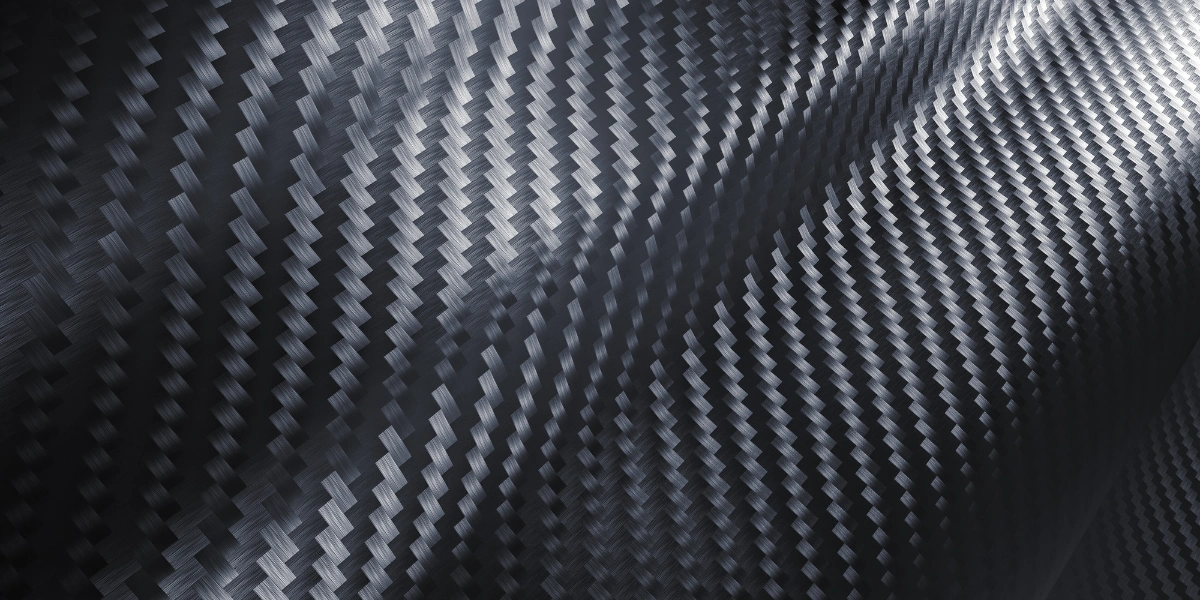
- Blog
- 10 Apr 2025
Carbon Fiber Production Process: A Simple Guide
Carbon fiber has become an essential material in many industries due to its exceptional strength, lightweight nature, and versatility. From aerospace to automotive, sports equipment to construction, carbon fiber is used to create durable and high-performance products. Understanding the carbon fiber production process is key to appreciating why this material stands out over traditional options. In this guide, we will walk through how carbon fiber is made, starting from its raw materials to the finished product, and explore the factors that influence its quality and performance.
What Is Carbon Fiber? Key Properties and Uses
Carbon fiber is a strong, lightweight material made from thin strands of carbon atoms bonded together in a crystalline structure. Known for its high strength-to-weight ratio, carbon fiber is stronger than steel but much lighter, making it ideal for industries like aerospace, automotive, and sports equipment. It also offers excellent stiffness, corrosion resistance, and thermal stability. Products like carbon fiber plates are commonly used in construction and engineering for their durability and lightweight benefits. Additionally, its versatility allows it to be combined with materials like epoxy resin to create composites for even greater strength and flexibility.
Why Carbon Fiber Is Preferred Over Traditional Materials
Carbon fiber is favored over traditional materials like steel and aluminum due to its unique combination of strength, lightness, and durability. Its high strength-to-weight ratio allows for stronger yet lighter structures, improving performance and energy efficiency in industries such as aerospace and automotive. Unlike metals, carbon fiber is corrosion-resistant and has excellent fatigue strength, ensuring long-lasting performance even under stress. Its adaptability, especially when combined with epoxy resin, also makes it ideal for creating complex shapes without compromising strength, giving it an edge over conventional materials in both design and function.
