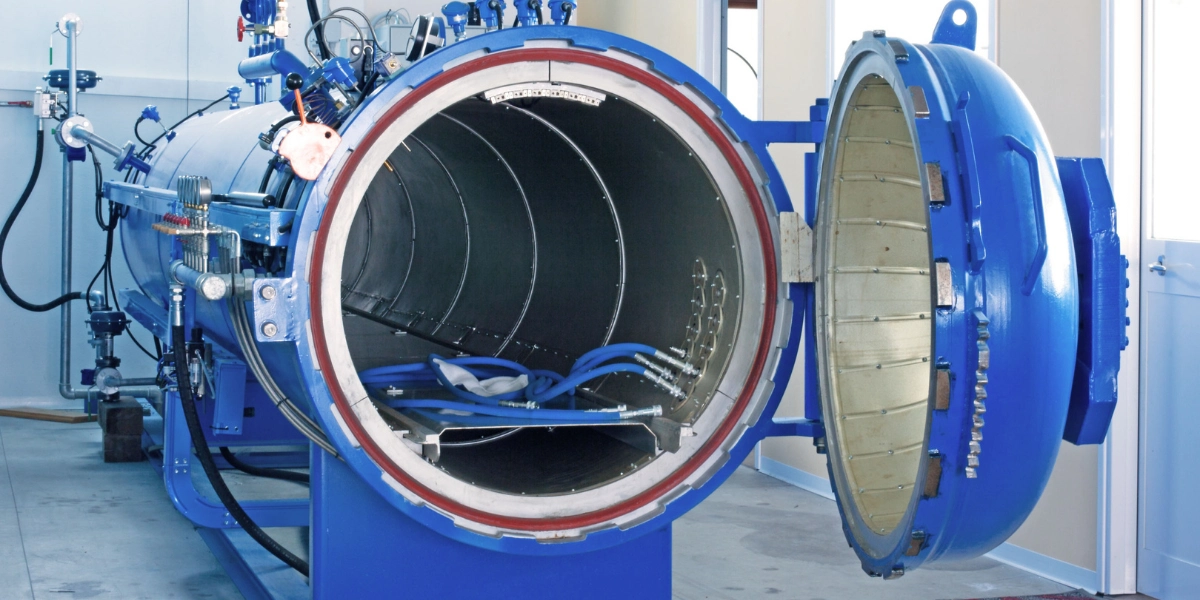
- Blog
- 13 Jan 2025
What Is a Composite Autoclave?
Composite autoclaves are an important part of making high-quality composite materials. These systems are especially useful when working with carbon fiber supplements, which add strength and durability to composite parts. If you’ve ever wondered how things like carbon fiber parts for airplanes or cars are made strong and lightweight, the answer often involves a composite autoclave. These machines use high pressure and heat to make sure the materials are strong and durable. This process is key in industries like aerospace and automotive, where the materials need to be light but incredibly tough.
What Is a Composite Autoclave?
Composite autoclaves are specialized pressure vessels designed to facilitate the curing process of composite materials, such as carbon fiber-reinforced polymers. This vessel process allows manufacturers to create lightweight, high-strength materials that are commonly used in aerospace, automotive, marine, and other industries requiring strong but light materials. These autoclaves can maintain high pressure and temperature levels, ensuring that the composite materials attain the desired level of strength, rigidity, and durability.
Composite materials, such as those incorporating carbon fiber supplements, are increasingly popular due to their high performance and light weight. Carbon fiber is often combined with other components, such as epoxy resin, which plays a crucial role in binding the fibers and adding structural integrity. By using a composite autoclave, manufacturers can precisely control the curing process, leading to consistent results and superior quality.
The Role of Composite Autoclaves in Composite Manufacturing
Composite autoclaves are integral to the manufacturing process of high-performance components. During the production of parts like aircraft wings, automotive body panels, or wind turbine blades, maintaining a precise and controlled environment is crucial. Composite autoclaves allow for a controlled high-temperature and high-pressure setting, which promotes a thorough curing process of the resin matrix.
The main function of this vessel is to eliminate voids and imperfections that may form during the lamination process. By applying pressure and heat, the autoclave helps compact the laminate layers, improving the bonding between fibers and the resin. This meticulous process ensures the finished product exhibits excellent mechanical properties, reduced flaws, and enhanced durability.
How Does the Composite Autoclave Process Work?
The composite autoclave process is all about using high pressure and heat to create strong and durable composite materials. This process involves several steps, starting with the careful preparation of materials, followed by the curing phase inside the autoclave, and ending with thorough quality checks. Each stage is crucial in ensuring that the final product meets the desired strength and quality standards. Let’s break down how each part of this process works to better understand how composite materials are transformed into high-performance components.
Preparation of Composite Materials
The composite autoclave process begins with the preparation of the composite materials. Typically, carbon fiber or fiberglass fabrics are impregnated with a resin, usually an epoxy resin, which acts as the matrix to bind the fibers. These pre-impregnated materials, commonly known as prepregs, are then laid up in layers, either manually or using automated processes, to create the desired component shape.
