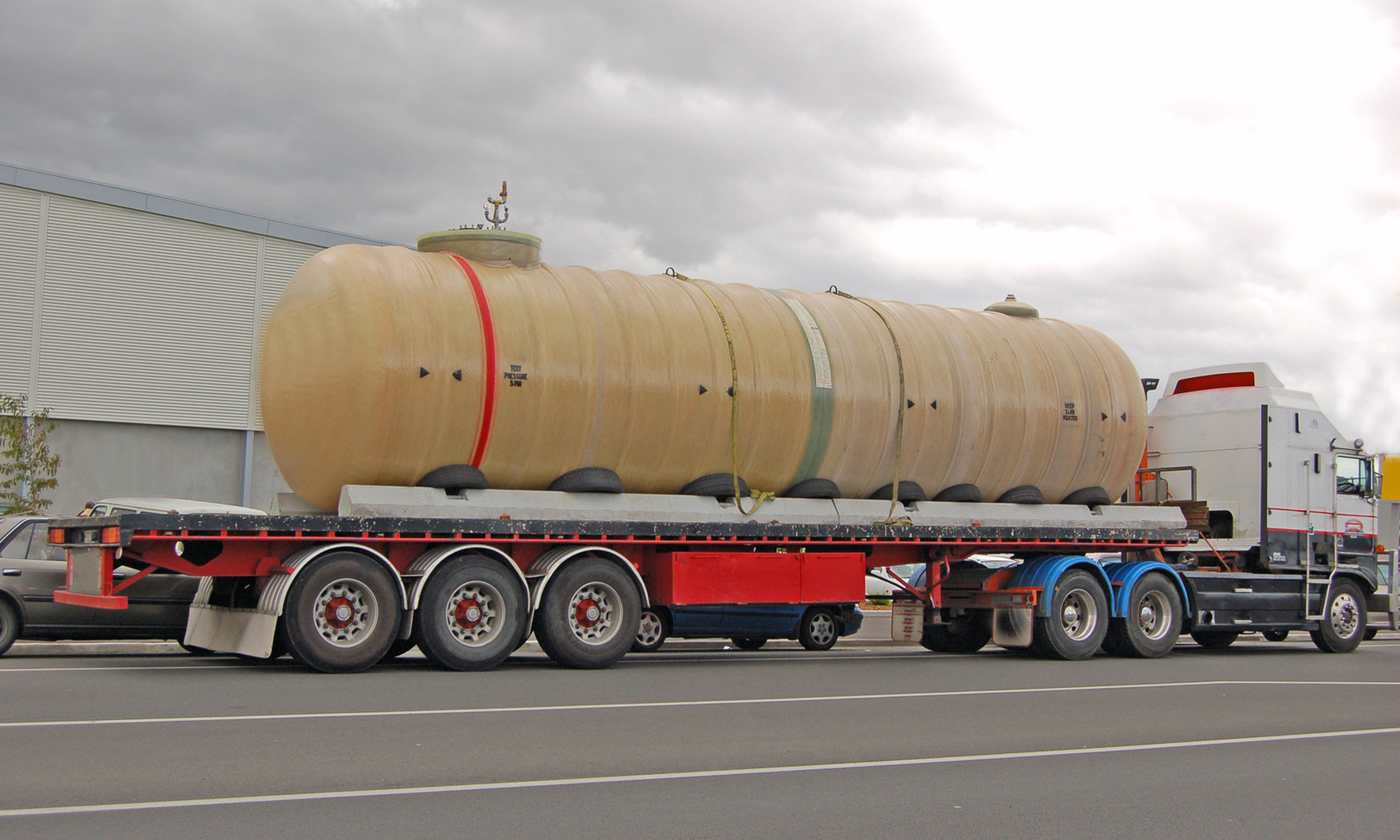
Chemical Containment and Infrastructure
Industries around the world are harnessing the transformative power of industrial composites to revolutionize manufacturing processes. By combining different materials, such as reinforcement materials and polymer resins, industrial composites offer unique properties that have reshaped the landscape of modern engineering solutions.
