Vacuum Bags
A vacuum bag is a critical component in the field of composite manufacturing, designed to encase materials during the vacuum bagging process. Made from a specialized vacuum bagging film, this bag forms a seal around the composite layup, allowing a vacuum to be applied. The application of vacuum pressure ensures the composite material is compacted and conforms precisely to the mold shape while removing any trapped air or excess resin. Utilizing vacuum bags dramatically improves the quality and integrity of composite parts, making them essential for producing lightweight and strong components for a variety of industries, including aerospace, automotive, and sports equipment.
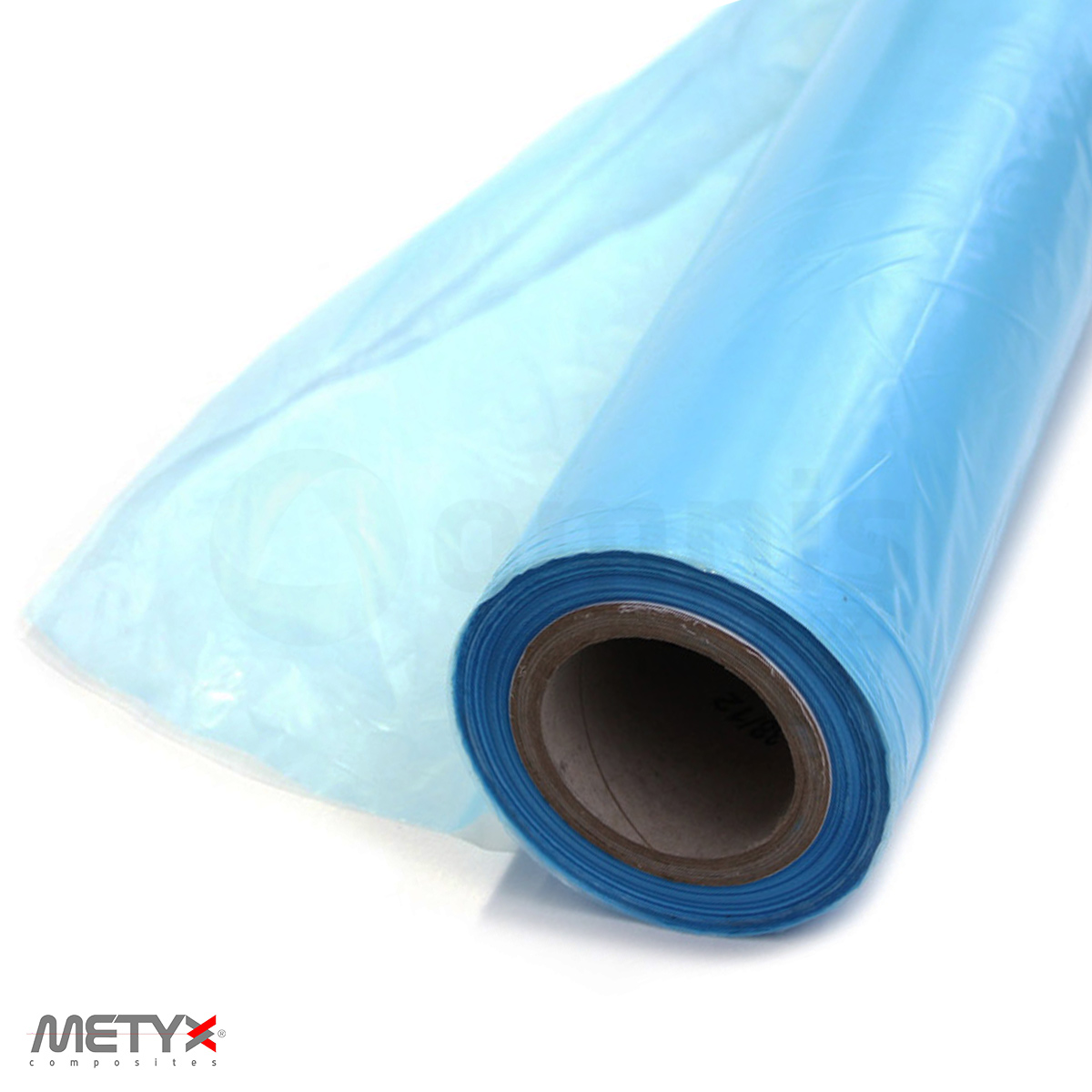
Vacuum Bag
ReviewHow does vacuum bagging work in composite manufacturing?
Vacuum bagging is a sophisticated process used in composite manufacturing to create high-strength, lightweight components with superior surface finishes. This method involves placing the composite layup inside a vacuum bag, then extracting the air to create a vacuum. The vacuum pressure compacts the material against the mold, ensuring that the resin is evenly distributed and that any excess resin and air are removed. Vacuum bagging enhances the fiber-to-resin ratio, reduces voids, and ensures a consistent laminate thickness, leading to parts with improved mechanical properties and quality.
What are the main advantages of using vacuum bags in composites?
