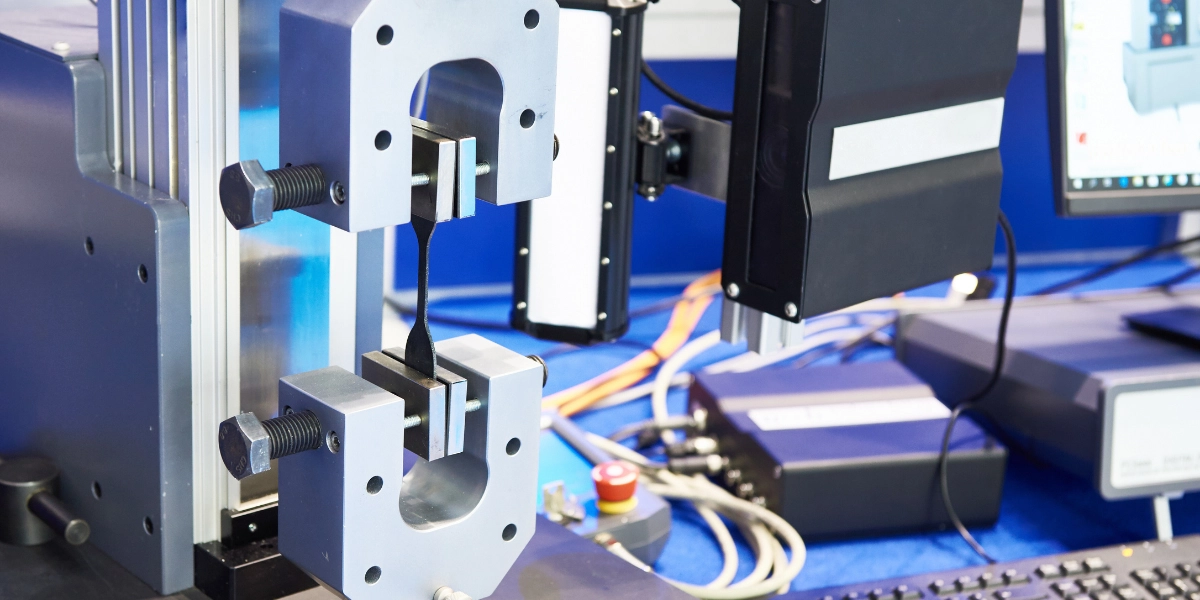
- Blog
- 23 Jun 2025
What is Composite Fatigue Testing and Why Does it Matter?
Composite materials are widely used today—from cars to airplanes, and even in sports and medical equipment. They are known for being lightweight, strong, and long-lasting. However, over time, repeated stress can cause them to weaken. This is where composite fatigue testing becomes essential. It allows engineers and designers to assess how long a composite material can perform safely before showing signs of failure. This testing supports the development of safer and more reliable products used in daily life.
What is Composite Fatigue?
Composite fatigue refers to the gradual damage that occurs in a composite material when it is exposed to repeated stress or cyclic loading over time. Unlike a single heavy impact, fatigue is caused by smaller, repetitive forces—such as vibration, bending, or twisting. Even when each load is minor, the repeated exposure can slowly reduce the material’s strength.
In composite materials, fatigue can appear differently compared to metals. Instead of a sudden crack, signs may include fiber breakage, matrix cracking, or delamination, where layers within the material begin to separate. These internal changes often grow over time and may eventually lead to structural failure.
In the case of composites in automotive applications—such as suspension arms or underbody panels—components are expected to endure continuous stress for long periods. Studying the fatigue behavior of composites and composite testing makes it possible to design parts that maintain strength and reliability over extended use.
How Composite Fatigue Testing Works
Composite fatigue testing helps to understand how composite materials behave under repeated stress. It involves applying controlled loads to a test sample over many cycles, simulating real-life use. This process helps detect how and when damage starts, how it spreads, and when the material eventually fails.
Fatigue Testing Methods
There are several methods used in composite fatigue testing, depending on the type of stress and the application. The most common types include:
- Tension–tension testing: A pulling force is applied repeatedly to the material. This method is used when parts are expected to experience stretching or pulling in real use.
