Polyester Resins
Polyester resins are synthetic resins formed by the reaction of dibasic organic acids and polyhydric alcohols. They are among the most widely used resins in the composites industry, cherished for their versatility, durability, and cost-effectiveness. Polyester resins are known for their excellent mechanical properties, chemical resistance, and ease of handling, making them the backbone of many manufacturing processes. Their adaptability allows them to be tailored for a broad range of applications, from marine and automotive components to construction and consumer goods. Offering an ideal balance between performance and cost, polyester resins provide a foundation for innovation in composite fabrication, enabling designers and engineers to push the boundaries of what's possible.
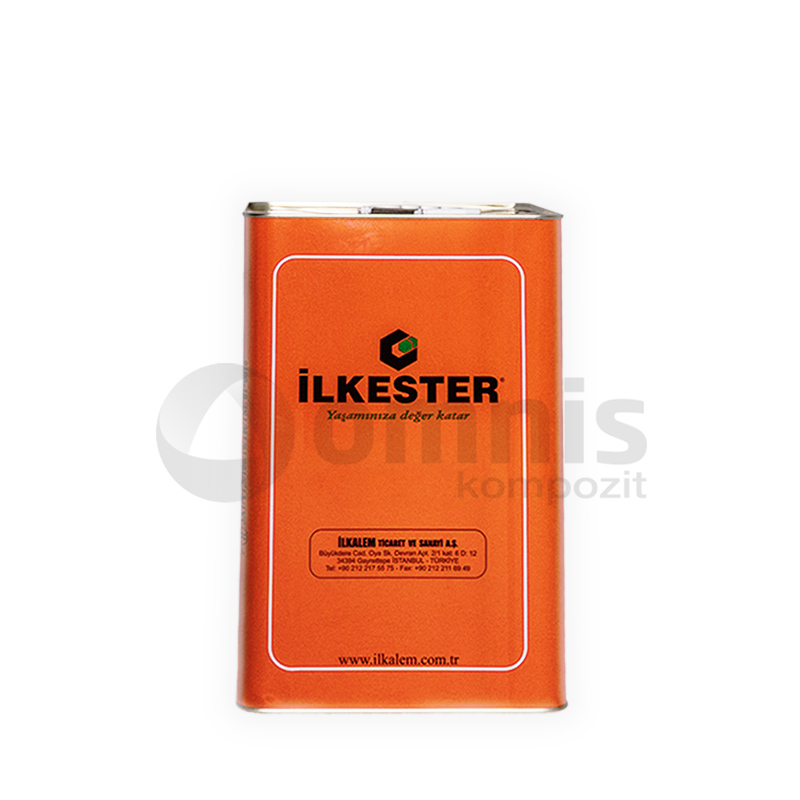
Furniture Type Polyester
Review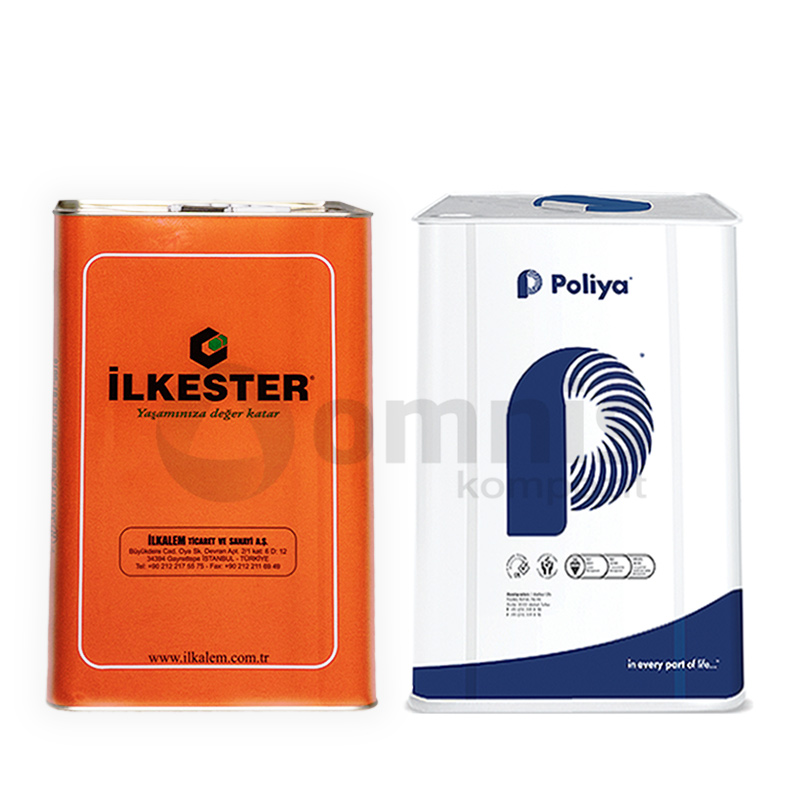
Polyester for Engineering Castings
Review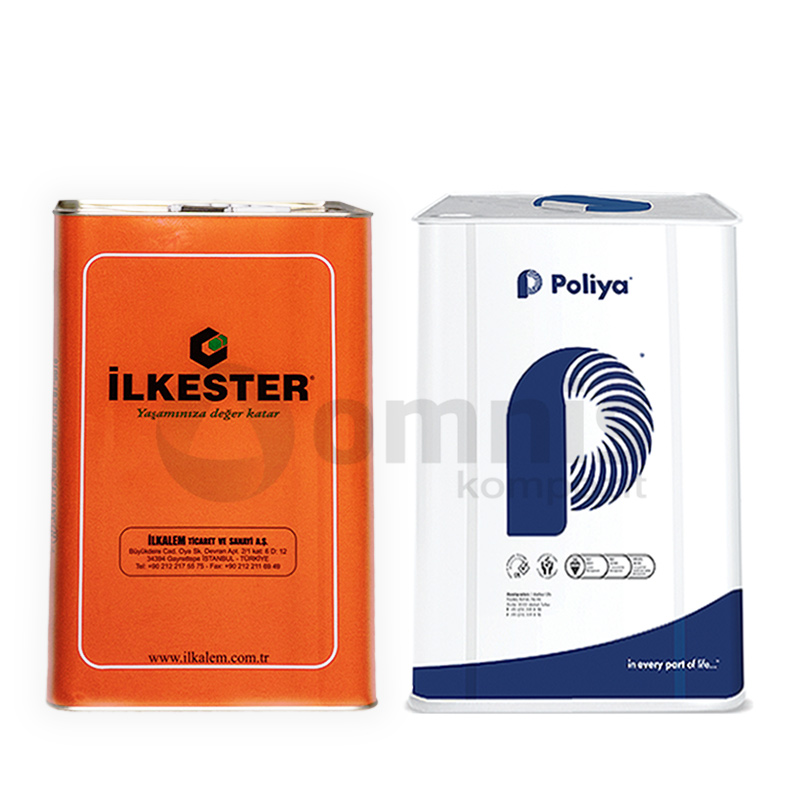
Button Type Polyester
Review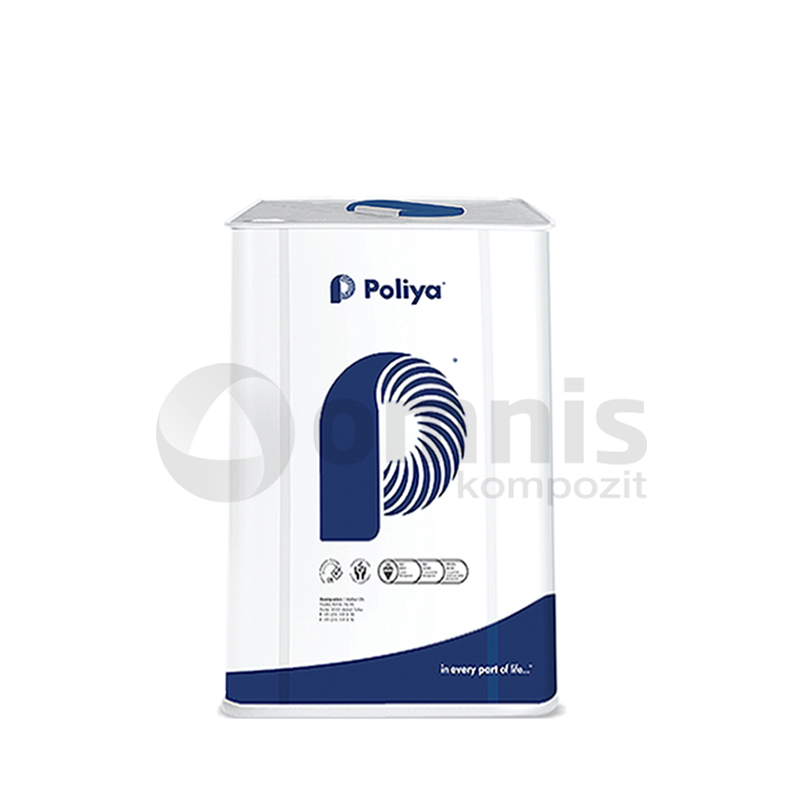
Paste Type Polyester
Review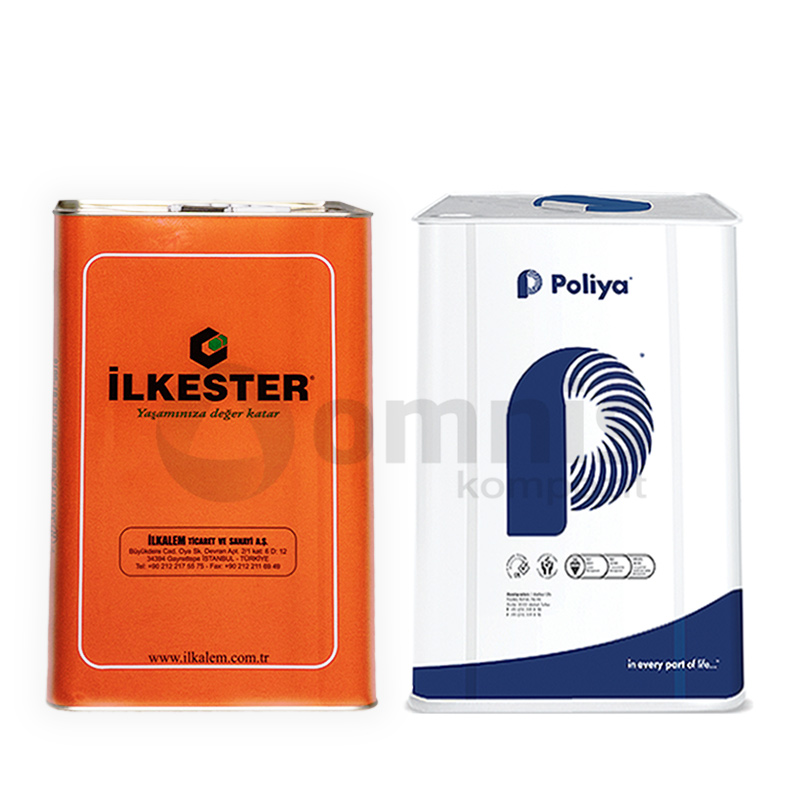
Chemical Resistant Polyester
