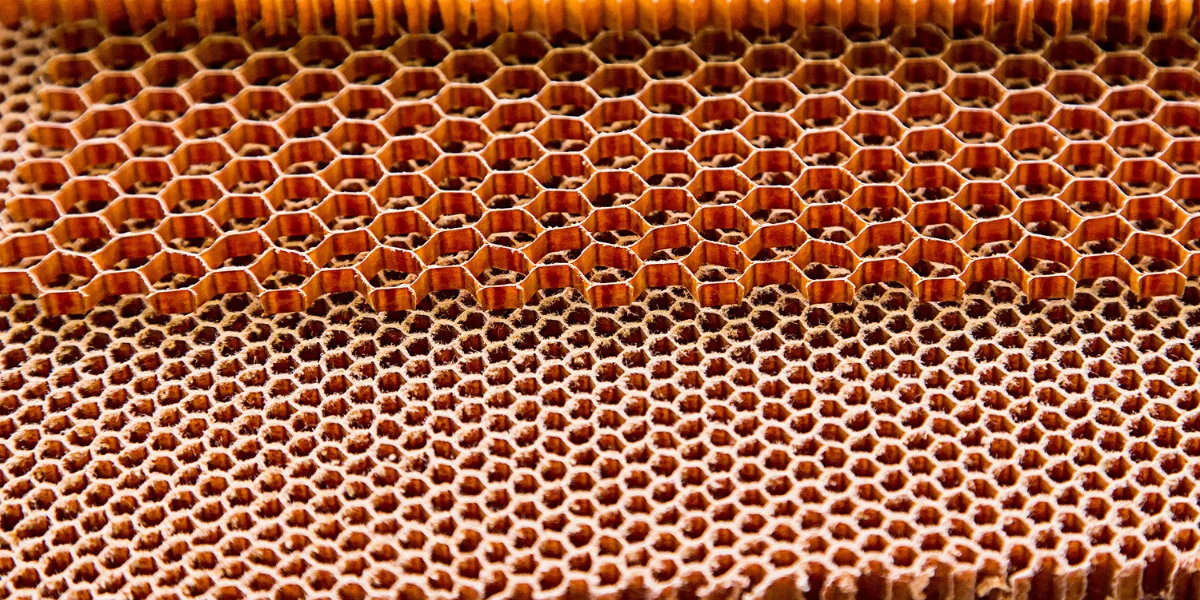
- Blog
- 10 Feb 2025
Diverse Applications of Composite Materials
Composite materials have transformed modern industries with their exceptional strength, lightweight properties, and design flexibility. These advanced materials combine two or more distinct components to create a superior product with enhanced performance. From aerospace to medical technology, the applications of composite materials continue to expand, providing innovative solutions across various sectors.
Applications of Composite Materials in Key Industries
Composite materials are widely used in numerous industries where performance, durability, and weight reduction are essential. Let’s explore how these materials contribute to some of the most important sectors.
Automotive Industry
The applications of composite materials in the automotive sector have significantly transformed vehicle design, efficiency, and performance. By incorporating advanced materials like carbon fiber-reinforced polymers (CFRP) and fiberglass composites, manufacturers can create lighter, stronger, and more durable vehicles. These materials are commonly used in car body panels, bumpers, chassis components, and even interior elements such as dashboards and seats. Their lightweight nature reduces the overall mass of the vehicle, which directly improves fuel efficiency, reduces emissions, and supports sustainability efforts without compromising safety or structural integrity.
In composites in automotive manufacturing, the strength and energy absorption capabilities of composite materials play a crucial role in enhancing crash resistance, offering better protection for passengers in case of collisions. Additionally, the design flexibility of composites allows for the production of complex shapes and aerodynamic features that contribute to better vehicle performance and aesthetics.
Modern electric vehicles (EVs) especially benefit from applications of composite materials in automotive. Lightweight composite materials help reduce the vehicle’s weight, which is essential for improving battery efficiency and extending the driving range. Since battery packs are often heavy, using composite materials in other vehicle components helps offset this weight, allowing for longer distances between charges. This combination of durability, energy efficiency, and design versatility makes composite materials a key factor in the future of sustainable automotive engineering.
Aerospace Industry
In the aerospace sector, composites in aviation have become indispensable due to their unique combination of lightweight properties, high strength, and resistance to extreme conditions. Aircraft manufacturers increasingly rely on advanced materials like carbon fiber-reinforced polymers (CFRP) and glass fiber composites to design critical components such as fuselages, wings, tail sections, and cabin interiors. These materials significantly reduce the overall weight of the aircraft, which leads to improved fuel efficiency, lower operational costs, and reduced carbon emissions—key priorities in modern aviation.
