Vacuum Infusion Consumables
Vacuum consumables are essential components in the vacuum infusion process, a technique widely used in the composites industry to create high-strength, lightweight structures. These consumables include a range of materials such as vacuum bags, peel ply, release films, breather fabrics, and sealant tapes, all designed to facilitate the optimal flow of resin through the reinforcement material under vacuum pressure. Vacuum consumables play a pivotal role in ensuring the integrity and efficiency of the vacuum infusion process. By carefully selecting and utilizing the right products, manufacturers and hobbyists alike can achieve superior quality in their composite projects, making these materials indispensable in the production of advanced composite parts.
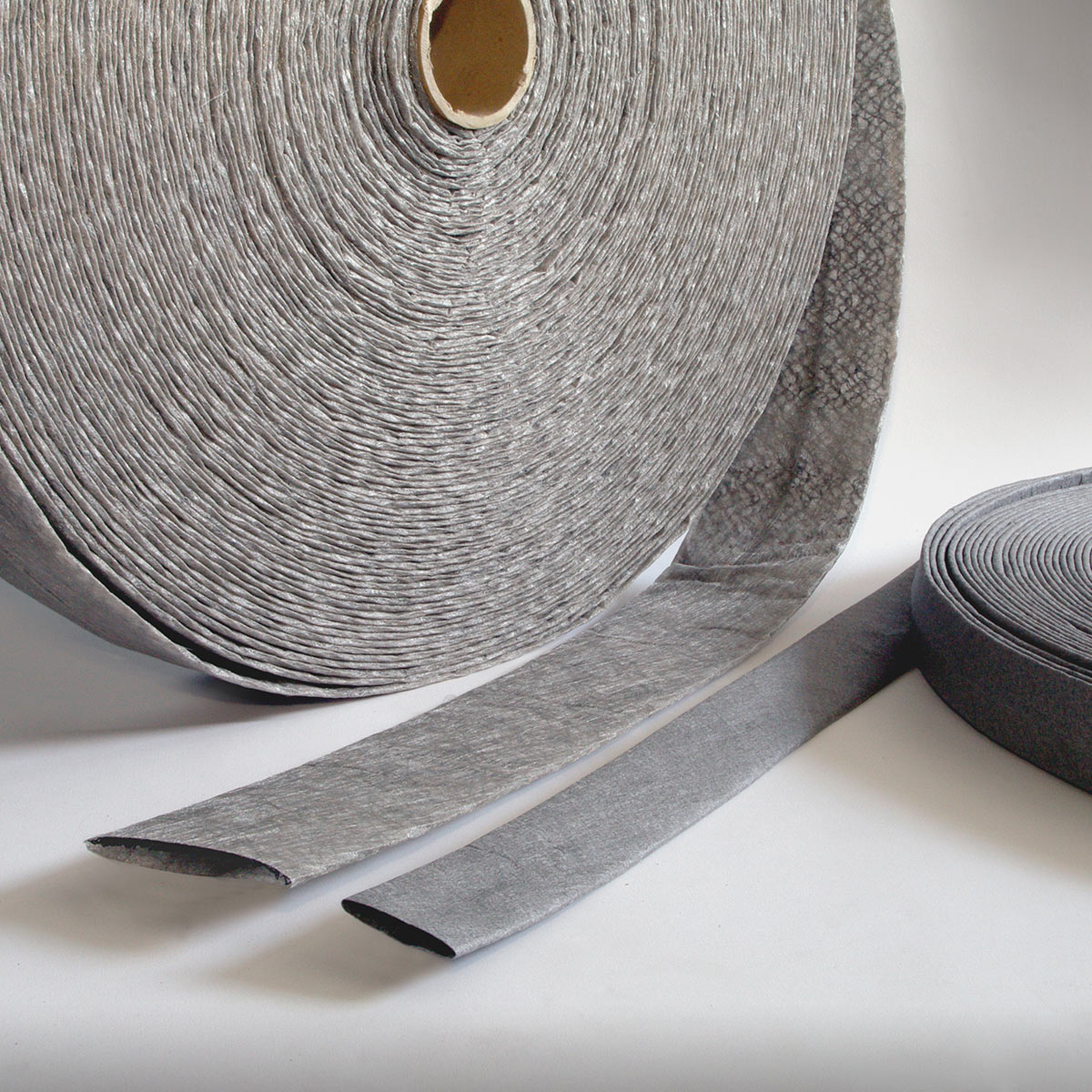
Enka Channel
Review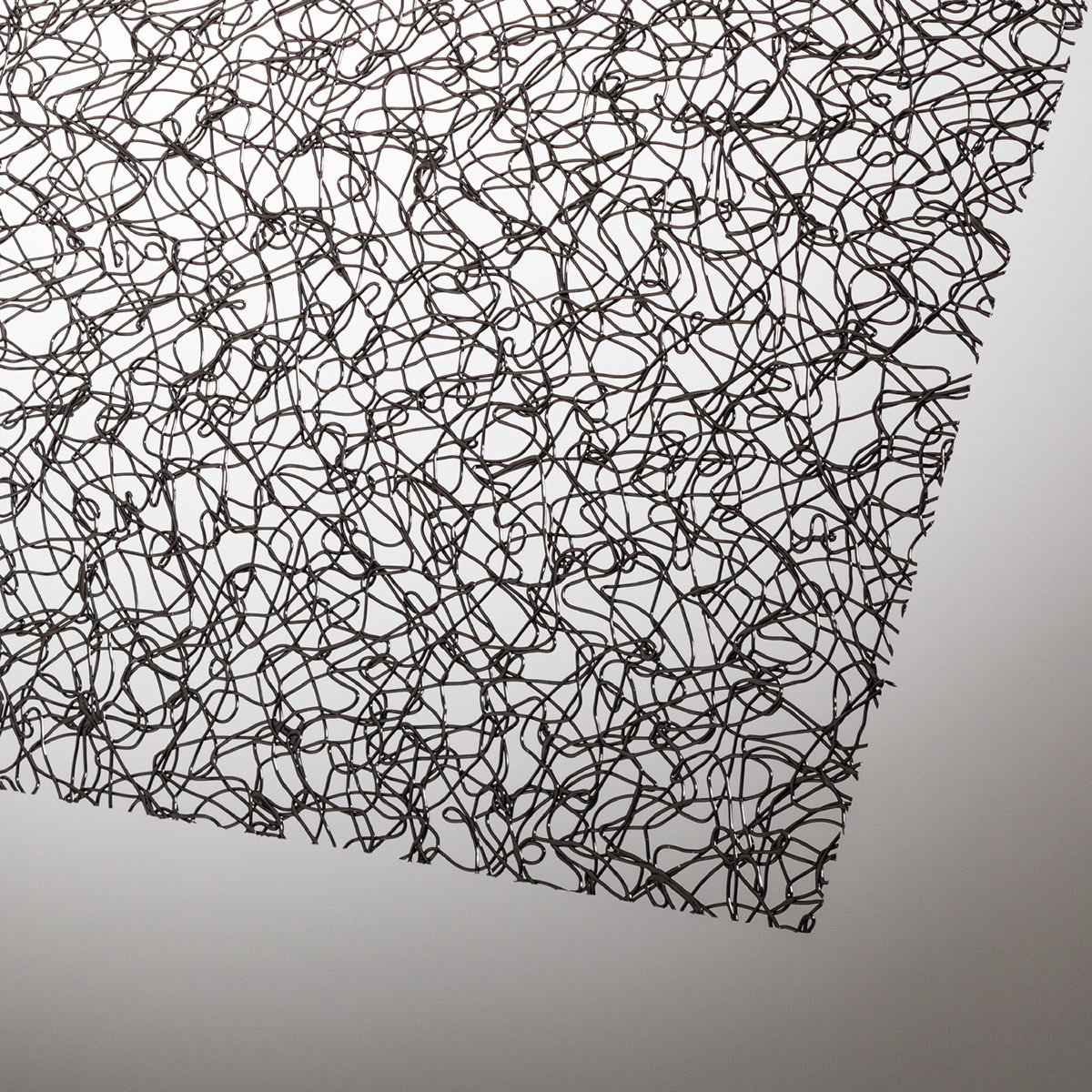
Enka Fusion 7202 Flow
Review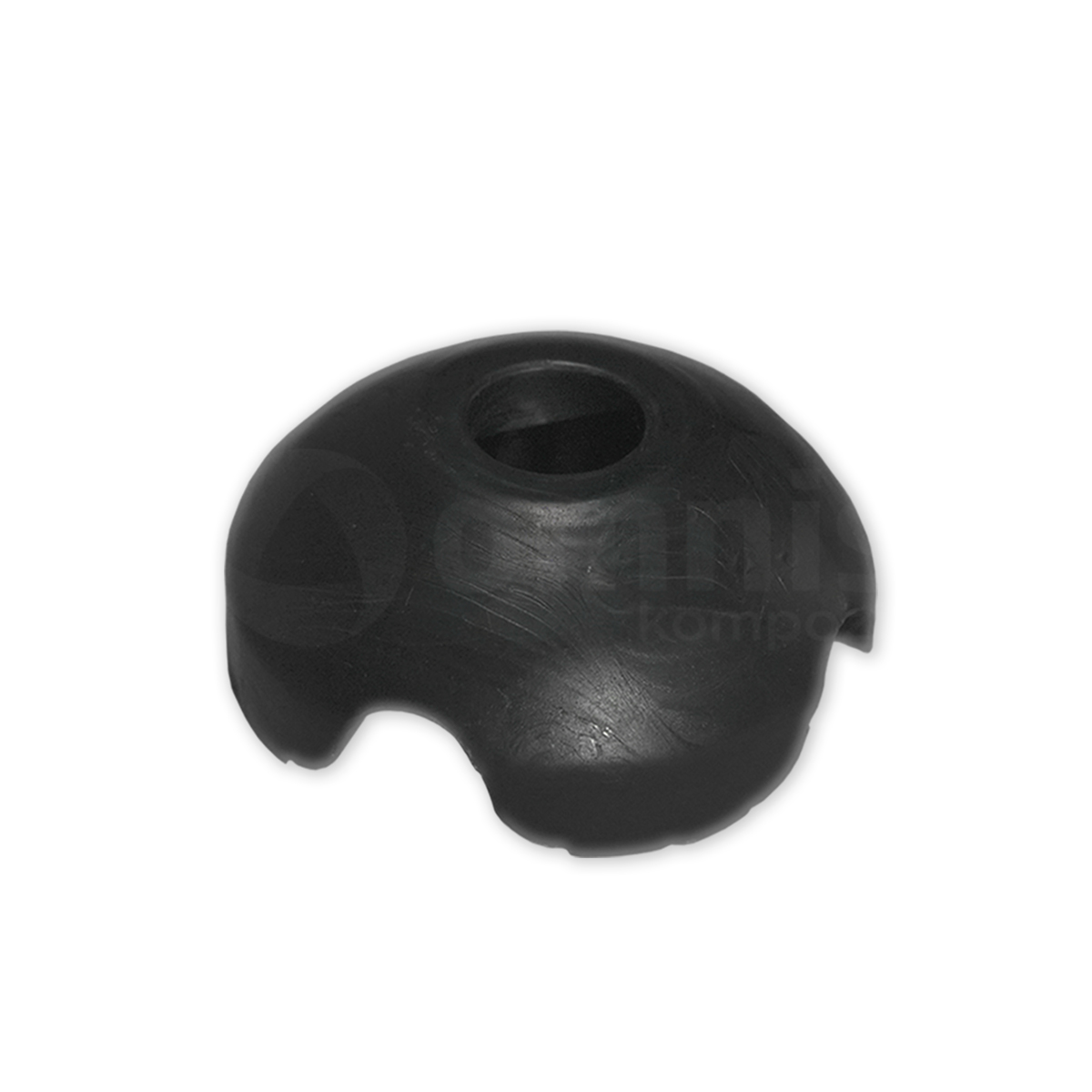
Infusion Block Connector
Review
Sheet Wax
Review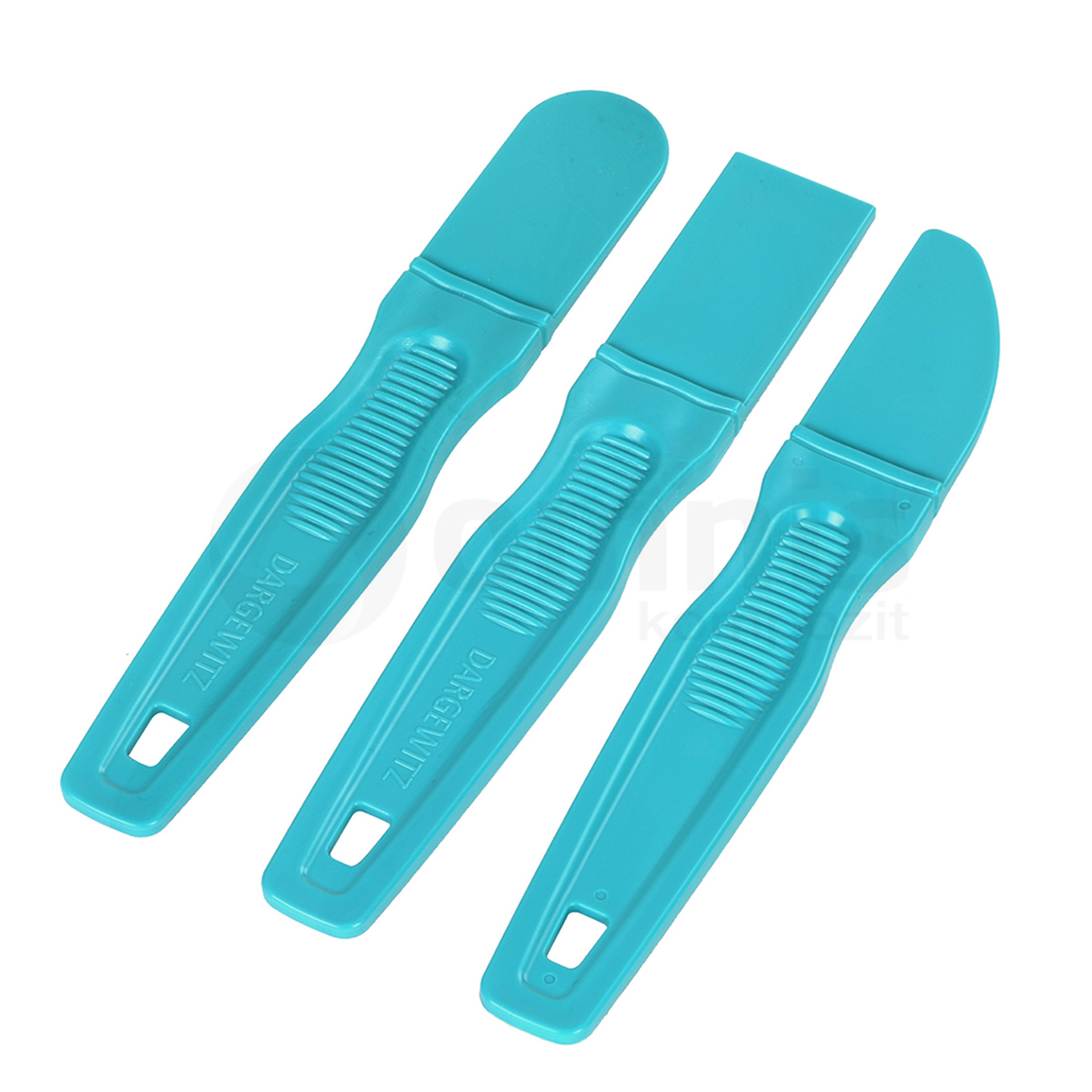
Prepreg Lamination Spatula
Review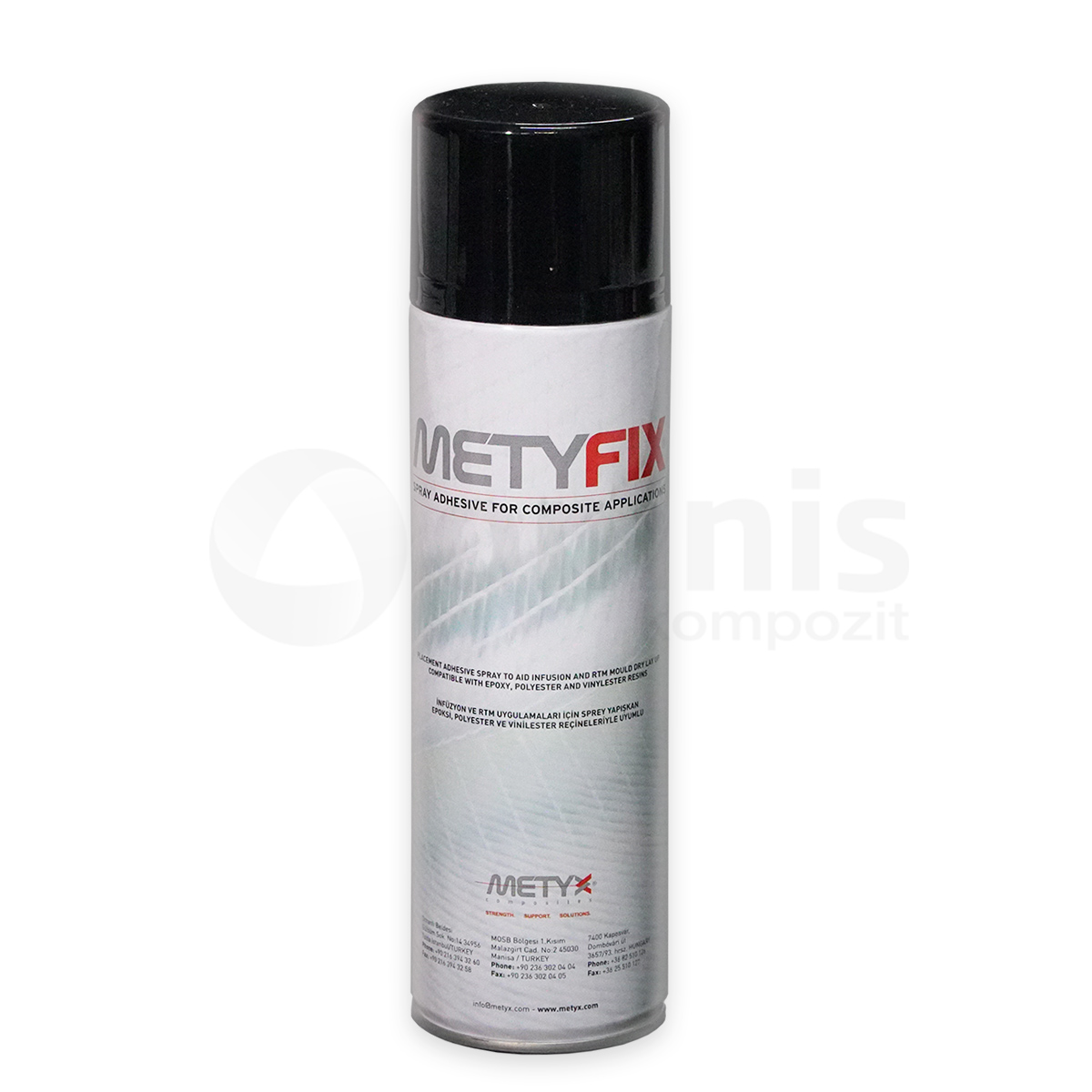
Metyfix Spray Adhesive
Review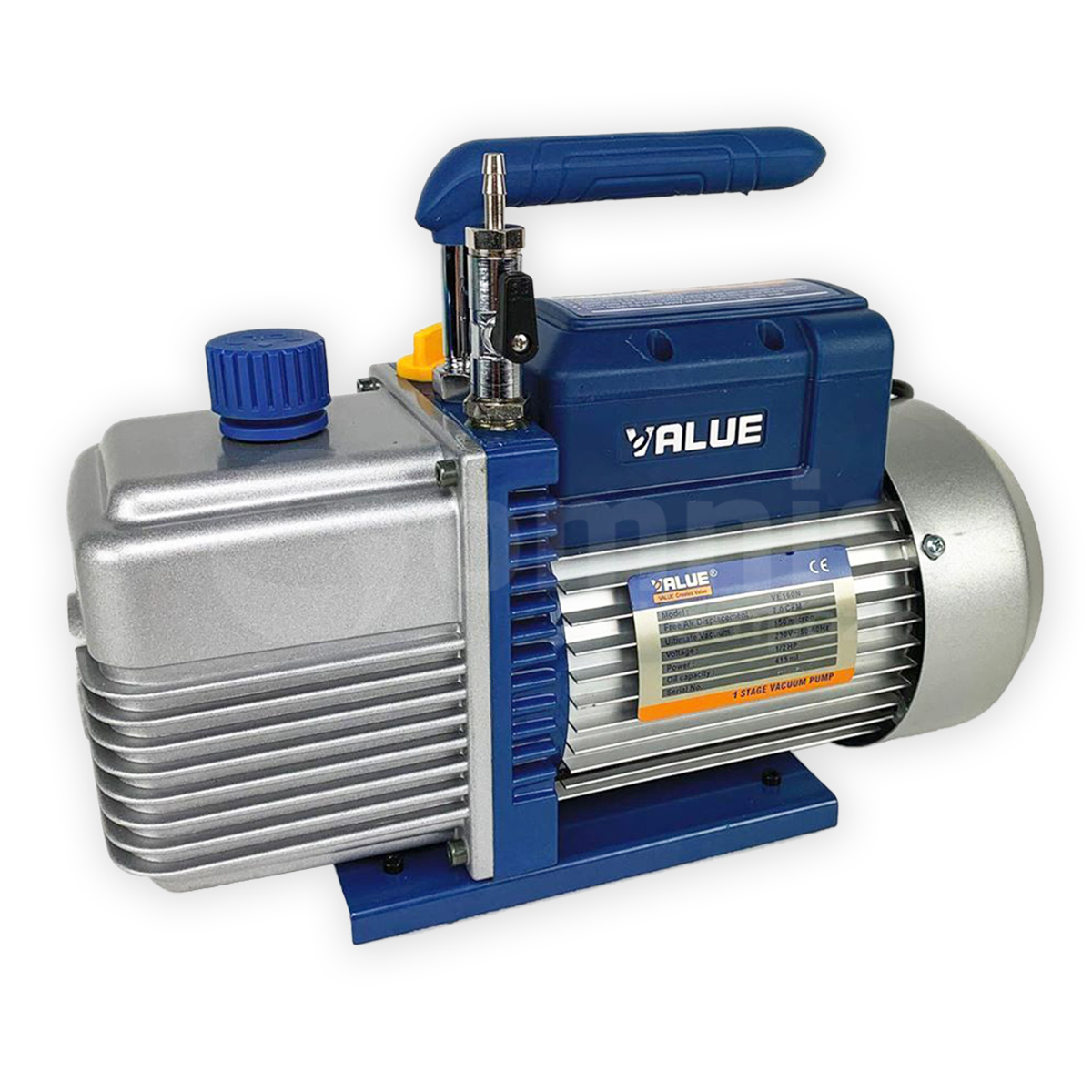
Vacuum Pump
Review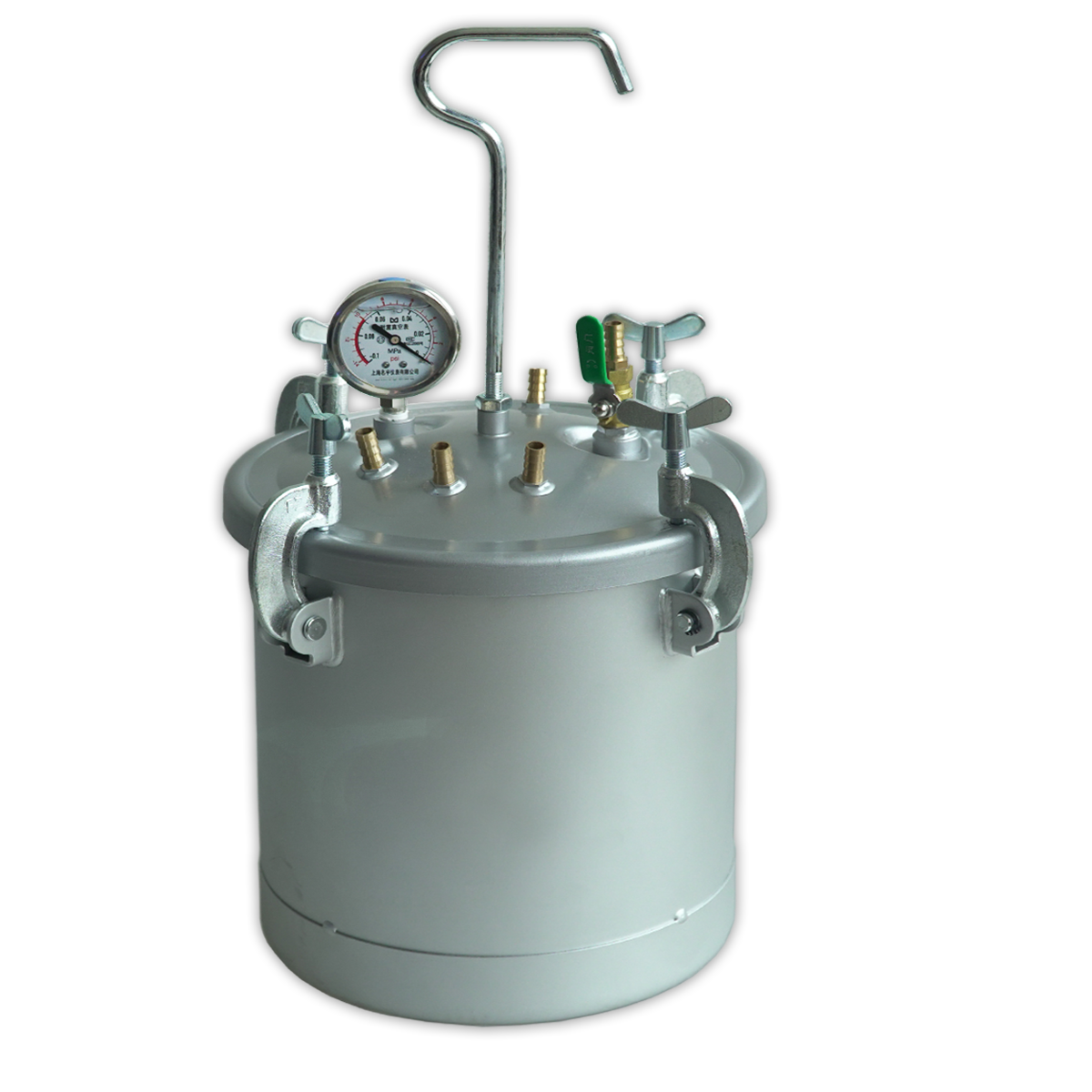
Resin Catch Pot
Review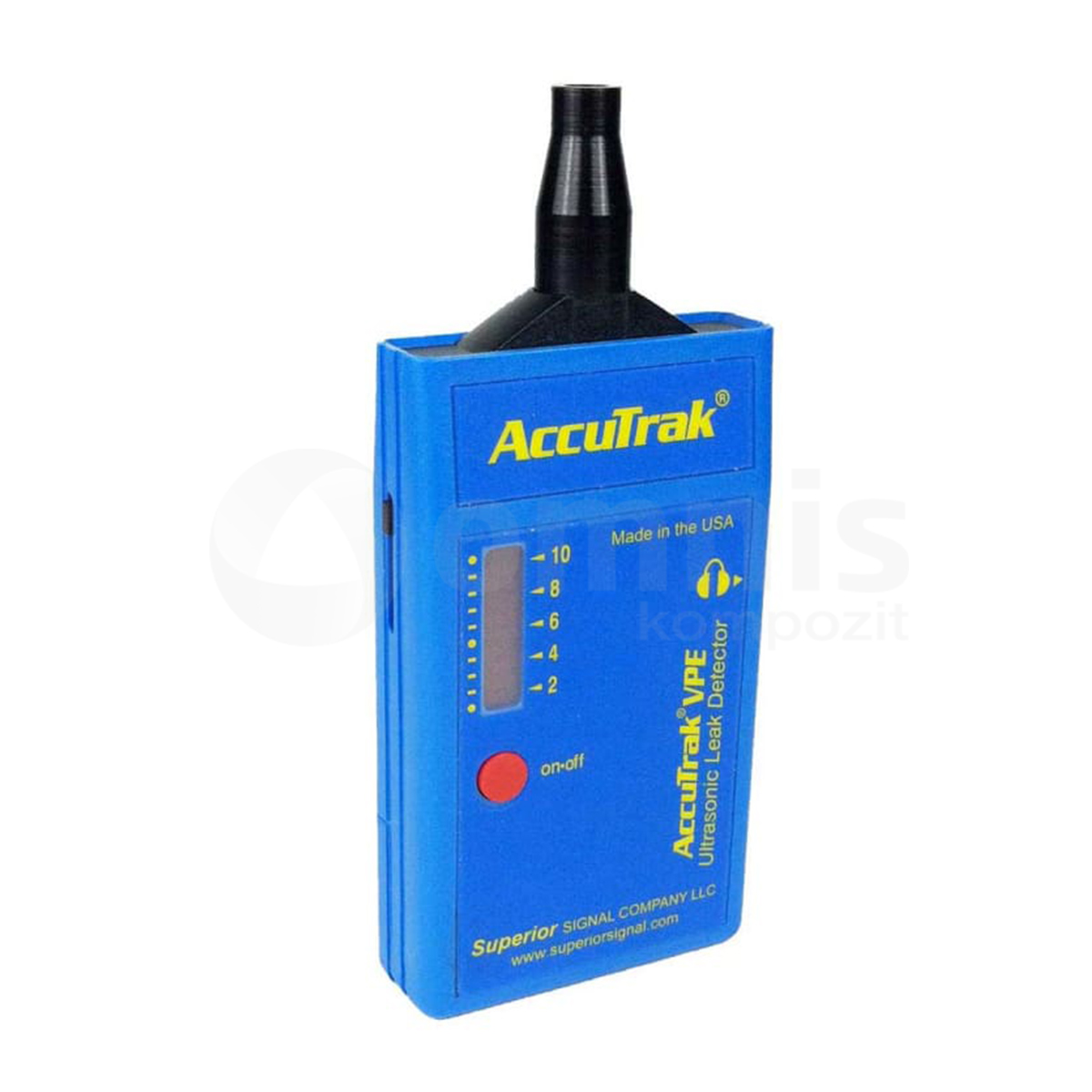
Vacuum Leak Detector
Review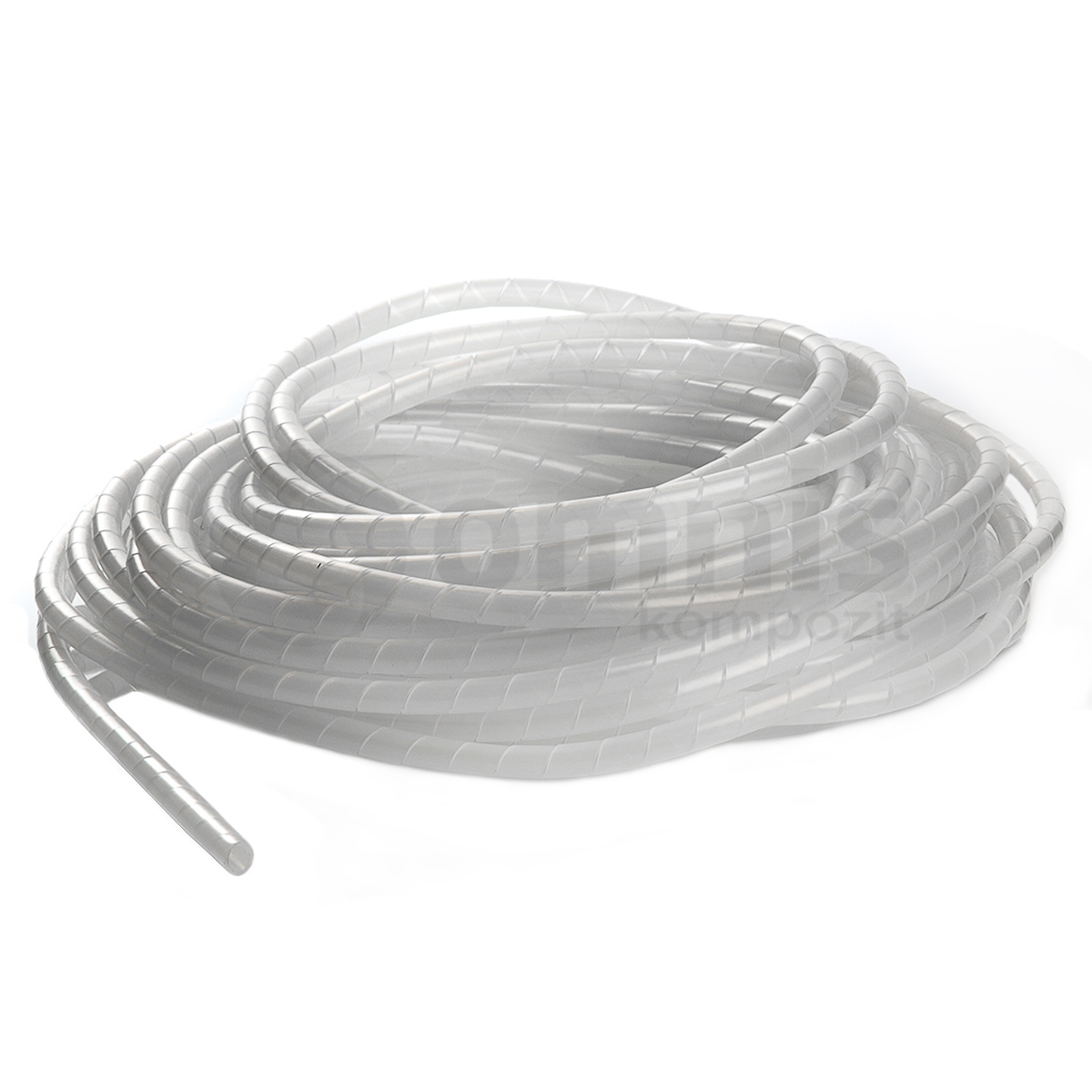
Spiral Infusion Hose No:4
Review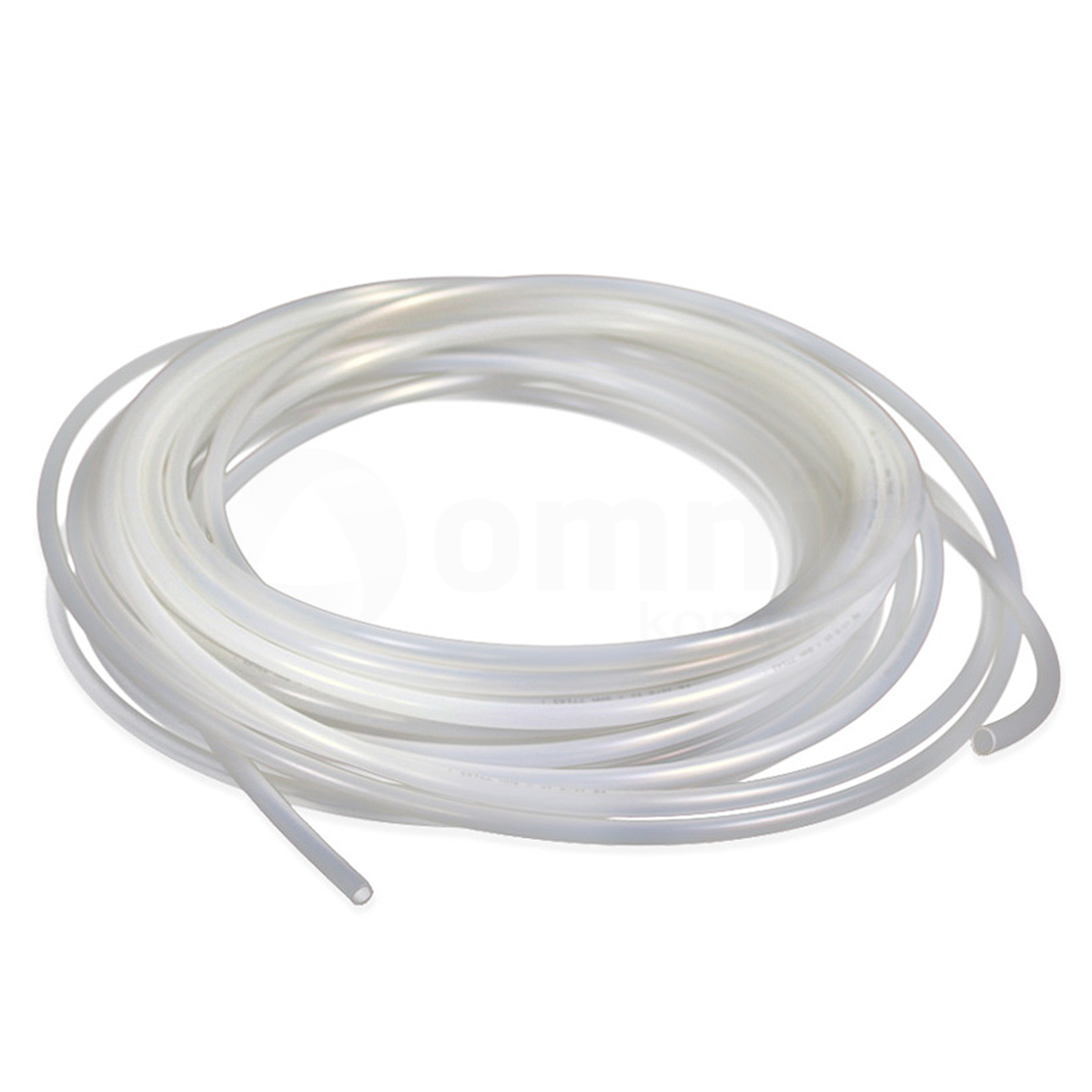
Infusion Hose 10×12 mm
Review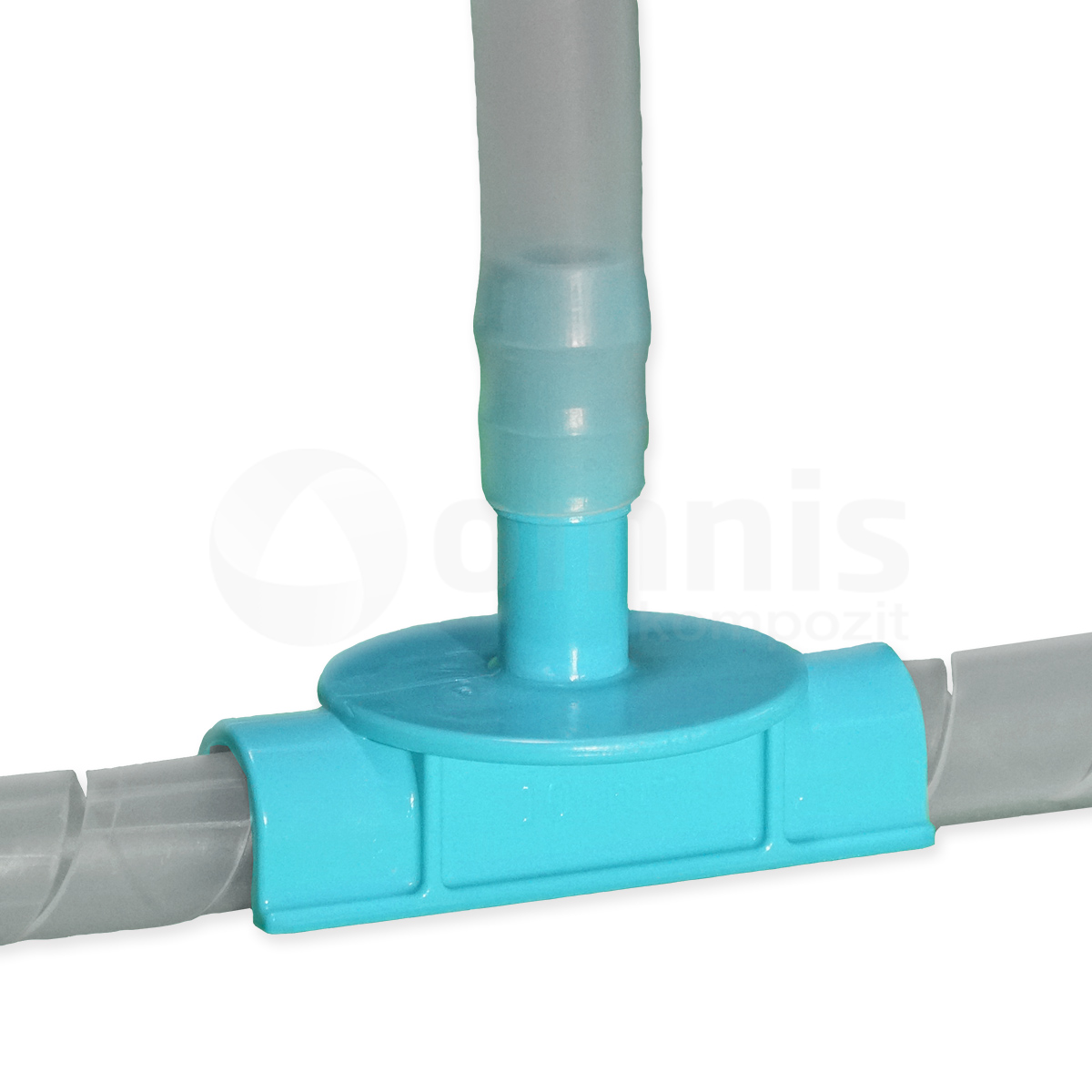
Infusion Resin T Inlet Connector
Review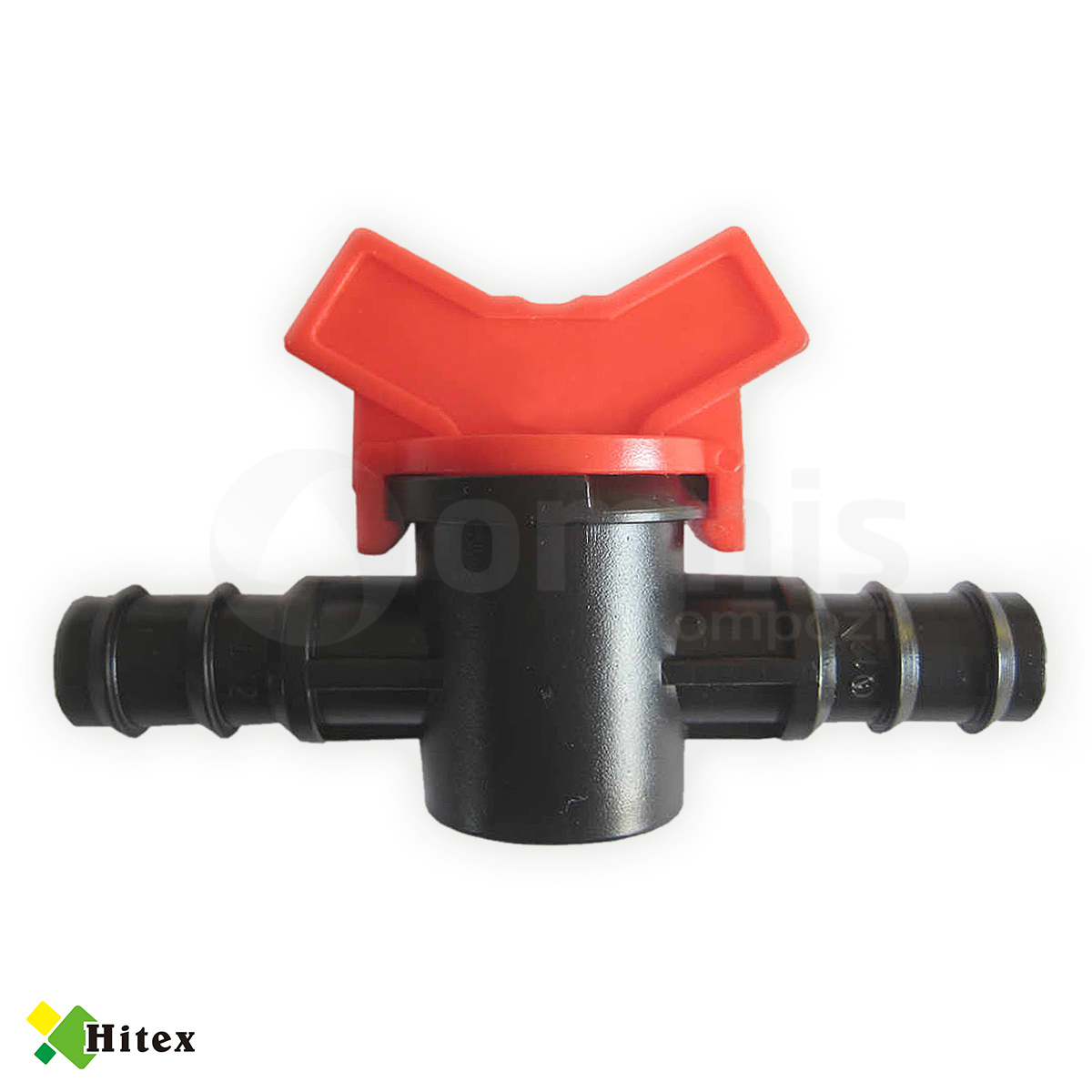
Valved Valve
