Vinyl Ester Resins
Vinyl ester is a high-performance resin used in the composite industry, bridging the gap between polyester resin and epoxy resin in terms of mechanical properties and chemical resistance. It is formulated from epoxy resin reinforced with a vinyl group, providing it with superior toughness and resistance to water and chemicals. It is known for its excellent adhesion, durability, and resistance to fatigue, making it an ideal choice for demanding applications that require robust material performance. Its unique chemical structure offers enhanced protection against osmosis and corrosion, making it a preferred resin for marine, automotive, and industrial applications.
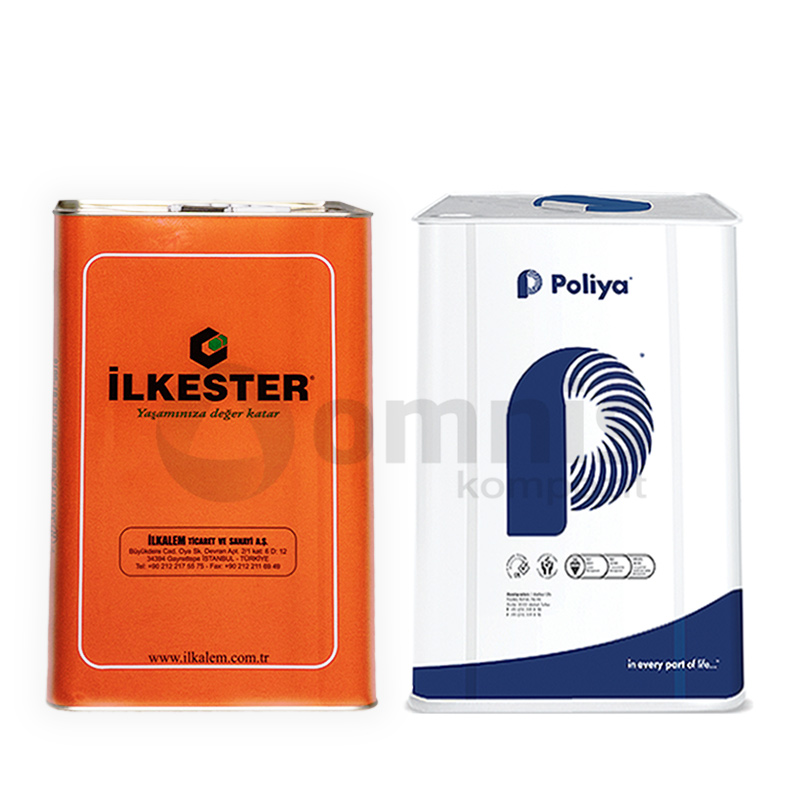
Bisphenol A Epoxy Vinyl Ester Resin
ReviewHow does vinyl ester resin differ from polyester resin?
It differs from polyester resin in several key aspects, including its chemical structure, mechanical properties, and resistance to environmental factors. Vinyl ester is derived from epoxy resin, which gives it superior strength, durability, and chemical resistance compared to polyester resin. It has a lower shrinkage rate during curing, resulting in better dimensional stability and surface finish. Additionally, it offers enhanced resistance to water absorption and osmosis, making it more suitable for marine and corrosive environments. While polyester resin is cost-effective and widely used for general-purpose applications, it is chosen for its higher performance in demanding conditions.
What are the key advantages of using vinyl ester resin in composites?
The key advantages of using vinyl ester resin in composites include its exceptional chemical resistance, superior mechanical properties, and excellent adhesion to reinforcement fibers. It provides composites with high strength and stiffness, making them durable under mechanical stress and impact. Its excellent resistance to water and chemicals, including acids and alkalis, makes it ideal for applications in corrosive environments. Additionally, the product’s low shrinkage rate during curing enhances the dimensional stability and surface finish of composite parts. These properties make it a preferred choice for high-performance applications in marine, automotive, and industrial sectors.
In what applications is vinyl ester resin most commonly used?
Vinyl ester resin is most commonly used in applications that require high strength, durability, and resistance to harsh environmental conditions. Its superior chemical and water resistance make it ideal for marine applications, such as boat hulls, decks, and other components exposed to seawater. It is also used in the manufacturing of tanks and pipes that handle corrosive chemicals, as well as in automotive and aerospace components that demand high performance and reliability. Additionally, its excellent mechanical properties make it suitable for wind turbine blades, sports equipment, and infrastructure projects requiring robust materials.
Can vinyl ester resin be used with both glass and carbon fiber reinforcements?
