GRC Machines
A GRC machine is specialized equipment designed for the production of Glassfiber Reinforced Concrete (GRC) products. GRC combines fine concrete with glass fiber reinforcements, resulting in a material that is lightweight, durable, and versatile. These machines automate the process of mixing, spraying, or extruding this composite material into various shapes and sizes, enabling the efficient manufacture of architectural elements, cladding panels, and decorative features. These machines are essential for producing high-quality GRC components that meet industry standards for strength, durability, and aesthetic appeal.
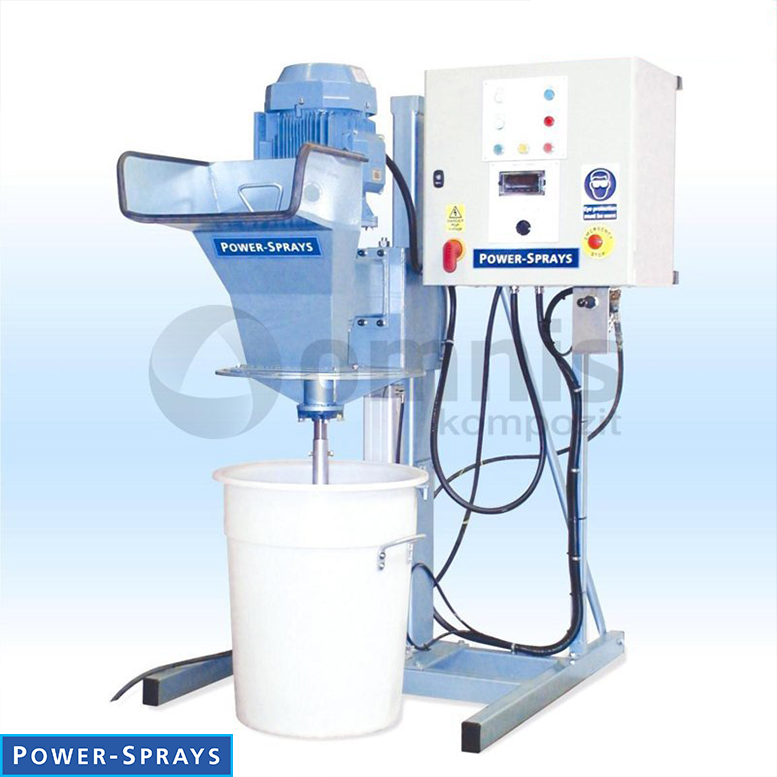
Power Sprays GRC 125
Review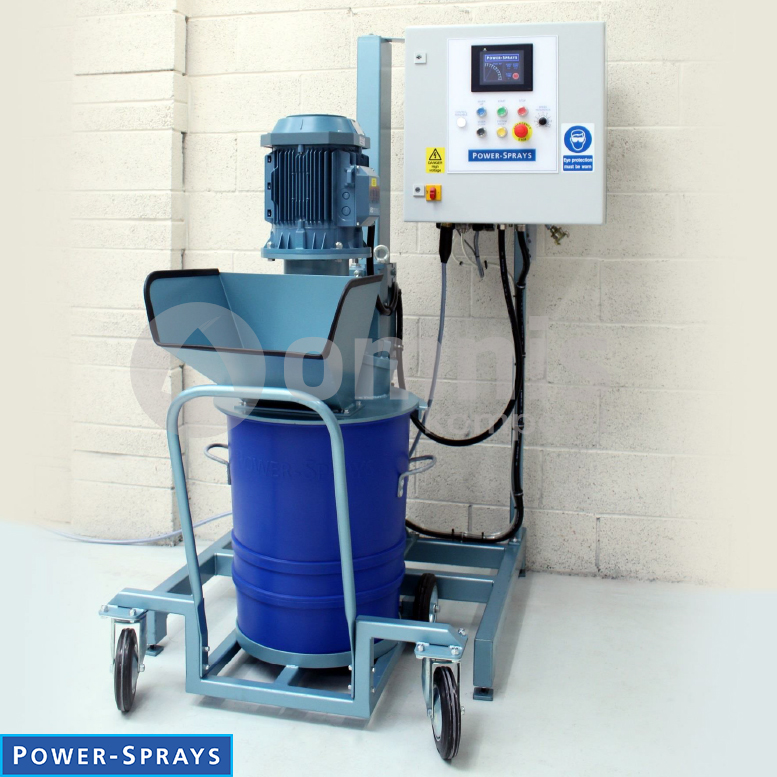
Power Sprays GRC 125 BT
Review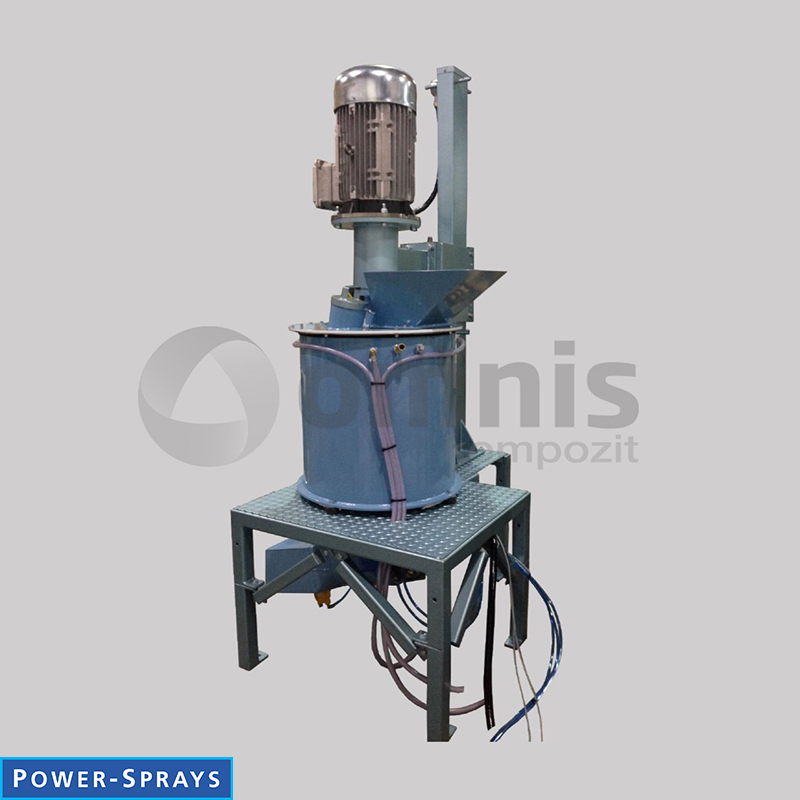
GRC250S Combination Mixer
