Peel Ply
It is a critical textile used in the composite manufacturing industry, designed to facilitate the production of high-quality composite parts. Acting as a sacrificial layer applied directly onto the surface of a composite layup, it is made from nylon or polyester fabrics that are heat-resistant and compatible with various resin systems. Its primary function is to create a textured surface on the composite part upon removal after the curing process. This surface preparation enhances bonding characteristics for subsequent processes or coatings, making it an indispensable tool for manufacturers seeking precision and reliability in their composite productions.
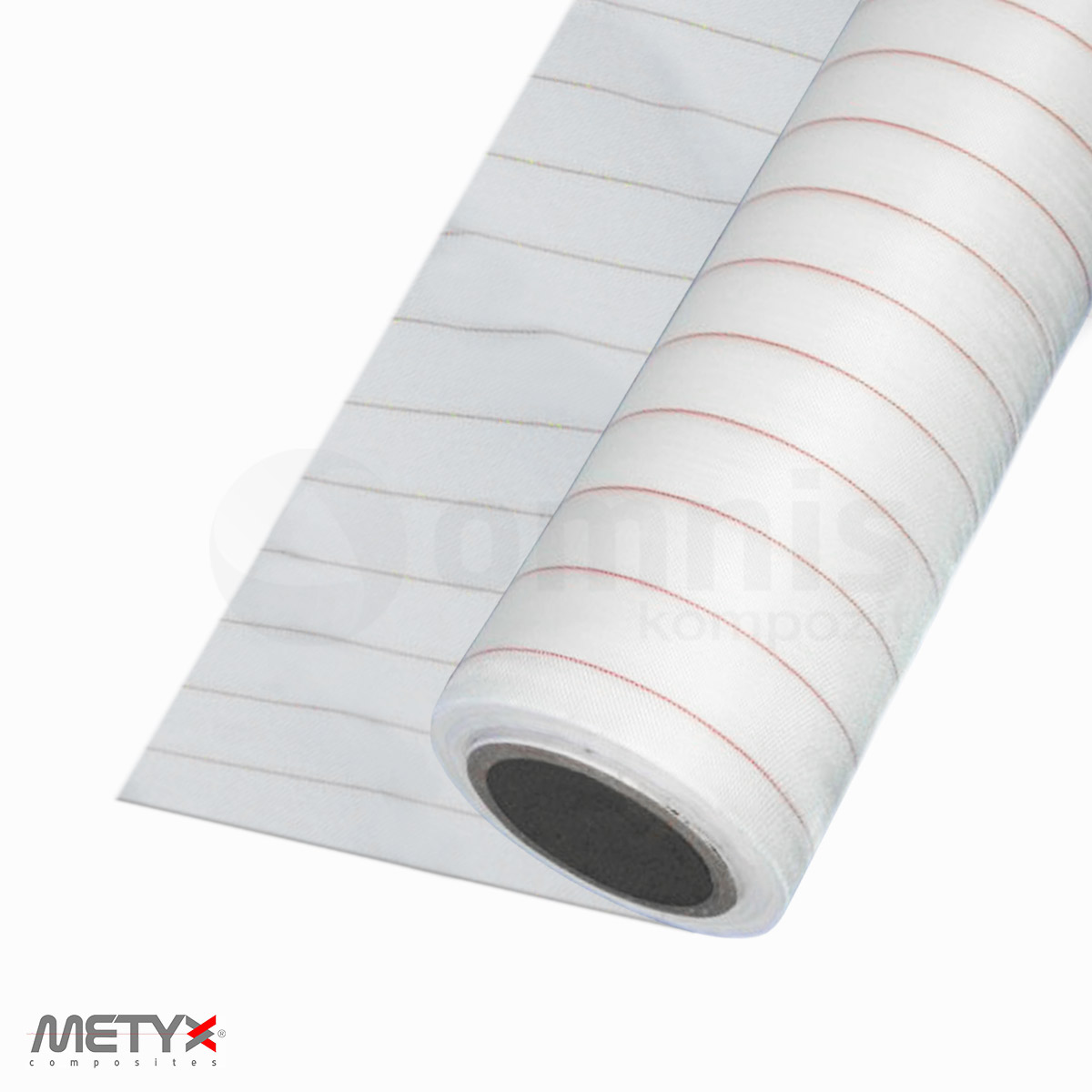
Peeling Fabric
ReviewHow does peel ply work in the composite manufacturing process?
