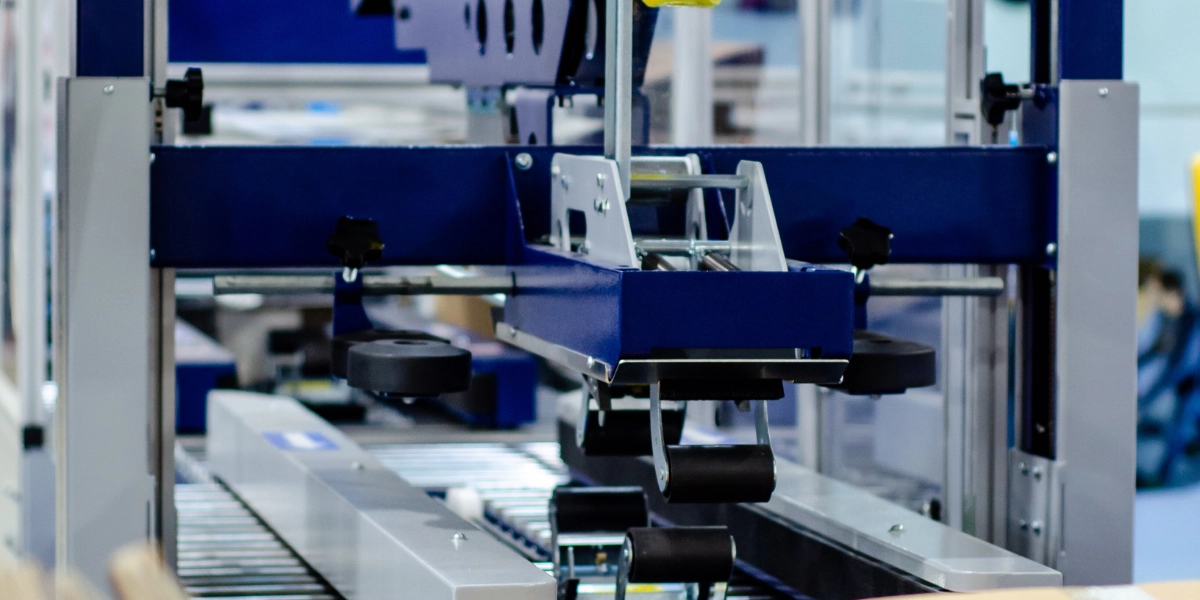
- Blog
- 12 May 2025
Top Benefits of Automated Tape Laying
In today’s fast-paced manufacturing world, automation plays a key role in improving both quality and efficiency. One of the most advanced technologies in the composite industry is automated tape laying. This method is used to build strong, lightweight parts by placing fiber-reinforced tapes onto molds in a precise way. It is especially important in industries like aerospace, automotive, and wind energy, where materials must be both durable and lightweight. ATL helps companies speed up production, reduce errors, and lower material waste. In this article, we will explore what automated tape laying is, how it works, and the many benefits it offers for modern composite manufacturing.
What Is Automated Tape Laying?
Automated tape laying (ATL) is a manufacturing process that uses a machine to place thin strips of composite material, called tapes, onto a mold surface. These tapes are usually made of fiber-reinforced materials, such as carbon fiber, and are pre-impregnated with resin (prepreg). The machine moves along a set path to lay the tapes in layers, building the part step by step.
Unlike manual methods, ATL uses composite machines that are programmed to work with high precision and speed. It’s commonly used in the prepreg production process, especially for large or complex parts where accuracy and strength are important. This technology is often linked with automated fiber placement, another advanced method used in composite manufacturing.
Key Benefits of Automated Tape Laying
The growing demand for lightweight and durable components has made ATL a valuable solution across many industries. This advanced method offers several key advantages compared to traditional hand lay-up or manual processes. From faster cycle times to better quality control, ATL helps manufacturers meet high-performance standards while staying efficient and cost-effective.
Increased Production Speed
One of the biggest advantages of ATL is its ability to significantly increase production speed. Unlike manual processes, ATL systems can lay tape continuously and at high speeds, often covering large surface areas in a short amount of time. This means more parts can be produced in less time—an essential benefit in industries like aerospace and automotive, where deadlines are tight and production volumes are high.
By automating the tape placement process, manufacturers reduce the need for manual labor and minimize delays caused by human error or fatigue. With faster throughput, companies can scale their production and respond more quickly to customer demand, helping them stay competitive in the market.
Higher Precision and Consistency
Precision is critical in composite manufacturing. Automated tape laying machines are controlled by software that ensures each layer is placed exactly where it should be, with the correct angle, pressure, and spacing. This level of consistency is difficult to achieve with manual methods.
The result is higher-quality parts with fewer defects. Whether producing components for aircraft, satellites, or high-performance sports equipment, manufacturers can trust that each product meets strict design requirements. This is especially important in the carbon fiber structural reinforcement of critical load-bearing parts.
Reduced Material Waste and Costs
Material waste is one of the hidden costs in composite production. Manual lay-up often leads to off-cuts, overlaps, or errors that waste valuable prepreg material. In contrast, automated tape laying systems are optimized to use materials efficiently. They cut and place tapes with minimal waste, helping manufacturers save on raw material costs.
Additionally, because ATL reduces the need for rework or discarded parts due to mistakes, overall production costs go down. Over time, this can lead to significant savings, especially for large-scale production runs.
Improved Strength and Performance of Composites
The mechanical strength and performance of composite parts depend heavily on how accurately the fibers are aligned. ATL machines are designed to place tapes in ideal orientations, layer by layer, which improves the final part’s structural integrity.
When tapes are placed with exact tension and alignment, the resulting composite part can handle more stress and perform better in demanding environments. This is especially useful in aerospace applications, where both weight and strength are critical factors.
Enhanced Automation and Process Control
One of the most valuable features of ATL is the level of control it offers. Operators can program the machine to follow complex paths, adjust speeds, control temperature, and monitor quality in real time. This leads to more predictable outcomes and easier process monitoring.
As part of a smart factory system, ATL can also be integrated with other composite machines for a seamless prepreg production process, reducing manual touchpoints and increasing overall plant efficiency. When combined with technologies like automated fiber placement, it supports scalable, high-performance manufacturing solutions.
Applications of Automated Tape Laying
ATL is widely used in industries that require lightweight, high-strength components with excellent performance. One of the most common applications is in the aerospace sector, where ATL is used to produce large structural parts such as fuselage panels, wing skins, and empennage sections. These parts must be both strong and lightweight, making ATL an ideal solution.
In the automotive industry, ATL helps create composite parts that reduce vehicle weight and improve fuel efficiency. Electric vehicle (EV) manufacturers, in particular, benefit from ATL’s precision and speed for building battery enclosures and structural components.
The wind energy sector also relies on ATL to produce long, durable wind turbine blades. These blades must withstand heavy environmental stress while remaining lightweight to operate efficiently.
In sports equipment, such as high-end bicycles, tennis rackets, and racing helmets, ATL ensures that composite parts are manufactured with exact specifications for maximum performance and safety.
With its ability to deliver fast, precise, and high-quality results, automated tape laying is becoming essential in any field that demands strong, lightweight composite parts.
Automated tape laying offers a smart, efficient way to produce high-quality composite parts. With faster production, better precision, and less waste, it’s a valuable tool for industries like aerospace, automotive, and energy. As part of modern composite manufacturing, ATL supports stronger, lighter, and more reliable products.