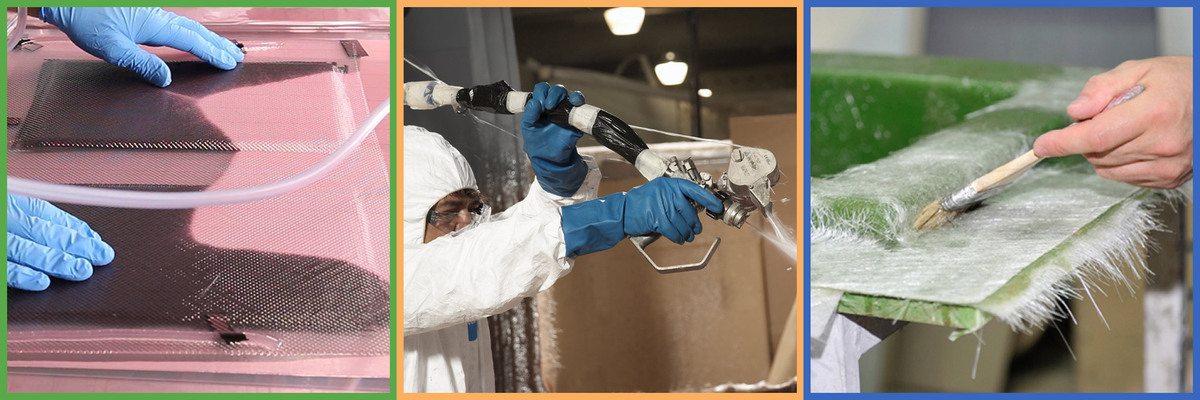
- Technical Bulletin
- 10 Oct 2023
Overview of Composite Production Methods
Composite materials are used in dozens of different sectors. With the rapid increase in application areas, composite production methods continue to diversify and develop. It is necessary to consider these methods, which differ according to their usage areas, one by one. Before discussing these methods, it is useful to know what composite material is and what it does. In this article, we look at what a composite is and how it can be processed.
What is Composite?
A new material created by combining two or more raw materials is categorically called a composite. The resulting material is expected to have superior properties of the combined materials. Composites, which are also formed from matrix and reinforcement materials, are used extensively in the aerospace, marine, infrastructure, energy and automotive sectors. It should also be mentioned that there are different composite production methods depending on the area of use.
What are Composite Production Methods?
When it comes to polymer-based composite materials, production methods can be examined under two main headings: open molding and closed molding. These methods play an important role in achieving the unique properties and performance of composite materials.
Open Molding
This method uses a single mold or guide and has 3 different sub-production techniques: hand lay-up, spraying and cord winding. This method is uncomplicated and cost-effective, requiring a small amount of equipment. Open molding is also the most widely used method in the composite manufacturing process.
1.Hand Deposit Method
In hand lay-up, also known as hand lay-up, the reinforcing fabrics are applied to the molds by hand and the liquid resin is impregnated into the fiber layers. In the hand lay-up method, the mold must first be cleaned and gelcoat must be applied to the surface. After gelcoat and skink coat (surface layer), the fiber layers are wetted with resin and laid down. The most important point to be considered in hand lay-up, which is the most basic composite production method, is the good penetration of the resin into the fiber layers.
2. Spraying Method
The spraying method is more efficient than a hand lay-up method. With less resin consumption, a higher fiber/resin ratio is achieved in the part. It accelerates the mass production of parts with a particularly large surface area. In this method, chopped fibers are sprayed into the mold with the help of a special gun. The trimmer on the gun ensures that the fibers are trimmed, the resin sprayed with the hardener at the gun tip is mixed and the resin mixture is thrown into the mold together with the trimmed fibers. Spraying perpendicular to the surface should be taken into account as this will avoid material waste. Clippers and spraying machines can be attached to the robot arms, making the process semi-automatic. After spraying, the rolling process is applied. This process removes the air from the resin.
3. Fiber Winding (Filament Winding Method)
The fiber winding method is suitable for mass production. In this process, the fibers are continuously wetted with resin. Then it will be pulled from the reel and wound on the mold (madrel) which has a rotating mechanism. Products wound from different angles can produce products with different mechanical properties.