Review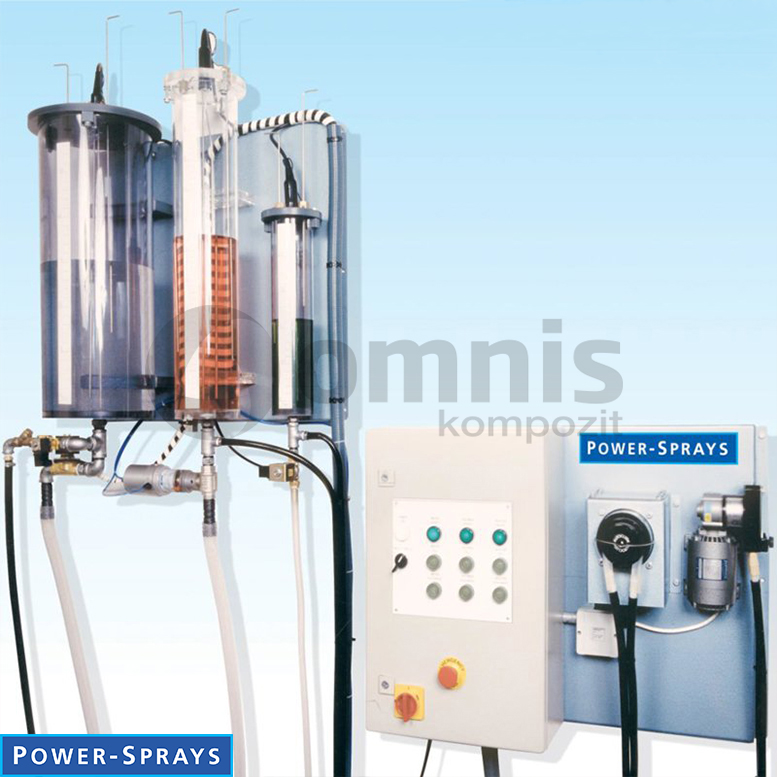
Power Sprays 3 Liquid Material Dosing Systems
Review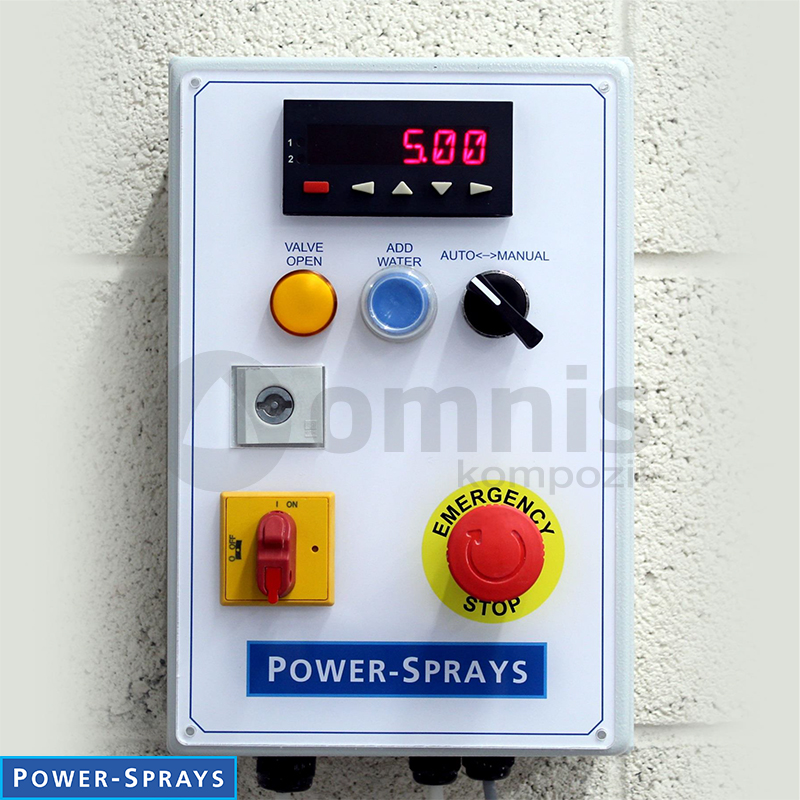
Digital Water Meter
Review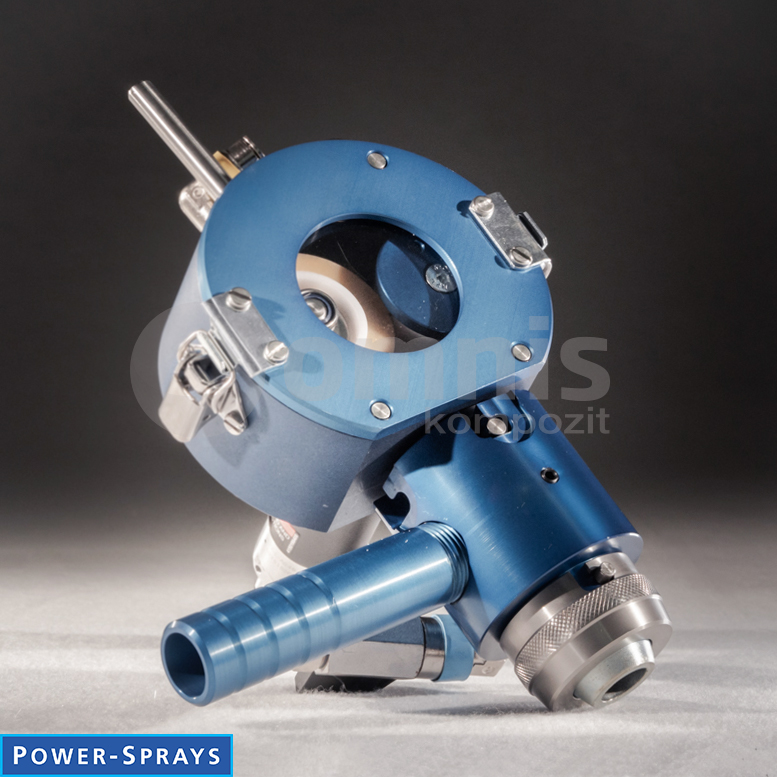
Power Sprays Spray Guns
Review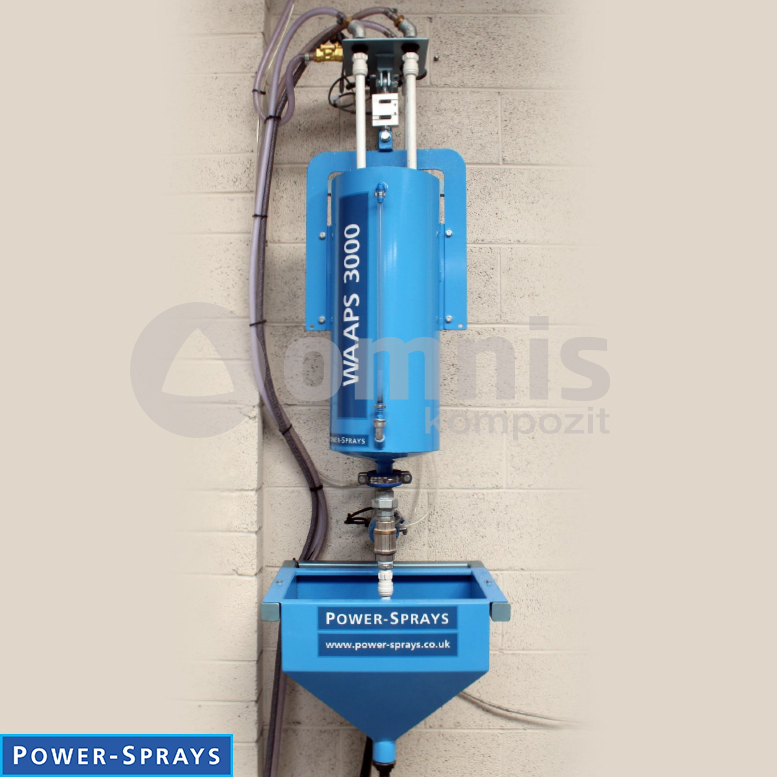
WAAPS 3000 Liquid Material Dosing Systems
Review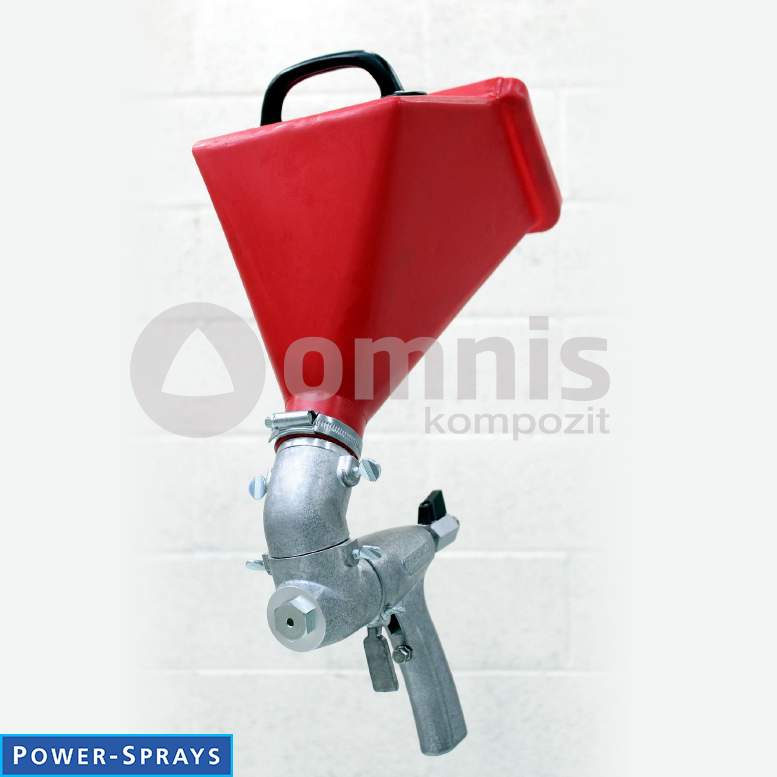
Power Sprays MK3
