Machinery
Composite machines are specialized pieces of equipment designed to fabricate materials by combining two or more distinct substances, often fibers and resins, to leverage their unique properties in the final product. These machines are critical in producing composite materials, which are known for their superior strength-to-weight ratios, durability, and resistance to environmental conditions. The technology behind composite machines varies widely, accommodating different composite manufacturing processes such as lay-up, filament winding, pultrusion, and resin transfer molding. Each process and machine is tailored to the specific requirements of the composite material being produced, making composite machines integral to industries such as aerospace, automotive, construction, and sports equipment manufacturing.
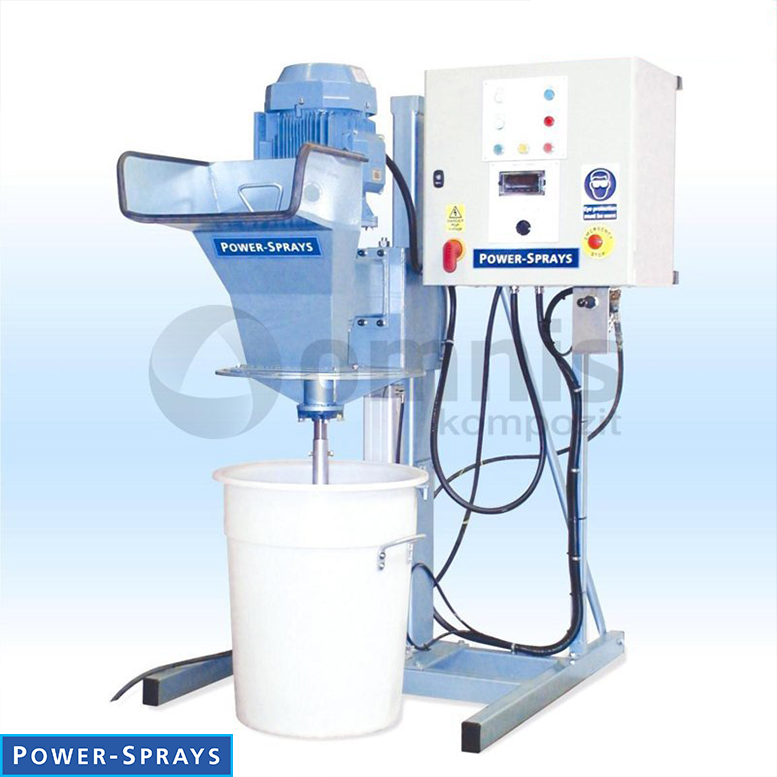
Power Sprays GRC 125
Review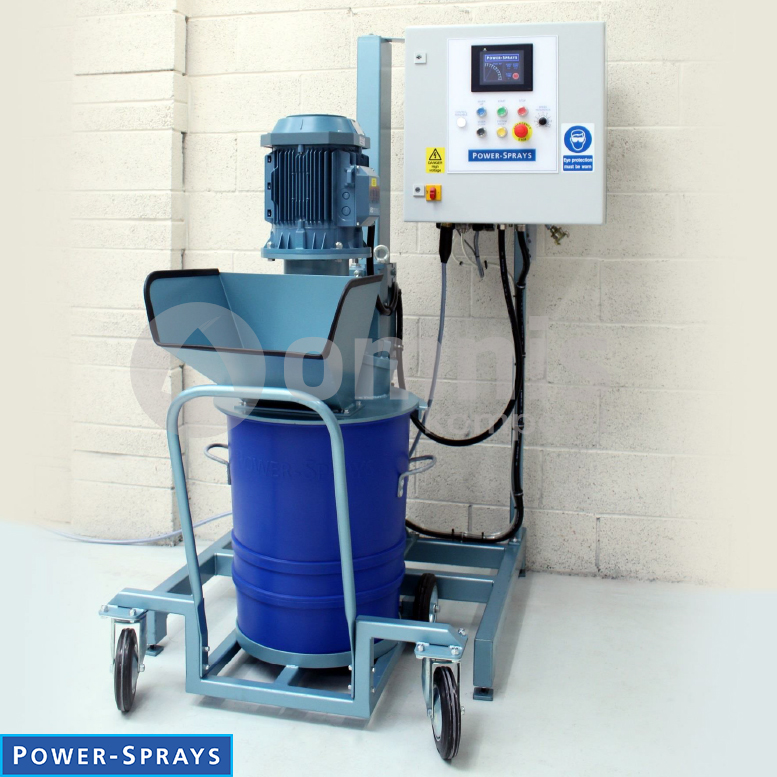
Power Sprays GRC 125 BT
Review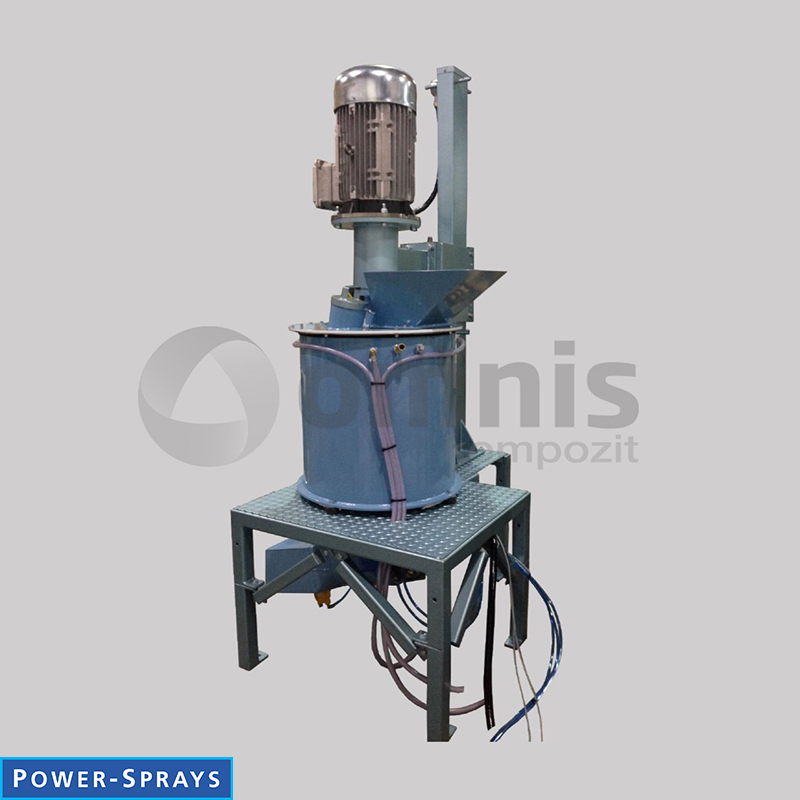
