RTV2 Silicone
RTV2 silicone, or Room Temperature Vulcanizing 2-component silicone, is a high-performance moulding silicone known for its exceptional flexibility, strength, and detail replication capabilities. This two-component system, consisting of a base and a catalyst, cures at room temperature to form a durable, flexible mold. RTV2 silicone is widely regarded for its ease of use and versatility, making it an ideal choice for a broad range of molding applications. From intricate artistic creations to industrial parts, RTV2 silicone provides reliable and consistent results that professionals and hobbyists alike depend on.
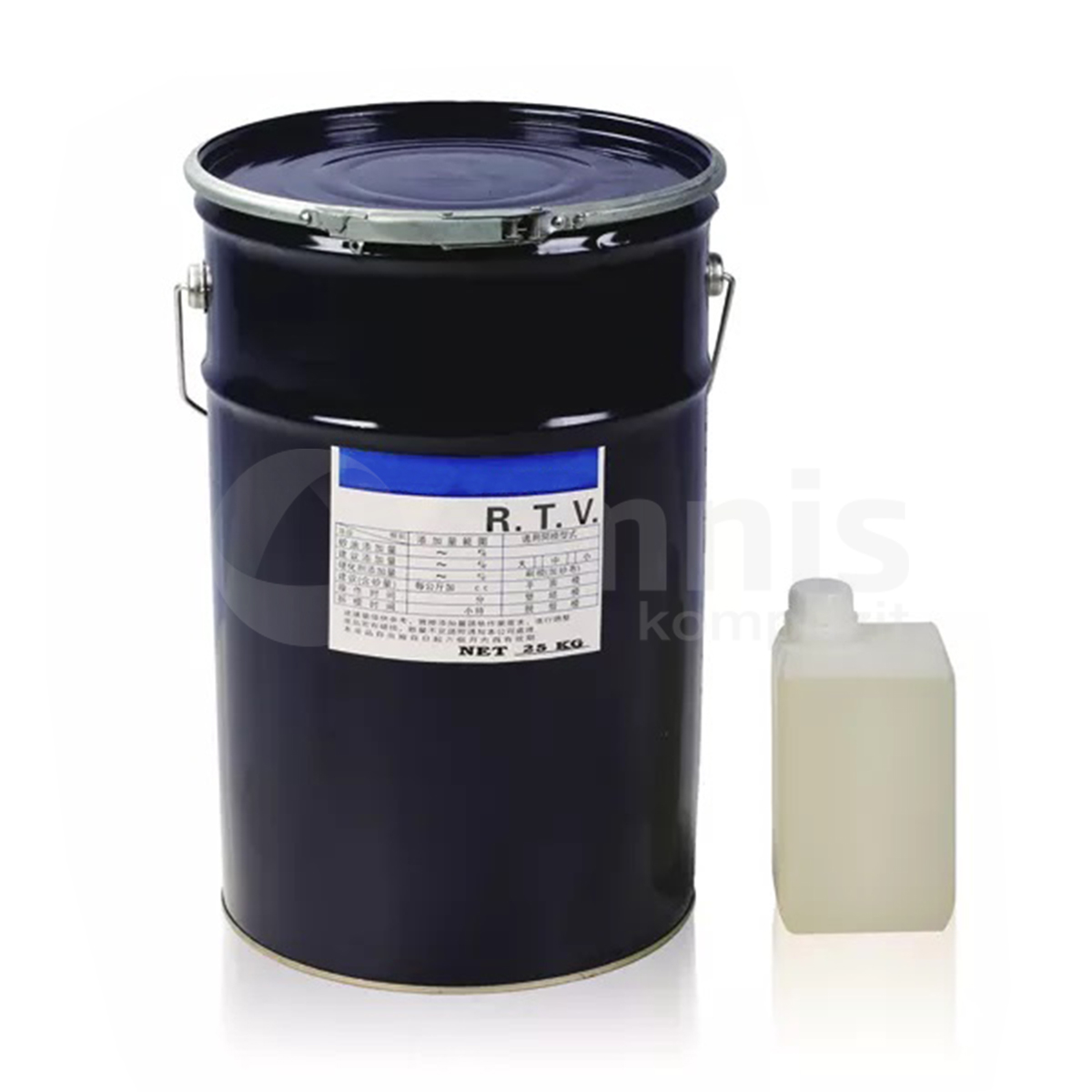
RTV2 Mold Silicone
ReviewHow is RTV2 silicone used in mold making?
