Fillers
Composite filling refers to the incorporation of fillers into a polymer matrix to enhance or modify the properties of the composite material. These fillers, which can be particulate, fibrous, or in other forms, are distributed throughout the matrix to improve mechanical strength, thermal properties, and dimensional stability, among other characteristics. Composite fillings are integral to the design and manufacturing of composite materials, allowing for the creation of products that meet specific requirements for a wide range of applications, from automotive and aerospace components to consumer goods and construction materials. By selecting appropriate fillers, manufacturers can tailor the performance of composites to achieve desired outcomes in terms of durability, cost-effectiveness, and environmental impact.
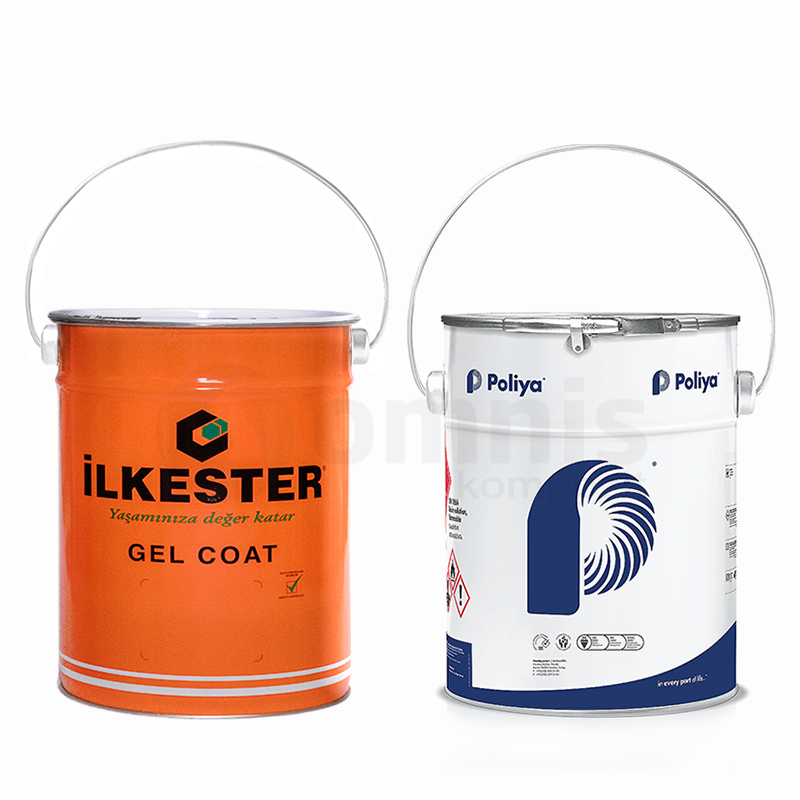
Adhesives
Review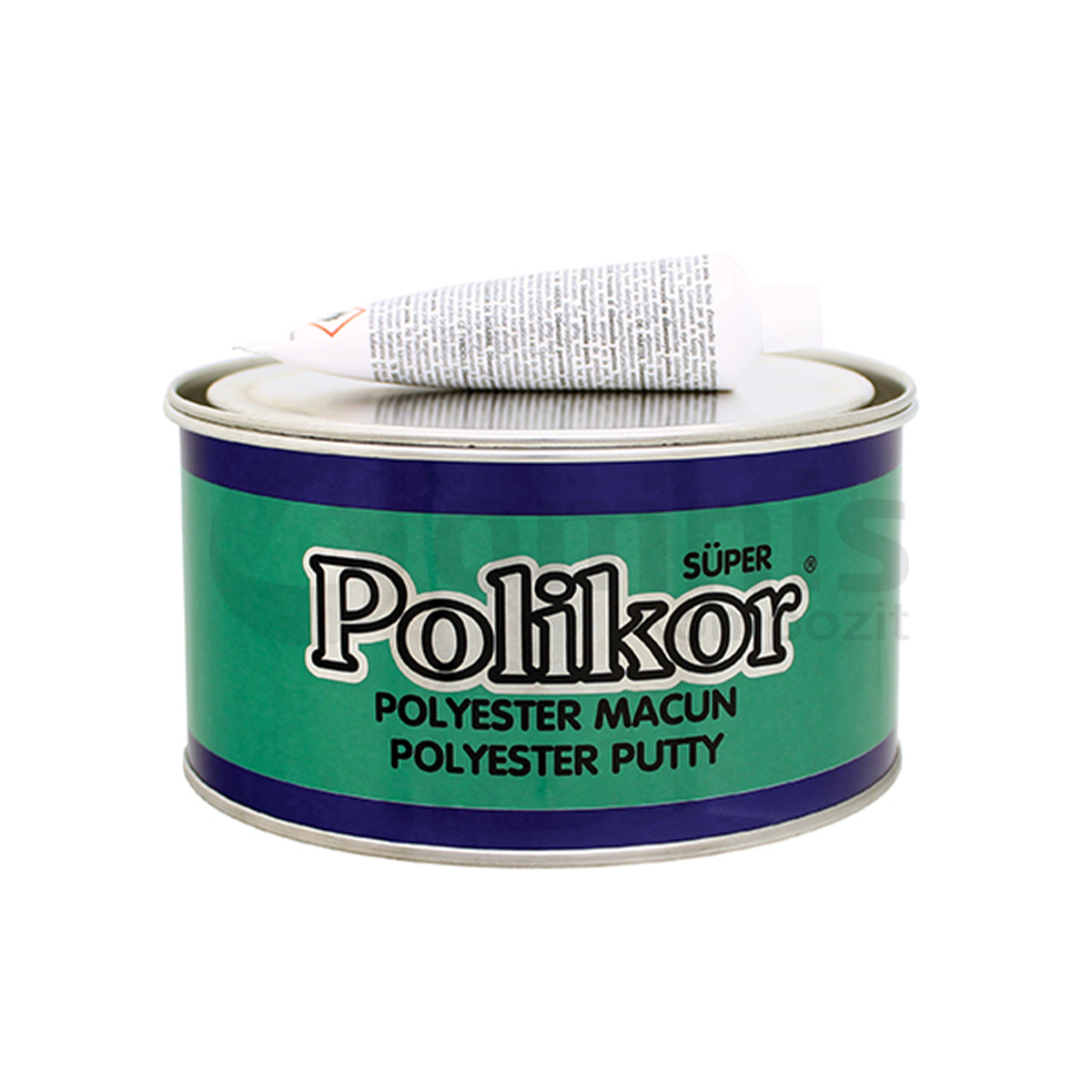
Polyester Putties
Review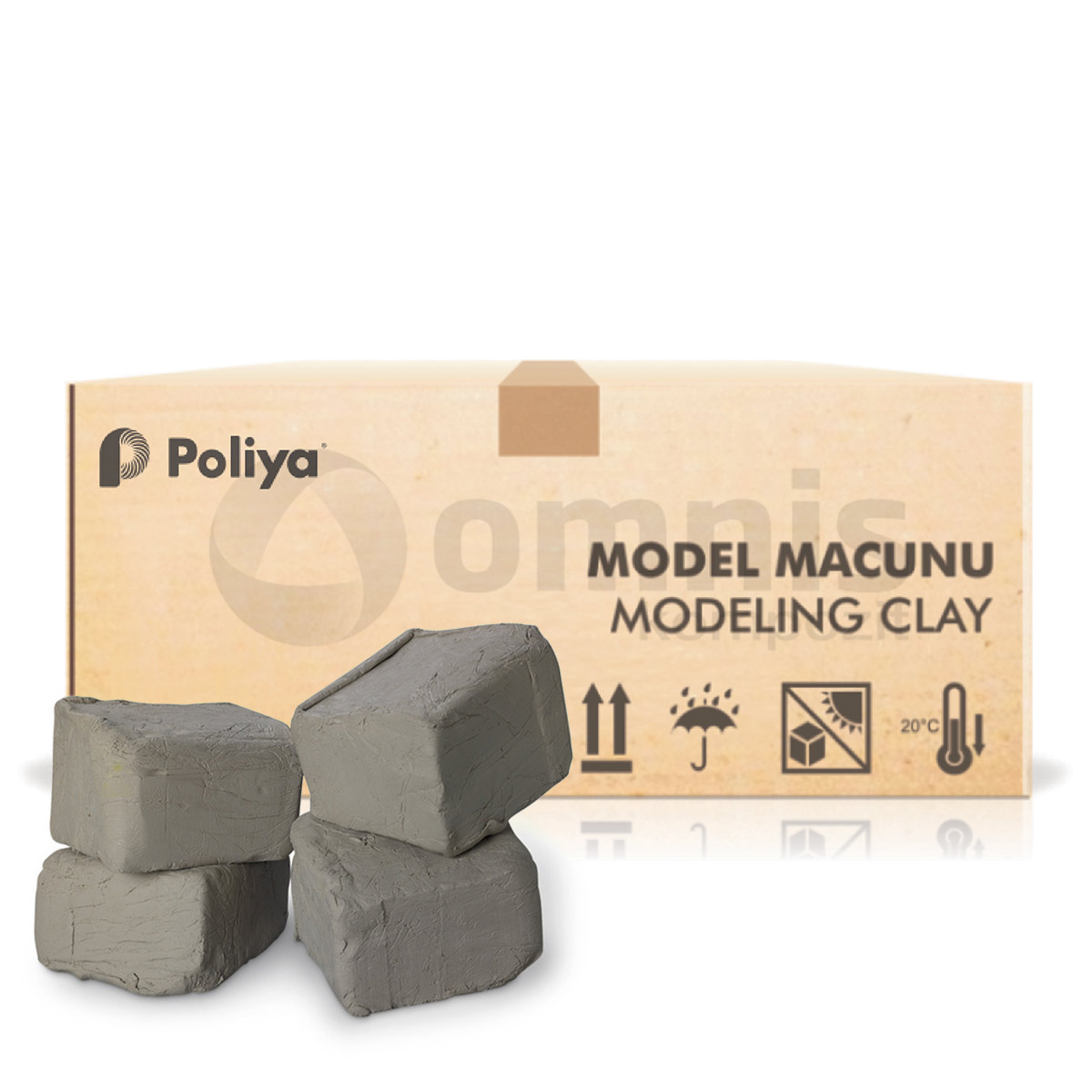
Model Paste
Review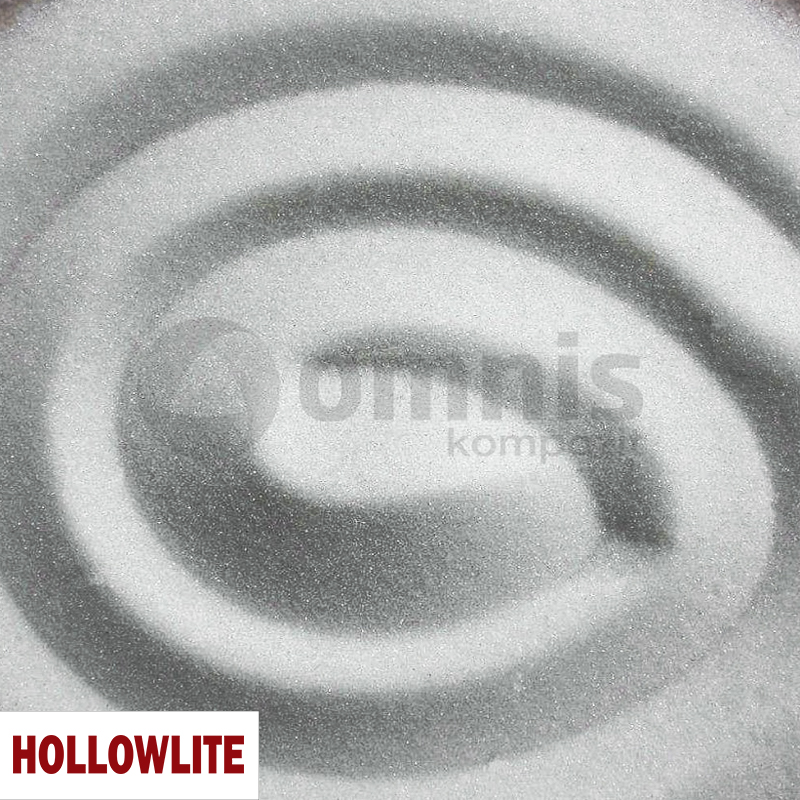
Hollow Glass Ball
