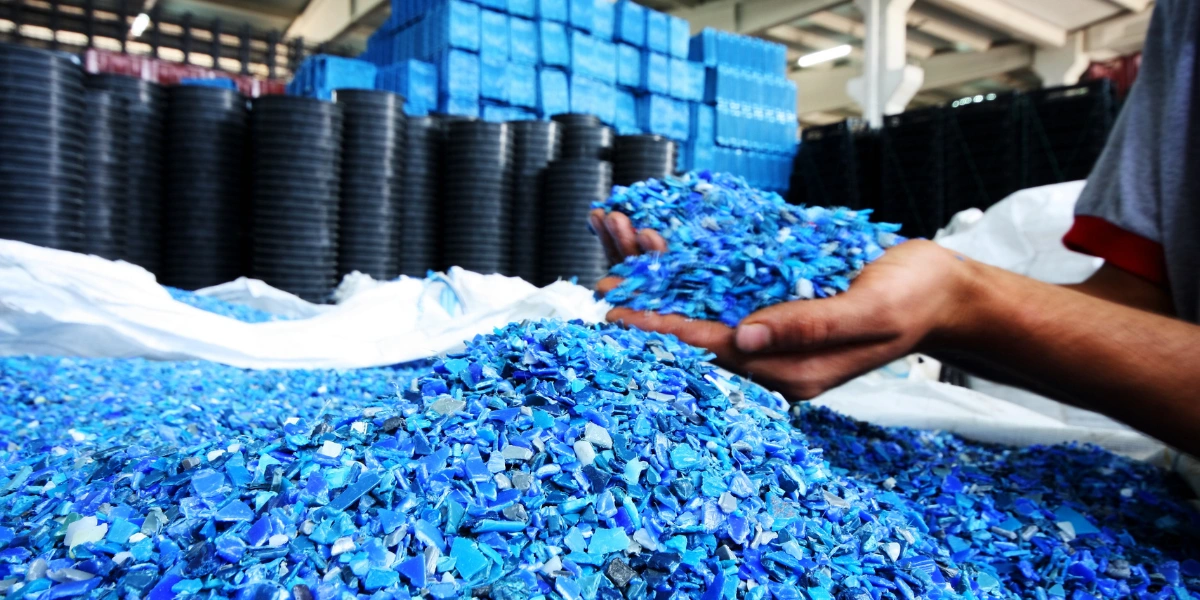
- Blog
- 30 Jan 2025
Plastic Manufacturing: Transforming Modern Industries
Plastic manufacturing is everywhere. From the packaging of the food we eat to the parts in the cars we drive, plastic has become a fundamental material that shapes our daily lives. It is used because it is versatile, affordable, and adaptable to a wide range of applications. The ability to mold plastic into any shape means it can be used for countless products. As industries continue to grow and evolve, manufacturing adapts to meet new demands, making it a crucial part of the modern economy. In this article, we will explore how plastic manufacturing is influencing industries, the processes involved, and the trends driving the industry towards a sustainable future.
The Role of Plastic Manufacturing in Modern Industries
Plastic manufacturing has become a crucial part of many modern industries. It plays a significant role in making a wide variety of products that we use every day. From car parts to household goods, plastics are used because they are versatile, lightweight, and durable. The affordability and flexibility of plastic make it an attractive material for manufacturers, allowing them to create everything from small, intricate components to large, robust structures. As industries evolve, manufacturing continues to meet new demands, providing solutions that are cost-effective and efficient.
Key Plastic Manufacturing Processes
There are several key processes used in plastic manufacturing, each with its unique advantages. Understanding these processes is essential to see how plastic items are made and how they differ in their applications.
Injection Molding
Injection molding is one of the most common methods used in plastic manufacturing. This process involves injecting molten plastic into a mold to create a desired shape. Injection molding is ideal for producing high volumes of parts with precision. It is often used for making products like bottle caps, automotive parts, and household containers. One of the main benefits of injection molding is that it allows for detailed designs with consistent quality. Mold release agents are often used to ensure that the finished part can be removed from the mold smoothly without damage. This process is highly efficient for mass production and results in durable products.
