Accelerator
An accelerator in composite manufacturing is a chemical additive used to speed up the curing process of resins, facilitating a quicker transformation from liquid to solid state. Accelerators are essential for enhancing the efficiency of composite production, allowing for faster mold turnovers and improved productivity. They work by increasing the rate of the chemical reaction between the resin and the hardener or catalyst, without compromising the quality and integrity of the final composite product. The use of accelerators is critical in applications where time and performance are of the essence, making them invaluable in the manufacturing of high-quality composite materials.
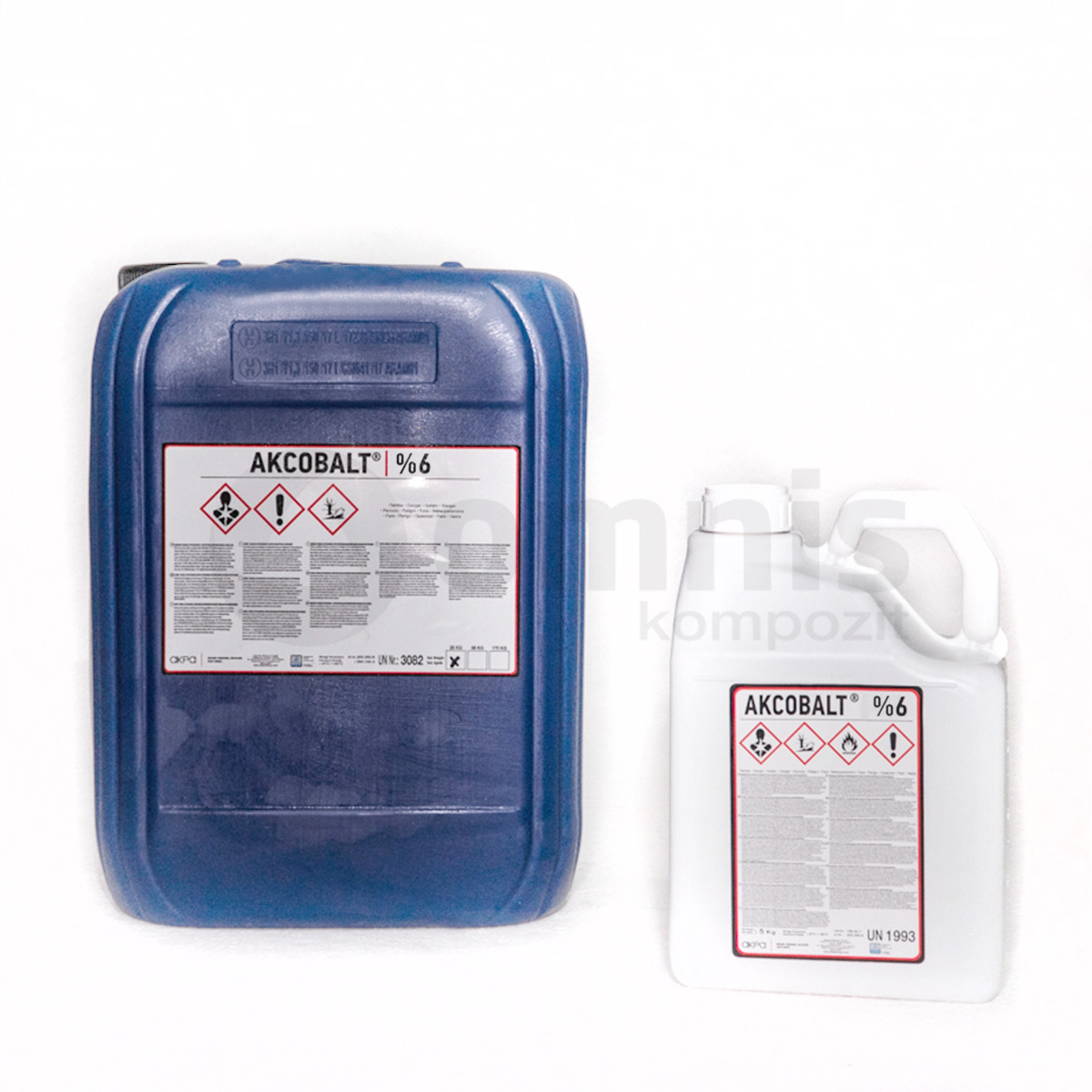
Accelerators
ReviewWhat is a cobalt accelerator, and how does it work?
A cobalt accelerator is a specific type of accelerator used predominantly with unsaturated polyester resins in composite manufacturing. It acts by enhancing the reactivity between the polyester resin and the peroxide catalyst, significantly speeding up the curing process. They are typically cobalt salts, with cobalt octoate being a common form. These accelerators work by facilitating the decomposition of the peroxide into free radicals, which then initiate the polymerization of the resin. This mechanism ensures a faster and more efficient cure, making cobalt accelerators a key component in the production of polyester-based composites.
How do accelerators affect the curing process of composites?
Accelerators, including cobalt accelerators, play a pivotal role in the curing process of composites by reducing the time required for the resin to harden and reach its optimal strength and thermal properties. By speeding up the chemical reactions involved in curing, accelerators enable composite manufacturers to achieve quicker cycle times and increased throughput. This efficiency does not come at the expense of the composite’s quality; properly formulated, the use of accelerators can lead to materials with excellent mechanical and physical properties, suitable for a wide range of applications.