RTV2 silicone is extensively used in mold making due to its superior detail capture, flexibility, and ease of use. The process involves mixing the silicone base with the catalyst in precise ratios, then pouring or applying it over the master model. As it cures at room temperature, RTV2 silicone perfectly contours to the shape and details of the model, creating a highly accurate and flexible mold. This moulding silicone is a favorite among artists, engineers, and manufacturers for creating molds of objects for casting a wide variety of materials.
What are the main advantages of using RTV2 silicone for moulding?
The main advantages of using RTV2 silicone for moulding include its excellent detail reproduction, high tear strength, and flexibility. Additionally, RTV2 silicone molds are durable, resistant to chemicals and high temperatures, and can be used with a wide range of casting materials. This moulding silicone is also non-toxic and can be used for food-grade applications, making it incredibly versatile. Whether for complex industrial components or intricate art pieces, RTV2 silicone delivers top-quality results with every use.
Can RTV2 silicone be used with all types of casting materials?
RTV2 silicone is compatible with a wide array of casting materials, including resins, plasters, waxes, and low-melting metals. Its chemical resistance and non-reactive nature make it an ideal choice for producing high-quality casts without compromising detail or causing harm to the mold. However, when working with specific materials, it’s advisable to conduct a compatibility test to ensure the best results and extend the lifespan of the RTV2 silicone mold.
How do I prepare the surface before applying RTV2 silicone?
Proper surface preparation is crucial for achieving the best results with RTV2 silicone. The master model should be clean, dry, and free of any contaminants that could interfere with the silicone’s adhesion or cure. Applying a suitable release agent or sealer may be necessary, especially for porous or delicate surfaces. Ensuring a smooth, prepared surface helps in achieving flawless molds with exceptional detail reproduction using RTV2 moulding silicone.
What are the curing characteristics of RTV2 silicone?
RTV2 silicone cures at room temperature, transforming from a liquid to a solid state through a chemical reaction between the base and the catalyst. This process typically takes from a few hours to overnight, depending on the product formulation and ambient conditions. The cured RTV2 silicone exhibits excellent strength, flexibility, and dimensional stability, making it suitable for creating durable molds that accurately replicate the original model’s details.
Can RTV2 silicone molds be used for food-grade applications?
Yes, certain formulations of RTV2 silicone are designed specifically for food-grade applications. These products meet stringent safety standards, ensuring that molds made from this moulding silicone can safely come into contact with food items. It’s essential to choose a food-grade RTV2 silicone when creating molds for culinary purposes, such as chocolate, candy, or baking molds, to ensure safety and compliance with health regulations.
How do I calculate the amount of RTV2 silicone needed for a mold?
Calculating the amount of RTV2 silicone required for a mold involves measuring the volume of the model and the desired mold thickness. This can be achieved by using a simple calculation or by employing a silicone calculator tool provided by many manufacturers. It’s important to account for any undercuts or complex details that may increase the silicone usage. Accurately estimating the amount ensures that you mix enough RTV2 moulding silicone for your project, avoiding waste and ensuring a successful molding process.
Can RTV2 silicone molds be used for high-temperature applications?
RTV2 silicone molds are capable of withstanding high temperatures, making them suitable for applications such as casting low-melting metals, waxes, and certain types of resins that require heat. However, the maximum temperature that an RTV2 silicone mold can endure varies depending on the specific formulation. Always consult the manufacturer’s guidelines to ensure the silicone meets your project’s temperature requirements
How can I remove air bubbles from RTV2 silicone before it cures?
Removing air bubbles from RTV2 (Room Temperature Vulcanizing, 2-component) silicone before it cures is crucial for ensuring a flawless, high-quality finish in molds or castings. Here are several effective methods to remove air bubbles:
1. Degassing with a Vacuum Chamber
- Procedure: After mixing the silicone components, place the mixture in a vacuum chamber and apply a vacuum. The reduced pressure in the chamber causes the air bubbles to expand and rise to the surface, where they burst. This process can significantly reduce or eliminate air bubbles.