What Are Industrial Composites?
Industrial composites, also known as composite materials, have become a cornerstone in various sectors, including aerospace, automotive, construction, and marine. Their lightweight nature, exceptional strength, and remarkable resistance to corrosion and fatigue make them the material of choice for designers and engineers seeking cutting-edge solutions.
The Role of Composites in Modern Industries
Composites have become indispensable in industrial composite manufacturing, playing a vital role in producing lightweight materials that offer exceptional durability and high performance. Their utilization has revolutionized industries such as aerospace and automotive, where weight reduction is crucial for enhancing fuel efficiency and overall performance.
Composites, with their superior strength-to-weight ratios compared to traditional materials like metals, allow manufacturers to design products that are lighter and more fuel-efficient, without compromising structural integrity. This advancement has significantly impacted the aerospace and automotive sectors, enabling the creation of innovative and efficient designs.
In addition to their lightweight properties, composites also possess excellent resistance to chemicals, moisture, and temperature variations. These characteristics make them ideal for applications in harsh environments, expanding their usage into various industrial composite industries beyond aerospace and automotive. The versatility of composites has opened up new opportunities in sectors such as construction, marine, and renewable energy.
Overall, composites have proven to be a game-changer for modern industries, providing lightweight industrial composite materials with exceptional strength and durability. Their usage has not only improved fuel efficiency and performance but also allowed for the development of innovative designs and solutions. As manufacturing processes continue to evolve and technology advances, composites will continue to play a significant role in shaping the future of various industries.
The Manufacturing Process of Industrial Composites
The manufacturing process of industrial composites involves several key steps. First, a reinforcement material is combined with a polymer resin to create a composite material. The reinforcement material can be carbon fiber, fiberglass, or aramid, while the polymer resin can be epoxy, polyester, or vinyl ester. These components are carefully chosen to achieve the desired properties in the final composite material.
The reinforcement material provides the strength and stiffness to the composite, while the polymer resin acts as a binder to hold the reinforcement together. The combination of these two components creates a material that is both lightweight and strong, making it ideal for various industrial applications.
The next step in the manufacturing process is forming the composite material into the desired shape. This can be done using techniques such as molding, pultrusion, or filament winding. Molding involves placing the composite material into a mold and applying heat and pressure to create the desired shape. Pultrusion involves pulling continuous fibers through a resin bath and then through a heated die, resulting in a constant cross-sectional shape. Filament winding involves precisely winding continuous fibers onto a rotating mandrel to create a cylindrical shape.
Once the composite material is formed into the desired shape, it undergoes the curing process. Curing involves applying heat, pressure, or a combination of both to harden the polymer resin. This step is critical for transforming the composite material into a rigid and durable material with the desired mechanical properties. The curing process can vary depending on the specific resin being used and the desired properties of the final composite.
The manufacturing process of industrial composites is a highly controlled and precise process. It requires expertise in material selection, composite forming techniques, and curing methods to ensure the final product meets the required specifications. By understanding and carefully executing each step in the manufacturing process, manufacturers can produce high-quality industrial composites that offer exceptional performance in various industries.
Advancing Technology and Its Impact on Composite Materials
Advancing technology has brought about significant advancements in the field of composite materials, revolutionizing their production and opening up new possibilities for their applications. Two key areas where technology has had a profound impact are automation in composite production and the development of smart composites.
Automation in Composite Production
Automation has transformed the way composite materials are manufactured, enhancing efficiency, reducing labor costs, and ensuring consistent quality. With the advent of automated processes such as robotic layup and automated fiber placement, manufacturers can now produce complex composite structures with unparalleled precision and repeatability. This not only saves time but also allows for greater design freedom and the creation of intricate shapes that were previously challenging to achieve.
