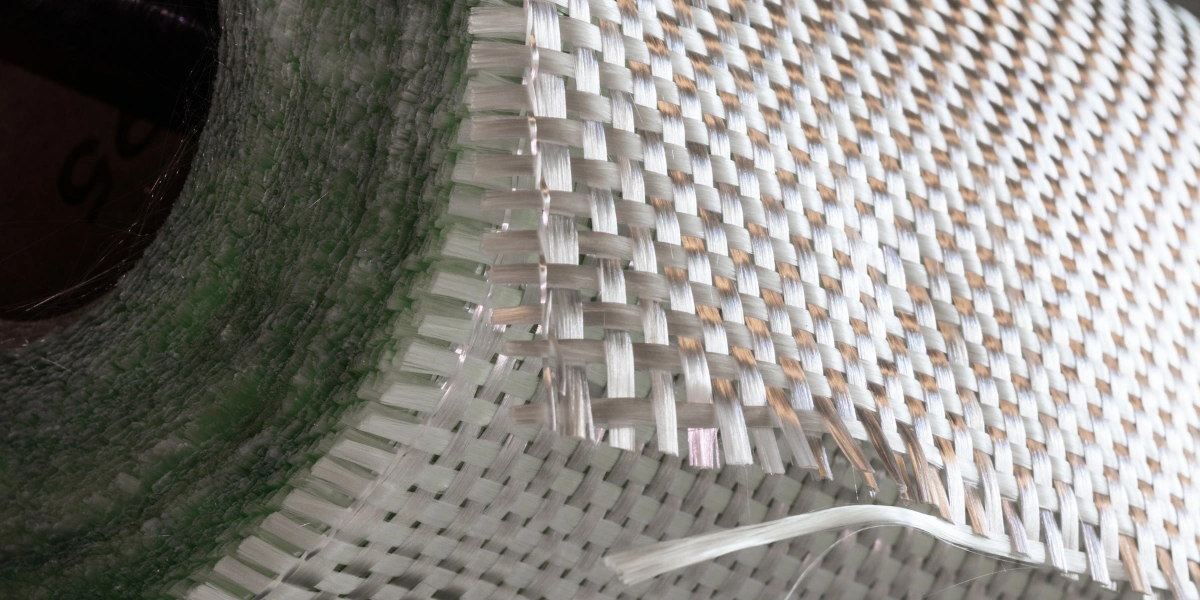
- Blog
- 20 Dec 2024
A Comprehensive Guide to Filament Winding
Filament winding is a specialized manufacturing process that has been transforming the way we create high-strength composite materials. From aerospace to automotive, this advanced technique is being used to produce lightweight yet durable structures that meet demanding engineering requirements. By precisely winding continuous strands of fiber, impregnated with resin, around a rotating mold, winding offers unmatched strength, customization, and cost-efficiency. In this guide, we will explore the details of winding, its techniques, and why it has become a crucial technology for industries that demand performance and reliability.
What is Filament Winding?
Filament winding is an advanced manufacturing technique used to create composite structures with exceptional strength and precision. It involves winding continuous strands of fibers, typically glass, carbon, or aramid, around a rotating mandrel to create cylindrical shapes. These fibers are often impregnated with a resin, such as epoxy resin, which helps bond them together and provides additional durability. The winding process is widely used to manufacture lightweight yet strong structures, such as pressure vessels, pipes, and aerospace components. The unique ability of winding to create highly tailored and reinforced shapes makes it a go-to technology in numerous industries today.
The Filament Winding Process
The winding process is relatively straightforward but requires precision and a thorough understanding of materials. It begins by mounting a mandrel—which serves as the mold for the final product—onto a winding machine. Fibers are then soaked in resin and wound around the mandrel in a specific pattern to achieve the desired strength and characteristics. Depending on the application, different types of resins, such as epoxy resin, are used to enhance the composite’s overall properties. After the winding is complete, the structure is cured, often through heat, to solidify the resin and ensure the fibers are tightly bonded together. This meticulous process results in a highly durable and efficient composite product.
Types of Filament Winding Techniques
Filament winding techniques can be categorized into several types based on the angle and orientation of the fiber placement. These techniques allow manufacturers to achieve the desired properties for a wide range of applications, each with its own unique benefits. Let’s explore some of the most common winding techniques used in the industry.
