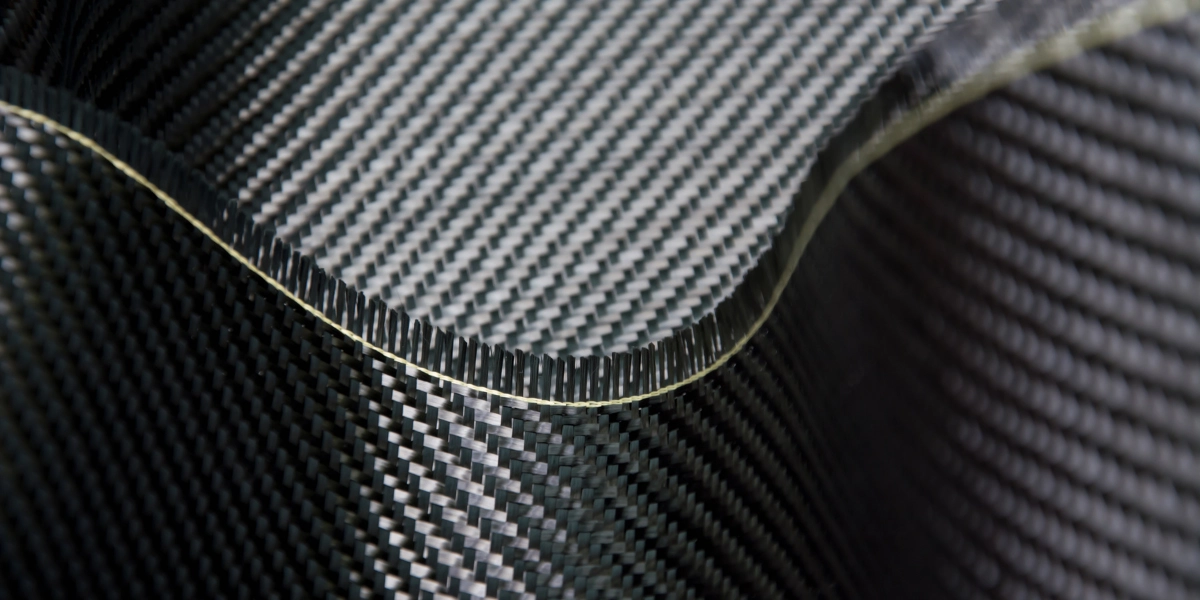
- Blog
- 3 Mar 2025
Thermoplastic Composites: Properties and Uses
Thermoplastic composites are revolutionizing modern material engineering, offering a unique blend of strength, flexibility, and sustainability. These advanced materials combine fiber reinforcements with a thermoplastic matrix, creating lightweight yet durable components for various industries. As demand for eco-friendly and high-performance materials grows, reinforced thermoplastics have become increasingly popular in sectors like automotive, aerospace, and construction. In this blog, we will explore the properties, benefits, and applications of thermoplastic composites, along with insights into their manufacturing processes and challenges.
What Are Thermoplastic Composites?
Thermoplastic composites are materials made by embedding reinforcing fibers such as carbon fiber or glass fiber within a thermoplastic polymer matrix. The polymer matrix can be melted and reshaped multiple times without degrading its structural properties, making these composites both durable and recyclable.
The fibers provide mechanical strength and stiffness, while the thermoplastic matrix offers flexibility, impact resistance, and heat tolerance. Common thermoplastic polymers used in these composites include polypropylene (PP), polyether ether ketone (PEEK), and polyamide (PA).
Difference Between Thermoplastic and Thermoset Composites
Thermoplastic and thermoset composites share similarities but have distinct differences that influence their applications and performance:
- Curing Process: Thermoplastics can be reheated and reshaped multiple times, while thermosets undergo a chemical curing process, making them rigid and non-reversible.
- Recyclability: Reinforced thermoplastics are recyclable due to their ability to be remelted, while thermosets are not.
- Durability: Thermoplastics offer better impact resistance and flexibility, whereas thermosets are often stronger in static load conditions.
- Manufacturing Speed: Reinforced thermoplastics generally allow faster production due to their ability to be molded and cooled quickly.
These differences make reinforced thermoplastics ideal for industries focused on sustainability and rapid production cycles.
Benefits of Thermoplastic Composites
Reinforced thermoplastics offer numerous advantages across industries, including:
- Lightweight and Strong: These materials provide excellent strength-to-weight ratios, making them suitable for applications where weight reduction is essential.