Blow Molding
Blow molding is another widely used plastic manufacturing process, particularly for creating hollow parts like bottles and containers. In blow molding, plastic is heated until it becomes soft and then blown into a mold to form a shape. The main advantage of blow molding is its ability to produce uniform, thin-walled hollow items at a low cost. This method is very common in the packaging industry, where plastic bottles and containers are produced in large quantities. Blow molding is essential in creating items that are lightweight and resistant to impacts, making them suitable for food and beverage storage.
Thermoforming
Thermoforming is used to shape plastic sheets into specific forms by heating them until they become flexible. The heated plastic sheet is then placed over a mold and pressed into the desired shape. This process is simple but highly effective, especially for creating large parts or products with shallow details. Thermoforming is commonly used to make packaging trays, cups, and lids. Because it works well with a variety of plastics, thermoforming is a versatile manufacturing method. It is also cost-effective for producing items in medium to large quantities, making it useful for many industries, especially in packaging and consumer goods.
3D Printing with Plastics
3D printing is a relatively new method in plastic manufacturing but has already made significant impacts. This process allows manufacturers to create plastic parts layer by layer, directly from a digital design. The main advantage of 3D printing is its ability to create complex and customized parts without the need for molds. It is often used for prototyping or creating small batches of unique items. With the development of various plastic materials, including polyester resins and other composites, 3D printing has opened up new possibilities for creating strong and lightweight parts. It has revolutionized fields such as healthcare, where custom medical devices can be printed quickly and efficiently.
Industries Transformed by Plastic Manufacturing
Plastic manufacturing has transformed various industries by offering affordable and flexible solutions. The automotive industry, for example, relies on plastics for lightweight components that improve fuel efficiency. Plastic parts are used in everything from bumpers to dashboards, which helps reduce vehicle weight and enhances performance. In the medical industry, plastics are used to create sterile, disposable items like syringes and tubing, which help maintain hygiene and reduce contamination risks. The electronics industry also benefits from plastic manufacturing as plastics are used for casings, insulation, and many small parts in electronic devices.
Additionally, the construction industry has seen changes with plastic manufacturing. Materials like FRP reinforcement (Fiber-Reinforced Polymer) are used to strengthen structures while keeping them lightweight. FRP reinforcement is popular because it offers high strength while being corrosion-resistant, making it ideal for use in environments where traditional materials might degrade.
Sustainable Practices in Plastic Manufacturing
The plastic manufacturing industry is working towards more sustainable practices to reduce its environmental impact. Recycling is one of the main ways manufacturers are trying to make plastic production greener. Many factories now use recycled plastics to make new products, which reduces waste and the need for raw materials. Additionally, biodegradable plastics are being developed to lessen the environmental impact of plastic products after their use. Sustainable practices also include reducing energy consumption during manufacturing by using more efficient machinery and processes. The use of epoxy resin, for example, is not only to enhance product durability but also to reduce the frequency of replacements, leading to less waste over time.
Challenges and Future Trends in Plastic Manufacturing
Plastic manufacturing faces several challenges, particularly concerning environmental concerns and waste management. The industry is under pressure to find ways to reduce plastic waste and improve recycling methods. Many consumers and governments are pushing for alternatives to single-use plastics, which has led to innovation in biodegradable and compostable materials.
In terms of future trends, there is a focus on improving manufacturing processes to be more energy-efficient and less polluting. 3D printing, for example, continues to evolve, allowing for less material waste compared to traditional methods. Mold release agents are also being improved to be more environmentally friendly, reducing the number of chemicals used in the manufacturing process. Additionally, the development of advanced materials like polyester resins and other sustainable alternatives is helping shape a future where manufacturing is more aligned with environmental needs.
The future of plastic manufacturing will be defined by a balance between innovation and sustainability. Manufacturers are looking for ways to meet consumer needs while reducing their environmental impact. By adopting new technologies, using recycled materials, and improving production methods, plastic manufacturing can continue to shape modern industries while moving toward a greener future.