- Considerations: Vacuum degassing equipment can be an investment, but it’s highly effective, especially for professional or high-precision applications.
2. Pressure Casting
- Procedure: Pour the mixed silicone into the mold and then place the mold in a pressure pot, where it is subjected to high pressure. The increased pressure compresses the air bubbles to a size that is too small to affect the quality of the silicone cast.
- Considerations: Like vacuum degassing, pressure casting requires specific equipment. It’s suitable for applications where bubble-free results are critical.
3. Pouring Technique
- Procedure: Pour the silicone in a thin, steady stream from a height. This method allows many of the bubbles to pop as the silicone flows into the mold. Pouring into the lowest part of the mold and letting the silicone slowly fill up can also help minimize air entrapment.
- Considerations: This method is more accessible as it doesn’t require special equipment, but it may not remove all bubbles, especially those deep within the mixture.
4. Using a Vibrating Table
- Procedure: Place the mold on a vibrating table after pouring the silicone. The vibrations help bring bubbles to the surface, where they can burst.
- Considerations: This method can be combined with careful pouring techniques for improved bubble removal without specialized degassing equipment.
5. Manual Techniques
- Procedure: For small projects, using a toothpick or a fine needle to pop surface bubbles or gently tapping the sides of the mold can help remove some air bubbles.
- Considerations: These techniques are more labor-intensive and less effective for removing bubbles from within the silicone but can be useful for surface bubbles.
6. Proper Mixing Techniques
- Procedure: Mix the components slowly and thoroughly to avoid introducing excess air into the mixture. Some recommend using a folding motion rather than a stirring one to minimize air entrapment.
- Considerations: This method focuses on preventing the problem rather than fixing it but is crucial for reducing the number of bubbles formed during mixing.
Each of these methods has its own set of advantages and considerations, and the choice of method can depend on the specific requirements of the project, including the size of the cast, the level of detail needed, and the equipment available.
What is the lifespan of an RTV2 silicone mold?
The lifespan of an RTV2 (Room Temperature Vulcanizing, 2-component) silicone mold can vary significantly based on several factors, including the type of silicone used, the complexity of the mold, the materials cast into the mold, and how the mold is used and maintained. However, a general estimate for the lifespan of an RTV2 silicone mold ranges from 20 to 100 or more castings. Here’s a breakdown of the factors that can influence a silicone mold’s lifespan:
1. Type of Silicone
The hardness (measured in Shore A) and the quality of the silicone material can affect its durability. Harder silicones may resist wear better with stiff or abrasive casting materials, but they might also be more prone to cracking with repeated flexing. High-quality silicones are more resistant to chemical degradation and physical wear.
2. Casting Material
The type of material being cast (e.g., concrete, plaster, resin, wax) can affect the mold’s lifespan. Abrasive materials or those that can chemically interact with silicone will wear out the mold faster. Epoxy and polyurethane resins, for example, can be harsher on molds than less reactive materials like wax or soap.
3. Mold Design
Molds with intricate details or significant undercuts may experience more stress during the demolding process, leading to wear and potential tearing over time.
4. Use and Care
Using a mold release agent can extend the life of a silicone mold by reducing wear during the demolding process.
Proper cleaning and storage of the mold are crucial. Molds should be cleaned gently and stored in a cool, dry place out of direct sunlight to prevent degradation of the silicone.
5. Frequency of Use
Giving the mold time to rest between castings can help prolong its life. Continuous, back-to-back use can accelerate wear and tear.
6. Environmental Factors
Extreme temperatures and high humidity can affect the chemical structure of silicone over time, potentially reducing the lifespan of the mold.
Despite these variables, RTV2 silicone molds are favored for their flexibility, non-stick properties, and fine detail reproduction. To maximize the lifespan of a silicone mold, it’s essential to consider the factors above and follow best practices for mold use, cleaning, and storage.
How do I clean and maintain RTV2 silicone molds?
Cleaning and maintaining RTV2 (Room Temperature Vulcanizing, 2-component) silicone molds is crucial for extending their lifespan and ensuring the quality of the castings. Proper care involves gentle cleaning to remove residues and correct storage to prevent deformation or damage. Here are the steps and tips for cleaning and maintaining RTV2 silicone molds:
Cleaning Process
- Remove Residue Immediately: After demolding, remove any residual casting material from the mold as soon as possible. Silicone is non-stick, so most materials should come out easily.