Can they be used with all types of polyester resins?
They are compatible with a broad spectrum of unsaturated polyester resins, widely used in composite manufacturing for their versatility and superior mechanical properties. They are particularly effective in enhancing the curing of these resins under various conditions. However, it’s important to select the appropriate type and concentration of cobalt accelerator based on the specific resin formulation and the desired cure characteristics. Consulting with resin and accelerator suppliers can provide valuable guidance in matching the accelerator to the resin system for optimal performance.
What are the main advantages of using cobalt accelerators?
The main advantages of using cobalt accelerators in composite manufacturing include improved processing speed, enhanced control over the curing process, and the ability to cure at lower temperatures. These benefits lead to increased productivity, energy savings, and potentially lower manufacturing costs. Additionally, they can contribute to the production of composites with consistent and reliable mechanical properties, as they promote a more uniform cure throughout the material. Their effectiveness in accelerating the cure of unsaturated polyester resins makes them indispensable in the efficient production of high-quality composite parts.
How do you determine the correct amount of cobalt accelerator to use?
Determining the correct amount of cobalt accelerator to use requires careful consideration of the resin system, the desired cure speed, and the processing conditions. Manufacturers typically start with recommendations provided by the accelerator supplier, which are then fine-tuned through trial and error. The amount of accelerator can vary depending on factors such as the type of resin, the presence of other additives, and the ambient temperature. Conducting small-scale tests to observe the cure characteristics and adjusting the accelerator concentration accordingly is a common practice to achieve the desired balance between cure speed and material properties.
Can they be used in conjunction with other curing agents?
Yes, they are often used in conjunction with other curing agents, such as peroxides, to initiate and control the curing process of unsaturated polyester resins. The accelerator optimizes the activity of the curing agent, allowing for a faster and more efficient cure. It’s important to carefully balance the concentrations of the accelerator and the curing agent to achieve the desired cure speed and properties of the composite material. Compatibility and proportioning guidelines provided by the manufacturers of both the accelerators and curing agents should be followed to ensure optimal results.
What safety precautions should be taken when handling cobalt accelerators?
When handling accelerators, it’s important to adhere to strict safety precautions due to their potentially hazardous nature. Personal protective equipment (PPE), such as gloves, safety goggles, and protective clothing, should be worn to avoid skin and eye contact. Working in a well-ventilated area or using appropriate exhaust systems can prevent inhalation of fumes or dust. Additionally, following the manufacturer’s safety data sheets (SDS) for proper handling, storage, and disposal instructions is crucial for maintaining a safe working environment. Safety training and awareness of the specific risks associated with accelerators are essential for all personnel involved in their handling.
How do environmental conditions affect the performance of cobalt accelerators?
Environmental conditions, such as temperature and humidity, significantly impact the performance of cobalt accelerators in the curing process of composites. Cobalt accelerators are temperature-sensitive; their reactivity increases with temperature. Thus, higher ambient temperatures can lead to faster curing times, whereas lower temperatures may slow down the reaction, necessitating adjustments in accelerator concentration. Humidity can also influence the curing process, although its effect is more indirect, possibly affecting the conditions of storage and application rather than the chemical activity of the cobalt accelerator itself. Manufacturers need to consider these environmental factors when using cobalt accelerators to ensure consistent and optimal curing of composites.
Are there different types of cobalt accelerators for specific applications?
Yes, there are different types of cobalt accelerators available, tailored for specific applications and resin systems. These variations often involve differences in cobalt concentration, the type of solvent used, or the specific cobalt salt employed. Some accelerators are formulated for faster curing times or for use at lower temperatures, while others are designed to provide a more extended working time or enhanced compatibility with specific resin formulations. Selecting the right type of accelerator is crucial for achieving the desired cure characteristics and performance in the final composite material, making it important for manufacturers to consult with suppliers to identify the most suitable accelerator for their particular application.
How do cobalt accelerators influence the final properties of the composite material?
They play a crucial role in influencing the final properties of the composite material by regulating the curing process of unsaturated polyester resins. By ensuring a more efficient and controlled cure, accelerators contribute to achieving optimal cross-link density in the polymer matrix, which in turn affects the material’s mechanical strength, thermal stability, and chemical resistance. Proper use of cobalt accelerators can result in composites with improved performance characteristics, including higher tensile strength, better impact resistance, and enhanced durability. The selection and concentration of the cobalt accelerator must be carefully optimized to match the specific requirements of the application, ensuring the composite material meets or exceeds the expected performance criteria.
Can the use of cobalt accelerators reduce the overall curing time of composites?
Absolutely, the use of accelerators can significantly reduce the overall curing time of composites. By increasing the rate of the chemical reaction between the polyester resin and the peroxide catalyst, cobalt accelerators enable the resin to achieve a solid state more rapidly. This reduction in curing time allows for faster production cycles, increasing throughput and efficiency in manufacturing processes. However, it’s important to balance the accelerator concentration to avoid too rapid curing, which could lead to incomplete impregnation of the reinforcement material or the development of internal stresses. Proper formulation and testing are essential to harness the benefits of cobalt accelerators in shortening curing times without compromising the quality and integrity of the composite material.