Review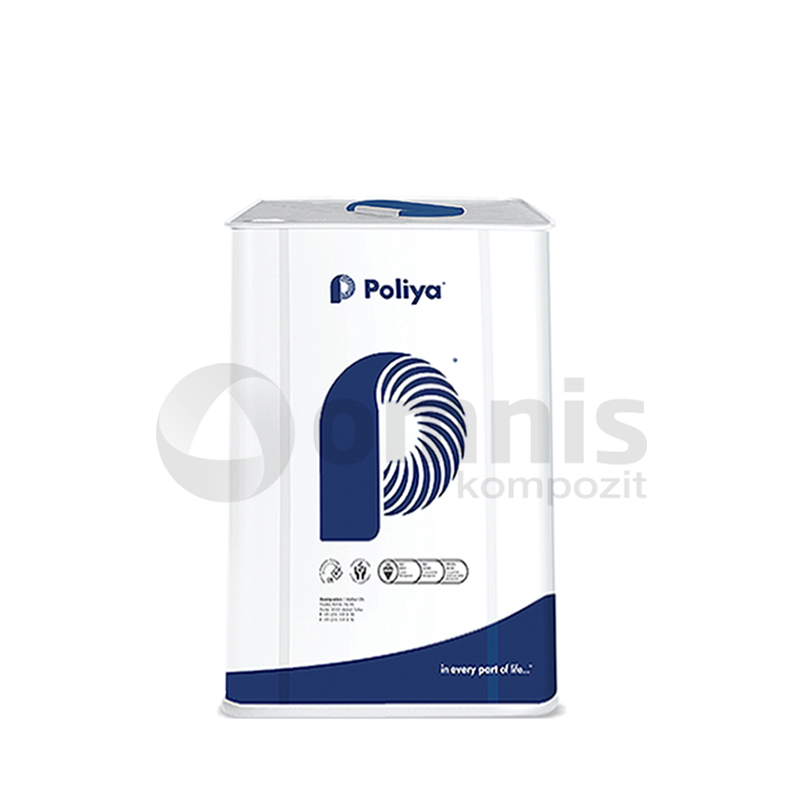
Continuous Drawing Type Polyester
Review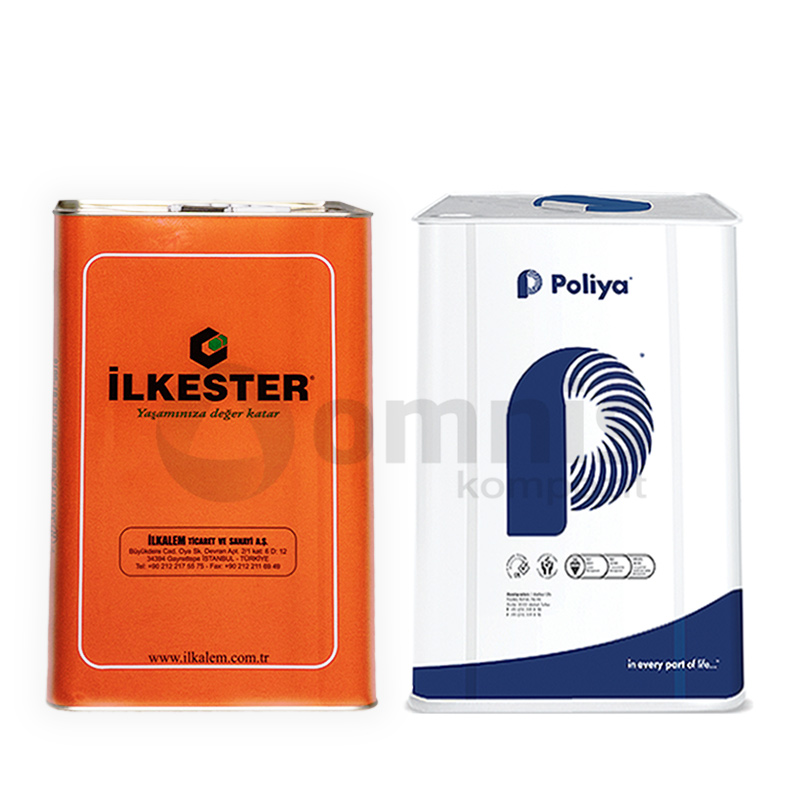
Acrylic Back Applications
Review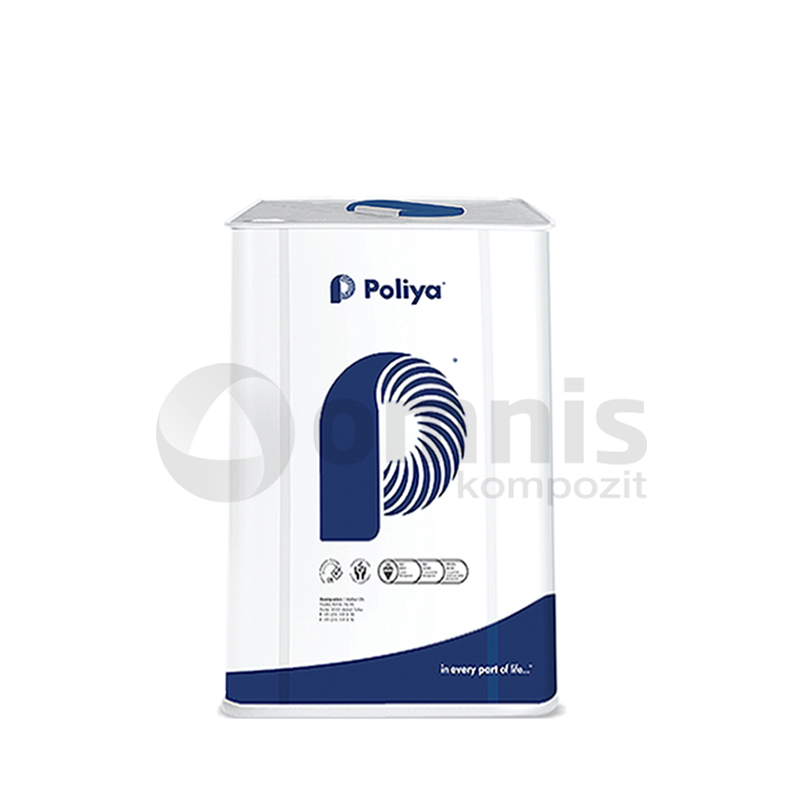
Roving Winding Type Polyester
Review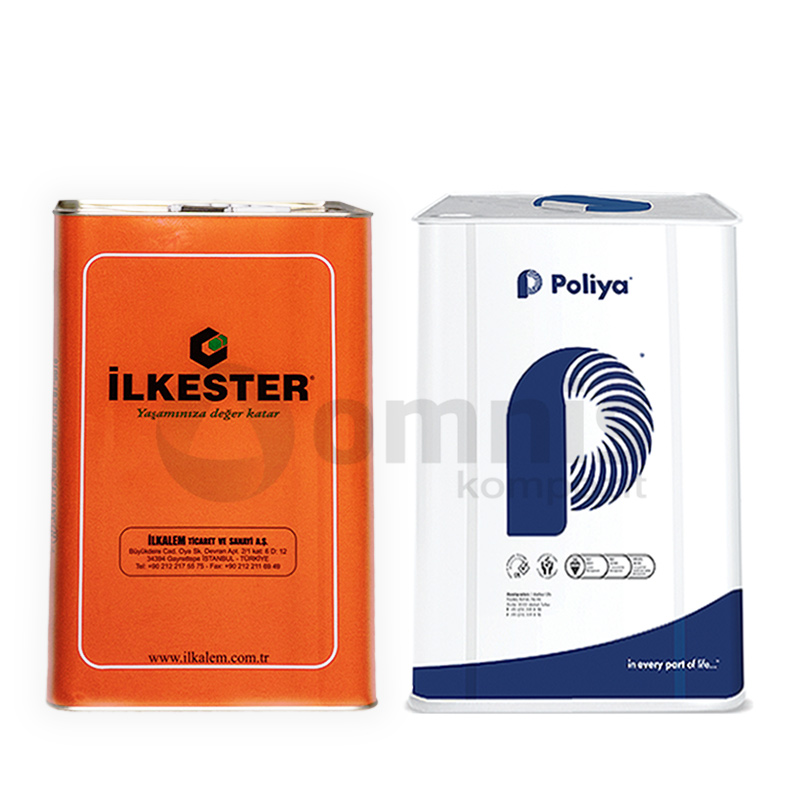
Pultrusion Type Polyester
Review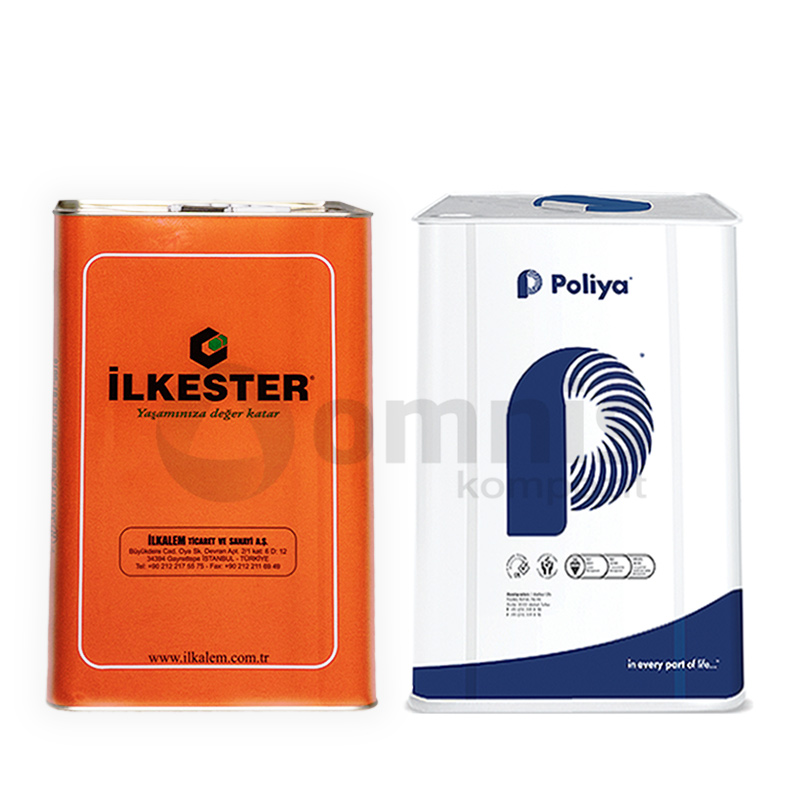
SMC-BMC Type Polyester
