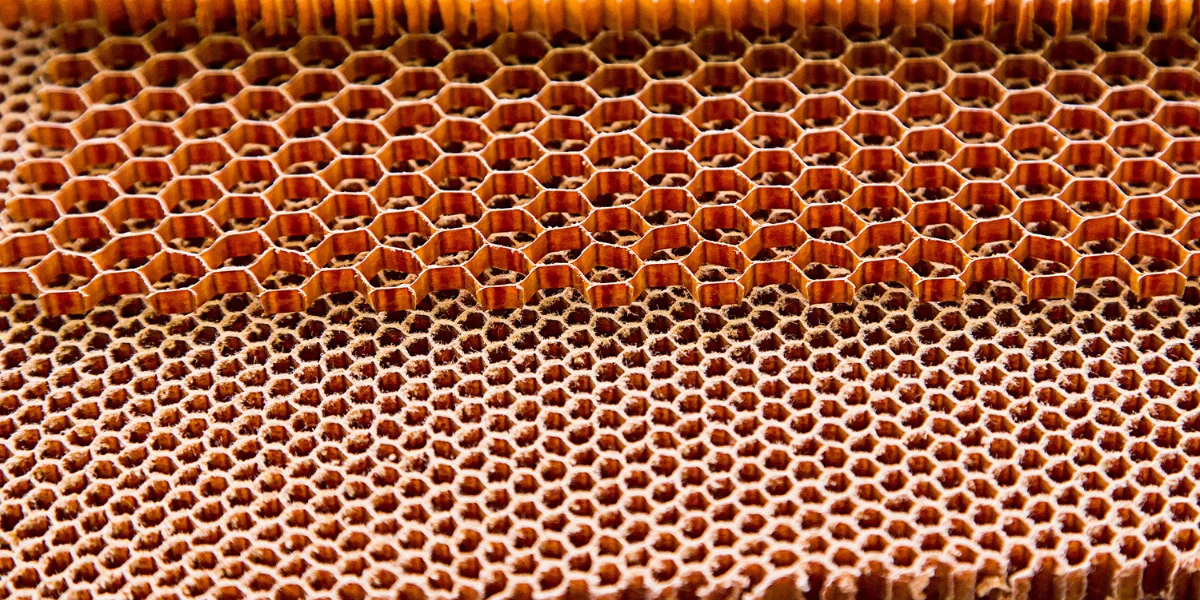
- Blog
- 10 Jan 2025
Key Composite Manufacturing Processes and Their Applications
Composite materials have become an integral part of modern engineering and manufacturing, offering a unique combination of strength, lightweight characteristics, and adaptability. The use of composites has expanded into multiple industries, from aerospace to automotive, all of which require specific properties that traditional materials often cannot provide. To harness the full potential of composite materials, it’s essential to understand the composite manufacturing processes involved. In this article, we will take a closer look at some of the key composite manufacturing processes, both traditional and advanced, as well as their applications and advantages.
Key Composite Manufacturing Processes
The production of composite materials involves several different manufacturing techniques, each suited to specific requirements and end-use applications. Here, we explore some of the most common composite manufacturing processes, including hand lay-up, resin transfer molding, filament winding, and pultrusion.
Hand Lay-Up
Hand lay-up is one of the oldest and simplest composite manufacturing processes. In this technique, layers of reinforcing material, such as fiberglass, are manually placed into a mold and saturated with resin. The layers are then left to cure, resulting in a strong composite structure. Hand lay-up is ideal for creating large, complex shapes with relatively low tooling costs, making it popular for producing boat hulls, panels, and custom parts. This process is particularly suitable for applications requiring flexibility in design, although it may be labor-intensive and less consistent compared to more automated processes.
Resin Transfer Molding (RTM)
Resin Transfer Molding (RTM) is a more sophisticated composite manufacturing processes that provides higher precision and repeatability than hand lay-up. In RTM, dry fibers are placed into a closed mold, and then liquid resin is injected to saturate the fibers. Once the resin cures, the part is removed from the mold. RTM is well-suited for producing medium to high-volume parts with consistent quality, and it offers greater control over fiber placement and resin usage. RTM is frequently used for automotive components, where both performance and repeatability are key considerations.
