PVC Foam Plates
PVC foam stands as a versatile and innovative core material widely utilized in the composite industry for its exceptional balance of strength, durability, and lightweight properties. Comprising polyvinyl chloride, this foam exhibits a closed-cell structure that endows it with excellent dimensional stability and resistance to moisture and chemicals. Its adaptability and performance benefits make PVC foam a preferred choice for a broad array of applications, from marine and automotive to construction and aerospace, providing an optimal solution for manufacturers seeking to enhance the quality and efficiency of their composite structures.
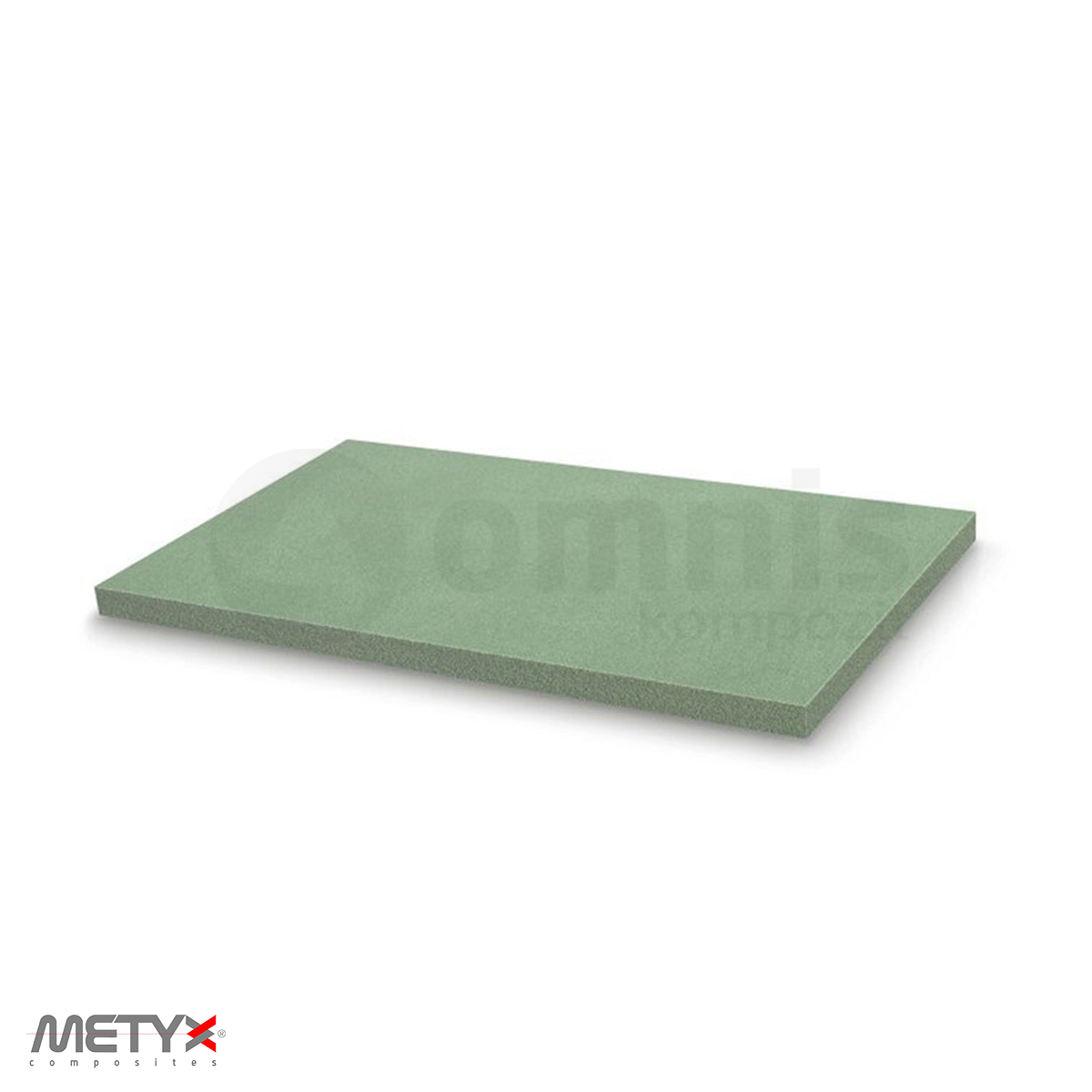
PVC Foam Plate
ReviewHow is PVC foam manufactured?
It is manufactured through a process that involves the expansion of polyvinyl chloride (PVC) mixed with a blowing agent and other additives under controlled conditions. This process results in a closed-cell foam that provides a uniform density and consistent properties throughout the material. The manufacturing technique can be tailored to produce PVC foam with varying densities and mechanical properties, allowing it to meet the specific requirements of different applications. The precise control over the foam’s structure and composition during manufacturing ensures its high quality and performance in composite structures.
What are the main advantages of using PVC foam in composite structures?
