Release Film
A release film, also known as a separator film, is a specialized material used in the manufacturing process to prevent sticking between the product and the mold or tooling surface. It acts as a barrier, ensuring easy removal of the finished product from the mold without damaging its surface. These films are designed to withstand various manufacturing conditions, including high temperatures and pressures, making them suitable for use in composite manufacturing, injection molding, and other fabrication processes where a non-stick surface is crucial. Their application ensures a smooth, defect-free finish on the final product.
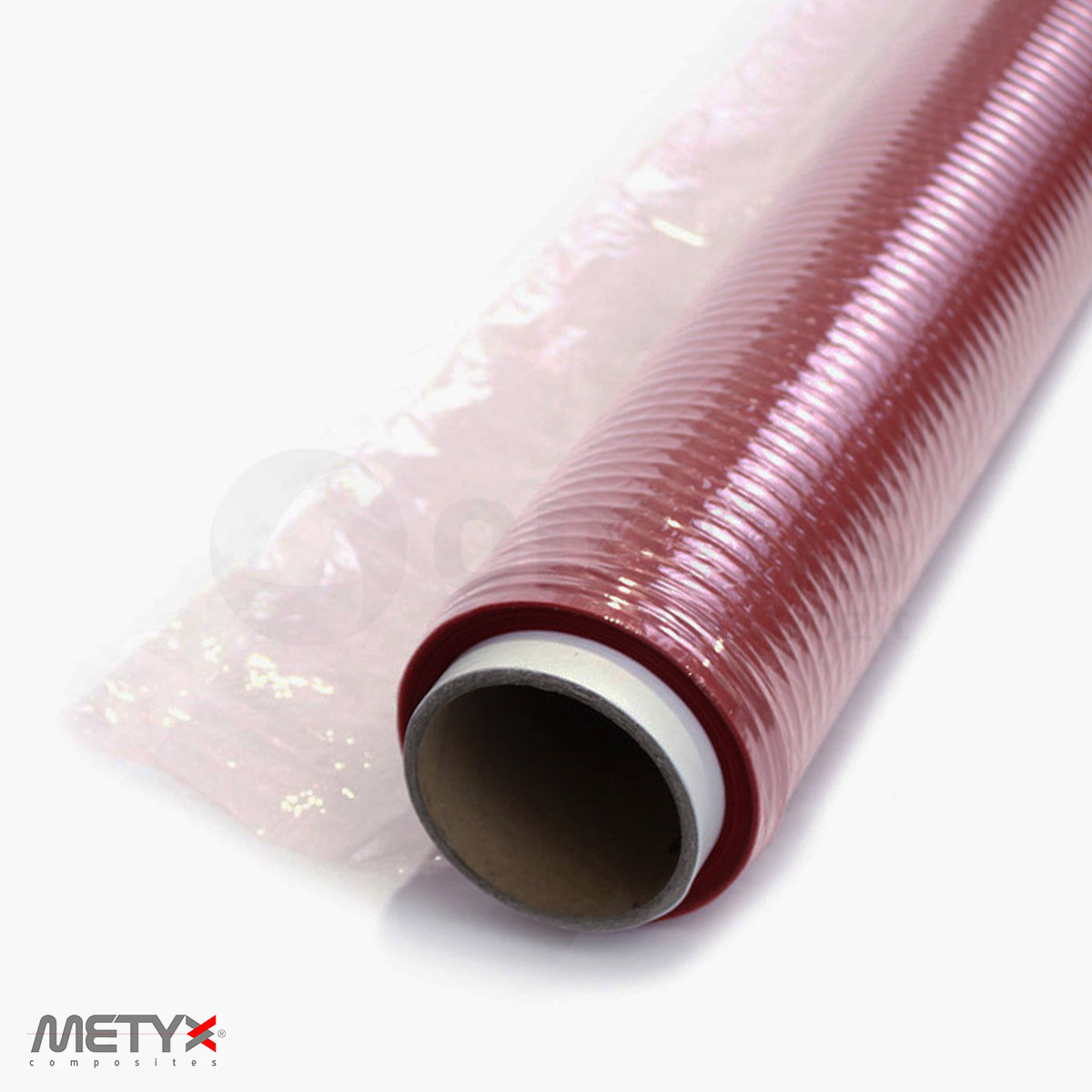
Perforated Release Film
ReviewWhat are the main applications of release films in manufacturing?
