Honeycomb Plate
PP honeycomb, or polypropylene honeycomb, stands as a marvel in the field of composite materials, offering a lightweight yet exceptionally strong core solution for a myriad of applications. This innovative material features a unique honeycomb structure made from polypropylene, a thermoplastic polymer known for its versatility and durability. PP honeycomb is celebrated for its ability to provide remarkable strength and rigidity to composite structures while maintaining a minimal weight. This makes it an ideal choice for industries looking to enhance performance without compromising on weight efficiency, such as aerospace, automotive, marine, and construction.
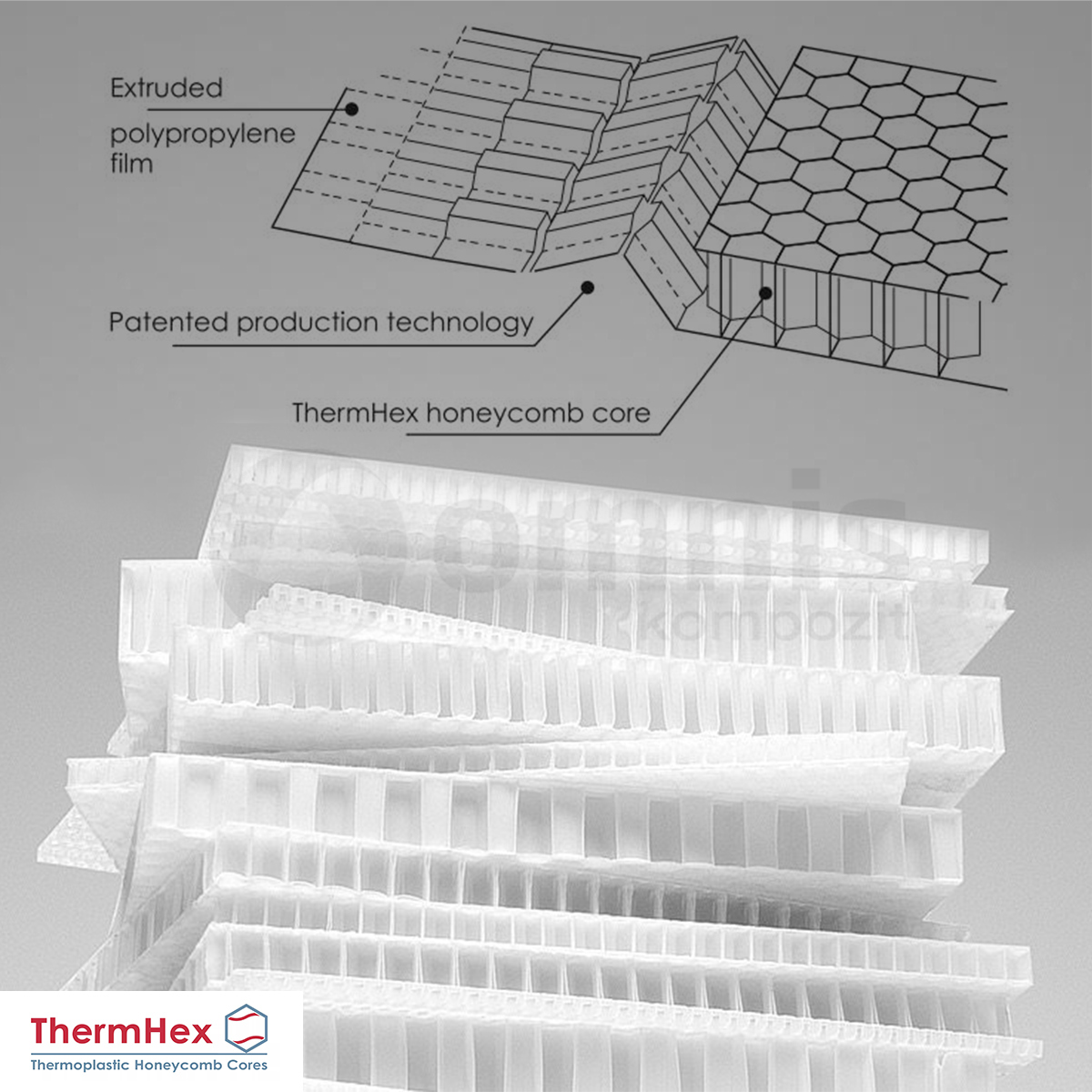
PP Honeycomb-Honeycomb Plate
ReviewHow is PP honeycomb manufactured?
PP honeycomb is manufactured using a sophisticated process that often involves extrusion and thermoforming techniques. One of the most advanced methods employed is the ThermHex process, which produces PP honeycomb cores with uniform cell structures and consistent density. This process begins with the extrusion of a polypropylene film, which is then thermoformed into a honeycomb structure and bonded under heat and pressure to create a robust and resilient core material. This manufacturing technique ensures a high-performance product with excellent mechanical properties, suitable for a wide range of applications.