Review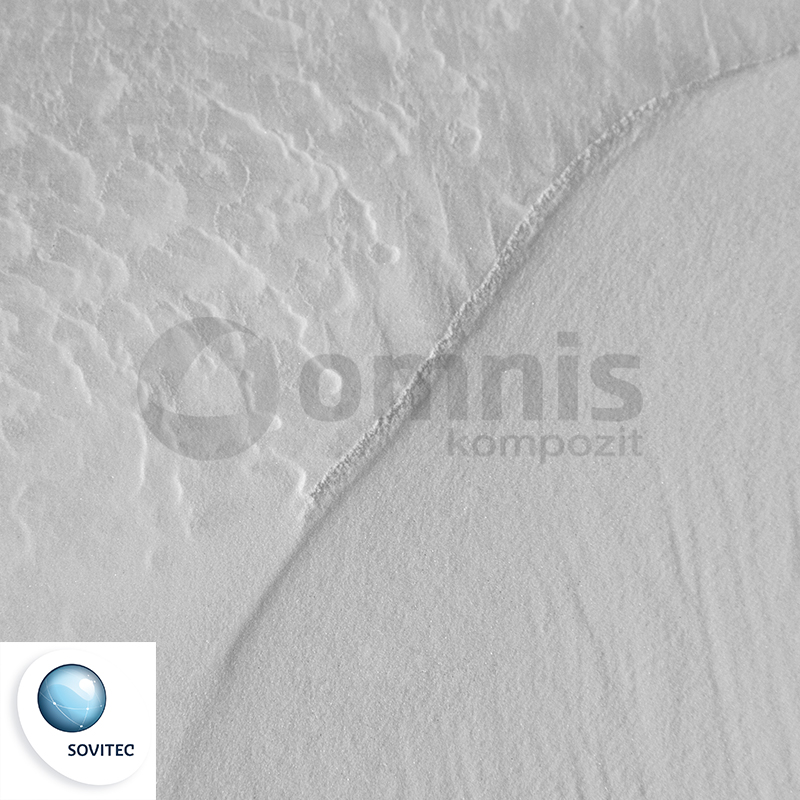
Filled Glass Ball
Review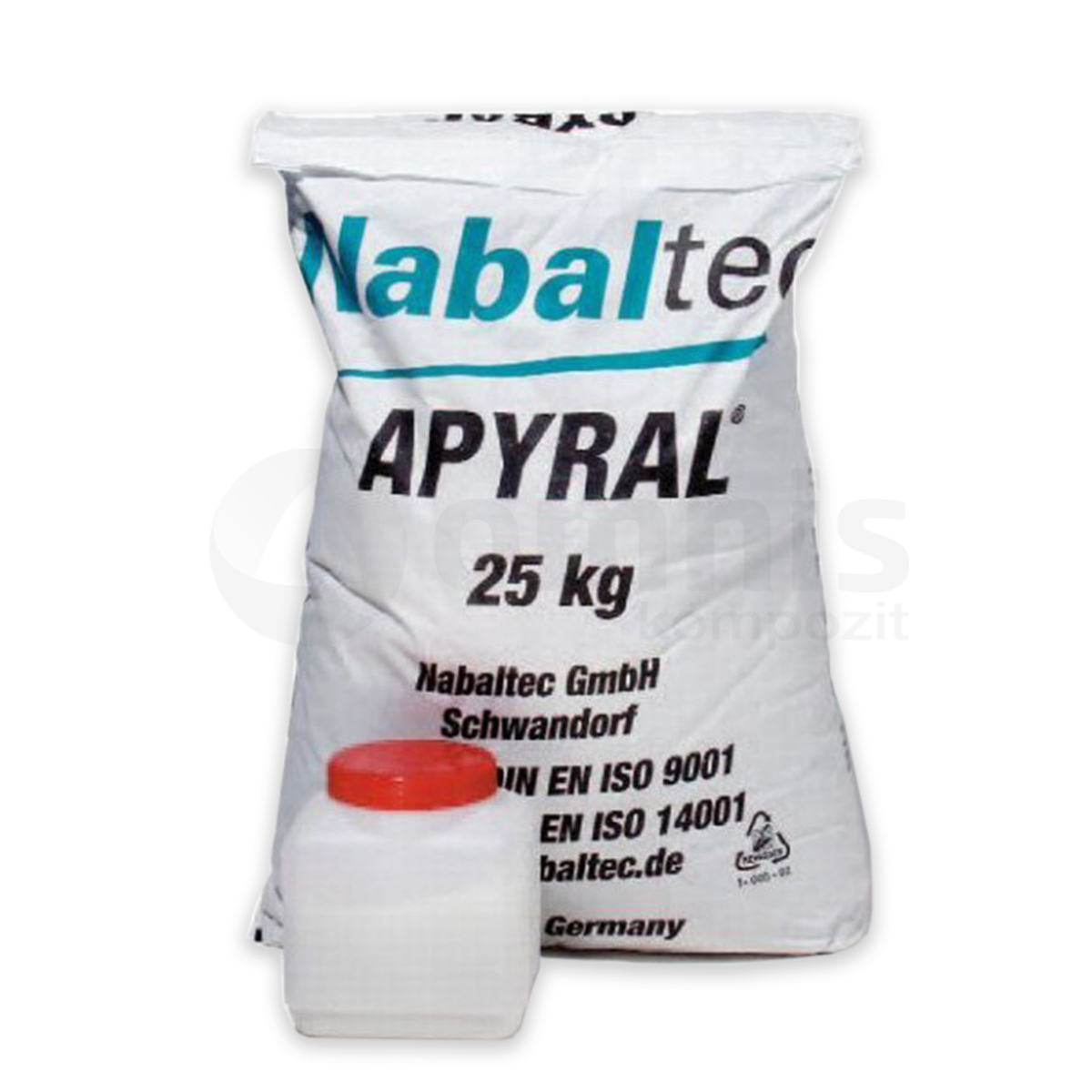
ATH Flame Retardant Filler-Apyral 16
Review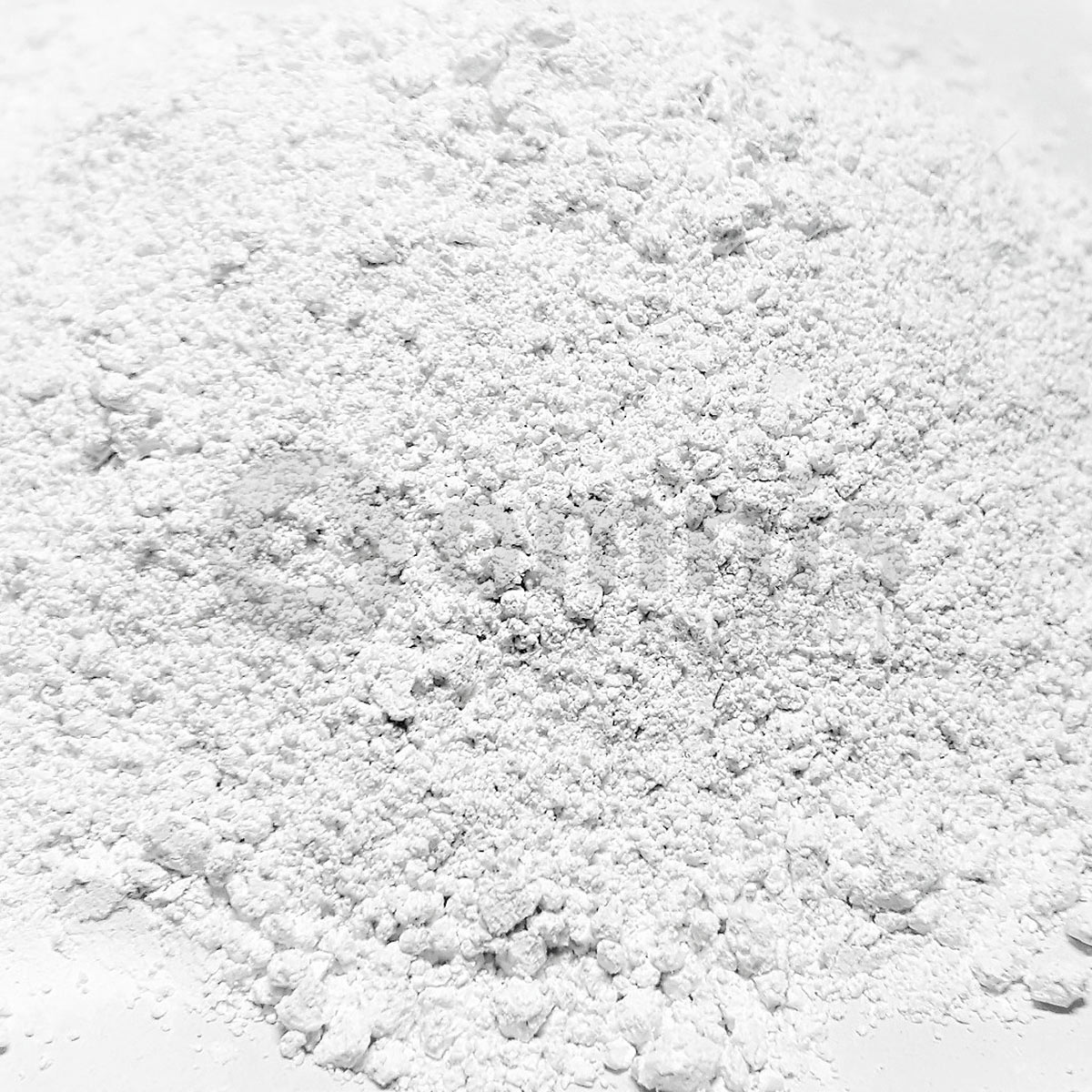
Talk
Review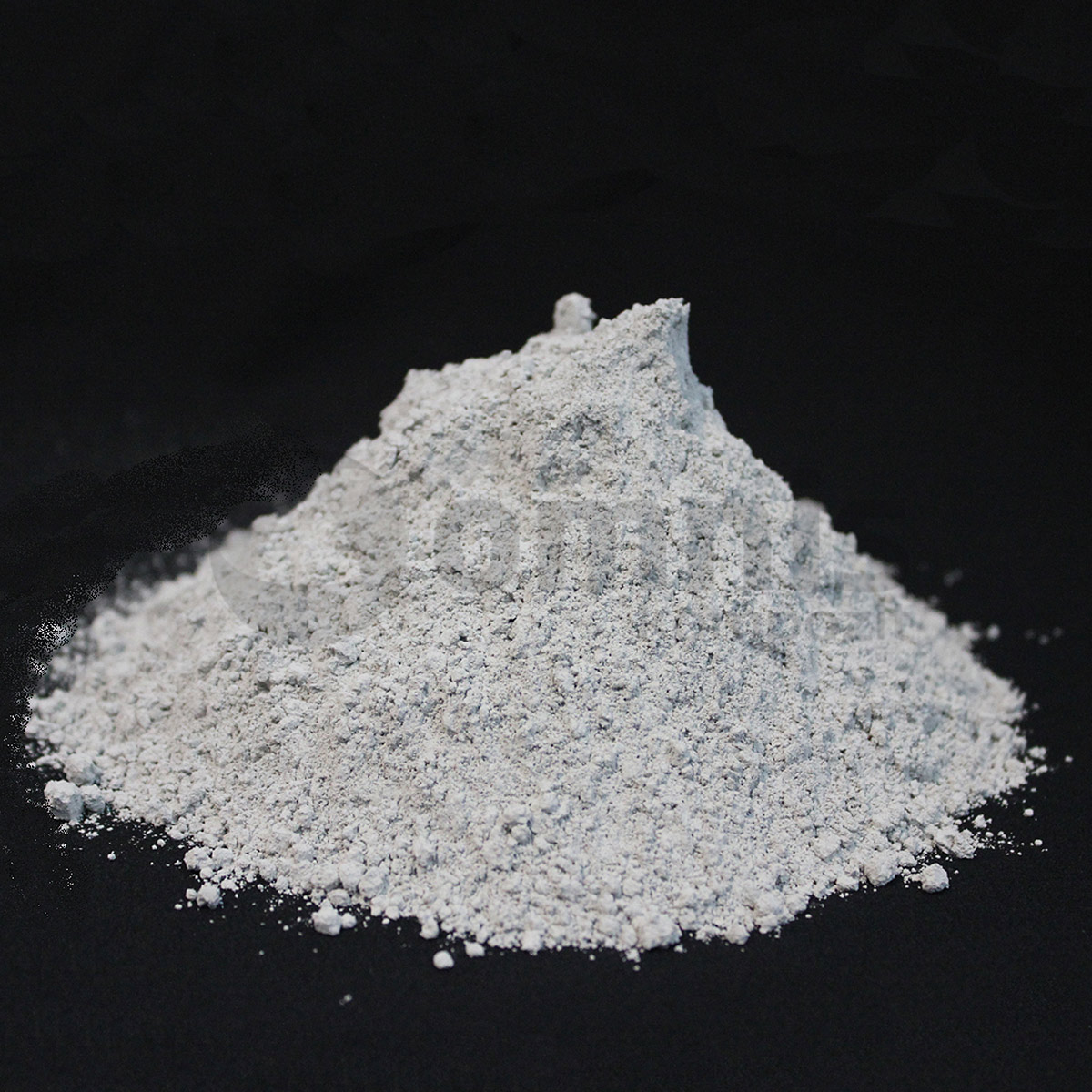
Calcite