- Compression–compression testing: This method applies pressure, helping to study materials used in parts that carry weight or experience pressure from above.
- Flexural or bending fatigue: Used to test how well a material performs under repeated bending, which is important for parts like beams or panels.
- Tension–compression testing: Combines both pulling and pushing forces, often used for parts exposed to mixed loads.
Each method helps simulate specific real-world conditions where composite materials are expected to perform.
Test Parameters: Load, Frequency, and Cycles
Three key parameters define a fatigue test:
- Load: The force applied to the material during testing. This can be constant or variable and is usually based on expected service conditions.
- Frequency: How fast the load is applied. It is measured in cycles per second (Hz). A higher frequency can speed up the test, but must be chosen carefully to avoid overheating or unnatural results.
- Cycles: The number of times the load is applied. Some tests go up to millions of cycles to simulate years of use in a short time.
By adjusting these parameters, engineers can study how a composite behaves in different real-life scenarios.
Equipment and Standards (ASTM, ISO)
Composite fatigue testing is performed using specialized machines that can apply repeated loads with high precision. These machines often include sensors and software to track data like stress, strain, and crack growth over time.
Testing is done according to international standards to ensure consistency and reliability. Two of the most common standards are:
- ASTM (American Society for Testing and Materials): Provides detailed methods for various fatigue tests on composites.
- ISO (International Organization for Standardization): Offers global guidelines that are widely accepted across industries.
Following these standards ensures that results are accurate and comparable across different labs and projects.
Why Composite Materials Need Fatigue Testing
Composite materials are designed to be strong and lightweight, but they can still suffer damage when exposed to repeated stress over time. Unlike metals, composites often hide early signs of failure within their layers. Cracks, fiber breaks, or delamination may not be visible from the outside until the damage is advanced.
This makes composite fatigue testing essential for predicting long-term performance and preventing unexpected failures. By understanding how and when damage starts, manufacturers can improve material design, select the right fiber-matrix combinations, and set proper safety limits for use.
Composite fatigue testing is especially important in industries like transportation, energy, and health—where reliability and safety are critical. For example, in composites in aviation, even small parts must resist thousands of takeoff and landing cycles without losing strength. Without fatigue data, it would be hard to trust composite parts in such demanding environments.
Testing helps reduce risks, extend product life, and lower maintenance costs. It also supports better quality control and allows engineers to design smarter, lighter, and safer composite structures.
Key Applications of Fatigue Testing
Composite fatigue testing plays a vital role in many industries where materials must stay strong under repeated use. It helps ensure that composite parts remain safe, reliable, and long-lasting in real-life conditions. Here are some key areas where fatigue testing is especially important:
- Aerospace Industry: In aircraft structures, such as wings, fuselage panels, and interior components, fatigue resistance is critical. Composites in aviation must handle high stress from takeoff, flight, and landing—often for thousands of cycles. Testing helps meet strict safety and performance standards.
- Automotive Industry: Lightweight composites are used in car frames, doors, underbody parts, and suspension systems. Composites in automotive improve fuel efficiency and handling, but these parts must survive road vibrations, bumps, and daily wear. Fatigue testing ensures they remain durable over time.
- Wind Energy: Composite blades in wind turbines face continuous stress from wind forces. Fatigue testing is necessary to predict how long these blades can operate safely before needing replacement.
- Sporting Goods: Bicycles, tennis rackets, and other equipment made with composites are exposed to repetitive impacts. Testing helps balance light weight with high durability.
- Medical Devices: In items like prosthetics or surgical tools, performance and safety under repeated use are essential. Fatigue testing ensures long-term reliability without failure.
In all these areas, composite fatigue testing supports better product design, longer service life, and reduced failure risks.
Composite fatigue testing is a key step in making sure composite materials perform safely and reliably over time. By understanding how these materials react to repeated stress, industries can create better products—from airplanes and cars to wind turbines and medical devices. With the help of proper testing methods and standards, composite technology continues to move forward, offering lighter, stronger, and longer-lasting solutions for the future.