- Recyclability: Since the thermoplastic matrix can be remelted, parts can be repurposed or recycled, reducing waste.
Corrosion Resistance: Reinforced thermoplastics resist moisture and chemicals, making them ideal for harsh environments. - Fast Processing Times: The ability to melt and reshape the matrix allows for faster production, especially compared to thermoset materials.
- Design Flexibility: Thermoplastics can be molded into complex shapes and structures with precision.
These benefits make reinforced thermoplastics a preferred choice in industries seeking efficient and sustainable materials for high-performance applications.
Applications of Thermoplastic Composites
Thermoplastic composites are widely used across industries due to their versatility and performance.
Aerospace Industry
Reinforced thermoplastics are increasingly used in the aerospace sector for structural components such as seat frames, floor panels, and fuselage sections. Their lightweight nature helps reduce fuel consumption while maintaining structural integrity under extreme conditions.
Composites in Automotive
In the composites in automotive sector, reinforced thermoplastics play a vital role in manufacturing lightweight parts that improve fuel efficiency and performance. Components like bumpers, interior panels, and underbody shields benefit from the strength and impact resistance of thermoplastic materials. This weight reduction also supports the growing demand for electric vehicles by extending battery range.
Construction and Infrastructure
Reinforced thermoplastics are used in construction for bridge reinforcements, pipes, and panels due to their corrosion resistance and durability. Their ability to withstand harsh weather conditions makes them ideal for outdoor structures.
Reinforced thermoplastics are used in prosthetics, braces, and surgical tools due to their biocompatibility and strength. Their lightweight properties enhance patient comfort, while the material’s moldability allows for custom-fit designs.
Sports and Recreation
High-performance sports equipment, including helmets, tennis rackets, and bicycles, often use reinforced thermoplastics for their durability and impact resistance while keeping weight minimal for optimal athletic performance.
How Thermoplastic Composites Are Manufactured
The manufacturing of thermoplastic composites involves combining fiber reinforcements with a thermoplastic matrix through heat and pressure. This process ensures the fibers are well-integrated into the polymer for optimal strength and performance.
Key Manufacturing Techniques
- Injection Molding: A popular method where thermoplastic pellets mixed with fiber reinforcements are melted and injected into a mold under high pressure. Injection molding is widely used for producing complex, high-volume parts with consistent quality.
- Compression Molding: Fiber-reinforced thermoplastic sheets are placed in a mold, heated, and compressed to form a part. This technique is ideal for large, flat components.
- Automated Fiber Placement (AFP): A robotic process where fiber tapes impregnated with thermoplastic resin are precisely placed and melted onto a mold for high-strength components.
- Pultrusion: Continuous fibers are pulled through a thermoplastic resin bath and then heated to create long, reinforced profiles.
Role of Additives and Modifiers
Additives and modifiers play a key role in enhancing the performance of thermoplastic composites. These include:
- Impact Modifiers: Improve toughness and resistance to sudden forces.
- UV Stabilizers: Protect the composite from UV radiation degradation.
- Flame Retardants: Enhance fire resistance for safety in critical applications.
- Reinforcing Fillers: Materials like glass fibers or carbon fibers increase the composite’s strength and stiffness.
These modifications allow reinforced thermoplastics to meet specific industry standards for safety, durability, and performance.
Challenges in Using Thermoplastic Composites
Despite their many advantages, thermoplastic composites present certain challenges that manufacturers must consider. One of the primary drawbacks is the higher material cost, particularly with advanced polymers like PEEK, which can be significantly more expensive than traditional materials. Additionally, the composite manufacturing processes for reinforced thermoplastics can be complex, often requiring specialized equipment and precise control of temperature and pressure, leading to higher initial setup costs. While thermoplastics generally offer good heat resistance, they may not perform as well as thermoset composites in extremely high-temperature environments, which can limit their use in specific applications. Bonding can also be a challenge, as achieving strong adhesive joints with reinforced thermoplastics is often more difficult compared to thermoset materials, requiring additional surface treatments or the use of mechanical fastening techniques.
To sum up, thermoplastic composites are shaping the future of material engineering with their unique combination of strength, lightweight properties, and recyclability. Their versatility makes them suitable for a wide range of industries, including composites in automotive, aerospace, construction, and medical devices. While they present certain challenges like higher material costs and complex composite manufacturing processes, their long-term benefits in sustainability, performance, and design flexibility make them a valuable investment. As technology advances, reinforced thermoplastics will continue to drive innovation in modern manufacturing.