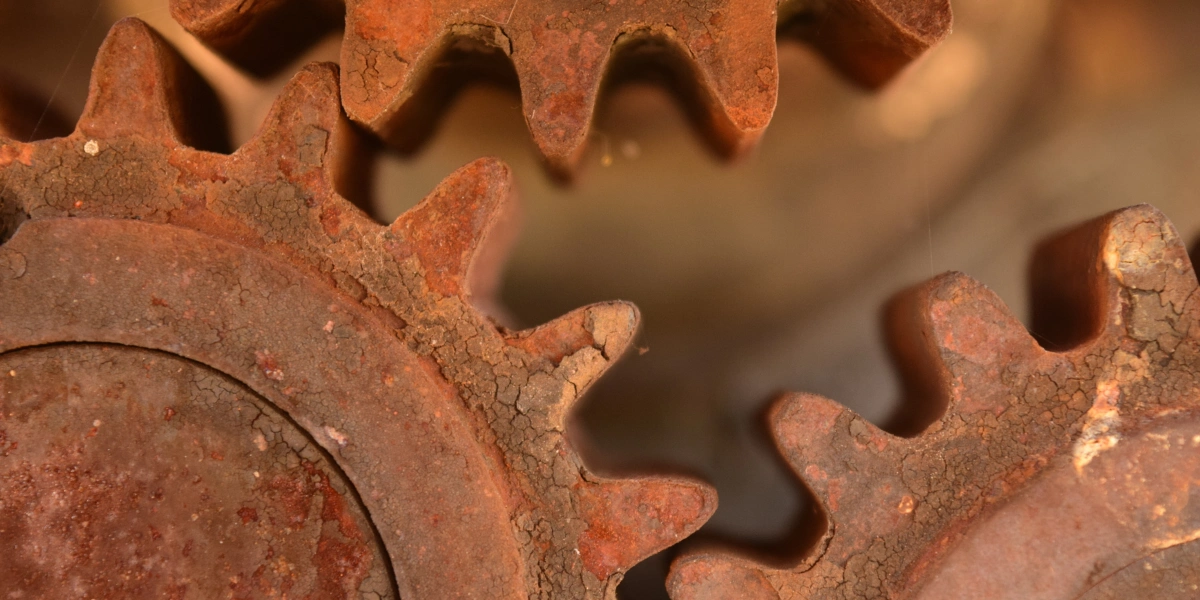
- Blog
- 24 Dec 2024
Understanding Galvanic Corrosion
Galvanic corrosion is a common but often overlooked problem that affects many different industries and applications. It occurs when two dissimilar metals come into contact with each other in the presence of an electrolyte, causing one metal to corrode more rapidly than it otherwise would. This type of corrosion can lead to serious structural damage, costly repairs, and even complete failure of metal components if not properly managed. Understanding the mechanisms behind corrosion, as well as how to prevent it, is crucial for maintaining the integrity and longevity of metal structures.
What is Galvanic Corrosion?
Galvanic corrosion is a type of electrochemical corrosion that occurs when two different metals come into electrical contact in the presence of an electrolyte, such as water. Essentially, it is the result of an electrochemical reaction that takes place between dissimilar metals, leading to the accelerated corrosion of one of the metals. This kind of corrosion can significantly reduce the lifespan of metal components and structures, making it a critical issue to understand and manage in various industries. Proper knowledge of corrosion can help prevent material failure and ensure long-term durability.
How Does Galvanic Corrosion Occur?
Galvanic corrosion occurs when two metals with different electrochemical potentials are placed in an electrolyte. In this scenario, the more reactive metal becomes the anode, while the less reactive metal acts as the cathode. The anode metal corrodes at an accelerated rate, while the cathode remains relatively protected. The electrolyte, often in the form of moisture or saltwater, facilitates this electrochemical process. For example, when aluminum and copper are used together without proper insulation, corrosion may set in, leading to severe damage over time. Understanding how corrosion occurs helps us adopt effective preventative measures.