GRC250S Combination Mixer
Review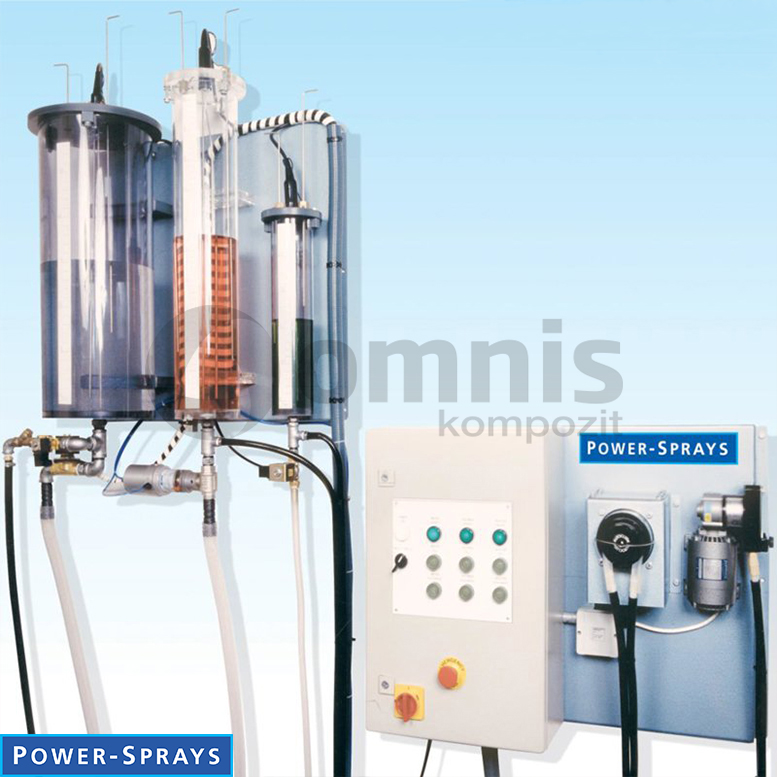
Power Sprays 3 Liquid Material Dosing Systems
Review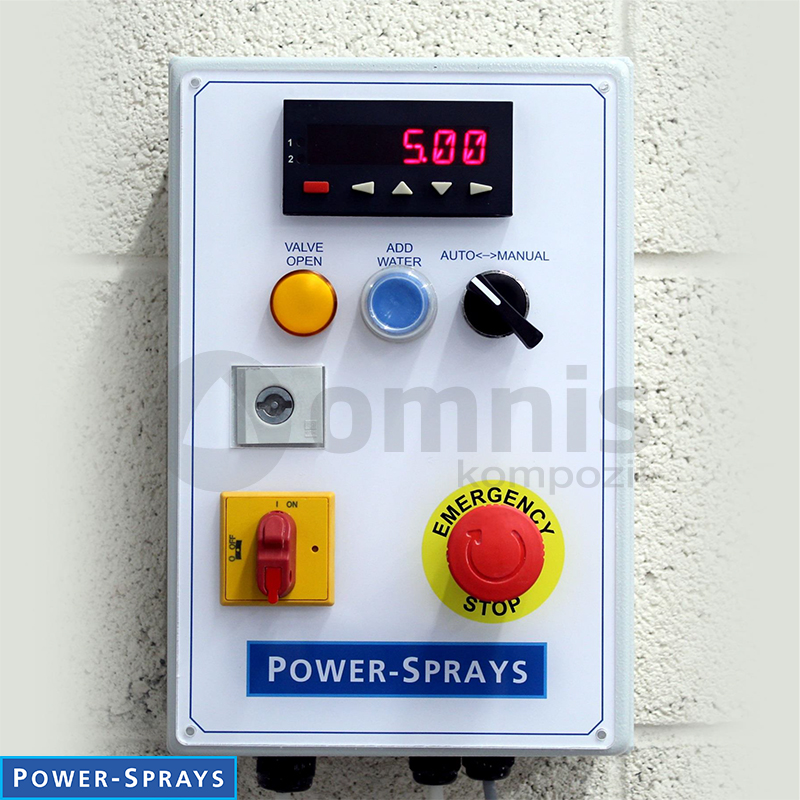
Digital Water Meter
Review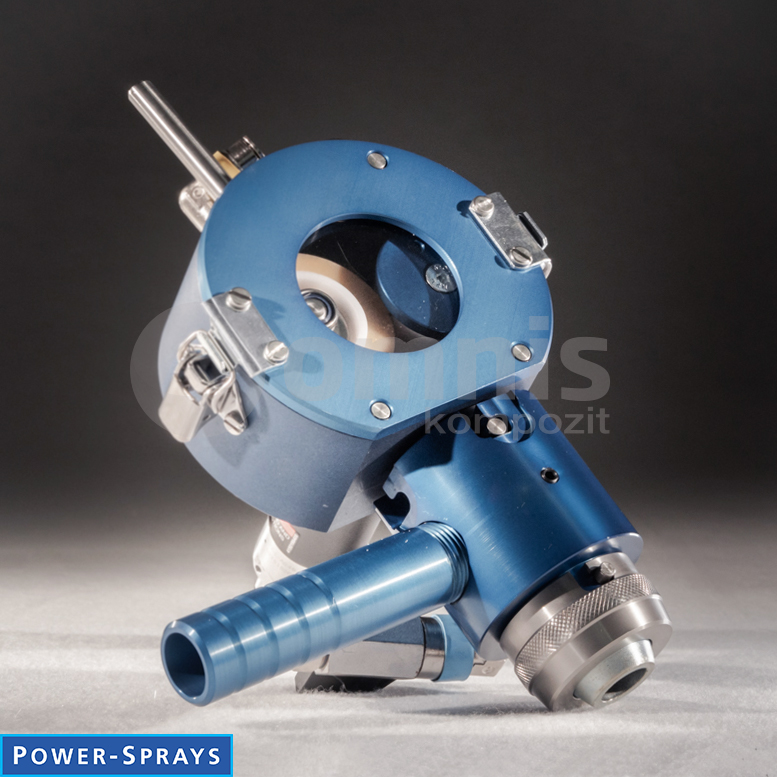
Power Sprays Spray Guns
Review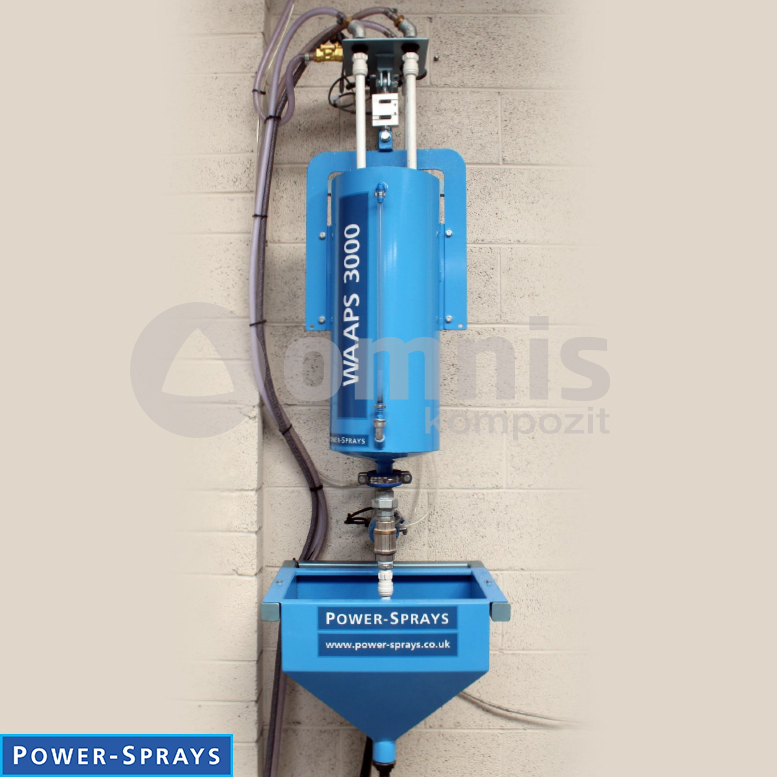
WAAPS 3000 Liquid Material Dosing Systems