It plays a pivotal role in the composite manufacturing process by serving as a barrier between the laminate and the air or vacuum bag. When a composite layup cures, the peel ply, which is laid directly onto the resin surface, embeds into the uncured resin. Upon curing, it can be peeled off, revealing a clean, textured surface that is ideal for secondary bonding or painting. This method significantly reduces the need for manual surface preparation, such as sanding or grinding, thereby streamlining the manufacturing process and ensuring a consistent, high-quality finish on the composite part.
What are the main benefits of using peel ply in composites?
The use in composites offers several key benefits, including improved adhesion for secondary bonding operations, reduced prep time for finishing processes, and a consistent, high-quality surface finish. The product eliminates contaminants such as release agents or amine blush from the composite surface, ensuring optimal conditions for adhesion. Furthermore, by negating the need for extensive manual surface preparation, it not only enhances the efficiency of the manufacturing process but also significantly reduces labor costs and the potential for human error, resulting in a more uniform and reliable product.
Can peel ply be used with all types of resin systems?
It is remarkably versatile and compatible with a wide variety of resin systems, including epoxy, polyester, and vinylester resins commonly used in composite manufacturing. Its material composition is specifically designed to interact effectively with these resins, ensuring that it can be easily removed after curing without leaving residues. However, it’s crucial to select the appropriate type for the specific resin system used, as different resins may require different types of peel ply for optimal performance and ease of removal.
How do I choose the right peel ply for my application?
Choosing the right product for your application involves considering several factors, including the type of resin system used, the desired surface finish, and the requirements for subsequent processing or bonding. The weave pattern, fabric weight, and material of the peel ply can all affect the final surface texture and compatibility with the resin system. For applications requiring high levels of adhesion for secondary processing, a type that leaves a rougher surface may be preferred. Consulting with material suppliers and reviewing technical specifications can help in selecting the most suitable peel ply for your specific needs.
How does peel ply affect the surface finish of a composite part?
Peel ply significantly influences the surface finish of a composite part by creating a uniform, textured surface ideal for secondary bonding or finishing. The texture and porosity of the product determine the roughness of the surface it leaves behind, which can be tailored to specific requirements. This controlled surface preparation enhances mechanical bonding properties and reduces the need for additional surface treatments, such as sanding or grit blasting, leading to a more efficient manufacturing process and a higher quality end product.
Can peel ply be used in vacuum bagging and resin infusion processes?
Yes, it is highly effective in both vacuum bagging and resin infusion processes. In vacuum bagging, it is placed directly on the composite layup under the vacuum bag to facilitate air removal and control resin content. In resin infusion, peel ply can be used as a barrier to ensure resin flows evenly across the layup, preventing dry spots and ensuring a high-quality finish. Its versatility and compatibility with these processes make peel ply an invaluable asset in achieving precise control over resin distribution and surface preparation in composite manufacturing.
What are the differences between peel ply and release films?
Peel ply and release films serve different purposes in composite manufacturing. While peel ply is designed to be removed after curing, leaving a textured surface that is ready for further processing, release films are used to prevent the composite part from adhering to the mold or bagging materials. Release films are typically smooth and non-porous, providing a barrier that facilitates easy part release without imparting texture to the surface of the composite. In contrast, peel ply is specifically used when a textured, bondable surface is desired.
How do you properly apply peel ply to a composite layup?
Applying peel ply to a composite layup requires careful attention to ensure it is smooth and wrinkle-free, covering the entire area where a textured surface or future bonding is desired. Start by cutting the product to the desired shape and size, slightly larger than the layup area. Lay the peel ply directly onto the wet laminate or prepreg material, ensuring full contact with the surface. Use a roller or squeegee to smooth out any wrinkles or air bubbles, ensuring the peel ply is fully adhered to the resin surface. Proper application ensures optimal surface preparation and ease of peel ply removal after curing.
Are there different types of peel ply for specific applications?
Yes, there are various types of it available, designed to meet the specific requirements of different composite manufacturing applications. Differences in types can include the fabric material (e.g., nylon, polyester), weave pattern, and weight, which can all influence the surface texture and compatibility with certain resin systems. Some peel plies are also treated with release agents to facilitate easier removal, while others are designed for high-temperature applications. Selecting the right type is crucial for achieving the desired surface finish and performance in the final composite part.
Can peel ply withstand high-temperature curing cycles?
High-temperature peel ply variants are specifically designed to withstand the elevated temperatures associated with certain curing cycles, such as those used in prepreg processing or autoclave curing. These peel plies are made from materials that can resist degradation at high temperatures, ensuring they maintain their integrity and can be successfully removed after the curing process. When working with high-temperature curing cycles, it is important to choose a peel ply that is rated for the specific temperature range of the process to ensure optimal performance and ease of removal.