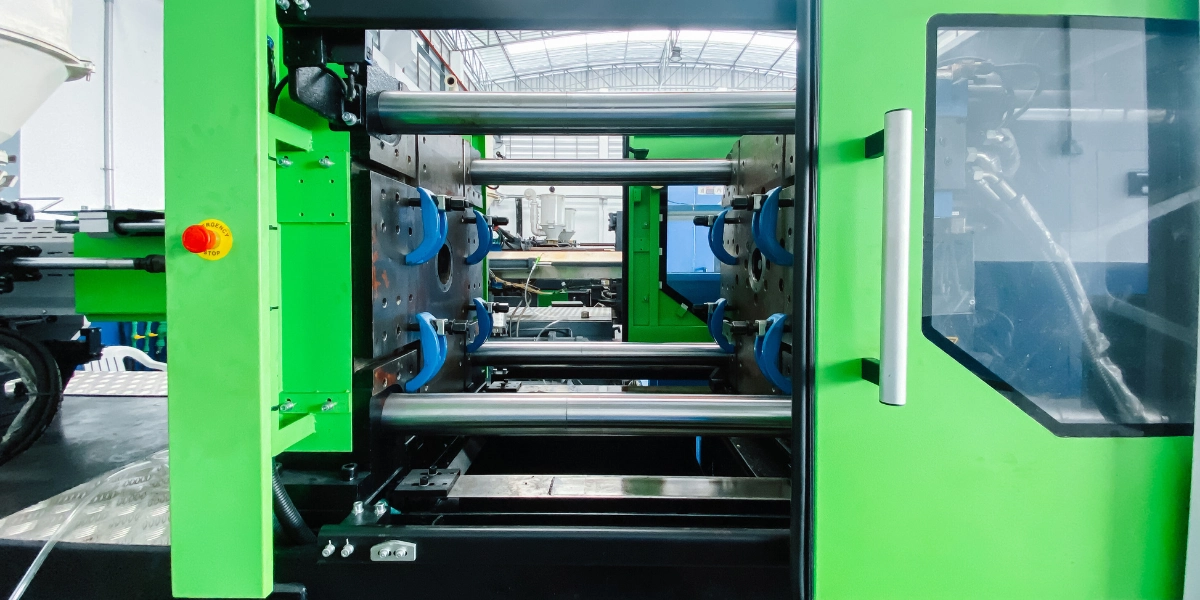
- Blog
- 20 Jan 2025
Understanding the Injection Molding Process
Injection molding is a popular manufacturing method used to make plastic parts. It is a process that allows manufacturers to create detailed components with high precision, and it’s commonly used in many industries, from automotive to consumer goods. The molding process uses various materials, including plastic and resins, to create parts quickly and efficiently. Interestingly, this method can also be used with carbon fiber supplements to make parts even stronger and lighter. In this article, we will explore what injection molding is, how it works, and why it is so valuable in manufacturing.
What Is Injection Molding?
Injection molding is a manufacturing process used to produce parts by injecting molten material into a mold. This process is typically used to create plastic parts, but it can also be used with metals, glass, or even composites. The method is efficient and cost-effective, particularly when creating large quantities of the same part. The key to molding is the mold, which defines the shape and features of the final product. By using a mold, manufacturers can produce complex shapes that would be difficult or impossible to achieve with other methods.
The Steps of the Injection Molding Process
The injection molding process consists of several key steps that ensure the final product meets the desired specifications. Each step is essential to making sure the final component is of high quality and free from defects.
Clamping
The first step in the injection molding process is clamping. In this step, the mold, which is usually made up of two halves, is held firmly in place by a clamping unit. The clamping unit ensures that the mold is securely closed so that the molten material can be injected without any leaks. The clamping force is crucial, especially when dealing with high-pressure materials that need to be injected with precision.
Injection
Once the mold is clamped tightly, the next step is injection. In this stage, the molten material, which can be plastic, epoxy resin, or even composites, is injected into the mold cavity. The molten material is pushed through a nozzle by an injection unit under high pressure. This stage is essential because it fills the mold entirely, ensuring that every part of the mold cavity is filled, creating the desired shape. The injection process is controlled carefully to avoid any air pockets or imperfections.
Cooling
After the molten material is injected, the cooling stage begins. Cooling is when the molten material solidifies and takes on the shape of the mold. This process can take a few seconds to several minutes, depending on the material used and the thickness of the part. Cooling is a crucial step because it affects the final properties of the part, including its strength and dimensions. Mold release agents may be used during this stage to help remove the cooled part easily from the mold without causing damage.
Ejection
The final step in the molding process is ejection. Once the part has cooled and hardened, it must be removed from the mold. The mold opens, and ejector pins push the part out of the mold cavity. Ejector pins are designed to minimize damage to the part as it is removed. After ejection, the part may require a few finishing touches, such as trimming excess material or polishing.
Advantages of Injection Molding in Manufacturing
Injection molding is a popular method in manufacturing for several reasons. One of the main advantages is its efficiency. Once the initial mold is created, the process can produce large quantities of parts in a short amount of time. This makes it ideal for mass production. Injection molding also offers great precision, which is vital for components that need exact specifications.
Another advantage is the versatility of materials. Manufacturers can use many different types of materials, such as plastics, composites, and resins. Polyester resins, for example, are commonly used for parts that require good flexibility and durability. The wide range of materials allows manufacturers to produce parts with a variety of properties, making injection molding useful for many different industries.
Key Materials Used in Injection Molding
There are several materials that are commonly used in injection molding. These materials are chosen based on the specific needs of the product, including strength, flexibility, and resistance to heat or chemicals.
Plastics are the most common materials used in molding. Thermoplastics like polypropylene, polyethylene, and ABS are popular because they are easy to work with and can be melted and reformed without degrading. Epoxy resin is also used for parts that require a high level of strength or are exposed to high temperatures. Epoxy resin is known for its adhesive properties and can add structural integrity to parts that need it. Additionally, glass reinforced concrete and other composite materials can also be used to create components that need added strength without a lot of weight.
Common Applications of Injection Molding
Injection molding is used in a wide variety of applications, and its versatility makes it valuable in many industries. In the automotive industry, molding is used to produce parts like dashboards, bumpers, and other internal components. These parts need to be both lightweight and durable, which makes injection molding a great choice.
The consumer goods industry also benefits from injection molding. Everyday items like plastic containers, toys, and household products are often made using this process. The ability to quickly produce large numbers of parts makes injection molding ideal for items that are mass-produced.
In the medical industry, precision is crucial. This type of molding is used to make components like syringes, medical equipment, and other small parts that require high levels of accuracy. Medical-grade materials are used to ensure that the parts are safe and meet strict quality standards. This method ensures consistency and quality across all the parts produced.
Injection molding is a versatile and efficient way to produce high-quality parts for various industries. By understanding the different steps of the process, the materials used, and the advantages it brings, it becomes clear why molding is such a valuable tool in modern manufacturing.