Review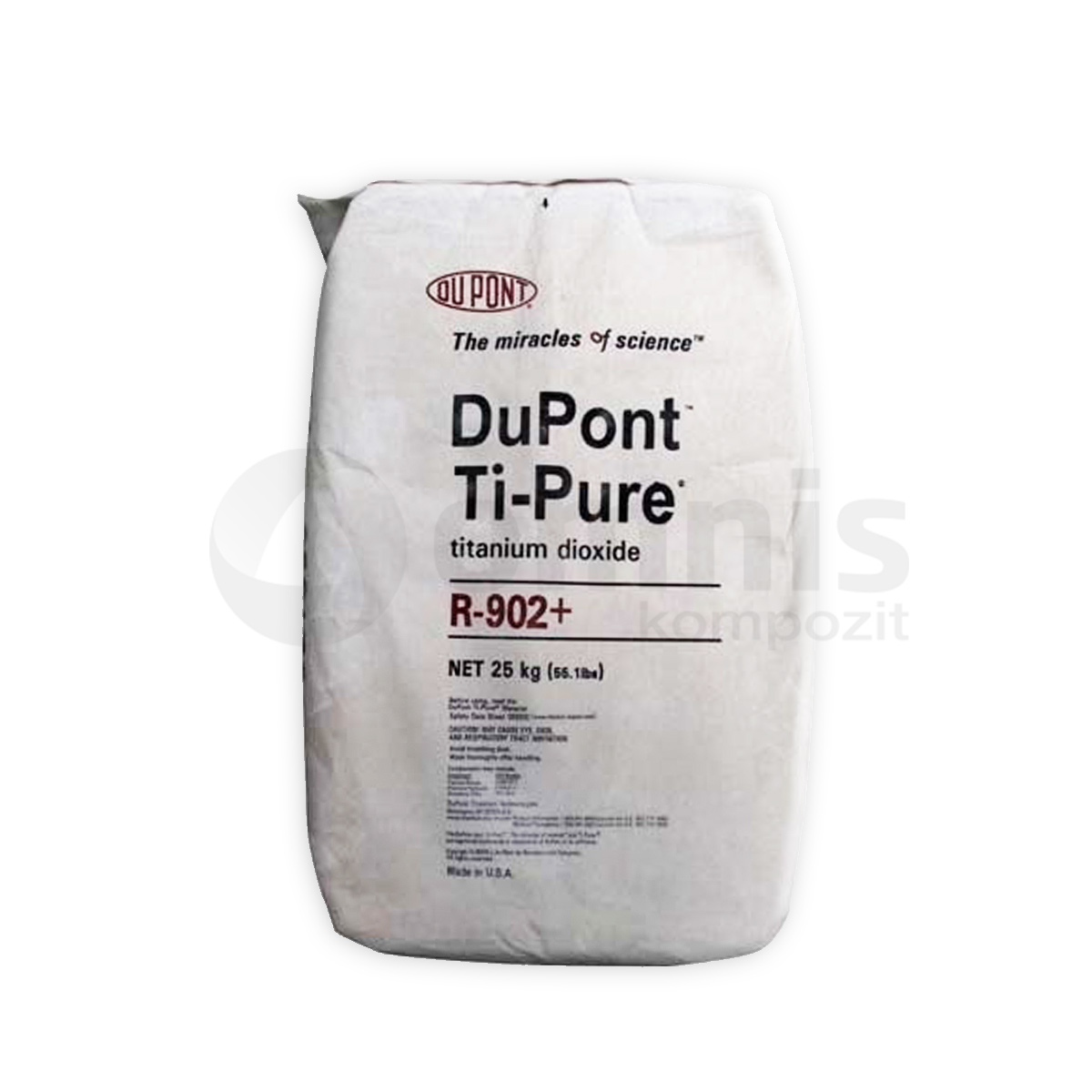
Titan Dioxide R-902
Review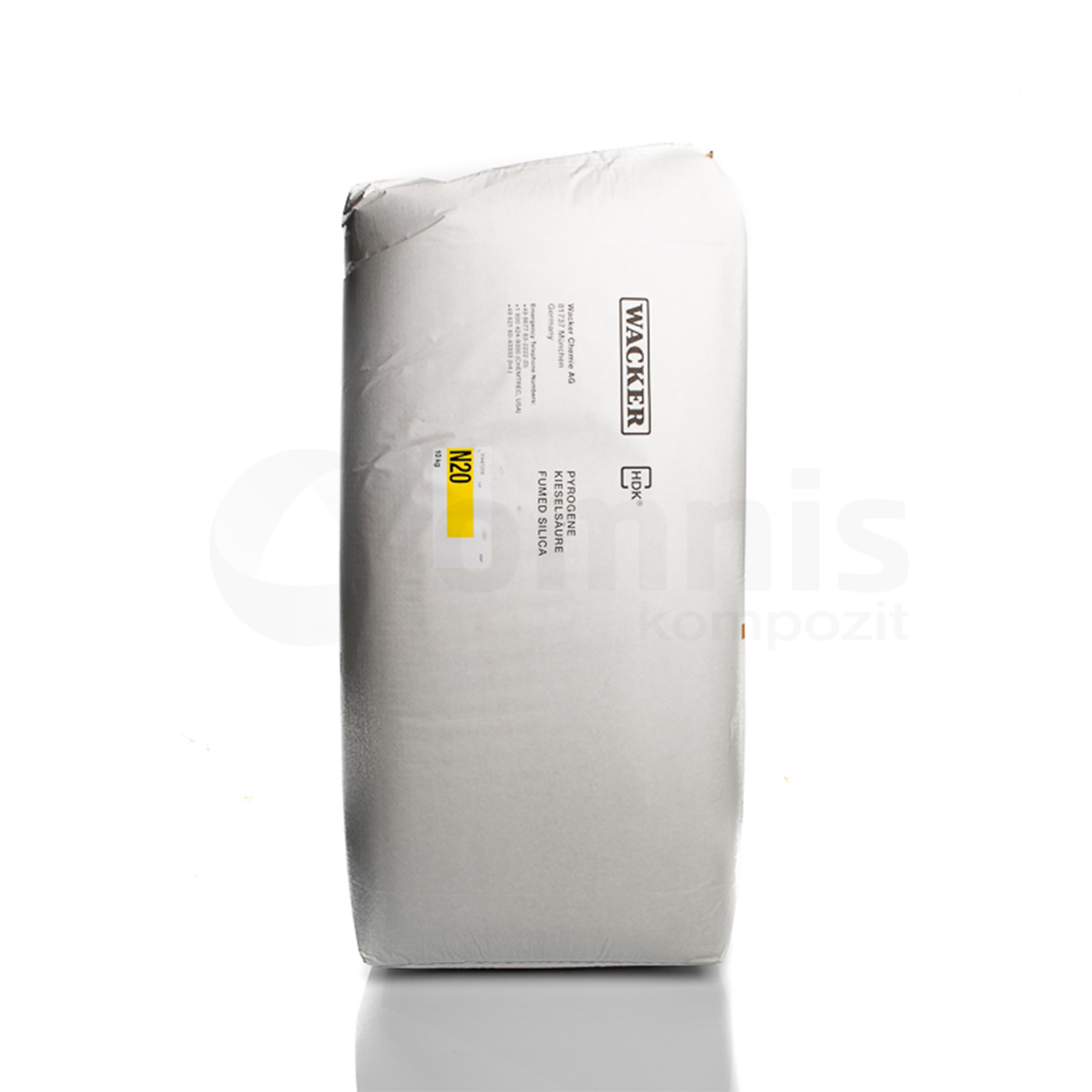
Fume Silica Thickener
Review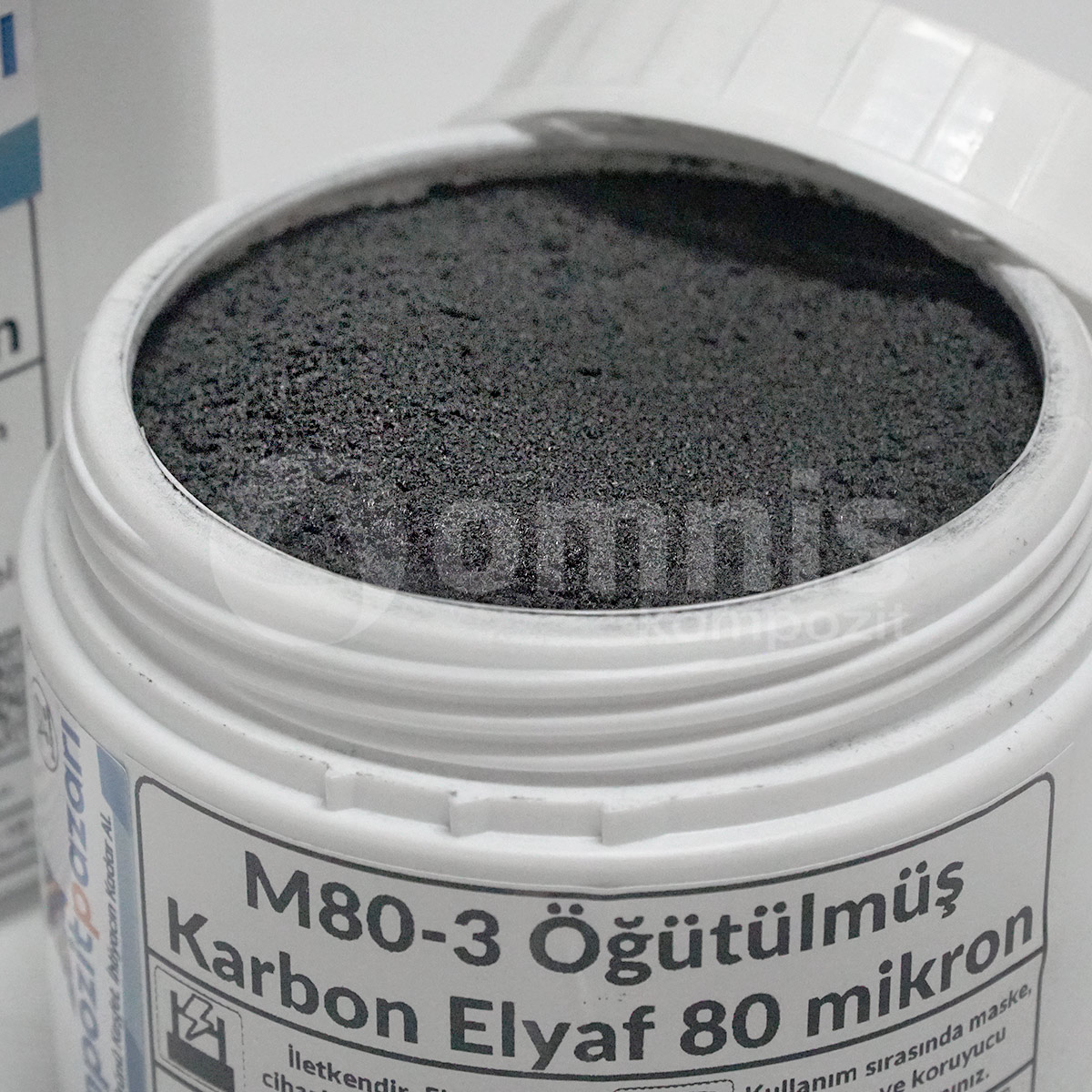
Ground Carbon Fiber
Review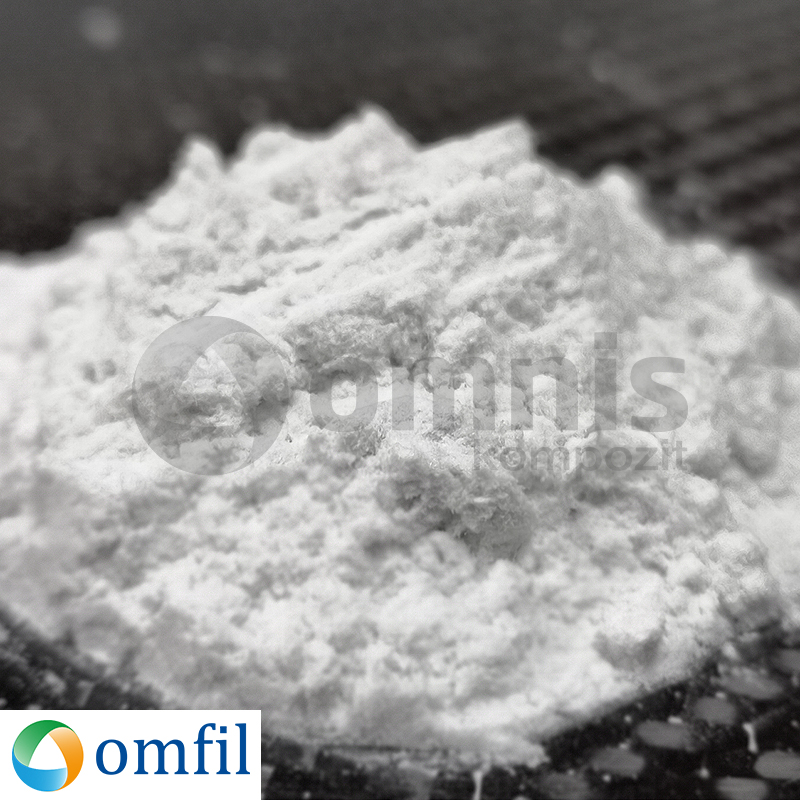
OMFIL Ground E-Glass