Helical Winding
Helical winding is one of the most commonly used winding techniques, especially for cylindrical components. In this method, fibers are wound at an angle relative to the mandrel’s axis. This winding angle can be adjusted to optimize the strength and stiffness of the final product. Helical winding is particularly effective for producing parts that need a balance between axial and circumferential strength, such as pipes and storage tanks. Filament winding with a helical approach allows for greater control over the mechanical properties of the composite.
Hoop Winding
Hoop winding, also known as circumferential winding, involves placing the fibers perpendicularly to the axis of the mandrel. This technique results in a high level of circumferential strength, making it ideal for pressure vessels and tanks that need to withstand significant internal pressures. Since the fibers are wrapped in a tight, consistent pattern, hoop winding is very effective for maximizing the burst strength of the product. In many cases, hoop winding is combined with other winding techniques to enhance the overall performance of the composite.
Polar Winding
Polar winding is a winding technique in which fibers are placed at varying angles, often covering the poles of the mandrel. This method is suitable for producing domed or rounded structures, such as spherical tanks or other components with complex geometries. Polar winding allows for fibers to be accurately placed over curved surfaces, providing tailored reinforcement exactly where it is needed. The ability of winding to handle these unique shapes makes it an invaluable tool in manufacturing products that require both high strength and complex forms.
Advantages of Filament Winding Technology
Filament winding technology offers numerous advantages, making it a preferred choice for producing high-strength composite materials. One of the main benefits of winding is the ability to create highly consistent and repeatable structures, which is crucial in industries where precision and reliability are essential. The continuous fibers used in winding contribute to its superior strength and performance, while the automated nature of the process allows for increased efficiency. Additionally, winding reduces material waste by ensuring that fibers are placed only where they are needed, leading to optimized usage and reduced costs. This makes winding an efficient and cost-effective solution for manufacturing advanced composite products.
Applications of Filament Winding in Various Industries
Filament winding is widely used in a variety of industries, ranging from aerospace to automotive, thanks to its versatility and strength. The ability of this technology to produce lightweight, reinforced structures with precise control over fiber placement makes it ideal for many demanding applications. Let’s take a closer look at how winding is applied across different sectors.
Aerospace and Defense
In the aerospace and defense industries, winding is used to create components that require high strength-to-weight ratios. This includes items like rocket motor casings, fuel tanks, and missile structures. Filament winding enables manufacturers to achieve the exact properties needed to ensure safety and performance in these critical applications. The use of advanced materials like carbon fiber and epoxy resin in winding further enhances the ability of these components to withstand the harsh environments they encounter. FRP reinforcement plays a significant role in aerospace applications by providing the necessary structural integrity.
Automotive and Transportation
The automotive and transportation industries have also embraced winding technology, particularly for manufacturing lightweight yet strong components such as drive shafts, pressure vessels, and suspension systems. By utilizing winding, manufacturers can create parts that reduce the overall weight of vehicles without compromising on performance. This weight reduction leads to improved fuel efficiency and lower emissions. In some cases, basalt fiber is used in combination with traditional materials to enhance the overall mechanical properties of these automotive components, offering an economical alternative to carbon fiber.
Marine and Wind Energy Industries
Filament winding is extensively used in the marine industry for producing high-strength pipes, masts, and hull components that can withstand the harsh conditions of the marine environment. The lightweight nature of winding products ensures they are easy to handle and install, while their excellent corrosion resistance provides long-lasting durability. In the wind energy sector, winding is used to manufacture large wind turbine blades, which need to be both lightweight and strong to efficiently harness wind energy. The incorporation of advanced materials like epoxy resin and fiber reinforcements ensures that these components are capable of delivering high performance in challenging conditions.
In conclusion, winding is a versatile and effective manufacturing process that offers significant advantages across multiple industries. From aerospace to automotive, this technology helps create strong, lightweight, and durable composite structures that are perfectly tailored to specific needs. By combining advanced materials like basalt fiber and epoxy resin with precise winding techniques, winding has become an indispensable part of modern manufacturing. If you are considering adopting this technology for your next project, understanding the different winding methods and their benefits can help you make an informed decision that will lead to superior results.