In order to get effective performance in the winding process, many variables such as pipe diameters, fiber angle, belt width, mandrel speed come into play. When the fiber solid is wound in sufficient quantity, the product will harden and separate into molds. Products such as water tanks, circular pressure tanks and cylindrical pipes are generally produced by fiber winding. With roving winding, it is possible to produce in a wide range of scales starting from small diameters up to huge infrastructure pipes with a diameter of 3 meters.
Closed Molding
One of the basic methods to be discussed in composite production methods is closed molding. It makes it possible to produce parts with better performance than open mold applications. The closed molding method uses a mold that completely encloses the product and therefore (except for vacuum infusion) the entire double-sided outer surface of the product comes out with mold surface quality. In open molding methods, a good surface can be obtained only on one side of the mold surface. Another fundamental and important difference is that the curing reaction of the resin can take place under controlled and desired conditions in closed mold production methods.
1. Resin Transfer Molding Method (RTM)
The resin transfer molding method is applied for parts with or without gelcoat. Felt, fabric or both are used in a dry way. RTM fibers, a raw material produced by combining glass fiber felts with a polypropylene or polyester flow medium in the middle, are designed for the RTM process. RTM fibers are now used in the RTM method. After the reinforcement material is placed in the mold, the mold is closed. Then the resin is pumped into the mold under pressure with the help of the RTM machine.
With the resin injection method, a higher quality product is obtained more quickly and economically compared to hand lay-up. Large-sized parts with complex geometries, as well as parts with sandwich structures, can be molded in a single process and different wall thicknesses can be achieved in different regions. In addition, an advantage in terms of environmental health is that the styrene in the polyester used does not evaporate into the environment since the system is closed.
2. Vacuum Infusion Method
The basic principle of the method, known as infusion for short, is that the resin is taken into the mold and with it into the fiber layers by vacuum. The fiber reinforcements are placed on the mold, then sealed with vacuum consumables and finally the vacuum bag, which will ensure air tightness. A vacuum pump takes the mold under vacuum from the air suction point determined on the system and the resin fed from the resin inlet points passes through the mold and tries to reach the pump. Since the mold is under vacuum in this process, the molding takes place under a load equal to atmospheric pressure without using any press. In this way, a higher and more stable fiber/resin ratio can be achieved and the mechanical performance of the part is improved. With the relatively simple vacuum infusion method, products with complex shapes and high mechanical performance can be produced.
3. SMC-BMC Hot Pressing Method
It is a method that provides hardening of ready-made molding products based on the effect of heat and pressure. It is the fastest process among composite production methods. It is a fast, serial molding method that provides a molding time of 3-6 minutes depending on the product size. It is possible to shape the pre-prepared, pulpy or doughy glass fiber-polyester-filler and additive mixture in metal molds at a temperature of 150-170 °C and under a pressure of 5-120 kgf/cm2.
It is used in mass production for composites. The hot pressing method used in the production process of composite products allows different materials to be combined under temperature and pressure. Pre-prepared composite materials are placed between hot molds. This method is particularly used in industrial applications.
5. Pultrusion Method
The pultrusion method is based on the principle that continuous glass fiber rovings are impregnated in a resin bath and then hardened as they are drawn through a hot die in the desired profile. Since the fiber reinforcements are arranged parallel to the length of the profile, very strong parts with a very high fiber ratio can be produced in one direction.
The pultrusion method, also called profiling, ensures low labor costs. Because it is an automated process, pultrusion supports rapid production. In addition, since pultrusion is a continuous process, parts of the desired length can be produced.
6. Continuous Lamination Method
In the continuous lamination method, which is among the composite production methods, composite products in sheet form are obtained. The fiber reinforcements, together with the resin, are compressed between two plastic films and baked while being pulled and baked to produce smooth, corrugated, transparent or opaque sheets on both sides. The method uses special lamination machines. The fiber-reinforced resin hardens rapidly in these machines under the influence of heat and pressure. The cured laminate can then be wound into coils and cut to specific sizes.
As a result, the sole purpose of all these methods is to enable composite products to be obtained. Composite, which is a durable and lightweight material, is produced by different methods. Composite production methods affect the properties and performance of composite materials. Therefore, it is important to choose the right methods according to the desired product and product quality.