Review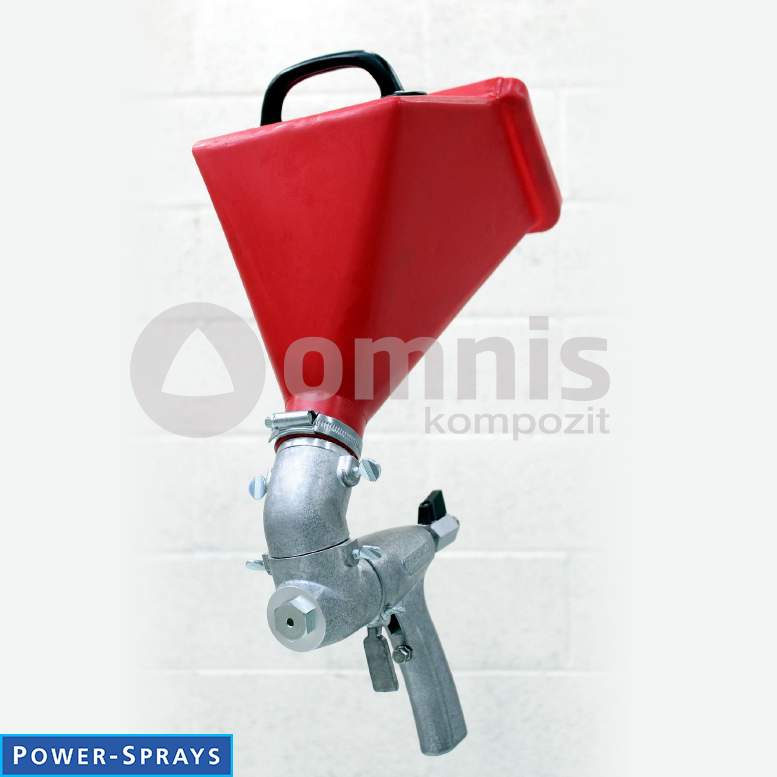
Power Sprays MK3
Review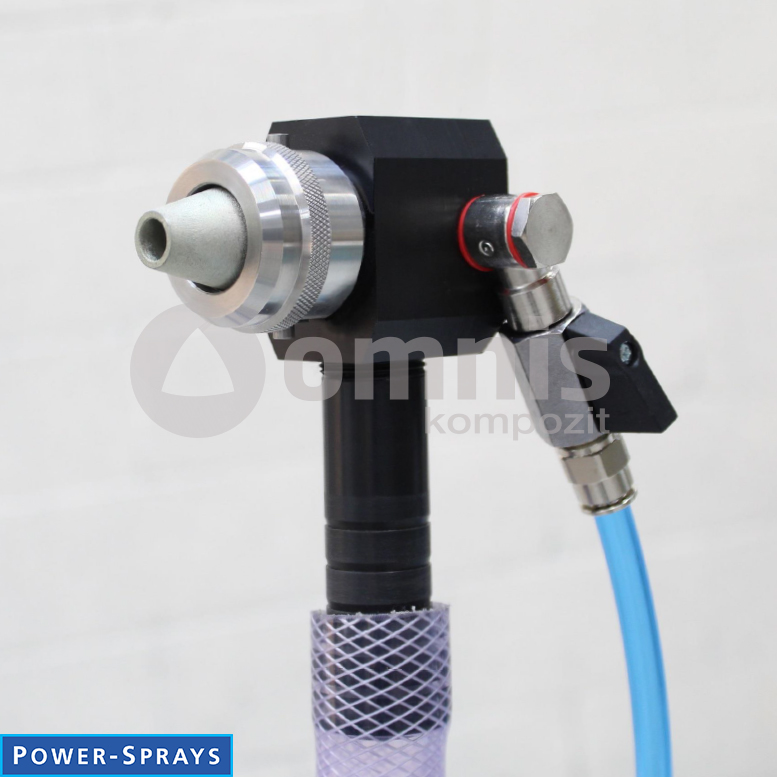
Power Sprays Light Mist Gun
Review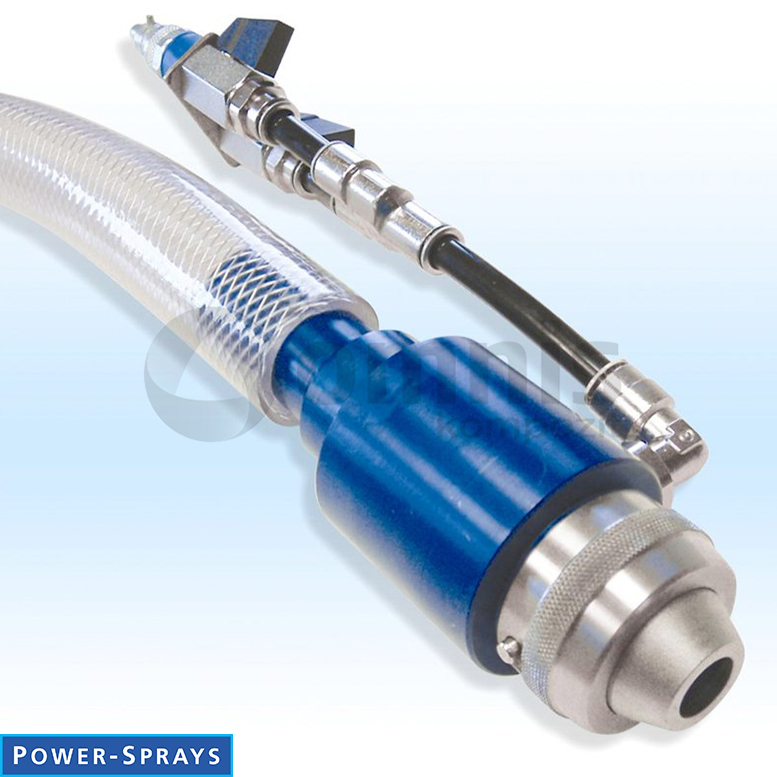
Power Sprays MK5A
Review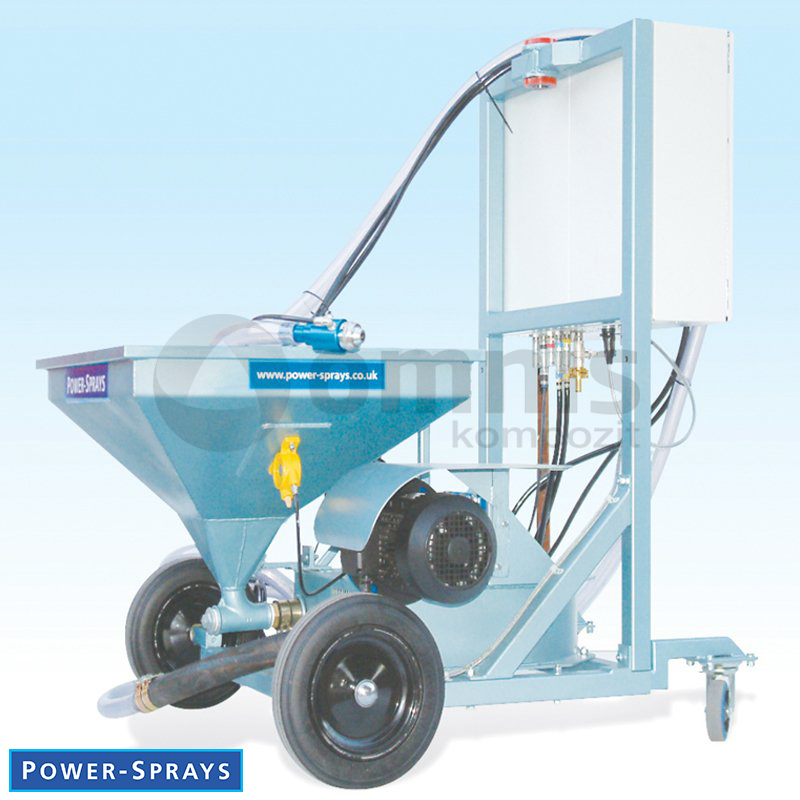
Power Sprays PS 38B
Review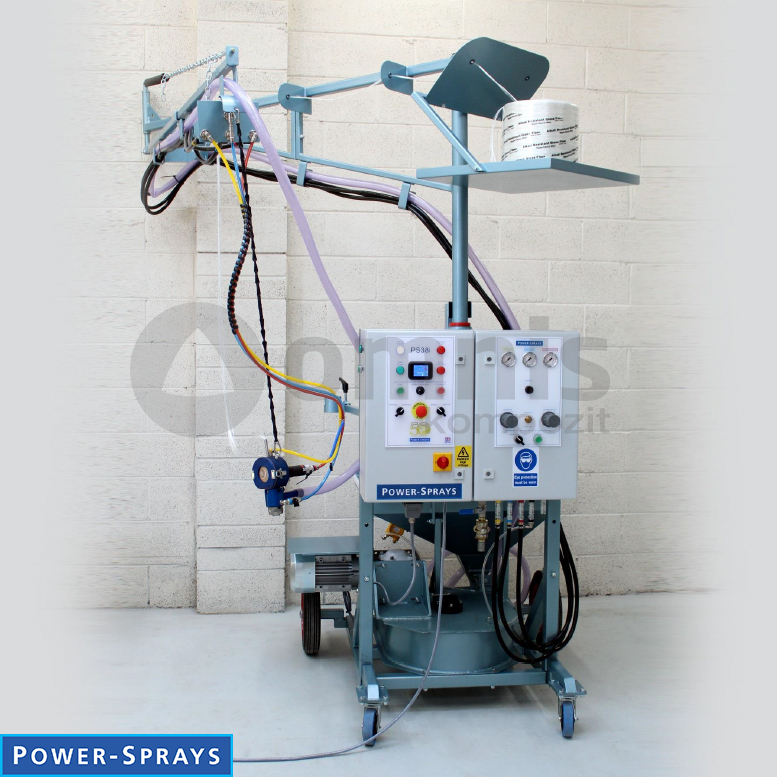
Power Sprays PS 38i