Filament Winding
Filament winding is a specialized composite manufacturing process used to create cylindrical shapes such as pipes, tanks, and pressure vessels. In this process, continuous fibers are wound around a rotating mandrel in a specific pattern and impregnated with resin. This technique allows for precise control over fiber orientation, which is crucial for optimizing strength. Filament winding is particularly effective for applications that require high mechanical properties, such as aerospace and industrial piping systems. By using advanced winding techniques, manufacturers can ensure that the final product meets stringent performance standards.
Pultrusion
Pultrusion is a continuous composite manufacturing processes used to produce long, straight components with a constant cross-sectional profile. In pultrusion, fibers are pulled through a resin bath and then through a heated die, where they are cured into a solid profile. This process is ideal for producing beams, rods, and channels used in construction, infrastructure, and utility applications. Pultrusion is efficient and cost-effective, making it an attractive choice for producing large quantities of composite materials. When combined with FRP reinforcement, pultruded products offer high strength and excellent durability, especially in environments that require resistance to corrosion and moisture.
Advanced Composite Manufacturing Processes
As composite technology evolves, so do the manufacturing processes that make these materials. Advanced composite manufacturing processes offer greater precision, automation, and flexibility. Below, we discuss some of the latest techniques, including Automated Fiber Placement, Automated Tape Laying, and 3D printing for composites.
Automated Fiber Placement (AFP)
Automated Fiber Placement (AFP) is an advanced composite manufacturing processes that uses robotic machinery to place fibers in precise patterns on a mold. This technology is often used for high-performance aerospace components where precision is critical. AFP allows for greater control over fiber alignment and placement, which is essential for optimizing the mechanical properties of the composite. With AFP, manufacturers can produce parts with complex geometries that would be difficult or impossible to achieve with manual methods. AFP also helps reduce material waste and increases production efficiency.
Automated Tape Laying (ATL)
Similar to AFP, Automated Tape Laying (ATL) is a composite manufacturing processes that uses automated systems to lay down pre-impregnated composite tapes in a continuous fashion. ATL is ideal for producing large, flat or slightly curved structures such as aircraft wings, fuselages, and wind turbine blades. The automation involved in ATL helps maintain consistency in part quality and minimizes labor costs. ATL also allows for the production of large-scale components more quickly compared to traditional hand lay-up techniques, making it an attractive option for high-volume production.
3D Printing for Composites
3D printing, also known as additive manufacturing, is a revolutionary approach to composite manufacturing that allows for the creation of complex, lightweight structures. In composite 3D printing, fiber-reinforced materials are used to print parts layer by layer, allowing for intricate designs and material optimization. This composite manufacturing process is still developing but holds significant promise for prototyping and small-scale production. 3D printing for composites can be used to create components with customized mechanical properties by strategically placing fibers to provide additional strength where needed. It also offers the flexibility to rapidly develop and test new designs without the need for costly molds.
Choosing the Right Composite Manufacturing Process
Selecting the right composite manufacturing processes depends on several factors, including the type of material, the desired properties of the end product, the production volume, and the cost constraints. For instance, hand lay-up may be suitable for low-volume, customized components, while advanced methods like AFP and ATL are more appropriate for high-performance aerospace parts that demand precision. When high strength and durability are required, FRP reinforcement can be incorporated into different processes, such as pultrusion or filament winding, to enhance mechanical properties. Ultimately, understanding the advantages and limitations of each composite manufacturing process will help in selecting the most efficient and cost-effective solution for a given application.
In conclusion, the field of composite manufacturing is vast and continually evolving, offering numerous methods to create high-performance materials that meet the needs of various industries. From traditional techniques like hand lay-up and RTM to advanced methods like AFP and 3D printing, each composite manufacturing process has its own unique strengths and applications. By choosing the right process for the job, manufacturers can ensure their composite products meet performance requirements while optimizing cost and efficiency. As technology continues to advance, we can expect even more innovative composite manufacturing processes to emerge, further expanding the possibilities for lightweight, durable, and high-performance materials.