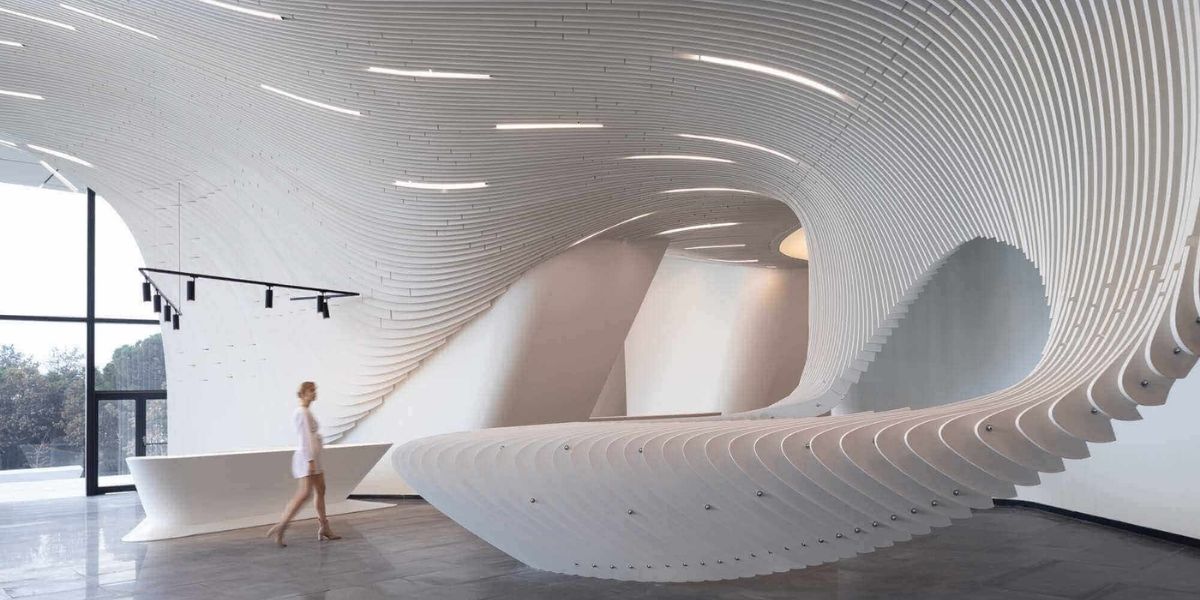
- Technical Bulletin
- 23 Oct 2023
GRC (Glass Fiber Reinforced Concrete) and Its Advantages
GRC (Glass Fiber Reinforced Concrete), which provides architects and engineers with the advantage of realizing the original facade arrangements and textures of their dreams and adding an artistic dimension to the facades, is one of the important materials of the construction industry. In this article, we will look at why this material should be used and the systems of application.
What is Glass Fiber Reinforced Concrete (GRC)?
GRC is the name given to the material formed after the high performance cement-based composition is reinforced with “alkali-resistant” glass fiber. In order to create a high-performance cement composition, silica sand and high quality white cement must be mixed in a precise ratio. The resulting blend is placed in molds with Alkali resistant glass fiber and polymer reinforcements. Alkali resistant glass fiber provides strength thanks to the zirconium on it and acts as reinforcement without melting in the cement.
The Importance of Quality Raw Materials and Equipment for GRC Production Technology
The materials needed to create glass fiber reinforced concrete must be of high quality. Deficiencies in the quality of these materials will prevent the cement-based product from fulfilling its task with full efficiency and cause the intended use of the product not to be achieved. This material allows the carcass carrier to work, turning the disadvantages of concrete, the basic load-bearing system of construction, into advantages. Thanks to these advantages, this material is critical for construction and its long-term use. For this reason, it is necessary to create this material from quality raw materials and to maintain the required precise ratio when creating it. In this context, the use of good equipment is essential to get the ratio right.
AR (Alkali Resistant) Glass Fiber
Two different production applications have been developed for the production of this material: spraying and premixing. Alkali Resistant Glass Fiber is critical in eliminating or turning many disadvantages into advantages in construction. Looking at the advantages of the material:
- Prevents cracks in concrete and provides strength.
- It replaces steel mesh, which is difficult to use.
- Thanks to its homogeneous distribution in the mixture, it controls shrinkage and cracking during the drying phase.
- Thanks to its specific gravity being the same as concrete, it does not settle to the bottom and leaves no traces on the surface.
- In addition to the compressive strength provided by ordinary concrete, it also has high limits in terms of tensile strength.
- It is 3 times more durable and 4 times more flexible than steel mesh, which is difficult to use, and offers a long service life with its stainless structure.
Acrylic Polymers for GRC (Glass Fiber Reinforced Concrete) Applications
Polycure FT, an acrylic polymer curing agent, provides moist curing in glass fiber reinforced concrete production. When used correctly and in sufficient quantities, Polycure FT forms a membrane layer on the mold, thus helping to reduce permeability. This property of the material prevents water from evaporating away and allows the cement to retain the moisture needed for hydration. Both methods developed for the production of this material use the Super Fluidizer Flowaid FT. The main purpose of using this method of spraying is to reduce the amount of water added to the cement. In this way, it is aimed to provide the desired fluidity and reduce the working time. The premix method, on the other hand, offers the advantages of high fluidity, low segregation, simpler mold production and longer mold life. Super Fluidizer PUMPAID FT is used for GRC material produced for pumping or coating processes, while FLOWAID SCC contributes to mold life and simple mold production thanks to its high fluidity.
Spraying and Fiber Trimming Systems for GRC Applications
Power Spray has been contributing to the development of production systems for this material for more than 60 years. Thanks to spraying and fiber trimming systems, alkali resistant roving fiber and GRC mortar are poured into the mold at the same time. The spraying method is used during this process. The main reason for using the spraying method at this point is to shorten the process time and achieve a better result in terms of strength. In the relevant method, the thickness of this material is preferred between 10-15 mm.
Power Spray GRC Systems
Power Spray GRC systems, which are compatible with the company’s products, are the most preferred system in the production of this material. That this system is so popular;
- High mobility of the entire system,
- Convenient height of the electric/pneumatic control panel with double chamber,
- This is due to its advantages, such as easy access to control instruments and protection of sensitive parts with a waterproof control cabinet.
PS9000A Spray System
The PS9000A Spray System, which is the most preferred system by glass fiber reinforced concrete producers due to its ease of use, brings many advantages. High mobility, easy loading and a structure that protects sensitive parts make the system highly preferred. The working principle of the system is based on a layout with air and mortar hoses connected, weight distributed and a hydrostatic transmission with variable speeds by a three-phase electric motor. Since the mortar damper is able to apply a low level of vibration, the system allows both manual and automatic filling. Thanks to the removable sieve, the soil reaches the pump easily and does not clog the spray nozzle.
In this article, we have touched upon what glass fiber reinforced concrete material is, how it is used in which areas and what advantages its use brings with it.