Review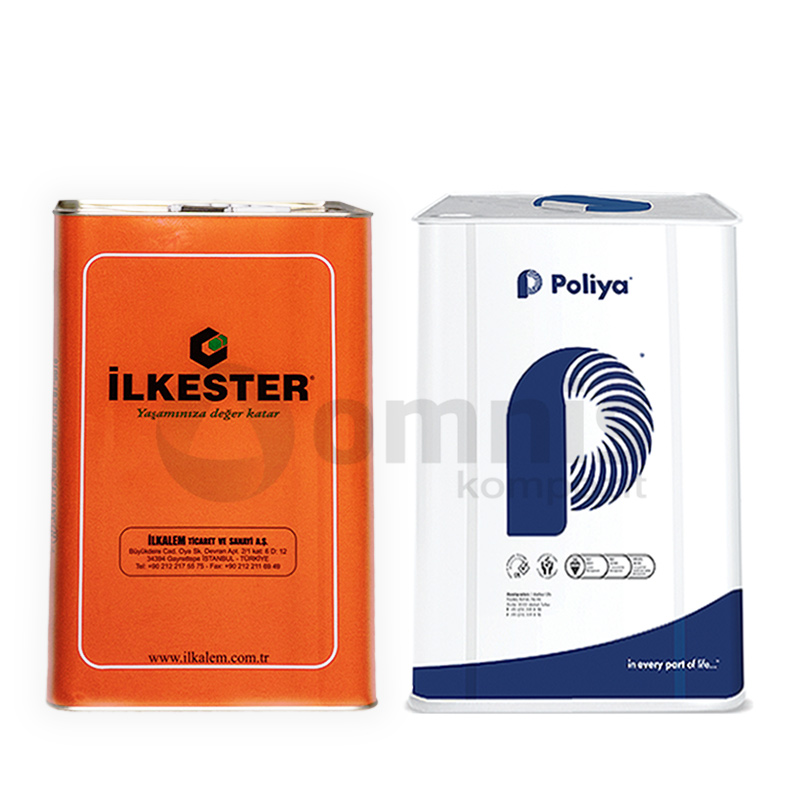
Flame Resistant Polyester
Review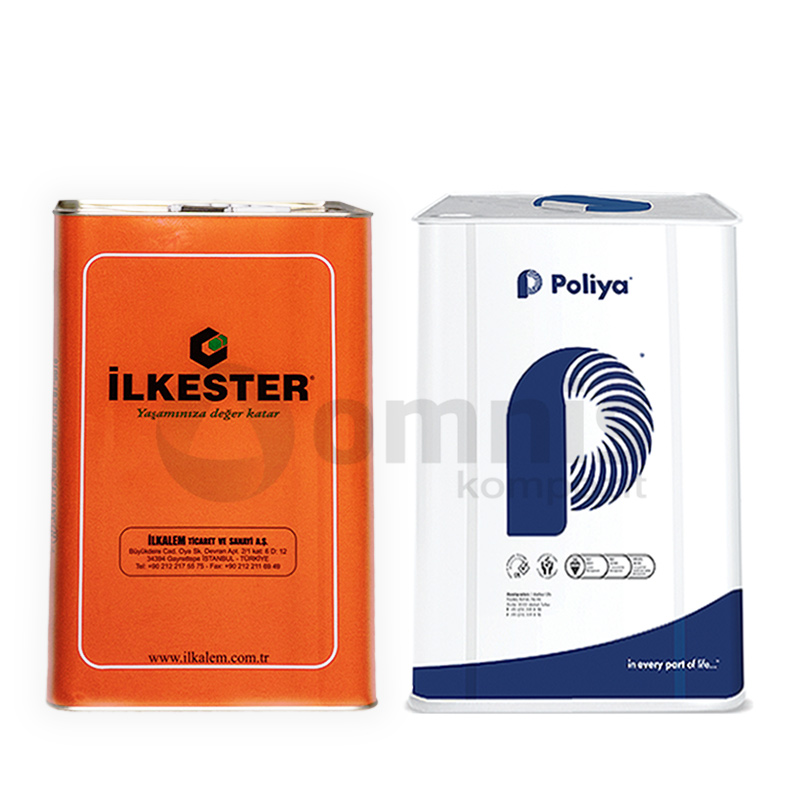
Casting Type Polyester
Review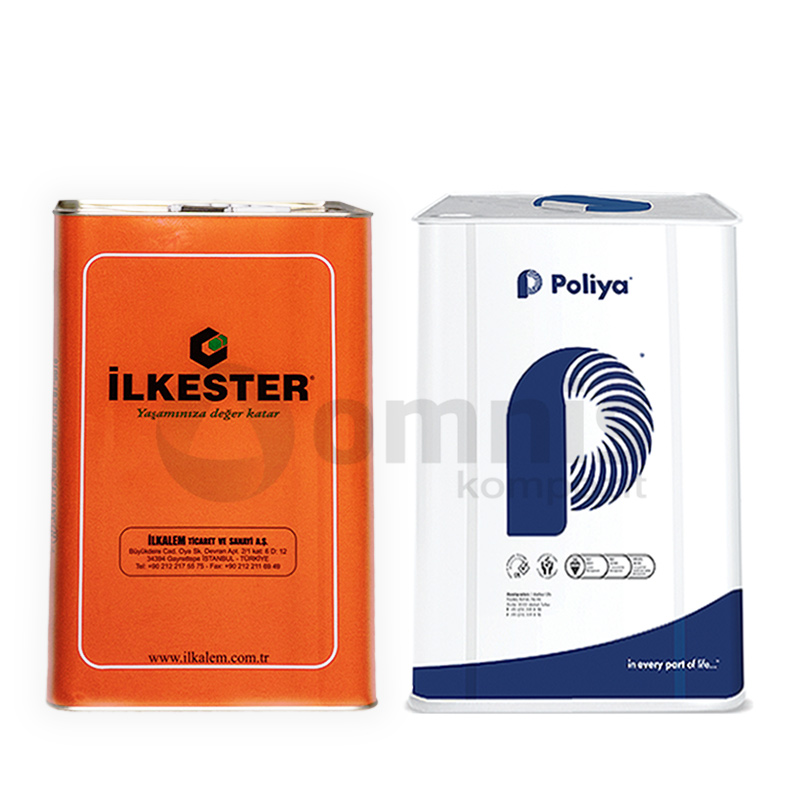
Mold Polyester
Review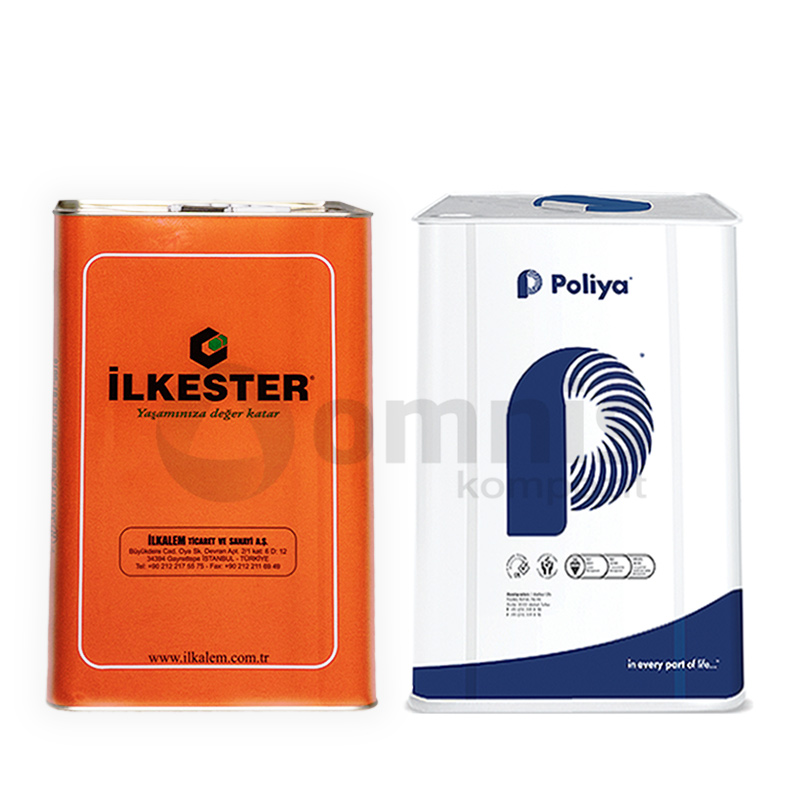
RTM Type Polyester
Review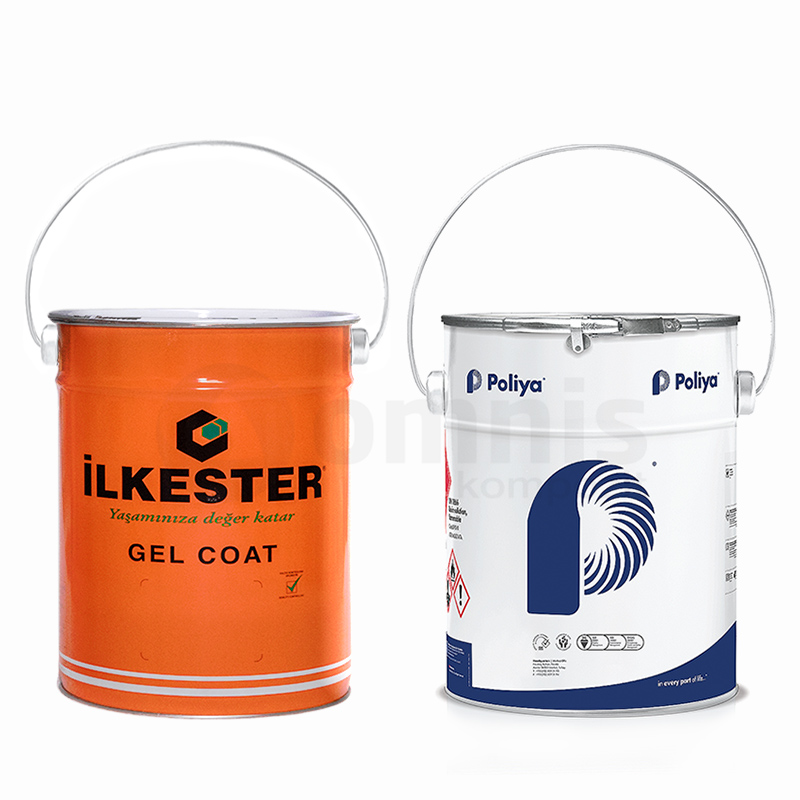
General Purpose Polyester
ReviewHow are polyester resins used in composite materials?
Polyester resins play a pivotal role in composite materials as the matrix that binds reinforcement fibers together, providing shape, structural integrity, and environmental resistance. When combined with fibers like glass or carbon, polyester resins create composite materials that are lightweight yet incredibly strong and durable. This synergy enables the production of parts and structures that can withstand demanding conditions while offering significant weight savings. Commonly used in hand lay-up and spray-up processes, these resins facilitate a wide range of manufacturing techniques, from simple moldings to complex and intricate shapes, making them indispensable in the composites industry.
What are the main types of polyester resins available?