Review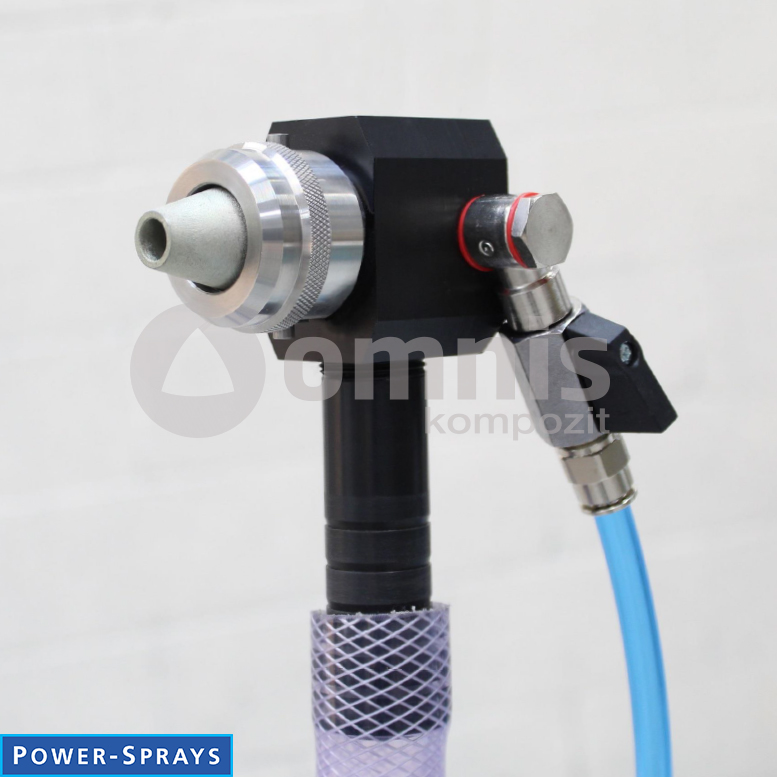
Power Sprays Light Mist Gun
Review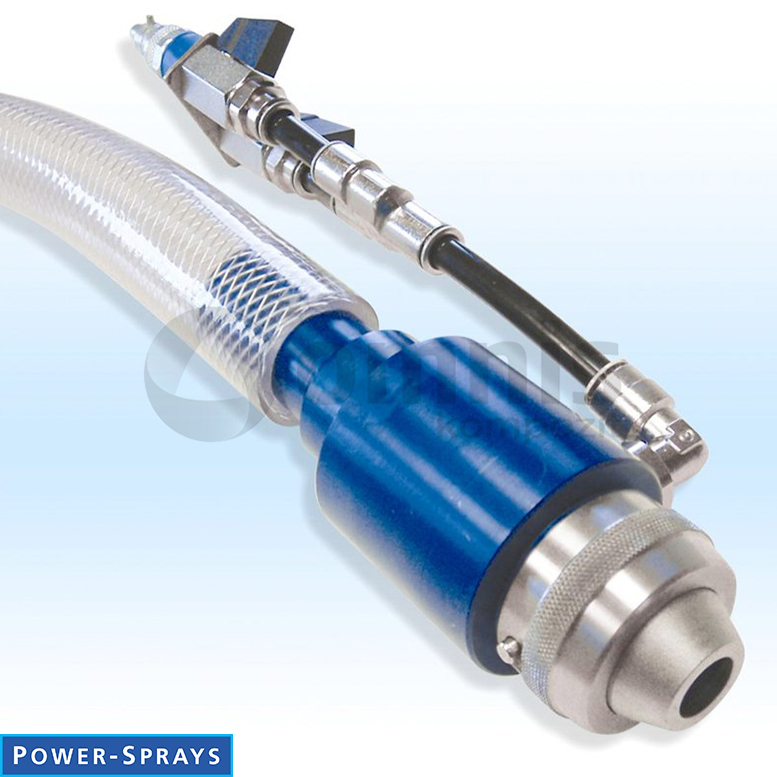
Power Sprays MK5A
Review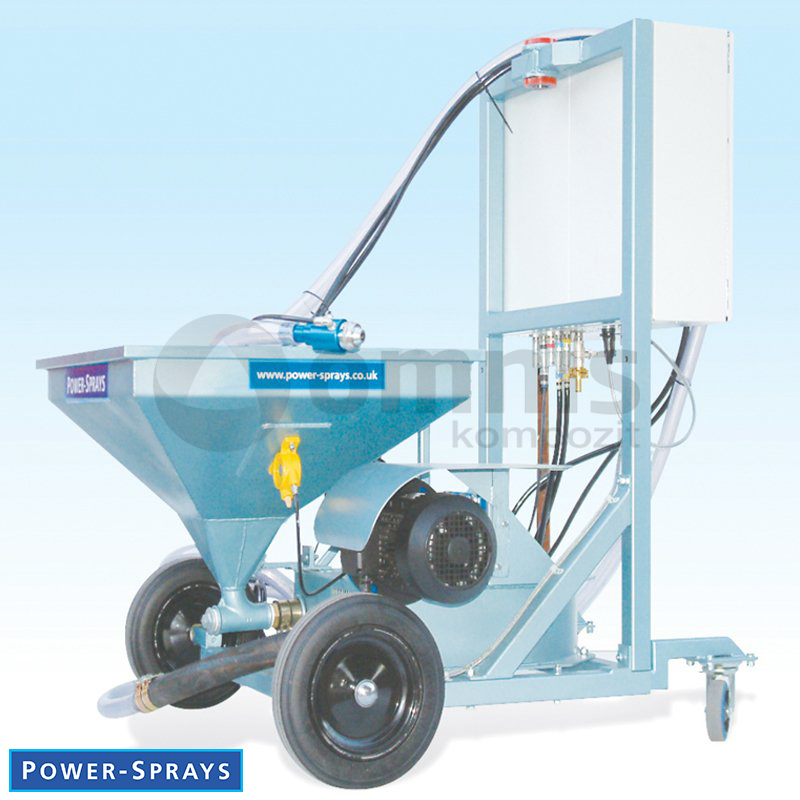
Power Sprays PS 38B
Review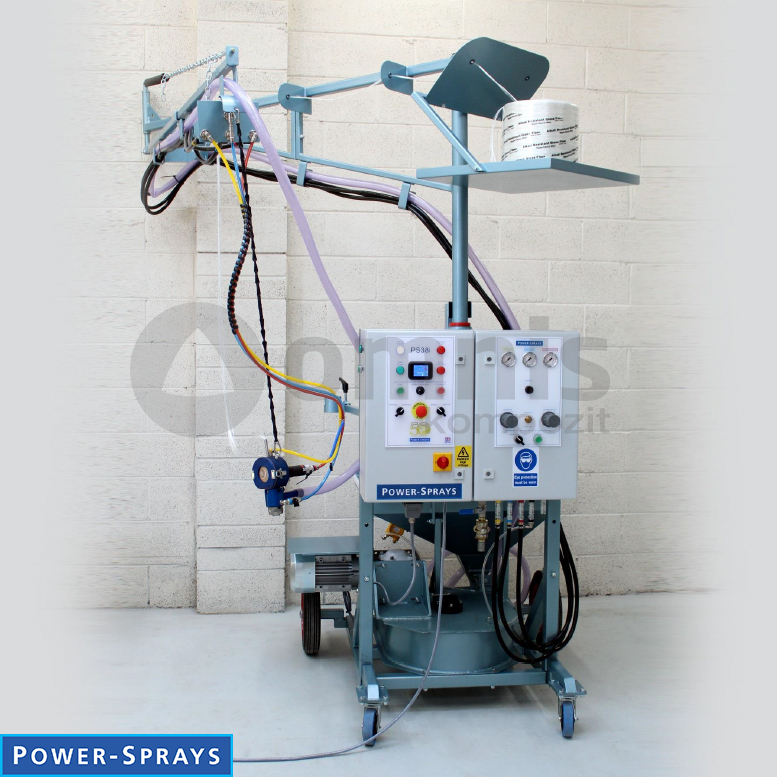
Power Sprays PS 38i
Review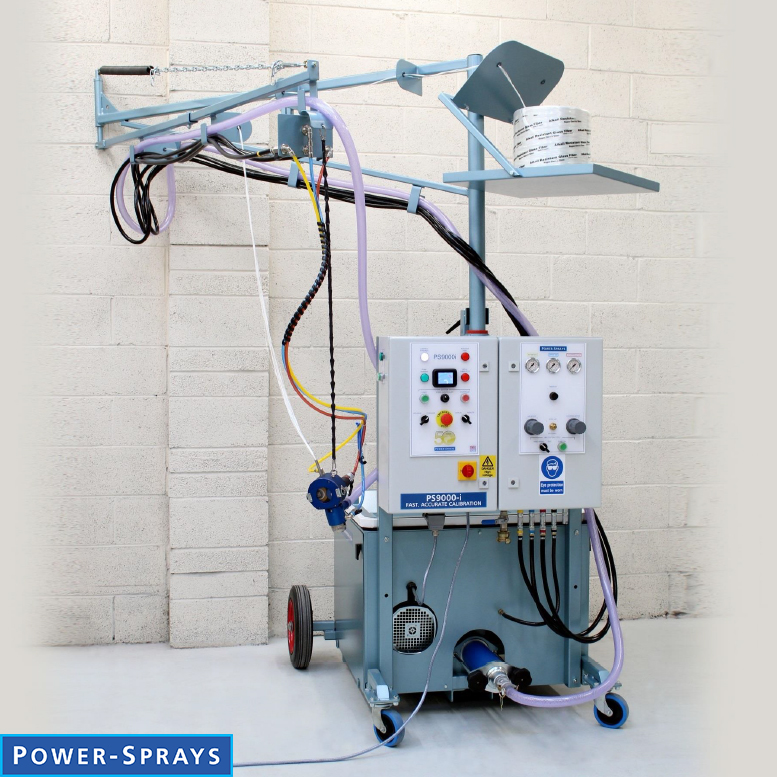
Power Sprays PS 9000i
Review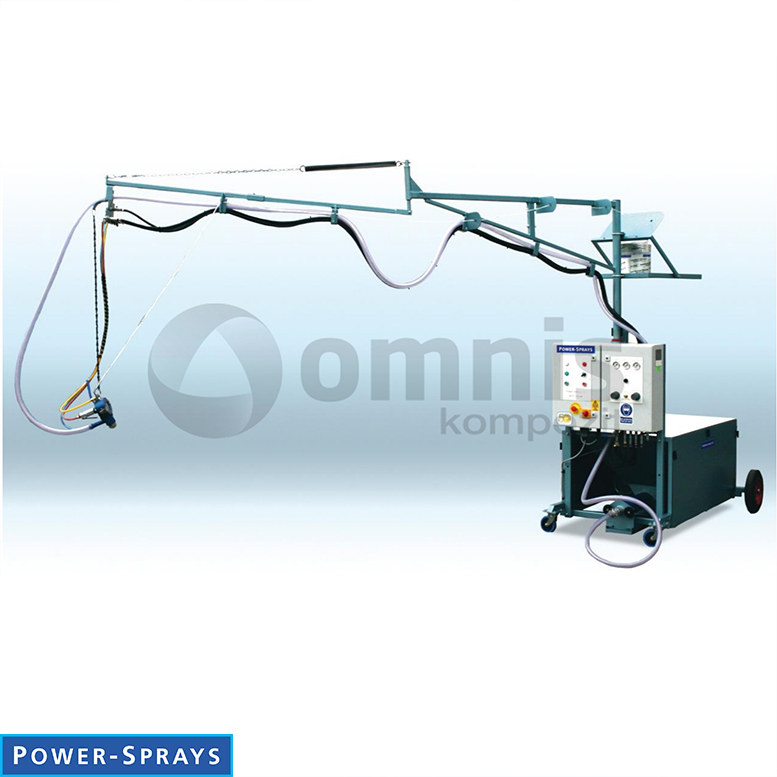
Power Sprays PS 10000i
ReviewHow does a GRC machine work?
A GRC machine works by precisely mixing cement, water, sand, and alkali-resistant glass fibers to create the GRC mixture. Depending on the type, the mixture can then be sprayed onto molds or extruded through dies to form the desired shapes. Spray machines use a high-velocity air stream to chop the glass fibers and mix them with the cementitious slurry before projecting the mixture onto a mold. Extrusion machines, on the other hand, push the mixed material through a die to create continuous profiles. The GRC components are then cured, either naturally or in a controlled environment, to achieve the required strength and durability.
What are the main types of GRC machines available?
The main types of GRC machines available include spray machines and premix machines. Spray machines are designed for the spray-up process, where the fiber and slurry are mixed and sprayed onto a mold simultaneously. This type is preferred for complex shapes and large surface areas. Premix machines, or extruders, blend the fibers and matrix beforehand, and the mixture is then shaped through extrusion or molding processes. Each type caters to different production needs and product specifications, allowing for a wide range of GRC applications.