What are the main advantages of using PP honeycomb in composite structures?
The use of PP honeycomb in composite structures brings a host of advantages, primarily due to its impressive strength-to-weight ratio. This material significantly enhances the mechanical performance of composites, providing superior stiffness and impact resistance while adding minimal weight. PP honeycomb is also known for its excellent corrosion resistance, chemical stability, and water resistance, making it an ideal core material for environments exposed to harsh conditions. Additionally, its energy absorption capabilities make it beneficial for applications requiring enhanced safety features, such as in the automotive and marine industries.
What is ThermHex technology in the context of PP honeycomb?
ThermHex technology represents a groundbreaking approach to manufacturing PP honeycomb, offering a cost-effective and efficient method for producing high-quality core materials. This innovative process involves a continuous production line that converts polypropylene into a honeycomb structure with outstanding uniformity and mechanical properties. The ThermHex technology allows for the production of PP honeycomb cores with smaller cell sizes and higher density, resulting in improved strength and stiffness for composite materials. This technology not only enhances the performance characteristics of PP honeycomb but also reduces production costs and environmental impact.
How does PP honeycomb compare to other core materials like foam or balsa?
PP honeycomb stands out from other core materials like foam and balsa due to its exceptional strength-to-weight ratio and durability. Unlike foam, PP honeycomb provides superior rigidity and shear strength, making it better suited for applications requiring high mechanical performance. Compared to balsa, PP honeycomb offers better moisture resistance and dimensional stability, ensuring long-term performance without the risk of rot or degradation. These qualities make PP honeycomb a more versatile and reliable choice for composite structures, particularly in demanding environments.
In what applications is PP honeycomb most commonly used?
PP honeycomb is most commonly used in applications where lightweight and high-strength materials are crucial for performance and efficiency. This includes industries such as aerospace, for interior cabin components; automotive, for body panels and chassis components; marine, for hulls and decks; and construction, for architectural panels and partitions. Its excellent mechanical properties and resistance to environmental factors also make it suitable for use in transportation, wind energy, and sporting goods, among other sectors seeking innovative solutions to enhance durability and reduce weight.
Can PP honeycomb be used in high-temperature environments?
PP honeycomb, while boasting a range of advantageous properties, has limitations regarding high-temperature environments due to the inherent thermal properties of polypropylene. It can maintain its structural integrity and performance characteristics up to a certain temperature threshold, typically around 80-100°C (176-212°F). Beyond this, PP honeycomb may begin to soften and lose mechanical strength. For applications involving higher temperatures, alternative materials or PP honeycomb variants with heat stabilizers might be considered to ensure the composite structure retains its properties under the specific operating conditions.
How does PP honeycomb contribute to the strength and stiffness of composites?
PP honeycomb contributes significantly to the strength and stiffness of composite materials through its unique cellular structure, which efficiently distributes loads and stresses across the entire panel. This honeycomb geometry provides exceptional resistance to bending and compression forces, allowing the composite to withstand high levels of mechanical stress without deformation. Additionally, the bond between the PP honeycomb core and the skins of the composite panel creates a sandwich structure that maximizes stiffness and strength while keeping weight to a minimum, enhancing the performance of the final product.
How do you cut and shape PP honeycomb for specific applications?
Cutting and shaping PP honeycomb for specific applications can be achieved through a variety of methods, depending on the accuracy and complexity required. Common techniques include using a fine-toothed saw for manual cuts, waterjet cutting for precise and intricate shapes, and laser cutting for high precision and smooth edges. When cutting PP honeycomb, it’s important to support the material adequately to prevent crushing or deformation of the cells. For shaping and forming, gentle heat may be applied to soften the polypropylene, allowing it to be molded into the desired form while maintaining the integrity of the honeycomb structure.
What types of resins and adhesives are compatible with PP honeycomb?
PP honeycomb is compatible with a wide range of resins and adhesives, including epoxy, polyester, and vinyl ester resins, which are commonly used in composite manufacturing. The choice of resin or adhesive depends on the application requirements, including mechanical properties, environmental exposure, and processing conditions. It’s essential to select materials that provide strong adhesion to the PP honeycomb and the skin materials to ensure the composite structure’s integrity and performance. Compatibility testing is recommended to confirm the bond strength and durability of the chosen resin or adhesive with PP honeycomb.
How does the thickness of PP honeycomb affect its performance characteristics?
The thickness of PP honeycomb directly impacts its performance characteristics, influencing stiffness, strength, and impact resistance of the composite structure. As the thickness increases, the panel’s ability to resist bending and compression improves, enhancing its overall mechanical performance. However, it’s crucial to balance the thickness with the weight requirements of the application, as thicker honeycomb cores will naturally increase the weight of the composite. Selecting the optimal thickness involves considering the specific demands of the application, including load-bearing requirements, environmental conditions, and weight constraints, to achieve the best combination of performance and efficiency.