Review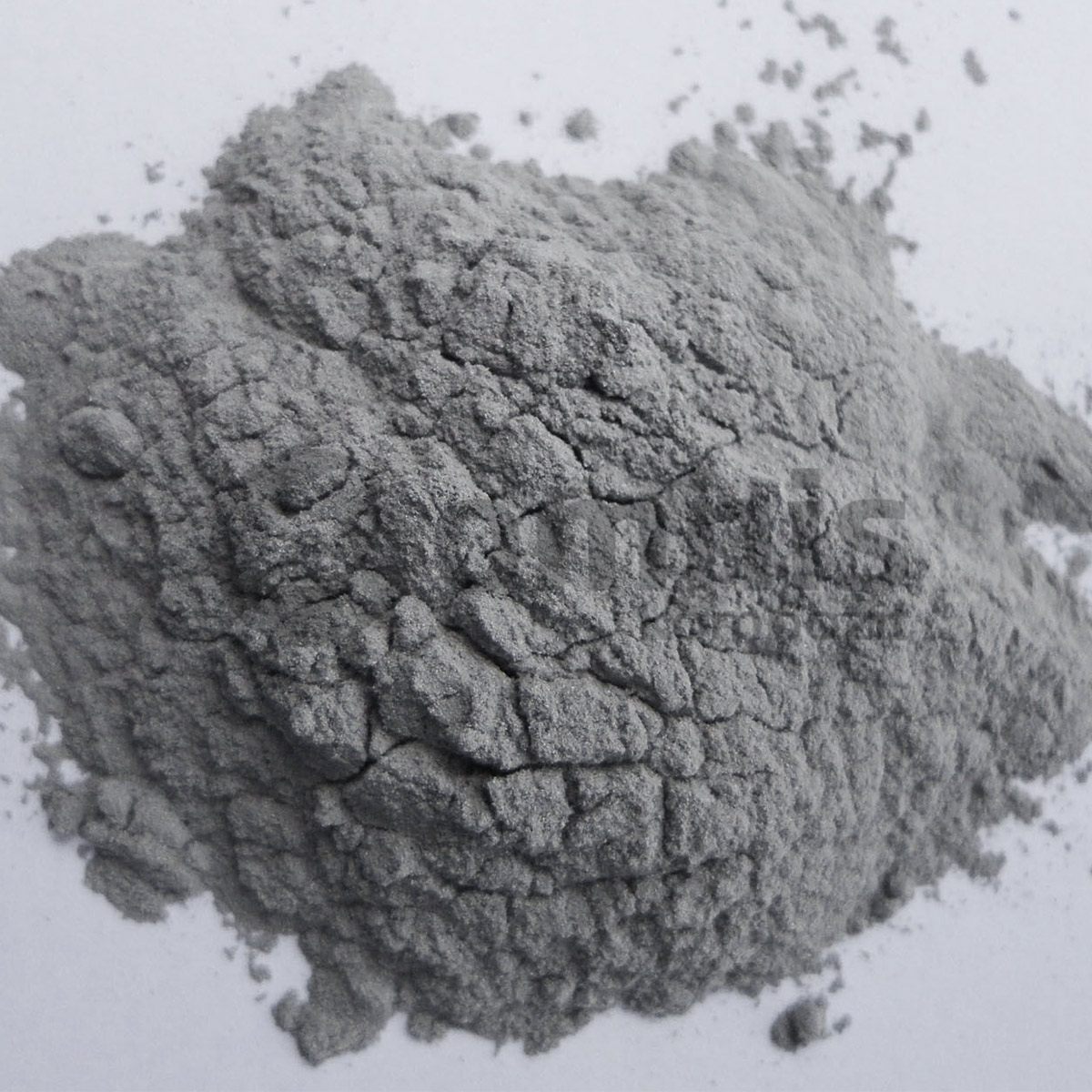
AL 100 Aluminum Powder
Review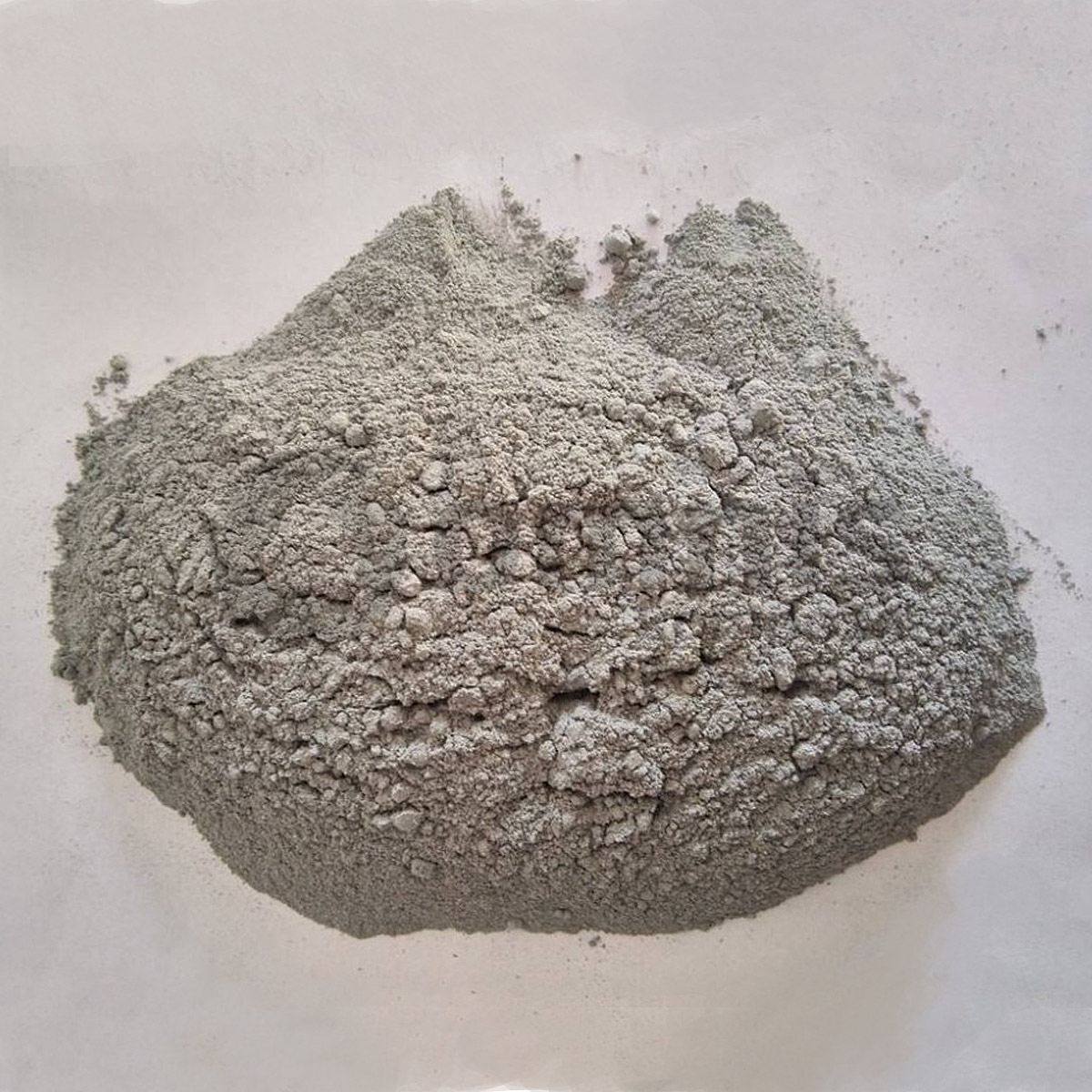
Micro Silica-Silica Ash-Fume
Review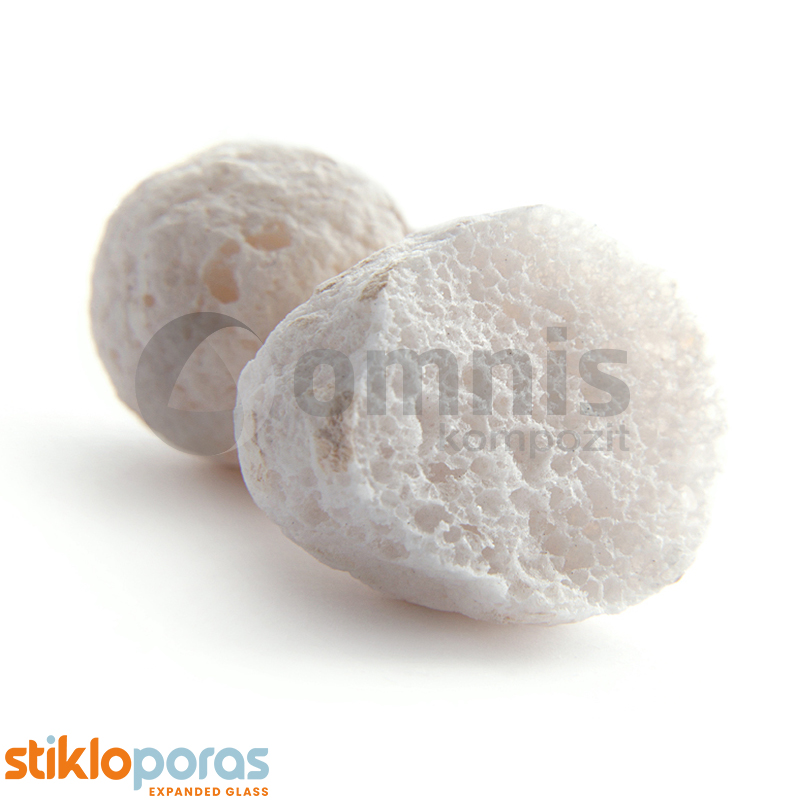
Stikloporas Expanded Glass
ReviewHow do mineral fillers enhance composite materials?
