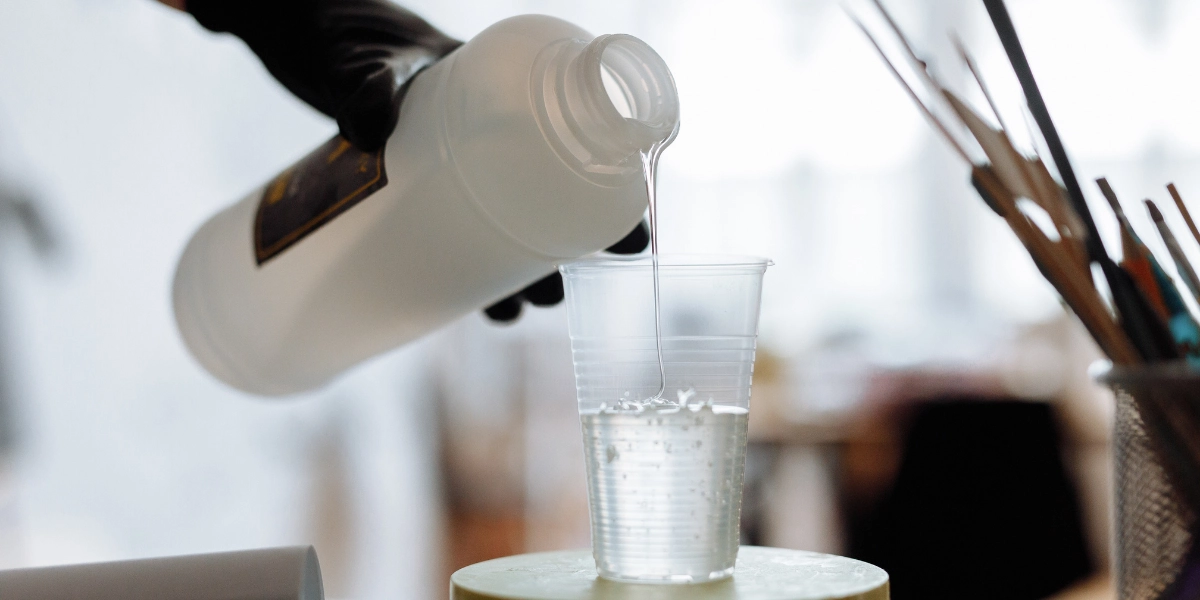
- Blog
- 27 Jun 2025
What are the Types of Resins in Composites?
Composite materials are valued for their high strength-to-weight ratio and versatility across many industries. A key component in these materials is the resin, which acts as the binder that holds the reinforcing fibers together, giving the final product its shape, stability, and performance. The choice of resin significantly impacts the mechanical properties, durability, and processing method of the composite. For example, epoxy resin is widely used for its excellent mechanical strength and chemical resistance, especially in demanding environments. Understanding the types of resins in composites is essential for selecting the right material for specific applications in fields such as automotive, aerospace, construction, and dentistry.
What Is a Resin in Composite Materials?
In composite materials, resin is the matrix that surrounds and supports the reinforcing fibers, bonding them together into a solid structure. It transfers stress between fibers, protects them from environmental damage, and defines the final shape of the product. Resins are typically polymers that can be molded and hardened to form rigid components.
There are many types of resins in composites, each offering different characteristics such as flexibility, heat resistance, chemical stability, and ease of processing. The most common options include epoxy resin, polyester resins, vinylester resin, and various thermoplastic composites. The right resin is chosen based on the performance requirements of the final product, including strength, weight, cost, and environmental resistance.
Two Types of Resins in Composites: Thermoset and Thermoplastic
All types of resins in composites fall into one of two primary groups: thermoset or thermoplastic. This classification affects not only the processing techniques but also the performance characteristics of the final product. Below is a closer look at the unique properties, advantages, and common types found in each category.