Review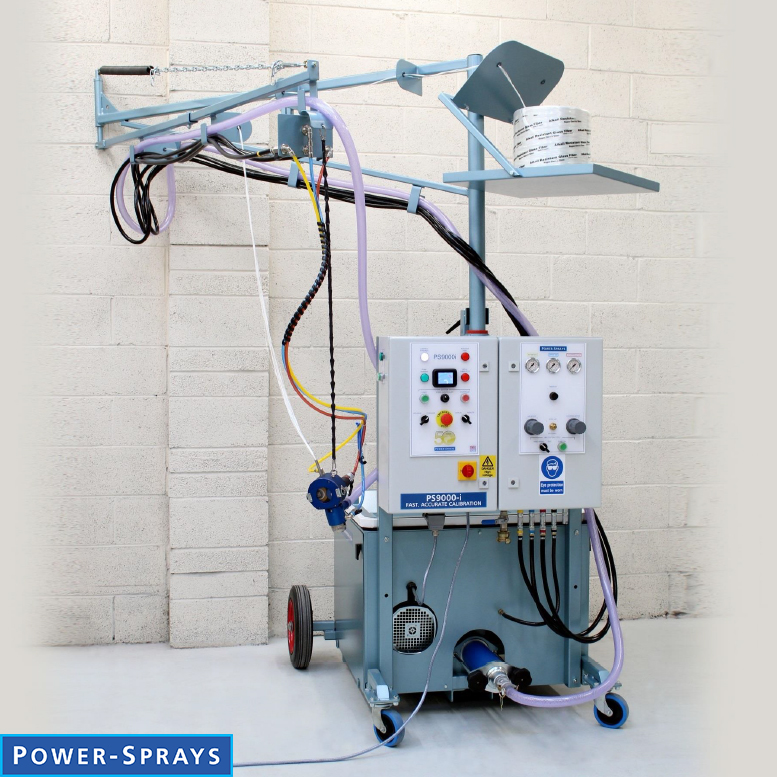
Power Sprays PS 9000i
Review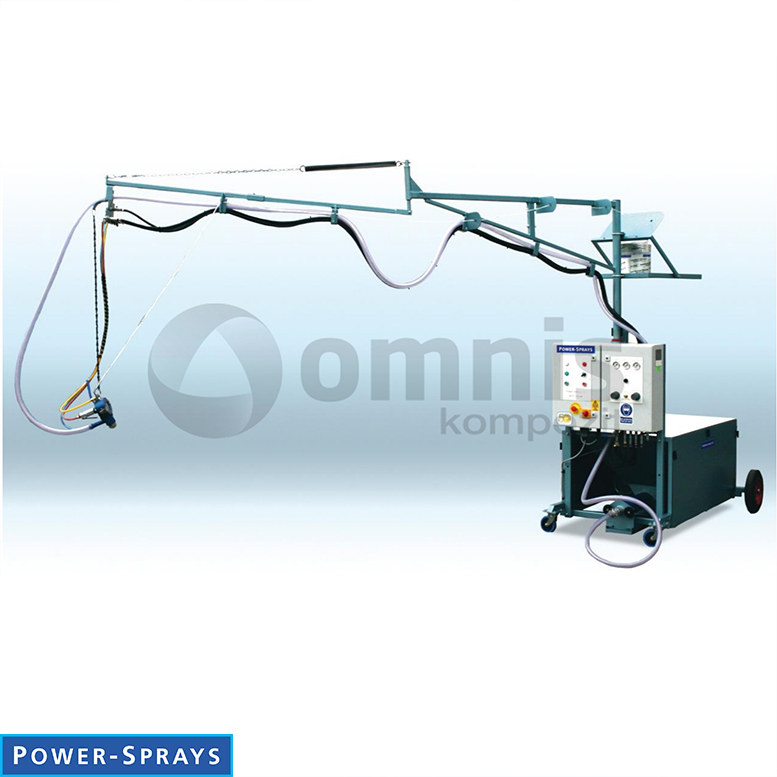
Power Sprays PS 10000i
Review
Composite Sheet Production
Review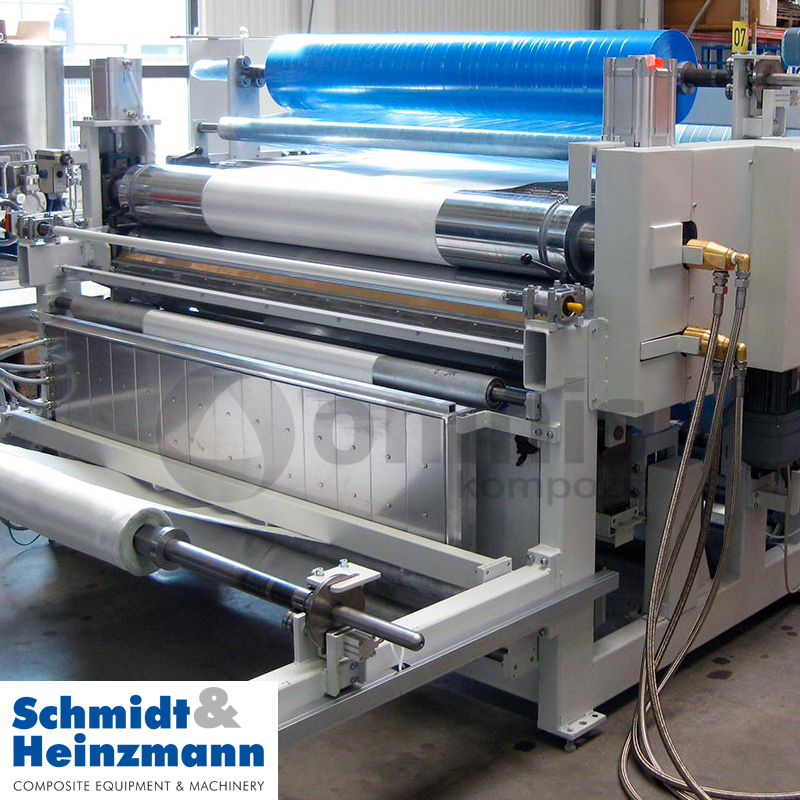
Thermosetting Prepreg Machines
Review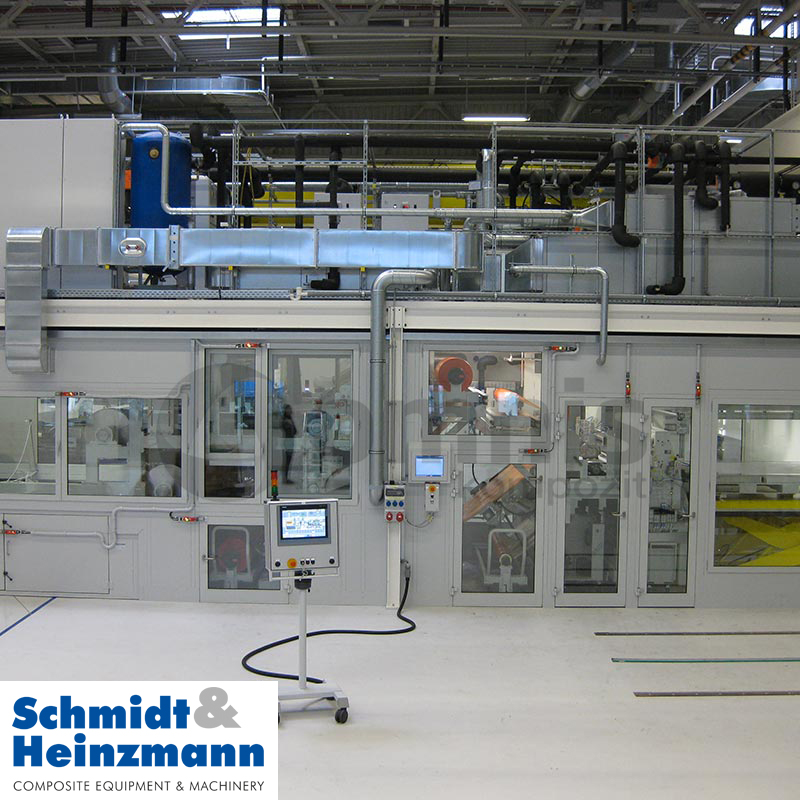
Thermoplastic Prepreg Machines