Mineral fillers enhance composite materials by improving their mechanical properties, reducing production costs, and modifying aesthetic qualities. These fillers, derived from natural or synthetic minerals, can increase the stiffness, strength, and thermal stability of composites while also improving their wear resistance and reducing shrinkage during curing. Additionally, mineral fillers can make composite materials more cost-effective by replacing a portion of the more expensive polymer matrix without significantly compromising the material’s overall performance. By carefully selecting and incorporating mineral fillers, manufacturers can achieve a balance between performance, appearance, and cost in their composite products.
What are the most common types of mineral fillers used in composites?
The most common types of mineral fillers used in composites include calcium carbonate, silica (quartz), talc, mica, and glass fibers. Calcium carbonate is widely used for its cost-effectiveness and ability to improve mechanical properties. Silica is chosen for its hardness and thermal stability, enhancing wear resistance and dimensional stability. Talc is utilized for its platy morphology, which improves barrier properties and stiffness. Mica is selected for its thermal stability and electrical insulation properties. Glass fibers, while not a mineral in the traditional sense, are commonly used to significantly enhance the strength and stiffness of composites. Each of these fillers offers unique benefits, making them suitable for specific applications within various industries.
How do I choose the right filler for my composite application?
Choosing the right filler for your composite application involves considering several factors, including the desired mechanical properties, thermal behavior, electrical characteristics, and cost constraints of the final product. Assess the compatibility of the filler with the polymer matrix, as well as its impact on processing conditions and the composite’s overall performance. Environmental and health safety aspects of the filler material should also be taken into account. Consulting with filler suppliers and conducting experimental trials can provide valuable insights into the effects of different fillers on your composite’s properties, helping you make an informed decision.
What are the benefits of using composite fillings in manufacturing?
Using composite fillings in manufacturing offers numerous benefits, including enhanced mechanical properties, improved thermal and electrical performance, reduced material costs, and the ability to tailor composites to specific application requirements. Fillers can increase the strength, stiffness, and impact resistance of composites, as well as improve their resistance to heat, wear, and corrosion. By adjusting the type and amount of filler, manufacturers can optimize the balance between performance and cost, enabling the production of high-quality composite materials that meet or exceed the demands of various industries.
Can mineral fillers improve the thermal properties of composites?
Yes, mineral fillers can significantly improve the thermal properties of composites. Fillers such as silica, alumina, and boron nitride are known for their high thermal conductivity and can be used to enhance the heat dissipation of composite materials, making them suitable for applications requiring efficient thermal management. Additionally, certain mineral fillers can increase the thermal stability and fire resistance of composites, allowing them to maintain their structural integrity and performance at higher temperatures or in fire-prone environments.
How do fillers affect the mechanical properties of composite materials?
Fillers affect the mechanical properties of composite materials by increasing their stiffness, strength, and impact resistance. The specific effects depend on the type, shape, size, and distribution of the filler particles within the polymer matrix. Properly selected and dispersed fillers can create a more uniform stress distribution within the composite, enhancing its load-bearing capacity and resistance to deformation. However, excessive filler content or poor dispersion can lead to agglomeration, reducing the composite’s toughness and leading to potential failure points.
What are the environmental impacts of using mineral fillers in composites?
The environmental impacts of using mineral fillers in composites vary depending on the type of filler, its source, and the lifecycle of the composite product. Natural mineral fillers, if sourced responsibly, can have a lower environmental footprint compared to synthetic fillers or pure polymer materials. However, the extraction and processing of minerals can contribute to environmental degradation if not managed sustainably. Incorporating fillers can also affect the recyclability and biodegradability of composite materials. Selecting eco-friendly fillers and considering the end-of-life options for composite products are important steps in minimizing their environmental impact.
How do mineral fillers contribute to the durability of composite materials?
Mineral fillers contribute to the durability of composite materials by enhancing their wear resistance, thermal stability, and resistance to environmental factors such as UV radiation, moisture, and chemicals. The improved mechanical properties provided by fillers can also reduce the likelihood of cracks and fractures under load, extending the lifespan of composite products. By carefully selecting appropriate fillers, manufacturers can create composites that maintain their performance and appearance over time, even in harsh operating conditions.
Can composite fillings be used in both thermoset and thermoplastic matrices?
Yes, composite fillings can be used in both thermoset and thermoplastic matrices. The choice of filler and its compatibility with the polymer matrix are crucial for ensuring optimal performance and processing characteristics. In thermoset composites, fillers can enhance mechanical properties and reduce curing shrinkage. In thermoplastic composites, fillers can improve stiffness, strength, and thermal properties while also influencing the material’s flow behavior during processing. The specific requirements of the application and the characteristics of the polymer matrix will determine the most suitable type of filler.
What are the challenges associated with mixing fillers into composite materials?
The challenges associated with mixing fillers into composite materials include achieving uniform dispersion, preventing agglomeration, and maintaining the desired viscosity and processing characteristics of the composite. Inadequate dispersion can lead to weak points in the material, affecting its mechanical properties and overall performance. Additionally, high filler loadings can increase the viscosity of the composite mixture, making it difficult to process and potentially affecting the surface finish of the final product. Addressing these challenges requires careful selection of filler materials, optimization of mixing techniques, and possibly the use of dispersing agents or compatibilizers.
How do mineral fillers affect the surface finish of composite products?
Mineral fillers can affect the surface finish of composite products in several ways. While they can improve the hardness and scratch resistance of the surface, high concentrations or poor dispersion of fillers can lead to a rough or uneven surface appearance. The size and shape of the filler particles also play a significant role in determining the surface quality. Fine, well-dispersed fillers can contribute to a smooth, aesthetically pleasing finish, whereas larger or irregularly shaped particles may result in surface defects. Proper processing techniques and finishing operations can help mitigate these effects and achieve the desired surface quality.
How do I calculate the correct amount of filler to use in my composite mixture?
Calculating the correct amount of filler to use in your composite mixture involves considering the desired properties of the final product, the characteristics of the filler and the polymer matrix, and the processing conditions. Start by determining the target mechanical, thermal, and aesthetic properties. Then, consult literature, material data sheets, and guidelines from filler suppliers to understand the effects of various filler loadings. Experimental trials are often necessary to optimize the filler content, balancing performance enhancements with potential drawbacks such as increased viscosity or processing difficulties. Mathematical models and software tools can also assist in predicting the effects of filler additions and guiding the formulation process.