Review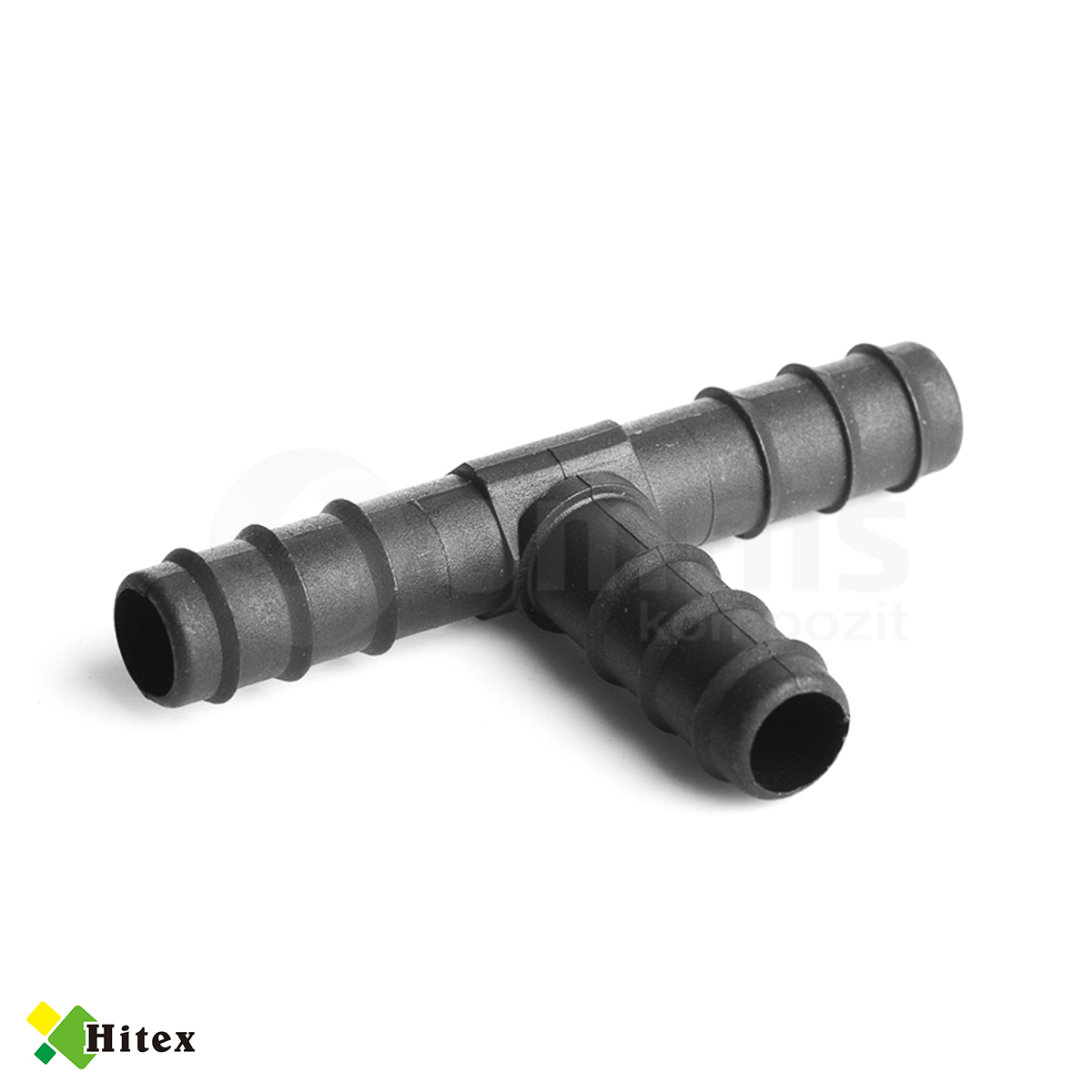
T-Connection
Review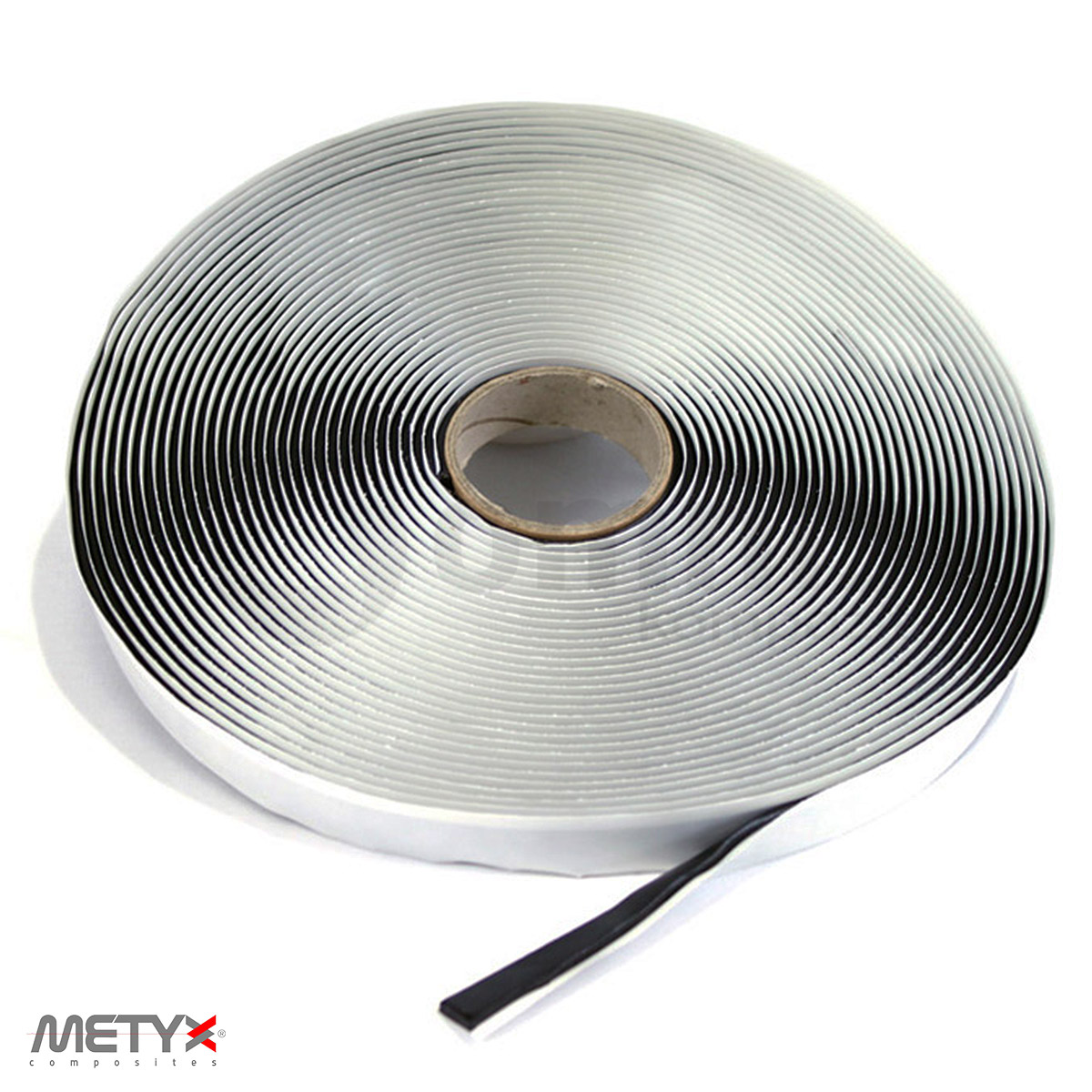
Vacuum Sealing Pastes
Review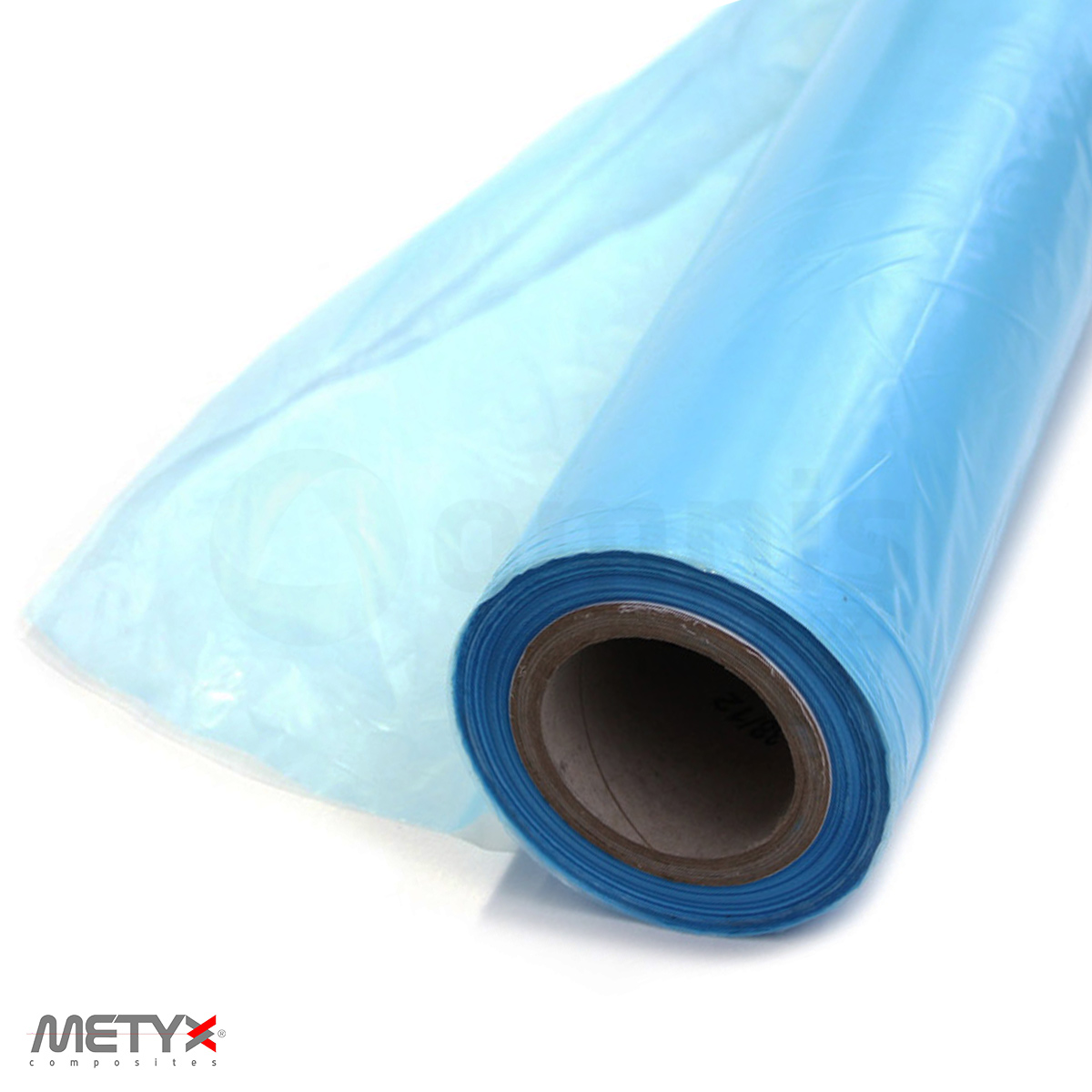
Vacuum Bag
Review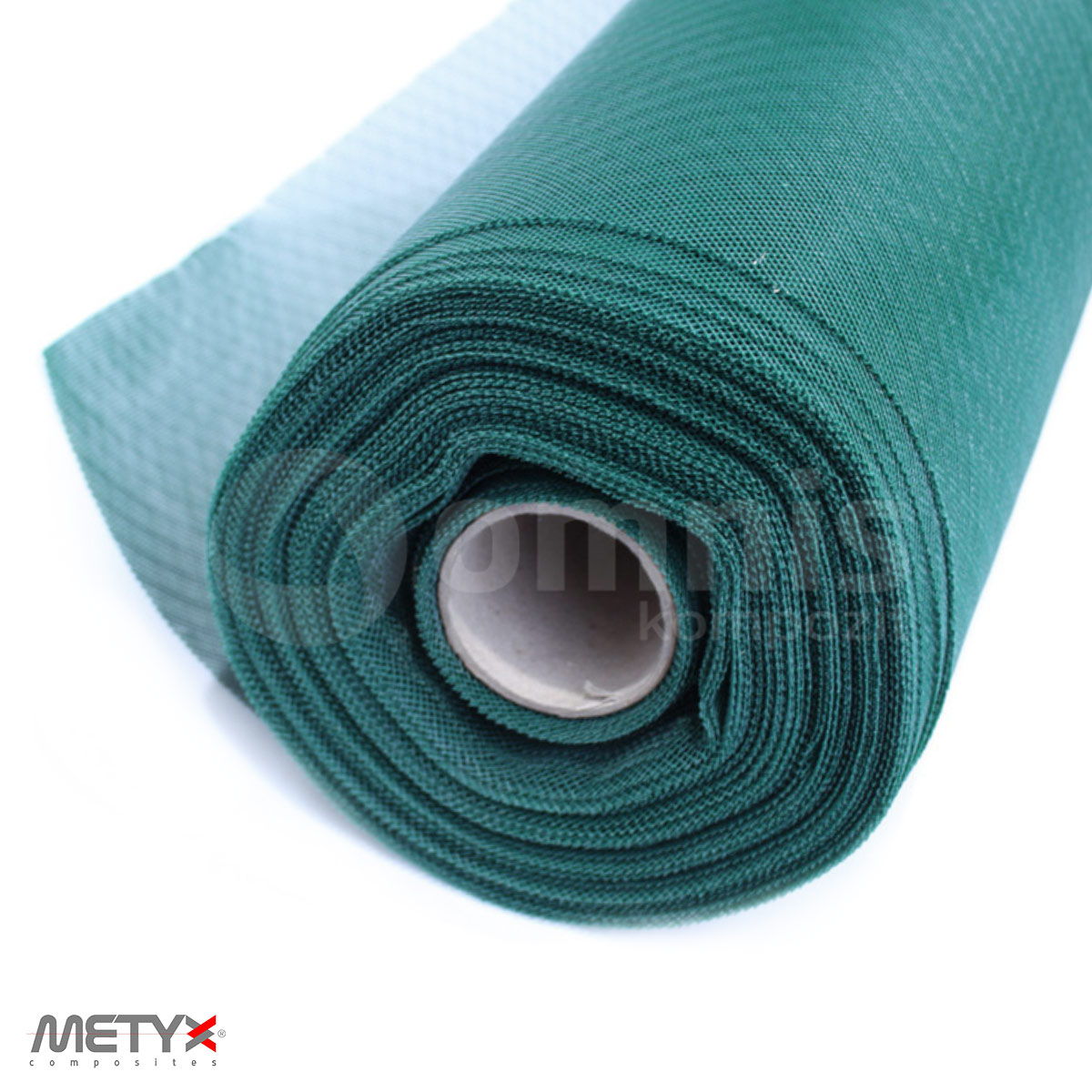
Flow Mesh
Review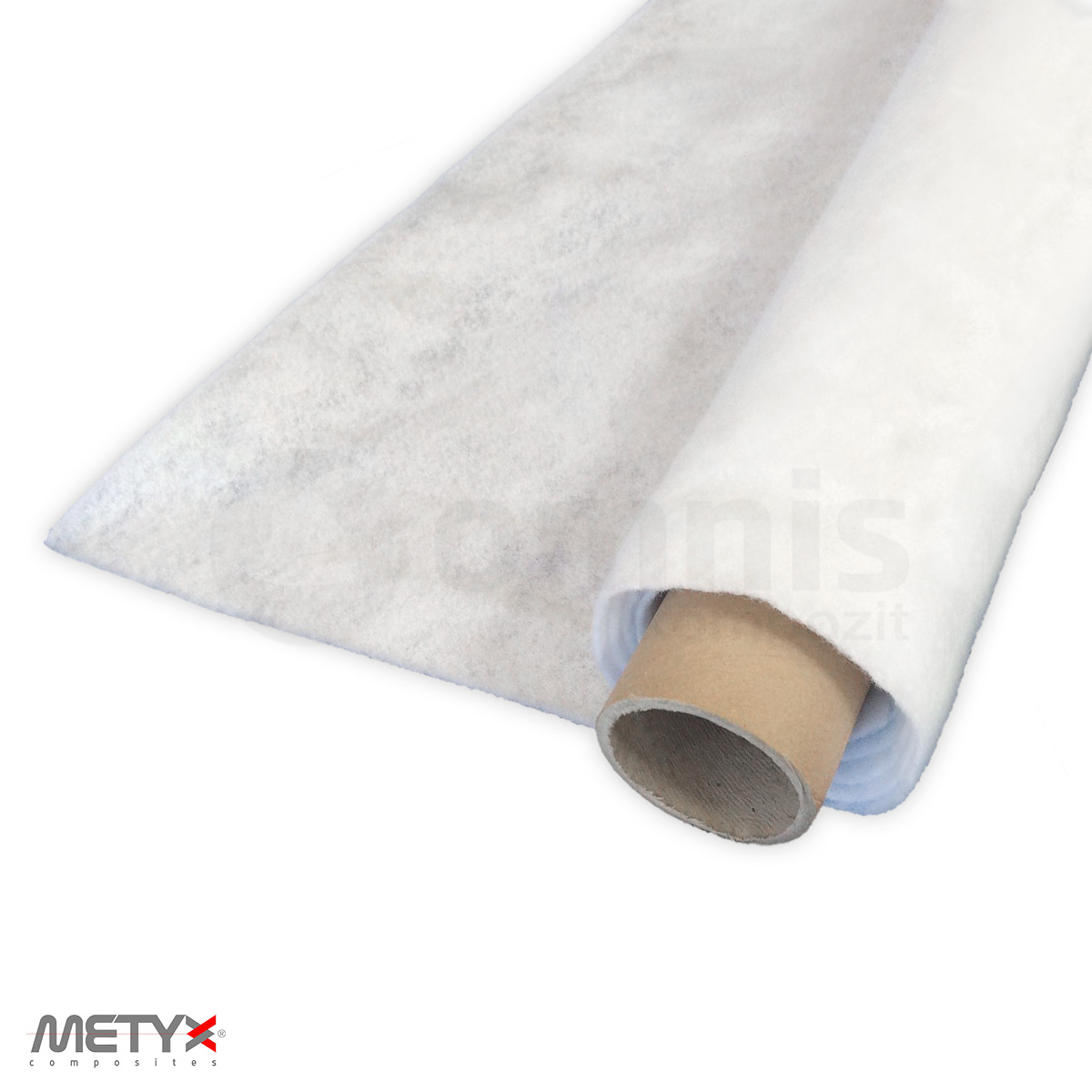
Vacuum Seal
Review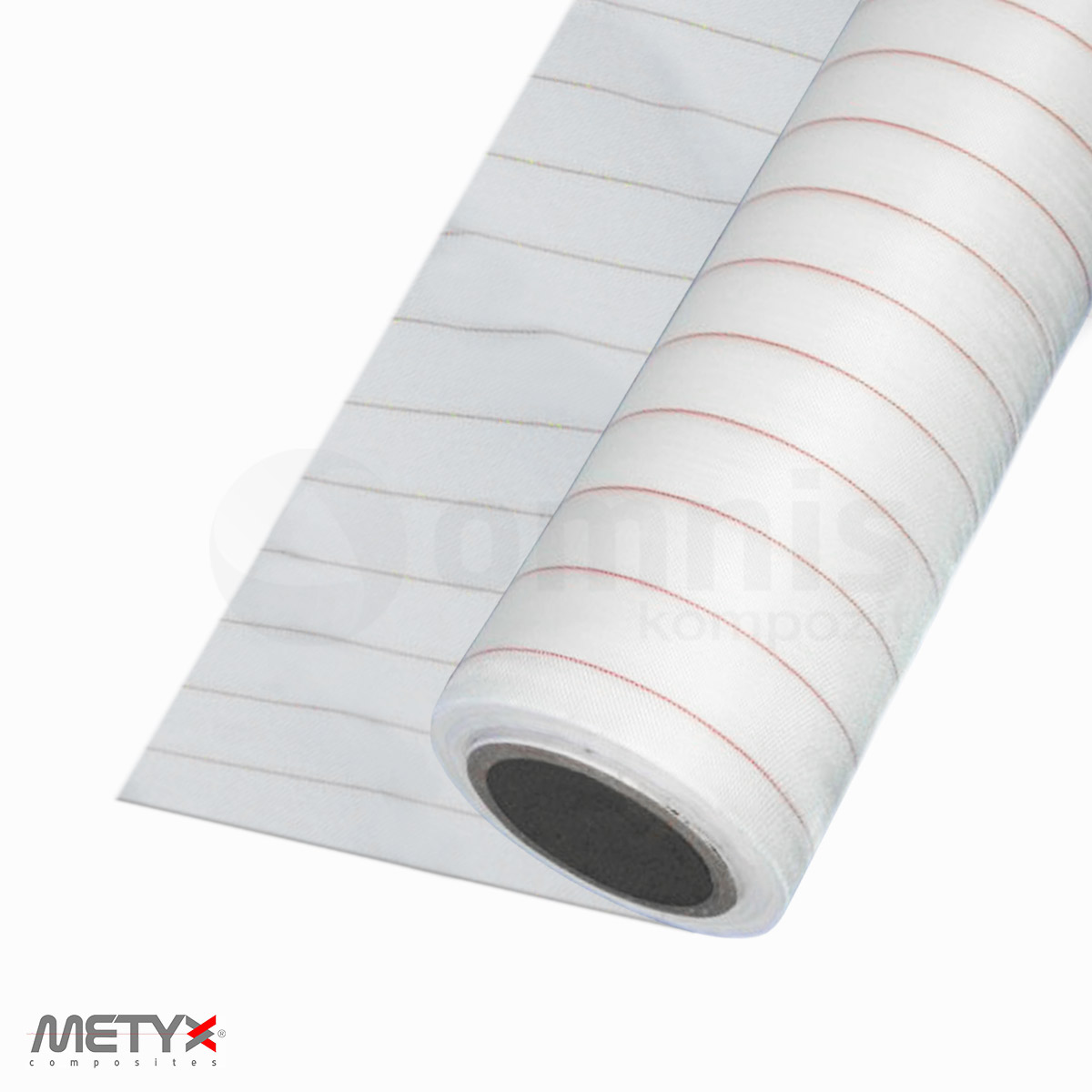
Peeling Fabric
Review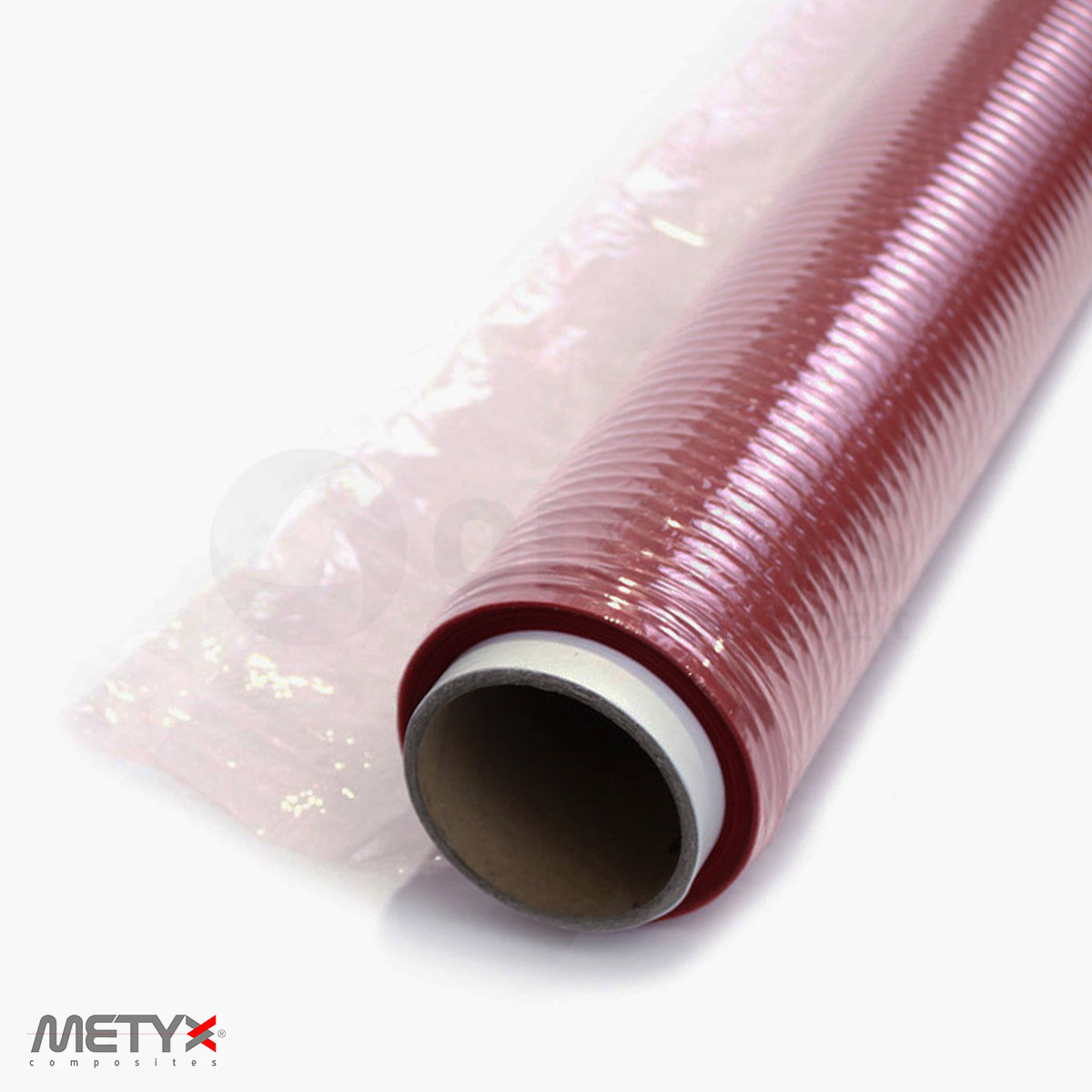
Perforated Release Film
ReviewWhy are vacuum consumables important in the infusion process?
Vacuum consumables are crucial in the infusion process because they ensure a controlled and efficient resin flow into the reinforcement fabric, achieving a high-quality composite material with excellent strength-to-weight ratios. These consumables help maintain a consistent vacuum pressure throughout the