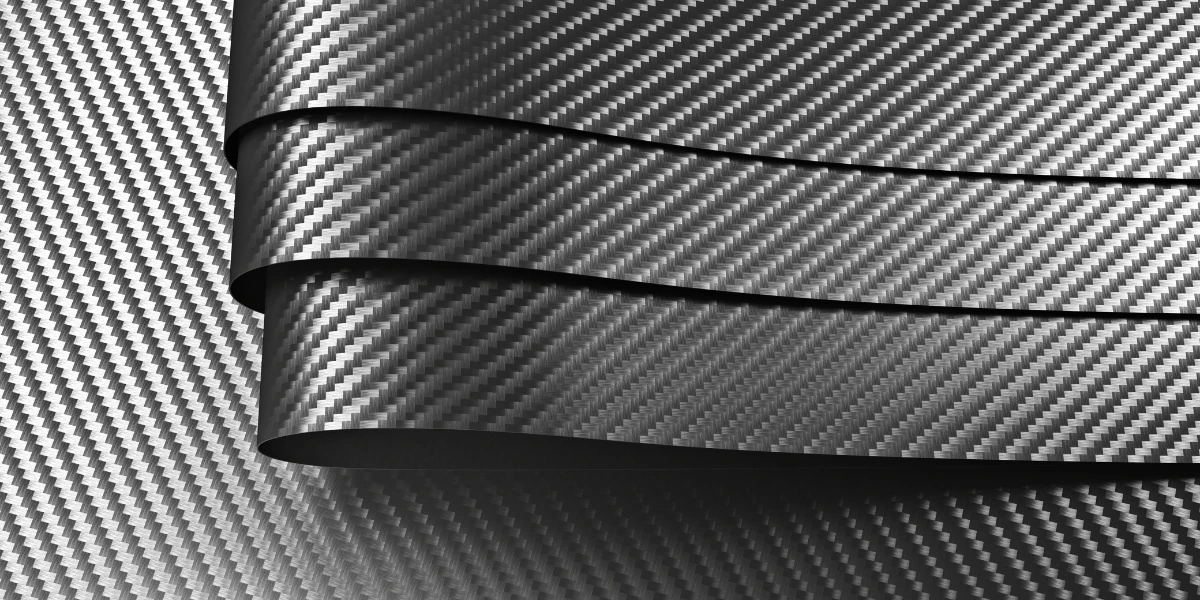
- Blog
- 18 Apr 2025
Prepreg Production Process: A Step-by-Step Guide
Prepreg materials play a crucial role in the world of advanced composites, offering high strength, durability, and precision. Used across industries like aerospace, automotive, and sports equipment, prepregs are essential for producing lightweight yet strong components. The prepreg production process involves carefully impregnating reinforcement fibers—such as carbon fiber—with a resin matrix, typically epoxy resin, under controlled conditions. This results in partially cured sheets that are easy to handle, store, and later mold into complex shapes. Mastering this process ensures high-quality composite parts with superior performance and consistency. In this guide, we will explore each stage of prepreg production, key materials used, and factors that influence the final product’s quality.
What Is Prepreg? Definition and Importance
Prepreg, short for “pre-impregnated,” refers to reinforcement fibers—such as carbon or glass fibers—that have been pre-coated with a resin system, usually epoxy resin. This resin is partially cured during the prepreg production process, allowing the material to remain tacky and flexible for easy handling and shaping before final curing. Prepregs are highly valued in industries like aerospace, automotive, and sports due to their excellent strength-to-weight ratio, consistent quality, and superior mechanical properties. They enable precise control over fiber-resin ratios, leading to lightweight yet durable components with minimal material waste.
Raw Materials Used in Prepreg Production
The prepreg production process relies on high-quality raw materials to achieve optimal performance in the final composite. The two main components are reinforcement fibers and resin systems. Common reinforcement fibers include carbon fiber, glass fiber, and aramid fiber, with carbon fiber plates being a popular choice for their exceptional strength-to-weight ratio. These fibers provide the structural backbone of the prepreg. The resin system, typically an epoxy resin, acts as the binding agent, offering durability, chemical resistance, and strong adhesion to the fibers. Additional materials like peel ply are sometimes used during production to create a textured surface for better bonding in later stages. The careful selection and combination of these materials directly impact the quality and performance of the prepreg.