The Rise of Smart Composites
Another exciting development in the field of composite materials is the emergence of smart composites. These composites integrate sensors or actuators directly into the composite structure, enabling them to sense and respond to changes in their environment. By incorporating functionality into the material itself, smart composites offer enhanced performance, increased safety, and improved efficiency. They can be used in a wide range of applications, from structural health monitoring in aerospace to vibration damping in automotive.
By utilizing advancing technology, the potential for composite materials continues to expand. Automation streamlines production processes, making composites more accessible and cost-effective. Furthermore, the development of smart composites opens up new frontiers in functionality and capabilities. As technology advances further, we can expect to see even more innovative uses for composite materials in various industries, driving progress and shaping the future of manufacturing and engineering solutions.
Essential Properties of Different Industrial Composite Materials
Industrial composite materials offer a wide range of properties depending on the specific reinforcement and resin used. These materials combine the strengths of various components to create unique properties that make them highly desirable in various industries. Some common essential properties of industrial composite materials include:
- High Strength: Industrial composites exhibit impressive strength, allowing them to withstand significant loads and forces, making them suitable for structural applications.
- Excellent Stiffness: Composites possess a high stiffness-to-weight ratio, providing rigidity and stability to structures without adding excessive weight.
- Outstanding Corrosion Resistance: Industrial composites are highly resistant to corrosion, making them ideal for applications in aggressive environments such as marine or chemical industries.
These properties make industrial composites suitable for a wide range of applications where durability, lightweight, and resistance to environmental conditions are crucial. Furthermore, the properties of composites can be further tailored to meet specific requirements in different industries. For example, composites can be engineered to have specific thermal conductivity, electrical conductivity, or fire resistance properties, making them versatile materials for various applications.
Industrial Composite Applications in Aerospace
The aerospace industry has experienced a significant transformation with the introduction of industrial composites. These lightweight, strong, and durable materials have revolutionized aircraft construction, offering numerous advantages in terms of aerodynamics, fuel efficiency, and overall performance.
Composite Materials Taking Flight
Composite materials, composed of reinforced fibers and polymer resins, are widely used in the manufacturing of various aircraft components. From wings and fuselages to tail sections, composites have become an integral part of the aerospace industry, replacing traditional materials with their exceptional properties.
Benefits in Aerodynamics and Fuel Efficiency
One of the key advantages of using industrial composites in aerospace applications is weight reduction. Composites are significantly lighter than conventional materials, enabling aircraft to carry more passengers or cargo without compromising structural integrity. This weight reduction contributes to improved aerodynamics, allowing for smoother flight and reduced drag.
In addition to enhanced aerodynamics, the use of composites in aerospace also leads to increased fuel efficiency. With lighter aircraft, fuel consumption is reduced, resulting in lower operating costs and a reduced environmental impact. This aligns with the industry’s ongoing efforts to improve sustainability and promote fuel-efficient technologies.
Overall, industrial composites have proven to be a game-changer in the aerospace industry. By harnessing their lightweight, strength, and durability, aircraft manufacturers can build more advanced and efficient aircraft that meet the demands of today’s aviation industry.
Composites in Automotive Manufacturing
When it comes to automotive manufacturing, composites are playing a crucial role in enabling the production of high-performance vehicles. The use of composite materials offers several advantages that are driving innovation in the automotive industry. One of the key benefits is weight reduction, which is essential for improving fuel efficiency and overall performance.
High-Performance Composites for Modern Vehicles
Composites are extensively used in the construction of body panels, chassis components, and interior parts, contributing to a significant reduction in vehicle weight. This not only improves fuel efficiency, but also enhances handling and agility. By utilizing high-performance composites, automakers can design vehicles that are lighter, yet maintain the required structural integrity and safety standards.
Enabling the Future of Electric Cars
The rise of electric cars is paving the way for even greater adoption of composites in automotive manufacturing. Electric vehicles (EVs) rely on lightweight materials to maximize their range and battery efficiency. Composites offer the ideal solution, as they are not only lightweight, but also provide excellent strength and durability. With the increasing demand for electric cars, the use of composites is expected to grow, enabling automakers to design more efficient and sustainable vehicles.