Yes, vinyl ester resin can be used with both glass and carbon fiber reinforcements, offering excellent adhesion and compatibility with these materials. Its superior mechanical properties and chemical resistance enhance the performance of composites reinforced with glass or carbon fibers, making them stronger, more durable, and resistant to environmental degradation. Vinyl ester resin’s versatility allows it to be effectively utilized in a wide range of applications, from marine and automotive to aerospace and industrial, where the benefits of glass and carbon fiber reinforcements are maximized.
What are the curing characteristics of vinyl ester resin?
The curing characteristics of vinyl ester resin include a relatively fast reaction time and the ability to cure at room temperature, although heat can be applied to accelerate the process and improve the final properties. Vinyl ester resin typically requires the addition of a catalyst or hardener to initiate the curing process. The resin’s low viscosity facilitates good wet-out of the reinforcement fibers, ensuring a uniform composite structure. Proper curing results in a composite with high strength, excellent chemical resistance, and superior durability. The specific curing conditions, such as temperature and time, can be adjusted based on the application requirements and desired properties of the composite.
How does vinyl ester resin perform in corrosive environments?
Vinyl ester resin performs exceptionally well in corrosive environments due to its superior chemical resistance. Its molecular structure, derived from epoxy resin, provides a dense cross-linked network that resists penetration by water, acids, alkalis, and other corrosive substances. This makes vinyl ester resin an ideal choice for applications in marine settings, chemical processing plants, and anywhere else that materials are exposed to harsh chemicals or constant moisture. Its ability to maintain structural integrity and mechanical properties in these conditions ensures the longevity and reliability of composites made with vinyl ester resin.
Can vinyl ester resin be used in high-temperature applications?
Vinyl ester resin can be used in high-temperature applications to a certain extent, as it offers better thermal stability compared to polyester resin, though not as high as epoxy resin. It can withstand continuous exposure to temperatures up to approximately 200°F (93°C) without significant degradation of its mechanical properties. For applications requiring resistance to higher temperatures, modifications to the resin formulation or the use of additives and fillers can improve its thermal performance. However, for extreme high-temperature applications, alternative materials with higher thermal stability may be more appropriate.
What safety precautions should be taken when working with vinyl ester resin?
When working with vinyl ester resin, it is important to take safety precautions to protect against skin irritation, allergic reactions, and inhalation of fumes. Wear protective clothing, gloves, and safety goggles to prevent skin contact. Use a respirator or ensure adequate ventilation in the workspace to avoid inhaling vapors, especially during mixing and curing processes. Always read and follow the manufacturer’s safety data sheets (SDS) for specific handling and safety instructions. Proper hygiene practices, such as washing hands and avoiding eating or drinking in the work area, are also crucial to minimize exposure to the resin.
How do environmental conditions affect the curing of vinyl ester resin?
Environmental conditions, such as temperature and humidity, significantly affect the curing of vinyl ester resin. Optimal curing typically occurs at room temperature, but higher temperatures can accelerate the curing process, while lower temperatures can slow it down or even inhibit complete curing. High humidity levels can also impact the curing process, potentially leading to surface imperfections or affecting the mechanical properties of the cured resin. It is important to control the environmental conditions during the curing process to ensure the desired properties and performance of the vinyl ester resin composite.
What are the storage and handling guidelines for vinyl ester resin?
The storage and handling guidelines for vinyl ester resin include keeping the resin in a cool, dry place away from direct sunlight and sources of heat. The resin should be stored in tightly sealed containers to prevent contamination and moisture absorption. Before use, ensure the resin is at room temperature for optimal handling and curing properties. Properly label and date the containers, and follow the manufacturer’s recommendations for shelf life to ensure the quality of the resin. Always use appropriate personal protective equipment (PPE) when handling vinyl ester resin to avoid exposure to chemicals.
How does the cost of vinyl ester resin compare to other types of resins?
The cost of vinyl ester resin typically falls between that of polyester resin and epoxy resin, reflecting its position as a middle-ground option in terms of performance and chemical resistance. While more expensive than polyester resin, vinylester resin offers superior mechanical properties and durability, making it a cost-effective choice for applications requiring higher performance. Although less expensive than epoxy resin, vinyl ester still provides excellent chemical resistance and strength, offering a balanced solution for many composite applications. The specific cost comparison will depend on the application requirements and the volume of resin used.
What are the limitations of using vinyl ester resin in composite manufacturing?
The limitations of using vinyl ester resin in composite manufacturing include its sensitivity to moisture during the curing process, which can affect the final properties of the composite. While vinyl ester resin offers excellent chemical resistance, it may not perform as well as epoxy resin in extremely harsh chemical environments or under prolonged high-temperature exposure. Additionally, vinyl ester resin can be more expensive than polyester resin, which may limit its use in cost-sensitive applications. Proper handling and storage are necessary to maintain the quality of the resin, and safety precautions must be taken to protect against potential health hazards associated with its use.