infusion process, preventing air entrapment and ensuring the resin fully saturates the reinforcement material. This not only enhances the structural integrity of the final product but also reduces waste and minimizes the risk of defects. The proper use of vacuum consumables is key to achieving optimal results in vacuum infusion projects, making them a fundamental aspect of the composites manufacturing process.
What types of vacuum consumables are available?
A wide variety of vacuum consumables are available to cater to different needs and stages of the vacuum infusion process. These include vacuum bags that encase the laminate and resin, ensuring airtight sealing; peel ply, which allows for easy removal of the bagging materials; release films that prevent the resin from adhering to the bag; breather fabrics that ensure even distribution of vacuum pressure and facilitate resin flow; and sealant tapes that secure the vacuum bag to the mold. Each type of consumable plays a specific role in enhancing the efficiency and effectiveness of the infusion process, making it crucial to select the right materials for your specific project requirements.
How do I choose the right vacuum consumables for my project?
Choosing the right vacuum consumables for your project involves understanding the specific requirements of your composite part, including its size, shape, and the type of resin system being used. Consider the compatibility of the consumables with the resin and reinforcement materials, as well as the desired finish and structural properties of the final product. It’s also important to factor in the complexity of the mold and the expected vacuum pressure to ensure that the consumables can withstand the infusion process without failure. Consulting with experts or suppliers can provide valuable insights and recommendations tailored to your project’s needs.
Can vacuum consumables be reused?
The reusability of vacuum consumables depends on the type of material and its condition after use. Some consumables, like certain types of release films and peel plies, are generally single-use due to resin contamination or damage during the demolding process. However, more durable items such as vacuum bags and some breather fabrics may be reused if they are carefully cleaned and inspected for integrity after each use. Reusing vacuum consumables when possible can reduce costs and environmental impact, but it’s crucial to ensure that the quality of the infusion process is not compromised by worn or damaged materials.
What are the key factors to consider when selecting vacuum consumables?
When selecting vacuum consumables, key factors to consider include the compatibility with the resin and reinforcement materials, the expected vacuum pressure, the complexity of the mold, and the desired finish of the final product. Additionally, the durability and potential for reuse of the consumables should be evaluated to optimize cost-efficiency and environmental sustainability. It’s also important to consider the supplier’s reputation and the quality of the consumables to ensure reliable performance throughout the infusion process. By carefully assessing these factors, you can select products that will contribute to the success of your composite manufacturing projects.
How do vacuum consumables affect the quality of the final product?
Vacuum consumables have a significant impact on the quality of the final composite product. High-quality consumables ensure airtight sealing and uniform vacuum pressure, which are critical for achieving complete resin saturation and minimizing voids within the laminate. This results in a composite material with optimal mechanical properties, including strength, stiffness, and durability. The choice of peel ply and release film can also affect the surface finish of the part, influencing both its aesthetic appeal and the need for post-processing. Using the right vacuum consumables is essential for producing composite parts that meet the highest standards of quality and performance.