How do I choose the right GRC machine for my project?
Choosing the right machine for your project involves considering several factors, including the scale of production, the complexity of the products being manufactured, and the specific properties required of the GRC components. Evaluate whether spray or premix technology better suits your needs based on the desired finish, detail, and production volume. Also, consider the machine’s versatility, ease of operation, and maintenance requirements. Consulting with manufacturers or suppliers can provide valuable insights and help you select a machine that meets your project’s specific requirements.
Can GRC machines be used for both small and large-scale production?
Yes, GRC machines can be used for both small and large-scale production. Smaller, more versatile machines are suitable for custom products and low-volume manufacturing, offering flexibility for producing a variety of designs. Larger, automated machines are designed for high-volume production, efficiently producing standardized GRC components with consistent quality. The scalability of GRC technology allows manufacturers to select equipment that matches their production capacity and to adjust their operations as demand changes.
What are the benefits of using a GRC machine in the manufacturing process?
The benefits of using a machine in the manufacturing process include increased efficiency, consistent product quality, and the ability to produce complex shapes and designs. GRC machines automate the mixing and application of the GRC material, reducing labor costs and minimizing errors. The precise control over the material composition and application ensures uniform quality across all products. Additionally, the versatility of machines enables the production of intricate designs that would be difficult or impossible to achieve with traditional concrete manufacturing methods.
How do GRC machines compare to traditional concrete manufacturing equipment?
GRC machines differ from traditional concrete manufacturing equipment in their ability to handle fiber-reinforced materials and produce lighter, stronger components. Traditional concrete equipment is designed for mass-producing standard concrete products without reinforcement or with steel reinforcement. In contrast, these machines are specifically engineered to mix glass fibers with concrete, allowing for the production of thin, lightweight panels with high tensile strength. This capability enables more innovative architectural designs and efficient use of materials.
What materials can be processed with a GRC machine?
A GRC machine can process a mixture of cement, water, fine aggregate (such as sand), alkali-resistant glass fibers, and admixtures designed to enhance the properties of the final GRC product. The specific formulation can be adjusted to meet the requirements of different applications, including variations in strength, durability, and appearance. The versatility of machines in processing these materials allows for a wide range of products to be manufactured, from architectural cladding and decorative elements to functional and structural components.
How does the use of a GRC machine affect the quality of GRC products?
The use of a GRC machine significantly affects the quality of GRC products by ensuring consistent mixing, accurate fiber distribution, and precise application of the GRC material. This leads to uniform mechanical properties, such as strength and durability, across all manufactured components. The controlled manufacturing process minimizes defects and variations, resulting in high-quality GRC products that meet specified performance criteria. Additionally, the ability to produce complex shapes and fine details enhances the aesthetic quality of GRC components.
Can GRC machines be customized for specific production needs?
Yes, GRC machines can be customized for specific production needs. Manufacturers often offer options for customization, including adjustable controls for material flow rates, interchangeable molds or dies for different product shapes, and integrated curing systems. Customization allows manufacturers to optimize their GRC production processes for efficiency, product quality, and versatility. Working closely with machine suppliers can ensure that the equipment is tailored to meet the unique requirements of your manufacturing operation.
What maintenance is required to keep a GRC machine in good working condition?
To keep a GRC machine in good working condition, regular maintenance is required, including cleaning to prevent material buildup, lubrication of moving parts, and inspection for wear and damage. Scheduled maintenance should follow the manufacturer’s recommendations, focusing on critical components such as pumps, mixers, and spray nozzles. Preventive maintenance helps avoid unexpected downtime, ensures consistent product quality, and extends the lifespan of the machine. Proper training for operators on maintenance procedures can also contribute to the efficient and safe operation of GRC equipment.
How energy-efficient are GRC machines?
The energy efficiency of GRC machines varies depending on their design, technology, and operational settings. Modern machines are increasingly designed with energy efficiency in mind, incorporating features such as variable speed drives, energy-saving motors, and automated control systems that minimize energy consumption. Manufacturers are focusing on reducing the environmental impact of GRC production by optimizing machine operations and materials processing. Selecting energy-efficient machines can contribute to lower operational costs and a reduced carbon footprint for manufacturers.