The use in composite manufacturing offers numerous advantages, including improved laminate consolidation, reduced void content, and enhanced mechanical properties. Vacuum bagging ensures even pressure distribution over the layup, resulting in higher-quality parts with better dimensional accuracy. This process also allows for greater control over resin content, leading to lighter, stronger components. Furthermore, vacuum bags contribute to a cleaner working environment by containing the resin within the bag, minimizing exposure to volatile organic compounds (VOCs).
Can vacuum bags be used with all types of resin systems?
Vacuum bags are highly versatile and can be used with a wide range of resin systems, including epoxy, polyester, and vinylester resins. The key is selecting the right type of vacuum bagging film that is compatible with the specific resin system used in the manufacturing process. Certain films are better suited for specific resins due to differences in chemical resistance and temperature tolerance. Understanding the properties of both the resin system and material is crucial for achieving optimal results.
How do I choose the right vacuum bag for my application?
Choosing the right vacuum bag involves considering several factors such as the type of resin system, the curing temperature, and the complexity of the part geometry. The vacuum bagging film should be chemically compatible with the resin and able to withstand the curing process’s temperature. The film’s thickness and durability should also match the application’s demands, ensuring it does not rupture or leak under vacuum pressure. Consulting with material suppliers and reviewing product specifications can help in selecting the most suitable product for your specific needs.
Are vacuum bags reusable, or are they single-use?
Vacuum bags are generally designed for single-use to ensure the highest level of quality and reliability in composite manufacturing. Using a new product for each part minimizes the risk of contamination and ensures optimal vacuum integrity. However, there are some reusable vacuum bagging systems available for certain applications. These systems can offer cost savings and reduce waste for large-scale productions or specific processes where the bag’s integrity is not compromised after initial use.
How does the vacuum bag affect the quality of the final composite product?
The product plays a crucial role in determining the quality of the final composite product. By applying uniform pressure across the composite layup and removing excess resin and air, the vacuum bag ensures the laminate is compact and void-free, resulting in improved mechanical properties. The process also allows for better fiber-to-resin ratios and ensures that the composite conforms precisely to the mold, enhancing the part’s structural integrity and surface finish.
Can vacuum bags be used in high-temperature curing processes?
Yes, they can be used in high-temperature curing processes, but it is essential to select a vacuum bagging film that can withstand the specific curing temperatures. High-performance films are designed to resist degradation at elevated temperatures, ensuring they maintain their integrity and functionality throughout the curing cycle. Selecting the appropriate film type for high-temperature applications is vital for achieving successful outcomes and preventing film failure.
What are the differences between vacuum bags and other bagging materials?
Vacuum bags differ from other bagging materials in their specific purpose and functionality within the composite manufacturing process. While bags are designed to encase the composite layup and apply a vacuum, other materials like release films, peel plies, and breather fabrics serve different functions, such as facilitating part release, providing a textured surface for bonding, or ensuring even resin distribution. Each material plays a unique role in optimizing the quality and efficiency of the manufacturing process.
How do you properly seal a vacuum bag to ensure airtight closure?
Properly sealing a bag is critical for achieving an airtight closure and ensuring the effectiveness of the vacuum bagging process. Start by carefully placing the composite layup and any necessary bagging materials inside the vacuum bag. Use sealant tape along the edges of the bag, pressing firmly to eliminate gaps and ensure a complete seal. Pay special attention to corners and connections, using additional sealant tape or tacky tape to address potential leak points. Ensuring the bag is fully sealed without any leaks is essential for maintaining vacuum pressure and achieving optimal compaction.
Are there different types of vacuum bags for specific applications?
There are various types available, each designed for specific applications within composite manufacturing. Differences in vacuum bagging films can include material composition, thickness, and temperature resistance, catering to diverse needs such as high-temperature curing, complex part geometries, or chemical compatibility with specific resin systems. Selecting the right type of bag is crucial for meeting the demands of the application and ensuring the success of the manufacturing process.
How does the thickness of a vacuum bagging film affect its performance?
The thickness of a vacuum bagging film directly affects its performance by influencing its durability, flexibility, and ability to withstand vacuum pressure and potential punctures. Thicker films offer greater resistance to punctures and tears, making them suitable for applications involving sharp or complex geometries. However, they may be less flexible and harder to conform to intricate molds. Conversely, thinner films provide better conformity but may be more susceptible to damage. Balancing thickness with the specific requirements of the application is key to selecting the most effective vacuum bagging film.
How do you troubleshoot common issues with vacuum bagging?
Troubleshooting common issues with vacuum bagging involves identifying and addressing potential sources of problems, such as leaks, inadequate vacuum pressure, or uneven resin distribution. Regularly check the sealant tape and connections for leaks, ensuring the vacuum bag is fully sealed. Use a vacuum gauge to monitor pressure levels, and apply additional sealant tape or adjust the bag placement as needed to achieve the desired vacuum. Additionally, ensure that the bagging materials are correctly positioned to facilitate even resin flow and pressure distribution. By systematically addressing these common issues, manufacturers can optimize the vacuum bagging process for improved results.