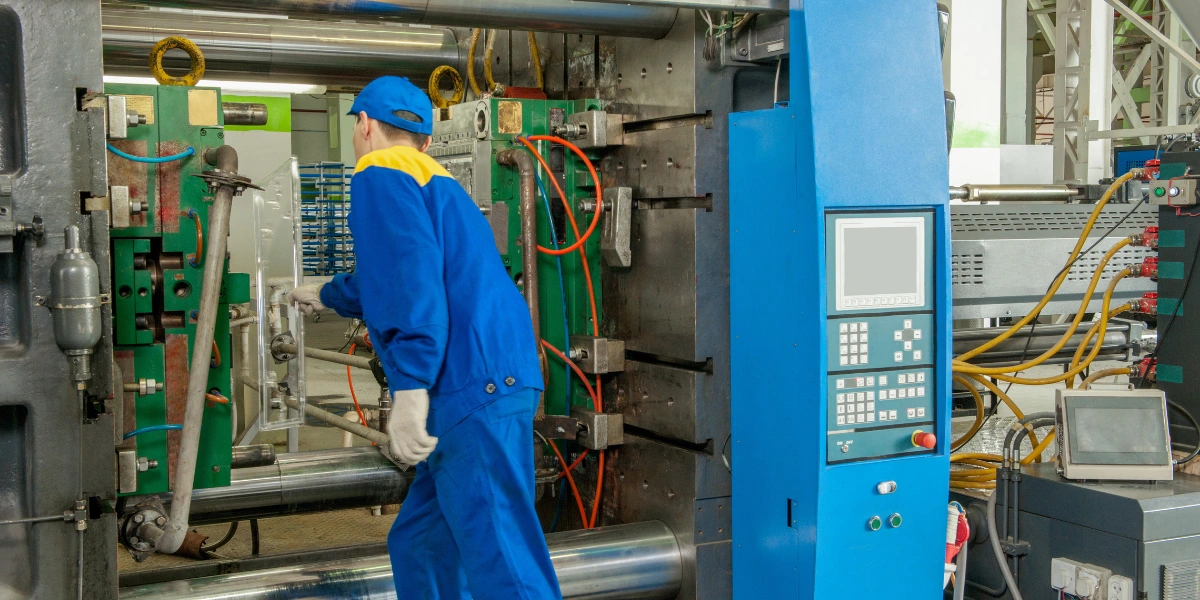
- Blog
- 24 Apr 2025
What Is Resin Transfer Molding?
In the world of composite manufacturing, resin transfer molding (RTM) stands out as a reliable and efficient method for producing strong, lightweight parts with a smooth surface finish. Often used in industries like automotive, aerospace, and dental tools, this method combines precision with repeatability. RTM is a closed molding process, which means the resin is injected into a sealed mold where the reinforcement material is already placed. This technique helps minimize waste and ensures high-quality results. Whether you’re new to composite materials or looking to improve your production process, understanding how resin transfer molding works can help you make smarter decisions.
Understanding Resin Transfer Molding
RTM is a method used to make high-quality composite parts by injecting resin into a closed mold that already contains a fiber reinforcement—such as fiberglass or carbon fiber. This process is known for producing strong and precise components with a clean surface finish on both sides.
Unlike open molding methods, RTM keeps everything sealed during production. This helps reduce air bubbles, improves consistency, and makes the final product more durable. It also creates less mess, which is great for maintaining a cleaner working environment.
One thing that sets RTM apart from other techniques like injection molding is the way the resin flows. In RTM, the resin is pulled or pushed through the fibers inside the mold, fully soaking them. Materials like epoxy resin are commonly used because they offer strong bonding, heat resistance, and a long lifespan.
Since this process is part of the closed molding process family, it’s also more environmentally friendly, as it reduces emissions and material waste. Plus, with the help of tools like vacuum equipment, air is removed from the mold before resin is injected, ensuring fewer defects in the final product.
How Does Resin Transfer Molding Work?
The resin transfer molding process happens in a few clear steps. First, the mold is prepared, then resin is injected into it, and finally, the part is cured and removed. Each stage plays an important role in making sure the final composite part is strong, precise, and ready to use.
Mold Preparation
Before anything else, the mold must be clean and treated with a release agent to stop the part from sticking. The reinforcement material—like fiberglass or carbon fiber—is carefully placed inside the mold. The mold is then sealed tightly to create a closed environment for the resin to flow. At this point, vacuum equipment may be used to remove air, preventing bubbles and ensuring the resin will fully saturate the fibers.
Resin Injection
Next, the liquid resin is injected into the mold under pressure. The resin flows through the fiber reinforcement, filling every space. This step must be done carefully to avoid dry spots or uneven distribution. Using the right type of resin, such as epoxy resin, is important for getting strong and durable results.
Curing & Demolding
After injection, the mold is heated to cure the resin. This hardens the material and locks everything in place. Once curing is complete, the mold is opened and the part is taken out. The result is a smooth, high-strength component with excellent performance and stability.
Advantages of Resin Transfer Molding
Resin transfer molding offers several key benefits that make it a popular choice across many industries—from automotive and aerospace to dental and medical applications.
One of the biggest advantages is the high-quality surface finish on both sides of the part. Because it’s a closed molding process, there’s better control over the shape and texture of the final product. This reduces the need for extra sanding or finishing work.
Another benefit is material efficiency. Since the resin is injected directly into the mold, there’s less waste compared to open molding. This not only saves money but also makes the process more eco-friendly.
RTM also supports strong mechanical properties. The resin fully saturates the fiber reinforcement, creating lightweight but durable parts. These parts perform well under stress, making them perfect for high-performance environments.
Finally, RTM is great for medium to high-volume production. Once the mold is set up, it’s easy to repeat the process, allowing manufacturers to produce consistent parts with high accuracy—just like in injection molding, but with more flexibility in material choice.
Applications of Resin Transfer Molding
Resin transfer molding is used in many industries thanks to its ability to produce strong, lightweight, and detailed parts. Its flexibility makes it ideal for both technical and cosmetic applications.
In the automotive industry, RTM is used to create body panels, bumpers, and structural parts that need to be tough but lightweight. The smooth surface finish also means less work is needed before painting or coating.
In aerospace, weight and strength are critical. RTM helps produce interior panels, brackets, and other components that must meet high safety standards while keeping the aircraft light.
For medical and dental tools, RTM offers the precision needed to produce clean, detailed parts with minimal defects. Its compatibility with materials like epoxy resin ensures long-term durability and chemical resistance—key in clinical settings.
RTM is also gaining popularity in sports equipment, such as bike frames, helmets, and rackets, where performance and weight are essential. In all these areas, resin transfer molding delivers consistent quality and reliability.
RTM is a smart and efficient way to create high-performance composite parts. Its ability to produce strong, lightweight, and visually clean components makes it a go-to solution in many industries—from automotive to medical. As a closed molding process, it reduces waste, improves quality, and supports medium to high-volume production. By using materials like epoxy resin and tools such as vacuum equipment, manufacturers can achieve excellent results with great consistency. Whether you’re improving your production line or exploring new materials, resin transfer molding offers a reliable and cost-effective path forward.