It offers several advantages when used in composite structures, notably its high strength-to-weight ratio, excellent thermal insulation, and superior resistance to moisture, chemicals, and impact. These properties make PVC foam an ideal core material for applications demanding durability and lightweight performance. Its closed-cell structure ensures minimal water absorption, enhancing the longevity and integrity of composite parts. Additionally, PVC foam provides excellent adhesive bonding characteristics, facilitating the creation of robust and reliable composite assemblies. Its versatility and efficiency in improving mechanical properties while reducing weight contribute significantly to its widespread use in various industries.
How does PVC foam compare to other core materials like balsa or honeycomb?
Compared to other core materials such as balsa wood and honeycomb structures, PVC foam offers a unique combination of properties. Unlike balsa, foam is inherently resistant to moisture and decay, providing a more durable and maintenance-free solution for composite structures. Compared to honeycomb cores, foam delivers a more uniform density and smoother surface, which can be advantageous in applications requiring a high-quality finish or extensive machining. While honeycomb cores may offer superior strength-to-weight ratios for specific applications, foam’s ease of handling, shaping, and its excellent adhesive properties make it a versatile and user-friendly option for a wide range of applications.
In what applications is PVC foam most commonly used?
PVC foam is most commonly used in applications that demand high strength, durability, and resistance to environmental factors. Its widespread use encompasses the marine industry for boat hulls and decks, the aerospace sector for lightweight panels, the wind energy industry for turbine blades, and the transportation sector for automotive body parts. Additionally, PVC foam finds applications in construction for insulation panels and architectural elements, as well as in sporting goods for high-performance equipment. Its adaptability and performance benefits make it a favored material across diverse industries seeking to leverage its superior mechanical properties and lightweight nature.
Can PVC foam be used in marine applications?
Absolutely, PVC foam is particularly well-suited for marine applications due to its exceptional resistance to water, moisture, and saltwater environments. Its closed-cell structure prevents water absorption, ensuring the integrity and buoyancy of marine structures such as boat hulls, decks, and bulkheads. PVC foam contributes to the durability and longevity of marine composites by providing a stable and lightweight core material that withstands harsh marine conditions, making it an ideal choice for the construction and refurbishment of various types of watercraft.
How does PVC foam contribute to the strength and stiffness of composites?
PVC foam significantly contributes to the strength and stiffness of composite structures through its dense, closed-cell composition, which offers excellent compression and shear properties. When used as a core material, PVC foam acts to distribute loads and stresses evenly across the composite part, enhancing its overall structural integrity. This property allows for the design of lighter, yet stronger and stiffer composite components capable of withstanding substantial forces and impacts. The incorporation of PVC foam into composite designs results in enhanced performance characteristics without compromising on weight, making it a critical component in the engineering of advanced materials.
Is PVC foam resistant to water and moisture?
Yes, PVC foam is highly resistant to water and moisture, thanks to its closed-cell structure that prevents the ingress of water. This characteristic makes it an excellent choice for applications where moisture resistance is crucial, such as in marine, outdoor, and construction environments. The ability of PVC foam to maintain its properties and integrity in damp conditions contributes to the durability and longevity of composite structures, protecting them against degradation and ensuring consistent performance over time.
Can PVC foam be painted or coated?
PVC foam can indeed be painted or coated to enhance its appearance or to add additional protective layers against environmental exposure. Before painting or coating, the surface of should be properly prepared to ensure good adhesion. This might include light sanding and cleaning to remove any dust or contaminants. It’s essential to use paints and coatings compatible with PVC to prevent any adverse reactions. Testing a small area first is recommended to verify the compatibility and desired outcome of the finish.
How do you cut and shape PVC foam for specific applications?
Cutting and shaping PVC foam for specific applications can be achieved using a variety of tools, including hand saws, circular saws, and CNC milling machines, depending on the precision and complexity required. The material’s ease of machining allows for the creation of intricate designs and precise fittings with minimal effort. When cutting or shaping PVC foam, it’s important to use sharp blades to ensure clean cuts and to take appropriate safety precautions, such as wearing protective eyewear and ensuring adequate ventilation to avoid inhaling any dust.
What types of adhesives are compatible with PVC foam?
PVC foam is compatible with a wide range of adhesives, including epoxy, polyurethane, and cyanoacrylate adhesives. The choice of adhesive depends on the specific requirements of the application, such as the need for flexibility, strength, or resistance to environmental conditions. For optimal bonding performance, it’s crucial to select adhesives specifically formulated for use with PVC materials and to follow the manufacturer’s recommendations for surface preparation and application. Compatibility testing is also advisable to ensure that the selected adhesive provides a strong and durable bond.
How does the density of PVC foam affect its performance characteristics?
The density plays a significant role in determining its performance characteristics, including strength, stiffness, and impact resistance. Higher-density PVC foam typically offers greater mechanical properties, making it suitable for applications requiring enhanced structural support and durability. However, increased density also results in a heavier material, which may impact the overall weight of the composite structure. Balancing the density with the specific performance requirements of the application is crucial for achieving the desired balance between strength, stiffness, and weight efficiency.