Review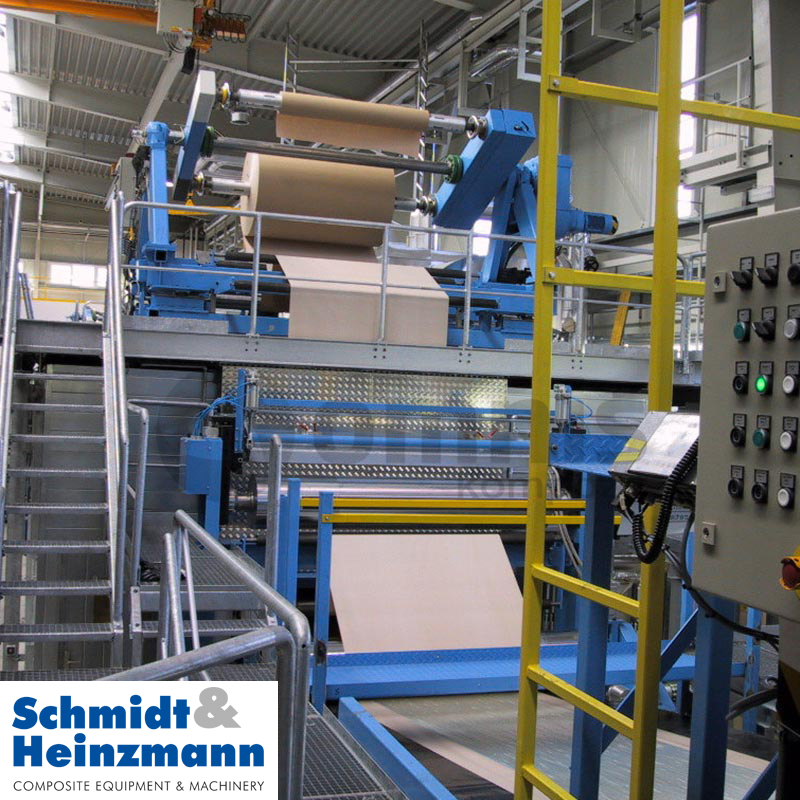
Prepreg Strip Production Lines
Review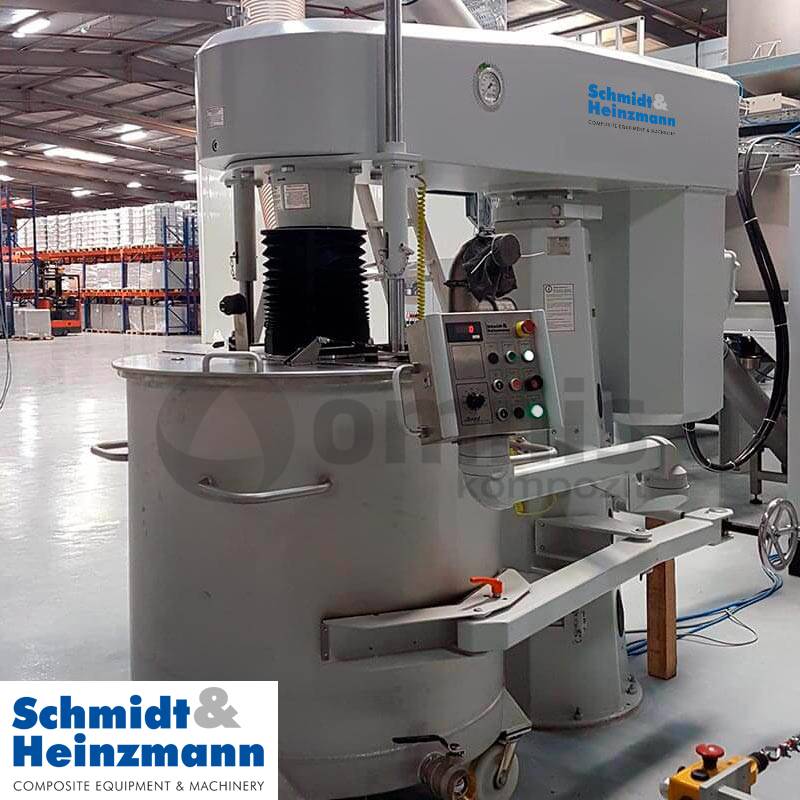
Material Preparation for SMC
Review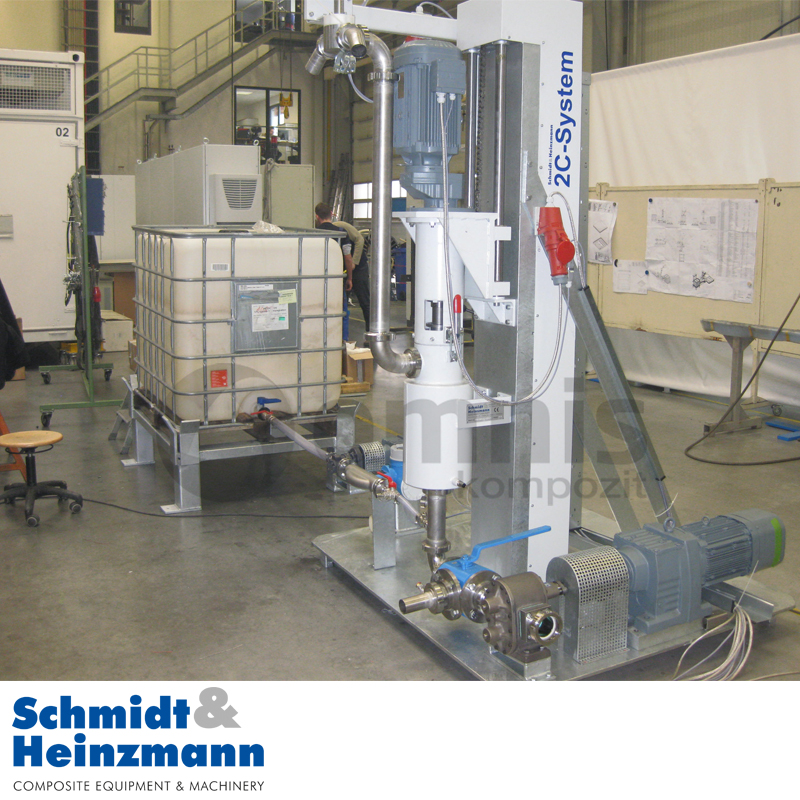
Pumping, Dosing and Mixing Systems (PDK) for SMC
Review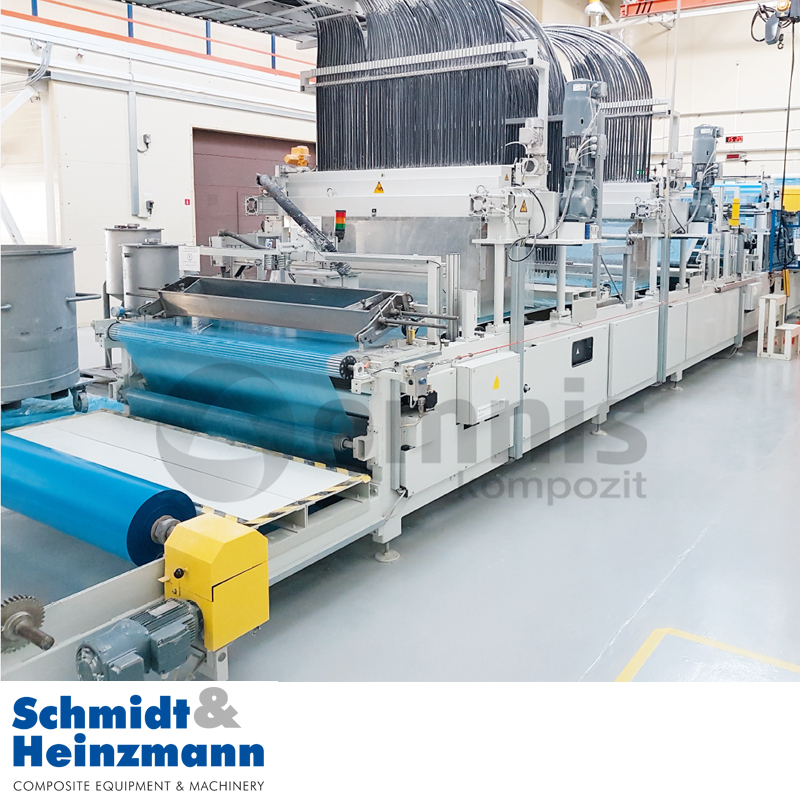
SMC Production Lines