- Use Mild Soap and Water: For most residues, washing with mild soap and warm water is sufficient. Use a soft, non-abrasive sponge or cloth to gently clean the mold. Avoid harsh chemicals or abrasive tools that can damage the silicone surface.
- Rinse Thoroughly: After washing, rinse the mold thoroughly with water to remove all soap residues, which could interfere with future castings.
- Dry Completely: Let the mold air dry completely before storing or using it again. Water left in the mold could affect the curing process of some casting materials or promote mold growth.
- Spot Cleaning: For stubborn residues, a soft toothbrush can be used to gently scrub the affected areas. Be very careful not to tear or damage intricate parts of the mold.
- Removing Grease or Oily Residues: If the cast material leaves behind grease or oil, a mild solvent like isopropyl alcohol can be used sparingly on a soft cloth to wipe the mold. Test the solvent on a small, inconspicuous area of the mold first to ensure it does not damage the silicone.
Maintenance and Storage
- Apply a Mold Release Agent: Before each use, applying a thin layer of mold release agent can help extend the mold’s life by reducing wear during the demolding process.
- Avoid Sharp Objects: Never use sharp or metal tools to demold or clean the mold, as these can cut or puncture the silicone.
- Store Properly: Store silicone molds in a cool, dry place away from direct sunlight. UV light can degrade silicone over time.
- Flat Surface Storage: Whenever possible, store molds on a flat surface or in a way that supports their entire structure to avoid distortion.
- Avoid Heavy Objects: Do not place heavy objects on top of silicone molds in storage, as this can cause permanent deformation.
- Regular Inspection: Periodically check your molds for signs of wear, tear, or degradation. Early detection of issues can help prevent poor-quality castings.
By following these cleaning and maintenance steps, you can ensure your RTV2 silicone molds remain in good condition, producing high-quality castings for as long as possible.
Can RTV2 silicone be colored or pigmented?
Yes, RTV2 (Room Temperature Vulcanizing, 2-component) silicone can be colored or pigmented. Adding color to silicone molds or castings allows for greater creativity and can be useful for prototyping, artistic projects, or functional parts where color differentiation is important. Here’s how you can add color to RTV2 silicone:
1. Silicone-Specific Pigments
The most reliable way to color RTV2 silicone is by using silicone-specific pigments. These pigments are designed to mix thoroughly with silicone without affecting its curing process or physical properties. They are available in a wide range of colors and can be mixed to create custom shades.
2. Adding Pigment
- Proportion: Add the pigment to one part of the silicone (usually part A) before combining it with the other part (part B). The amount of pigment needed is generally small; often, just a few percent of the total volume is sufficient to achieve a strong color. It’s important to follow the pigment manufacturer’s recommendations to avoid affecting the silicone’s curing and physical properties.
- Mixing: Thoroughly mix the pigment with part A to ensure an even color distribution before adding part B. Once part B is added, mix the components thoroughly again to ensure the color is uniform throughout the silicone.
3. Considerations for Coloring Silicone
- Test Before Use: Always conduct a small test mix to check the compatibility of the pigment with the silicone and to verify the final color. This is especially important for critical projects where exact color matching is necessary.
- Impact on Properties: Adding too much pigment can affect the silicone’s properties, potentially altering its curing time, strength, or elasticity. Keep pigment additions within the manufacturer’s recommended limits.
- Compatibility: Ensure the pigment is compatible with the specific type of RTV2 silicone you’re using. Some silicones may have specific requirements or limitations when it comes to coloring.
4. Alternatives to Pigments
- Powders and Glitters: For special effects, metallic powders or glitters can be mixed into the silicone. These should be used sparingly and mixed thoroughly to ensure even distribution and to avoid affecting the silicone’s curing process.
- Surface Coloring: If changing the entire mass of silicone isn’t necessary, consider painting the cured silicone surface with silicone-compatible paints or dyes for localized color.
Coloring RTV2 silicone expands its application possibilities but requires attention to detail and proper mixing techniques to ensure the desired outcome without compromising the material’s performance.