Common Galvanic Corrosion Examples
There are numerous common examples of corrosion that can be observed in everyday life and industrial environments. One of the most common examples is in marine settings, where dissimilar metals are frequently in contact with saltwater, which acts as an electrolyte. Galvanic corrosion in marine environments is especially concerning because saltwater significantly accelerates the corrosion process. Another example is in automotive and aerospace industries, where mixed metals are used for structural and performance reasons. Even in household plumbing, the combination of copper pipes with steel fixtures can cause corrosion if precautions are not taken.
Galvanic Corrosion in Marine Environments
In marine environments, Galvanic corrosion is a well-known challenge. Saltwater serves as an excellent electrolyte, making boats, ships, and other marine structures particularly susceptible to this type of corrosion. When different metals, such as stainless steel and aluminum, are used together in marine construction, the more reactive metal quickly deteriorates unless proper preventative measures are in place. This is why using compatible materials and applying protective coatings is essential for marine composite structures to avoid galvanic damage and extend their service life.
Corrosion in Automotive and Aerospace Industries
In the automotive and aerospace industries, corrosion can pose a serious risk to structural integrity. These industries often rely on different metals, like aluminum and steel, in order to achieve an optimal balance of strength and weight. However, if these metals are not adequately insulated from each other, corrosion can weaken essential components, which is a significant safety concern. For instance, in aerospace applications, epoxy resin is often used as an insulator between metals to reduce the risk of corrosion. This approach helps protect sensitive joints and extends the lifespan of critical aircraft components.
Effects on Household and Commercial Applications
Corrosion is also commonly found in household and commercial applications, such as plumbing systems. When copper and galvanized steel pipes are connected without a dielectric union, corrosion can rapidly occur, leading to leaks and costly repairs. Corrosion not only compromises the efficiency of household water systems but can also lead to health hazards due to metal leaching into water supplies. Similarly, in commercial buildings, using incompatible metals without appropriate separation techniques can result in significant maintenance costs and potential structural damage.
Preventing Galvanic Corrosion
Preventing corrosion requires careful planning and material selection. One of the most effective ways to prevent it is by choosing metals that are close to each other on the galvanic series, meaning they have similar electrochemical potentials. This minimizes the potential difference between the metals, reducing the likelihood of galvanic action. Additionally, using insulating materials, such as rubber gaskets or plastic spacers, between dissimilar metals can prevent direct contact and break the electrical circuit. Coating metals with protective layers, like paint or concrete chemicals, can also provide a barrier against the electrolyte and help reduce the risk of corrosion. Proper design and preventive measures are essential in ensuring the long-term performance of metallic structures.
The Impact of Galvanic Corrosion on Structural Integrity
Corrosion can have a profound impact on the structural integrity of metal components and assemblies. Over time, the anodic metal corrodes, leading to weakening, perforations, and eventual failure. This is especially concerning in critical infrastructure, such as bridges, buildings, and pipelines, where material failure can lead to catastrophic outcomes. The importance of preventing corrosion cannot be overstated, as it directly affects safety and reliability. In reinforced concrete structures, for example, corrosion can occur if dissimilar metal reinforcements are used without adequate protection, ultimately leading to compromised structural performance. The proper application of protective measures, such as using compatible materials or applying concrete chemicals, plays a crucial role in mitigating these risks.
In conclusion, understanding galvanic corrosion is essential for anyone working with metals, whether in large-scale industrial projects or simple household repairs. It occurs when dissimilar metals come into contact in the presence of an electrolyte, leading to accelerated deterioration of the more reactive metal. By carefully selecting materials, applying protective coatings, and ensuring proper insulation between different metals, corrosion can be effectively managed. This proactive approach not only extends the lifespan of metal components but also ensures safety, reliability, and reduced maintenance costs across various industries.