The main applications in manufacturing include composite lay-up processes, vacuum bagging operations, resin transfer molding (RTM), and autoclave curing of composite materials. They are widely used in the aerospace, automotive, marine, and sporting goods industries to produce high-quality composite parts. Release films facilitate the easy demolding of parts, protect the mold surface, and can be used to impart a specific surface texture to the finished product. Additionally, they are employed in the production of laminates, adhesives, and coated fabrics where separation between layers or products is required during processing or storage.
Can release films be used in high-temperature processes?
Yes, release films can be used in high-temperature processes. They are specifically engineered to withstand elevated temperatures often encountered in composite manufacturing, such as autoclave curing and resin transfer molding. Release films are made from materials like polytetrafluoroethylene (PTFE), polyester, and polyimide, which maintain their structural integrity and non-stick properties at high temperatures. This makes them ideal for applications requiring thermal stability, such as in the aerospace and automotive industries, where composite parts are cured at high temperatures to achieve desired mechanical properties.
How do I choose the right type of release film for my application?
Choosing the right type of product for your application involves considering several factors, including the manufacturing process, temperature requirements, desired surface finish, and chemical compatibility with the resin system. Evaluate the maximum temperature and pressure the film needs to withstand, and select a material that meets these requirements. Consider whether a perforated, non-perforated, or micro-perforated film is needed based on the desired resin flow and breathability. Additionally, the choice may be influenced by whether a glossy or matte finish is desired on the final product. Consulting with release film suppliers can provide valuable guidance in selecting the most suitable film for your specific application.
What materials are release films typically made from?
Release films are typically made from materials such as polytetrafluoroethylene (PTFE), polyester (PET), polyimide, and nylon due to their excellent thermal stability, chemical resistance, and non-stick properties. PTFE films are particularly valued for their high-temperature resistance and inertness, making them suitable for demanding applications. Polyester films offer a balance of performance and cost-effectiveness for moderate temperature processes. Polyimide films are chosen for their exceptional thermal stability in high-temperature applications. The selection of material depends on the specific requirements of the manufacturing process and the properties desired in the final product.
Are release films reusable or single-use?
Release films can be either reusable or single-use, depending on the material, application, and conditions of use. Some high-quality films, especially those made from durable materials like PTFE, can withstand multiple uses without degradation of their non-stick properties or physical integrity. However, in applications where the film is exposed to extreme conditions or where absolute surface quality is critical, single-use films may be preferred to ensure consistent results. The decision between reusable and single-use films will depend on cost considerations, environmental impact, and the specific requirements of the manufacturing process.
How do release films affect the surface finish of a product?
Release films can significantly affect the surface finish of a product. The texture and properties of the film’s surface are transferred to the composite or molded part during the curing or molding process. Using a smooth product results in a glossy finish on the final product, while a textured film can create a matte or patterned surface. The choice of product allows manufacturers to control the aesthetic appearance of their products without additional processing steps. Proper selection and application of products are crucial for achieving the desired surface quality and performance characteristics.
What are the benefits of using separator films in composite manufacturing?
The benefits of using separator films in composite manufacturing include improved process efficiency, enhanced product quality, and protection of the mold surface. Separator films prevent the composite material from sticking to the mold, facilitating easy demolding and reducing the risk of defects. They enable the production of parts with consistent surface finishes and can be used to impart specific textures to the product. Additionally, separator films protect the mold from wear and contamination, extending its service life and reducing maintenance requirements. Their use contributes to a more streamlined manufacturing process, resulting in higher-quality composite parts.
What are the key factors to consider when storing release films?
When storing release films, key factors to consider include temperature, humidity, and protection from damage. Films should be stored in a cool, dry place away from direct sunlight and extreme temperatures to prevent degradation of their properties. It is important to maintain a stable environment to avoid changes in the film’s dimensions or adhesion qualities. Films should be kept in their original packaging or wrapped securely to protect them from dust, moisture, and mechanical damage. Proper storage ensures the product remains in optimal condition for use, maintaining their effectiveness and reliability in the manufacturing process.