A key advantage of applications of composite materials in aviation is their exceptional tensile strength and fatigue resistance, which are essential for aircraft that endure continuous stress during long flights and varying atmospheric pressures. Composite materials also offer excellent corrosion resistance, which minimizes maintenance needs compared to traditional metal structures, extending the aircraft’s operational lifespan.
Modern airplanes, such as the Boeing 787 Dreamliner and Airbus A350, incorporate over 50% composite materials by weight. These aircraft benefit from reduced drag due to streamlined, aerodynamically optimized composite components. Additionally, the ability to mold composites into complex shapes allows for innovative designs, improving passenger comfort while maintaining structural integrity.
By combining performance, durability, and sustainability, composites in aviation continue to play a pivotal role in shaping the future of air travel, making it safer, more efficient, and environmentally friendly.
Construction and Civil Engineering
The applications of composite materials in construction focus on enhancing durability and reducing maintenance needs. Fiber-reinforced polymers (FRP) are used in bridges, tunnels, and building facades for their corrosion resistance and lightweight properties.
In composite in construction applications, composites are increasingly used for reinforcing concrete structures, offering superior crack resistance and extending the lifespan of infrastructures. Pultruded composite beams and panels also simplify installation while maintaining excellent load-bearing capacity.
Marine Industry Applications
Composite materials play a vital role in the marine industry, offering lightweight strength, corrosion resistance, and long-term durability in harsh marine environments. Marine composite solutions, such as fiberglass-reinforced plastics (FRP) and carbon fiber composites, are commonly used in boat hulls, ship decks, and underwater structures. These materials help improve fuel efficiency by reducing vessel weight while ensuring excellent performance against saltwater damage and weather exposure. From leisure yachts to large offshore platforms, composite materials contribute to safer, longer-lasting, and more efficient marine structures.
Boat and Ship Hulls
Marine composite materials are widely used in boat and shipbuilding due to their lightweight nature, corrosion resistance, and excellent water resistance. Fiberglass-reinforced plastics (FRP) are commonly used for boat hulls, as they reduce maintenance needs and improve fuel efficiency by lowering the vessel’s weight.
Offshore Platforms and Structures
In offshore industries, marine composite materials play a key role in constructing oil rigs, floating platforms, and underwater pipelines. Their resistance to saltwater corrosion and extreme weather conditions makes them ideal for harsh marine environments.
Industrial Applications of Composite Materials
Composite materials have become essential in various industrial sectors due to their superior strength, lightweight nature, and resistance to harsh environments. These advanced materials are widely used in applications where durability, performance, and cost-effectiveness are critical. From renewable energy to manufacturing tools, industrial composite solutions contribute to improved efficiency and sustainability. Their ability to resist corrosion, fatigue, and extreme temperatures makes them ideal for demanding applications, such as wind turbine blades, protective gear, and heavy machinery components.
Wind Energy
The applications of composite materials in wind energy focus on producing strong yet lightweight turbine blades. Composite materials, such as glass fiber-reinforced polymers (GFRP) and carbon fiber composites, help create large, efficient blades capable of withstanding high wind loads and prolonged environmental exposure.
Sports Equipment
Composites in sports have transformed athletic gear by offering lightweight, durable, and performance-enhancing materials. Carbon fiber and Kevlar are commonly used in bicycles, tennis rackets, golf clubs, and helmets, providing both strength and flexibility for high-performance sports equipment.
Medical Equipment
The applications of composite materials in the medical sector range from prosthetics to imaging equipment. Carbon fiber composites are ideal for prosthetic limbs due to their lightweight and strong characteristics, while radiolucent composites are used in MRI and X-ray tables to minimize interference during scans.
Advantages of Composite Materials in Various Applications
The widespread use of composite materials is driven by several key advantages:
- Lightweight: Composites offer exceptional strength-to-weight ratios, making them ideal for industries like aerospace, automotive, and sports.
- Durability: They resist corrosion, chemicals, and environmental wear, increasing the lifespan of structures and equipment.
- Design Flexibility: Composite manufacturing processes allow for complex shapes and custom designs to meet specific industry needs.
- Thermal and Electrical Insulation: Many composite materials provide excellent insulation properties, making them suitable for construction and electrical applications.
- Reduced Maintenance: Composites require less upkeep compared to traditional materials, lowering long-term costs.
From marine composite solutions for boats to composites in aviation for aircraft and industrial composite materials for wind turbines, the versatility of these materials continues to shape modern industries. As technology advances, the applications of composite materials will only expand further, providing innovative solutions for even more sectors.