Vacuum consumables play a critical role in this phase. To ensure optimal quality, the composite layup is covered with a vacuum bag, which is sealed around the mold to create a vacuum environment. The vacuum helps to remove air pockets and allows better compaction of the laminate layers during the autoclave process.
Autoclave Curing Cycle
Once the materials are prepared, they are placed into the composite autoclave for curing. The autoclave curing cycle is meticulously controlled and consists of several stages: ramping up temperature, maintaining the desired temperature, and applying pressure for a set amount of time. These conditions are programmed to ensure the resin fully impregnates the fiber layers and undergoes cross-linking, resulting in a hardened structure.
During the curing process, the pressure from the autoclave compacts the layers, driving out excess resin and minimizing void content. This process yields a high-quality, void-free composite part. Depending on the component and resin type, the curing cycle might last anywhere from a few hours to over a day, with specific temperature and pressure profiles tailored to optimize the curing reaction.
Post-Process Quality Control
After curing, the composite component is carefully removed from the autoclave, and post-process quality control is carried out. This quality control may involve ultrasonic inspections, x-rays, or other non-destructive testing methods to verify the integrity of the part. Composite autoclaves contribute significantly to ensuring the component meets strict quality standards and adheres to safety regulations.
Benefits of Using Composite Autoclaves for Manufacturing
There are several benefits to using these vessels in the manufacturing process:
- Superior Mechanical Properties: The application of high pressure and temperature ensures the complete impregnation of fibers, resulting in superior bonding and mechanical performance of the composite material.
- Consistent Quality: Composite autoclaves provide a controlled environment for curing, which means that the parts produced are consistent in terms of quality and performance. This repeatability is crucial in industries like aerospace where safety and reliability are paramount.
- Reduced Voids and Defects: The autoclave process reduces void content and minimizes other types of defects that could lead to weaker materials or failures. By compacting the fibers and resin, the autoclave process results in void-free, highly durable parts.
- Versatility: Composite autoclaves can be used for a wide range of parts and materials, from carbon fiber-reinforced polymers to fiberglass composites, making them versatile tools for various industries.
Advances in Composite Autoclave Technology
Technological advances have also driven improvements in composite autoclave capabilities. Modern autoclaves now feature more sophisticated control systems that enable precise monitoring of temperature, pressure, and vacuum throughout the curing cycle. Digital controls and real-time data logging help maintain optimal conditions, leading to higher efficiency and quality.
Another advancement is the integration of automation in loading and unloading materials, reducing human error and cycle time. Additionally, energy-efficient designs and insulation techniques have made autoclaves more sustainable, aligning with industry efforts to reduce the carbon footprint of manufacturing processes.
The use of computer modeling and simulation has also become commonplace in predicting the behavior of materials under autoclave conditions. This predictive capability helps in optimizing the curing cycle, reducing waste, and ensuring consistent results.
Challenges and Limitations of Composite Autoclave Usage
While composite autoclaves have numerous benefits, there are also some challenges and limitations associated with their usage.
- High Costs: One of the main challenges is the cost. Composite autoclaves are expensive pieces of equipment, and the operation costs are also high due to the energy required to maintain high pressures and temperatures. This has limited the adoption of these processes primarily to industries where high performance justifies the cost, such as aerospace and defense.
- Size Limitations: The size of the autoclave can also be a limiting factor. Manufacturing large composite structures, such as those required for wind turbines or aircraft fuselages, demands oversized autoclaves, which can be logistically challenging and costly to build and maintain. The industry has started to explore out-of-autoclave (OOA) technologies as alternatives to alleviate these size constraints.
- Labor and Expertise Requirements: The autoclave curing process requires specialized knowledge and skilled labor. The setup of vacuum bags, proper layup of prepregs, and management of the autoclave cycle are all labor-intensive tasks that require training and expertise. Automation and improved training programs are helping to overcome some of these challenges, but skilled labor remains a critical requirement.
- Long Cycle Times: Another limitation is the long cycle time. Depending on the component size and complexity, the curing process can take several hours to complete. Long cycle times can reduce overall production rates, which makes it challenging to meet high-volume demands. Some manufacturers are working on optimizing cycle times and exploring rapid-cure resins to address this challenge.
To sum up, composite autoclaves play an essential role in the manufacturing of high-performance composite materials, ensuring superior mechanical properties and consistency. From aerospace to automotive industries, the advantages of using these vessels are clear—void-free, high-strength components that meet rigorous standards.
However, challenges such as high costs, size limitations, and long cycle times remain obstacles to broader adoption. Advances in autoclave technology, such as improved digital controls and automation, are helping to address some of these issues, paving the way for even more efficient manufacturing processes. For now, the composite autoclave remains a crucial technology for producing the highest quality composite parts.