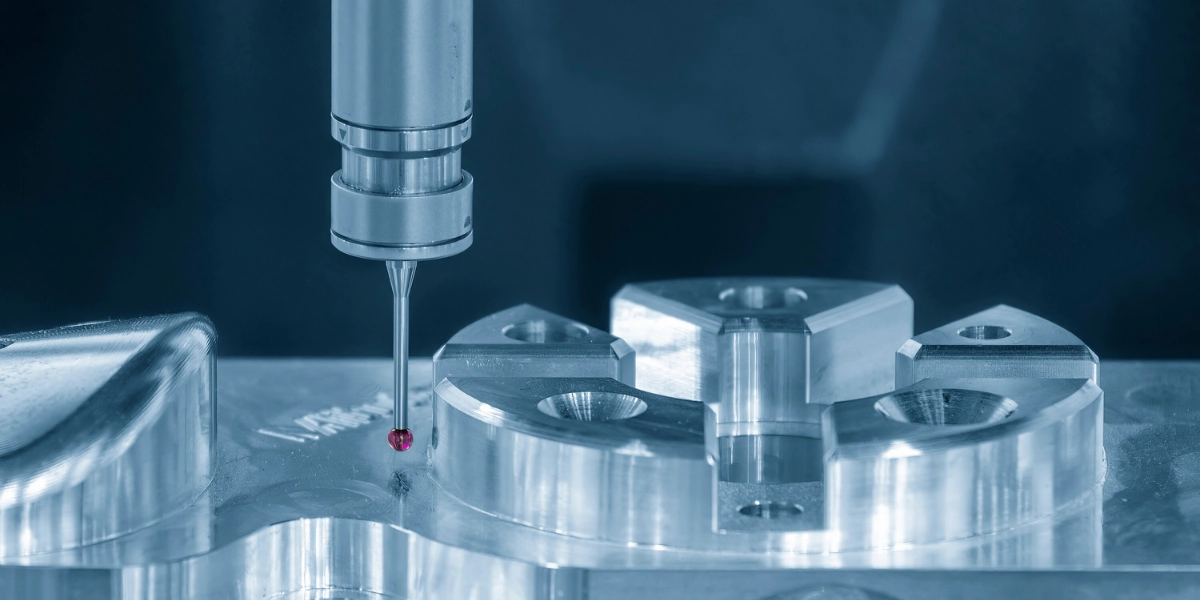
- Blog
- 11 Mar 2025
What is Compression Molding? A Deep Dive
Compression molding is a widely used manufacturing technique in the composite industry for producing strong, durable, and cost-effective parts. It involves shaping materials under heat and pressure, making it ideal for producing complex components with high strength and precision.
This article explores the basics of press molding, how it works, the materials involved, and its key benefits. Whether you’re a manufacturer, designer, or just curious about composite manufacturing processes, this guide will help you understand why compression molding plays a crucial role in modern production.
What is Compression Molding?
Compression molding is a manufacturing process where a material, often a polymer or composite, is placed into a heated mold cavity. The mold is then closed, and heat and pressure are applied to shape the material into a finished part.
This method is particularly effective for producing large, durable components with complex shapes, making it a popular choice in industries such as automotive, aerospace, and consumer goods manufacturing.
How Does Compression Molding Work?
The press molding process involves several key stages that ensure the material is shaped accurately and consistently.
1. Preparation of Raw Materials (Thermoset or Thermoplastic)
Before the molding process begins, the raw material must be prepared. Depending on the application, press molding can use thermoset or thermoplastic materials.
- Thermoset materials: These include epoxy resin, phenolic resins, and polyester resins. They harden permanently when heated, making them ideal for high-heat and structural applications.
- Thermoplastic materials: These materials, such as polypropylene and nylon, can be reshaped when reheated, offering more flexibility for certain products.
2. Placement of Material in the Mold Cavity
Once the raw material is prepared, it is carefully placed into the mold cavity. The material may be in the form of sheets, pellets, or pre-formed charges, depending on the specific application.
To ensure smooth part release after molding, mold release agents are often applied to the mold surface. These agents prevent the material from sticking to the mold, reducing damage and improving production efficiency.
3. Application of Heat and Pressure
The mold is closed, and heat and pressure are applied simultaneously.
- Heat: The mold is heated to a specific temperature based on the material type. For thermosets, this activates the curing process, while thermoplastics are melted into shape.
- Pressure: High pressure ensures the material flows evenly throughout the mold, filling every cavity and eliminating voids or air pockets.
This stage is crucial in press molding as it determines the strength, density, and quality of the final product.
4. Cooling and Removal of the Finished Part
Once the material has fully cured or cooled, the mold is opened, and the finished part is removed. Proper cooling ensures the part retains its shape and structural integrity.
After removal, the part may undergo additional finishing processes such as trimming, sanding, or coating, depending on the application.
Materials Used in Compression Molding
Compression molding can be used with a wide range of materials, making it a versatile choice for manufacturers. Some commonly used materials include:
- Epoxy Resin: Ideal for high-performance applications due to its strength, heat resistance, and chemical durability.
- Polyester Resins: Often used for automotive parts and construction materials due to their affordability and resistance to wear.
- Carbon Fiber and Glass Fiber Composites: Popular in aerospace and sports equipment for their lightweight yet strong properties.
- Thermoplastics: Such as polypropylene, nylon, and ABS for consumer goods and packaging.
The choice of material depends on the desired properties of the final product, such as heat resistance, flexibility, and mechanical strength.
Benefits of Compression Molding
Compression molding offers several advantages, making it a preferred method in various industries:
1. Cost-Effective for Large Production Runs
Compression molding is highly efficient for producing large quantities of parts, especially for medium to high production volumes. The use of reusable molds reduces long-term production costs.
2. High Strength and Durability
The application of heat and pressure ensures that parts produced through press molding are dense, strong, and capable of withstanding stress and impact. This makes it ideal for structural components.
3. Design Flexibility
Complex shapes and intricate designs can be achieved with press molding, including textured surfaces and precise details. This flexibility benefits industries like automotive and consumer electronics.
4. Material Versatility
From epoxy resin to polyester resins and fiber-reinforced composites, press molding supports a broad range of materials, allowing manufacturers to tailor products to specific needs.
5. Eco-Friendly Options
By using recyclable thermoplastics and efficient production techniques, press molding can contribute to more sustainable manufacturing practices.
6. Compatibility with Composite Manufacturing Processes
Compression molding can be seamlessly integrated with other composite manufacturing processes, such as injection molding and resin transfer molding. This compatibility allows manufacturers to produce hybrid components for specialized applications.
To sum up, press molding is a powerful and efficient manufacturing technique, widely used across industries for its ability to produce strong, durable, and cost-effective parts. From epoxy resin aerospace components to polyester resins used in automotive panels, the process supports a broad range of materials and applications.
By understanding the steps, materials, and benefits involved, manufacturers can make informed decisions about using press molding for their production needs. Its compatibility with other composite manufacturing processes and sustainability potential makes it a crucial tool for modern industries seeking efficiency and quality.
As technology advances, compression molding continues to evolve, offering even greater precision, eco-friendliness, and performance in the years to come.