Raw Materials Used in Carbon Fiber Production
The carbon fiber production process starts with specific raw materials known as precursors. The most commonly used precursor is polyacrylonitrile (PAN), which accounts for about 90% of carbon fiber production due to its high carbon content and stability. Other precursors include rayon and petroleum pitch, though they are less common. During production, these materials are transformed into carbon fiber through heat and chemical treatments. To enhance performance, the fibers are often combined with resins like epoxy resin to create strong, lightweight composites used in various applications, including carbon fiber plates for construction and engineering.
Step-by-Step Carbon Fiber Production Process
The carbon fiber production process involves several precise steps that transform raw materials into strong, lightweight carbon fibers. Each stage is crucial to achieving the desired strength, durability, and flexibility that make carbon fiber superior to many traditional materials. Below is a simple guide to the key steps in this process.
Stabilization: Preparing the Fiber for Carbonization
In the stabilization stage, the raw precursor fibers, typically made from polyacrylonitrile (PAN), are heated in air to around 200–300°C. This process alters the molecular structure of the fibers, making them thermally stable and ready for the next stage. Stabilization is essential, as it strengthens the fibers and prepares them for the high temperatures involved in carbonization without melting or breaking down.
Carbonization: Converting Fiber into Carbon Fiber
During carbonization, the stabilized fibers are heated to much higher temperatures, between 1,000°C and 3,000°C, in an inert atmosphere, usually nitrogen, to prevent burning. This step removes non-carbon elements like hydrogen, oxygen, and nitrogen, leaving behind pure carbon atoms arranged in tightly bonded crystals. This crystalline structure is what gives carbon fiber its remarkable strength and lightweight properties, making it ideal for high-performance applications like carbon fiber plates.
Surface Treatment: Enhancing Adhesion Properties
After carbonization, the fiber surfaces are chemically treated to improve their ability to bond with resins, such as epoxy resin. Without this treatment, the smooth carbon fibers would not adhere well to other materials, reducing the strength of the final composite. The surface treatment process involves exposing the fibers to oxidizing gases or liquid baths, which roughen the surface and introduce functional groups that promote strong adhesion.
Sizing: Protecting the Fiber for Further Processing
The final step in the carbon fiber production process is sizing, where the fibers are coated with a protective layer, often made of polymer-based materials. This coating shields the fibers from damage during handling and processing and enhances their compatibility with resins in composite manufacturing. Proper sizing ensures the carbon fibers maintain their integrity and performance in the final product. Additionally, sizing makes it easier to recycle materials in processes like carbon fiber recycling, helping reduce waste and promote sustainability in carbon fiber applications.
Key Factors Affecting Carbon Fiber Quality
Several factors influence the quality of carbon fiber during the carbon fiber production process. The choice of raw materials, especially the purity of the precursor like polyacrylonitrile (PAN), plays a crucial role in determining the final strength and performance of the fibers. Precise control over temperature and atmosphere during stabilization and carbonization is essential to achieving the desired crystalline structure. Additionally, surface treatment and sizing must be carefully managed to ensure strong adhesion with resins like epoxy resin and to protect the fibers during further processing. Any inconsistency in these steps can affect the strength, durability, and overall performance of the carbon fiber, impacting its use in applications such as carbon fiber plates.
The carbon fiber production process is a complex yet carefully controlled procedure that transforms raw materials into one of the strongest and most versatile materials available today. From stabilization and carbonization to surface treatment and sizing, each step ensures the fiber achieves its unique balance of strength, lightness, and durability. High-quality carbon fiber not only outperforms traditional materials but also offers diverse applications across industries, especially when combined with resins like epoxy resin. With growing attention on sustainability, advancements in carbon fiber recycling are making this material even more valuable for the future, supporting eco-friendly practices while maintaining top performance standards.