fiber tapes, enabling the creation of continuous and highly efficient composite structures. AFP technology in composites in aviation is commonly employed in the production of large-scale aircraft components such as fuselage sections and tail assemblies. By using AFP, manufacturers can reduce manufacturing time, improve overall quality, and achieve optimized performance in aircraft design.
Composites in Aviation: Enhancing Safety and Performance
The use of composites in aviation has revolutionized aircraft construction, leading to significant improvements in both safety and performance.
Composites provide enhanced structural integrity, minimizing the risk of catastrophic failure. The exceptional stiffness and strength of composites contribute to improved aerodynamic efficiency, enhancing aircraft performance, maneuverability, and reducing drag.
Furthermore, composites offer inherent damage tolerance properties, enabling structures to withstand impacts and reducing the likelihood of damage propagation. This translates to increased safety and durability for aircraft components.
From wings to fuselages, the integration of composites in aviation construction has ushered in a new era of flight, where safety is paramount, and performance is optimized. The industry continues to embrace composites as the go-to material for achieving superior safety standards and enhancing overall aircraft performance.
Challenges and Solutions in Composite Aircraft Maintenance
Composite aircraft maintenance poses unique challenges due to the complex nature of composite structures in aviation and the need for specialized repair techniques. Unlike traditional aluminum structures, composites require specific expertise and procedures to ensure their integrity and longevity in the aviation industry.
To address these challenges, non-destructive testing (NDT) techniques play a crucial role in ensuring the safety and performance of composite structures in aviation. Methods such as ultrasonic inspection and thermography are employed to detect hidden defects or damage within the composite materials without causing further harm. By identifying issues early on, aircraft maintenance professionals can take prompt action and prevent potential failures that could compromise the aircraft’s structural integrity.
When it comes to repairing composite aircraft structures, careful attention must be paid to both the expertise of the technicians and the materials used in composites in aviation. Skilled technicians with specialized knowledge in composite repairs are required to perform the repairs effectively and ensure the structural integrity of the aircraft. Advanced repair materials, such as high-quality epoxy resins and carbon fiber patches, are utilized to restore damaged composite components in a way that maintains their strength and durability.
Proper repair procedures are equally vital in composite aircraft maintenance in aviation. Surface preparation, bond quality inspection, and vacuum bagging are among the essential steps to achieve optimal repair results. Thoroughly preparing the damaged area, rigorously inspecting the bond quality, and using vacuum pressure during the curing process help guarantee that the repaired composite components meet the required standards for structural integrity and operational safety.
Non-Destructive Testing (NDT) Techniques for Composites
Composite aircraft structures present unique maintenance challenges, particularly when detecting subsurface damage that is invisible to the naked eye. To uphold rigorous aviation industry standards, non-destructive inspection methods have significantly developed to identify such imperfections. Techniques such as ultrasonic testing, thermography, and radiography are at the forefront of NDT innovations. These methods offer a window into the internal condition of composite materials, enabling technicians to diagnose and remedy issues without causing further harm. This vigilant attention to detail is essential for maintaining the structural health and overall safety of composite aircraft.
Addressing Repair Issues for Composite Aircraft Structures
When it comes to repairing composite structures, the aviation industry is continually refining its composite repair techniques. Traditional methods are often inadequate due to the specialized nature of these materials. Repair personnel must be extensively trained in advanced techniques such as bonding and patching, which require precision and adherence to exacting standards. By leveraging innovative solutions and best practices, maintenance teams can perform effective repairs that align with stringent safety regulations. These advancements underscore a commitment to not just maintaining, but enhancing the reliability and durability of composite aircraft for years to come.