The main types of polyester resins available include orthophthalic, isophthalic, and dicyclopentadiene (DCPD) resins. Orthophthalic resins, often referred to as general-purpose resins, are the most commonly used due to their cost-effectiveness and good mechanical properties. Isophthalic resins offer improved strength, durability, and chemical resistance, making them suitable for more demanding applications. DCPD resins are known for their superior toughness and impact resistance. Additionally, there are specialty polyester resins tailored for specific needs, such as fire-retardant, low-shrink, and low-styrene formulations, each designed to enhance certain characteristics of the composite material for specific applications.
How do I choose the right polyester resin for my project?
Choosing the right polyester resin for your project involves considering several factors, including the desired mechanical properties, environmental resistance, processing methods, and cost constraints. It’s essential to evaluate the specific requirements of the application, such as strength, flexibility, heat resistance, and chemical exposure. For projects requiring high strength and durability, isophthalic or DCPD resins might be more appropriate. In contrast, orthophthalic resins may suffice for less demanding applications. Additionally, consider the processing technique, as some resins are better suited for hand lay-up, while others are optimized for infusion or injection molding. Consulting with resin suppliers and reviewing technical datasheets can provide valuable insights, helping you select the most suitable polyester resin for your project’s unique needs.
What are the benefits of using polyester resins in composites?
The benefits of using polyester resins in composites include their exceptional strength-to-weight ratio, ease of processing, and cost-effectiveness. These resins enable the production of lightweight composite structures that are robust and durable, offering significant advantages over traditional materials in terms of performance and efficiency. Polyester resins also provide excellent chemical resistance and can be easily tailored with additives to meet specific performance requirements, such as enhanced UV stability or fire resistance. Their versatility across a wide range of manufacturing techniques makes them ideal for diverse applications, from automotive and marine to construction and consumer products, driving innovation in composite design and fabrication.
Can polyester resins be used with both glass and carbon fiber reinforcements?
Yes, polyester resins can be used with both glass and carbon fiber reinforcements, offering manufacturers flexibility in designing composite materials that meet specific strength, stiffness, and weight requirements. While glass fibers are more commonly paired with polyester resins due to their cost-effectiveness and adequate strength for many applications, carbon fibers can also be used to achieve higher strength and stiffness in critical performance applications. The choice between glass and carbon fibers depends on the project’s specific needs, balancing factors such as mechanical properties, weight considerations, and budget constraints.
What are the curing characteristics of polyester resins?
The curing characteristics of polyester resins are influenced by factors such as catalyst concentration, temperature, and the presence of accelerators or inhibitors. Typically, these resins cure at room temperature, undergoing an exothermic reaction when mixed with a catalyst, usually MEKP (Methyl Ethyl Ketone Peroxide). The curing process transforms the liquid resin into a solid, thermoset polymer, providing the composite material with its structural integrity. The rate of cure and final properties of the cured resin can be adjusted by altering the catalyst concentration, adding accelerators to speed up the reaction, or using inhibitors to extend the gel time, allowing for greater control over the manufacturing process.
How do polyester resins compare to epoxy resins in terms of performance?
Polyester resins and epoxy resins each have unique advantages and limitations, making them suitable for different applications. Polyester resins are valued for their versatility, ease of use, and cost-effectiveness, making them a popular choice for a wide range of composite applications. However, they generally offer lower strength, stiffness, and chemical resistance compared to epoxy resins. Epoxy resins, on the other hand, provide superior mechanical properties, adhesion, and environmental resistance, but at a higher cost and with more complex processing requirements. The choice between polyester and epoxy resins depends on the specific requirements of the application, balancing factors such as performance needs, processing capabilities, and budget constraints.
Can polyester resins be used in outdoor applications?
Yes, polyester resins can be used in outdoor applications, thanks to their good mechanical properties and the ability to be formulated with UV stabilizers and inhibitors that enhance their resistance to weathering and sunlight exposure. However, for long-term durability in harsh outdoor environments, it’s important to select the right type of polyester resin, such as an isophthalic or a specially formulated weather-resistant grade, which offers improved UV stability and resistance to water absorption. Proper surface treatment and the use of protective coatings can further extend the life of polyester-based composite structures in outdoor applications.
What safety precautions should be taken when working with polyester resins?
Working with polyester resins requires adherence to safety precautions to avoid health risks and ensure a safe working environment. Always work in a well-ventilated area and wear appropriate personal protective equipment (PPE), including gloves, safety glasses, and a respirator to protect against fumes and styrene exposure. Avoid skin contact with the resin and hardener, and clean any spills immediately using recommended cleaning agents. It’s also important to read and follow the manufacturer’s safety data sheets (SDS) for the specific resin you are using, which provide detailed information on handling, storage, and emergency measures. Proper training and awareness of the potential hazards can significantly reduce the risks associated with polyester resin use.