Step-by-Step Prepreg Production Process
The prepreg production process involves several precise steps to ensure the fibers are properly impregnated with resin and prepared for later molding and curing. Below is a breakdown of each stage:
Impregnation of Fibers with Resin
The process begins by feeding continuous reinforcement fibers, such as carbon fiber plates, into an impregnation system. These fibers pass through a resin bath or are coated using heated rollers to ensure even distribution of the epoxy resin. The goal is to fully saturate the fibers while maintaining a controlled resin-to-fiber ratio. Proper impregnation is crucial for achieving the desired mechanical properties and ensuring the prepreg’s consistency across different batches.
Controlled Curing and Partial Polymerization
After impregnation, the resin undergoes controlled heating to initiate partial curing, a process known as B-staging. This step allows the resin to reach a tacky yet stable state, making the prepreg flexible and easy to handle. Controlled curing ensures that the resin does not fully harden, preserving the material’s moldability for later processes like composite autoclave curing, where final hardening takes place.
Rolling and Storage of Prepreg Sheets
Once partially cured, the prepreg sheets are carefully rolled onto protective backing paper to prevent sticking and contamination. Materials like peel ply may be added to the surface to assist in later bonding processes. The rolls are then stored in controlled environments, usually at low temperatures, to slow down the curing process and extend shelf life. Proper storage is essential to maintain the prepreg’s quality until it’s ready for final molding and curing.
Key Factors Affecting Prepreg Quality
The quality of prepreg materials directly impacts the performance and durability of the final composite product. Several key factors in the prepreg production process influence this quality:
- Fiber-Resin Ratio: Maintaining the correct balance between reinforcement fibers and epoxy resin is critical. Too much resin can lead to weak, brittle parts, while too little can result in dry areas that compromise structural integrity.
- Impregnation Uniformity: Even distribution of resin across the fibers ensures consistent mechanical properties throughout the prepreg. Uneven impregnation can create weak spots and affect the final product’s performance.
- Temperature and Curing Control: Precise temperature management during partial curing (B-staging) is essential. Over-curing can harden the prepreg prematurely, while under-curing affects tackiness and handling. Controlled environments, like composite autoclaves, are often used in later stages to complete the curing process under optimal pressure and temperature.
- Storage Conditions: Prepreg sheets must be stored at low temperatures to prevent further curing before use. Poor storage conditions can reduce shelf life and affect the material’s flexibility and bonding capabilities.
- Cleanliness and Contamination Control: Any contamination during production, such as dust or moisture, can weaken the prepreg. Using protective materials like peel ply helps maintain surface quality and enhances bonding during final assembly.
Ensuring strict control over these factors guarantees high-quality prepregs that meet the performance demands of industries like aerospace, automotive, and sports.
Applications of Prepreg Materials
Prepreg materials are widely used across industries where strength, durability, and lightweight properties are essential. In the aerospace sector, prepregs are commonly used for aircraft structures, wings, and fuselage components due to their excellent strength-to-weight ratio. In the automotive industry, they help produce high-performance parts like body panels, hoods, and interior components, especially in motorsports and luxury vehicles. The sports and leisure industry also benefits from prepregs, using them in items like bicycles, tennis rackets, and golf clubs for enhanced strength and reduced weight. Additionally, in the wind energy sector, prepregs are used to manufacture durable, lightweight wind turbine blades. Thanks to the precision and consistency offered by the prepreg production process, industries can achieve superior product performance with reduced material waste.
The prepreg production process plays a crucial role in creating high-performance composite materials that meet the demanding standards of various industries. From the careful selection of raw materials like carbon fiber plates and epoxy resin to precise steps like impregnation, partial curing, and controlled storage, every stage impacts the final product’s quality. By understanding these processes and key quality factors, manufacturers can produce prepregs that offer exceptional strength, durability, and design flexibility. Whether in aerospace, automotive, or sports, prepregs continue to shape the future of lightweight, high-performance components.