Thermoset Resins
Thermoset resins are the most commonly used type in high-performance composite applications. Among the types of resins in composites, thermosets are known for their ability to form a permanent, rigid structure once cured. This structure cannot be re-melted or reshaped, making thermoset resins ideal for parts that must maintain stability under heat and pressure.
Epoxy resin is a leading example of this group. It offers excellent mechanical strength, chemical resistance, and adhesion to fibers, making it suitable for aerospace, dental, and marine applications. Polyester resins are another popular thermoset option, known for their cost-effectiveness and ease of use in large-scale production, such as in automotive parts and building materials. Vinylester resin bridges the gap between polyester and epoxy, offering better chemical resistance and toughness than polyester, while remaining more affordable than epoxy.
Thermoset resins are preferred when structural performance, long-term durability, and heat resistance are critical.
Thermoplastic Resins
Among the various types of resins in composites, thermoplastic resins behave differently from thermosets. They soften when heated and harden when cooled, allowing for reshaping and recycling. This makes thermoplastic composites attractive for applications requiring high production speed and flexibility.
These resins do not require a chemical curing process, which reduces cycle times and eliminates the need for cold storage. Thermoplastics also offer excellent impact resistance and are less brittle than thermosets. They are often used in transportation, packaging, and consumer products, where fast processing and reusability are key benefits.
Although they may require higher processing temperatures and pressures, thermoplastic resins provide long-term advantages in terms of sustainability and manufacturing efficiency.
Choosing the Right Resin for Your Composite
Selecting the right resin is a critical step in designing a high-performing composite. Among the types of resins in composites, the ideal choice depends on several factors, including the required mechanical strength, environmental conditions, cost limitations, processing method, and final application.
For example, in structural applications that demand high load-bearing capacity and resistance to harsh chemicals, epoxy resin is often the preferred choice. It delivers superior bonding and long-term durability, making it suitable for aerospace, marine, and dental restorations.
When budget is a key concern, polyester resins are widely used due to their low cost and ease of processing. They are ideal for non-critical components like panels, tanks, or automotive parts.
Vinylester resin is chosen when enhanced corrosion resistance and toughness are needed, such as in pipelines, boats, and chemical storage units. It offers better flexibility and chemical performance than polyester while being more economical than epoxy.
In fast-paced production environments, thermoplastic composites offer significant advantages. Their ability to be reheated and reshaped makes them ideal for recyclable products and applications with short manufacturing cycles, such as consumer goods and transport components.
The right resin balances performance and practicality. Understanding the different types of resins in composites and considering the specific demands of the end-use application helps manufacturers choose a resin that ensures long-lasting, cost-effective results.
Innovations and Trends in Resin Technology
The field of composite resins is continuously evolving, driven by the need for stronger, lighter, and more sustainable materials. Innovations in resin technology aim to improve performance, reduce environmental impact, and expand the use of composites across various industries. As the types of resins in composites continue to diversify, selecting materials that balance function and sustainability has become more important than ever.
One major trend is the development of bio-based resins, which are made from renewable resources such as plant oils or natural sugars. These resins reduce reliance on petroleum-based chemicals and support greener manufacturing practices without compromising mechanical performance.
Another area of innovation involves high-performance thermoplastic composites, which offer better recyclability and faster production cycles compared to traditional thermosets. These materials are gaining popularity in automotive and electronics sectors where lightweight, durable, and reprocessable components are in high demand.
Advancements in nano-modified resins are also significant. By adding nanomaterials like graphene or carbon nanotubes, resin systems can achieve enhanced thermal conductivity, electrical properties, and impact resistance. This opens new possibilities for applications in aerospace, defense, and advanced electronics.
Improved vinylester resin formulations are making these materials more competitive, offering greater toughness and chemical resistance with better handling properties during processing.
Overall, the future of resin technology is focused on sustainability, efficiency, and advanced performance. Innovations across various types of resins in composites are making composite materials more versatile and accessible for a wider range of applications, from infrastructure and healthcare to energy and consumer products.