Review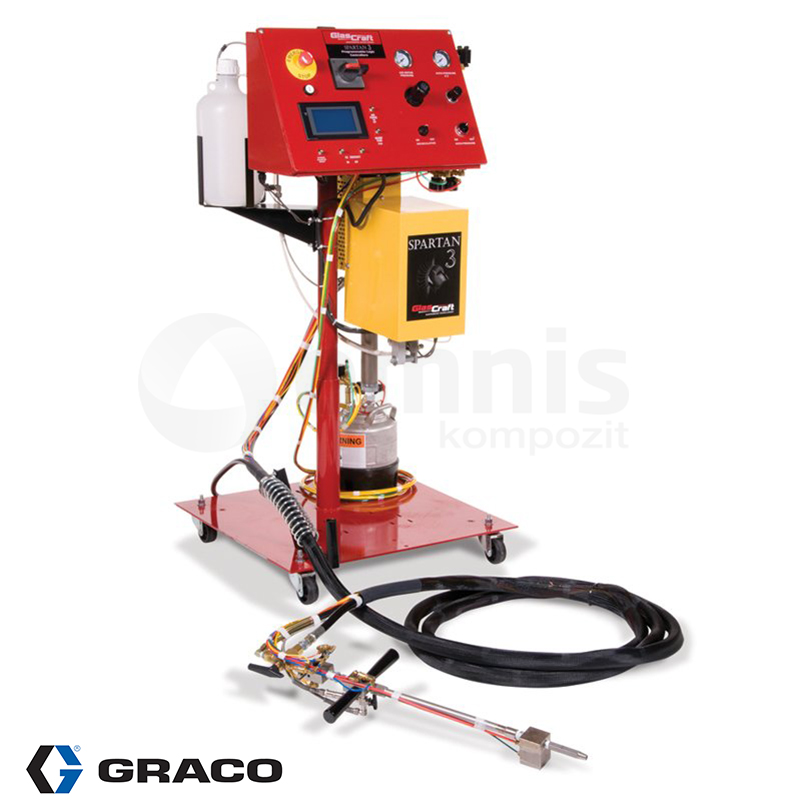
Graco RTM Machines
Review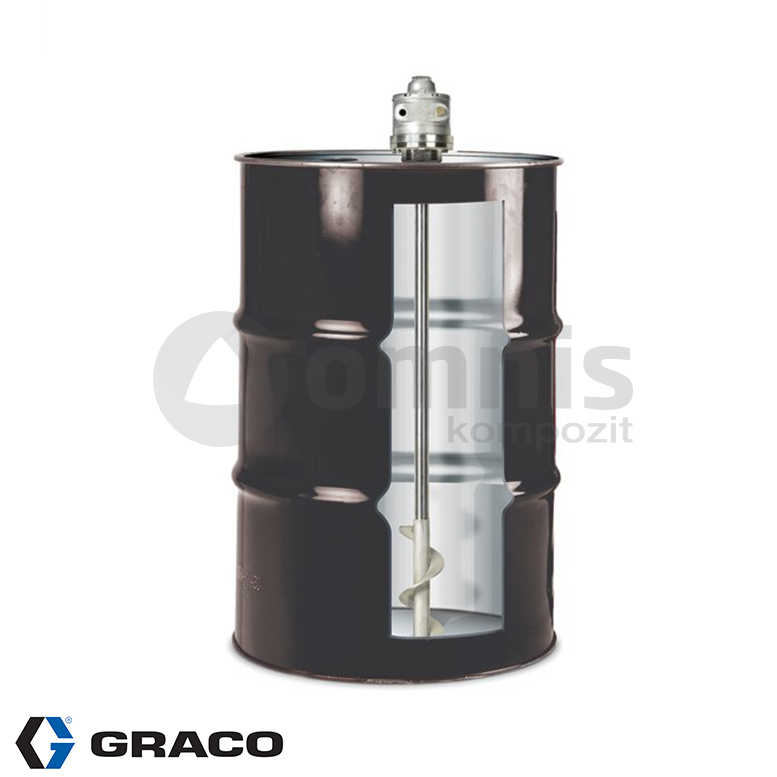
Graco Helix Resin Mixer
Review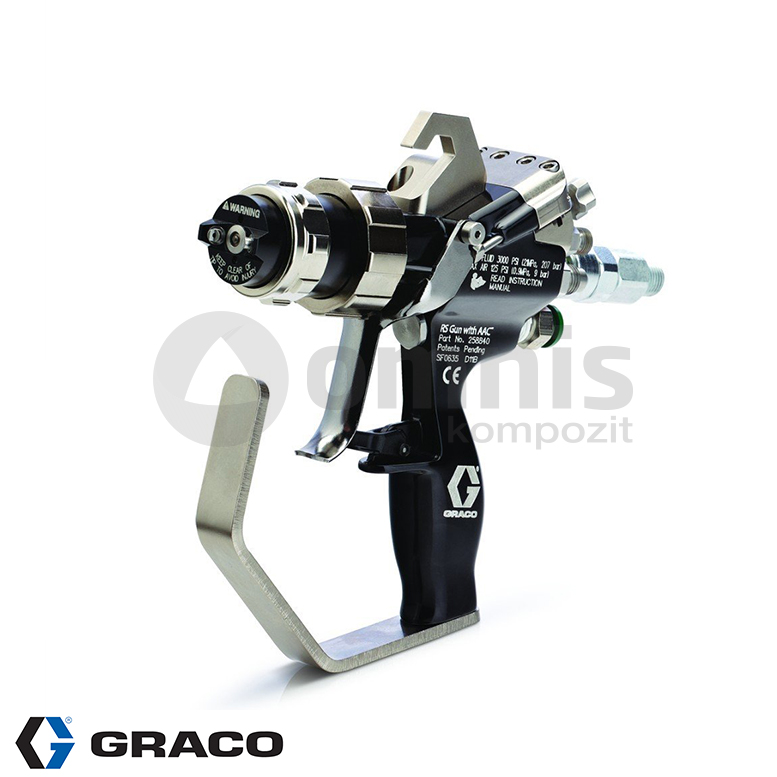
Graco RS Gelcoat Spray Gun
Review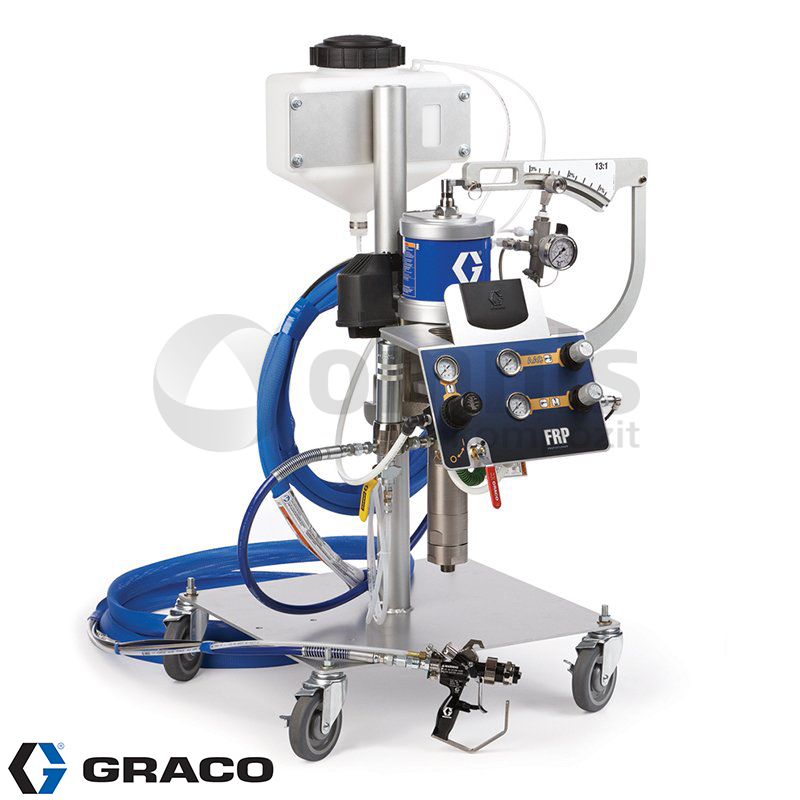
Graco Gelcoat Sprayer
Review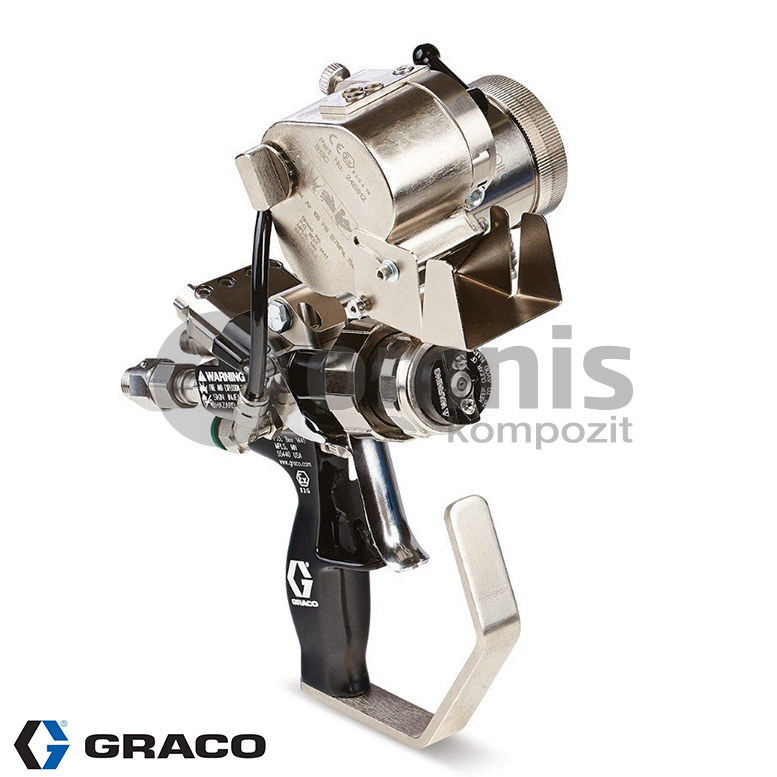
Graco RS Fiber Trimming Gun
Review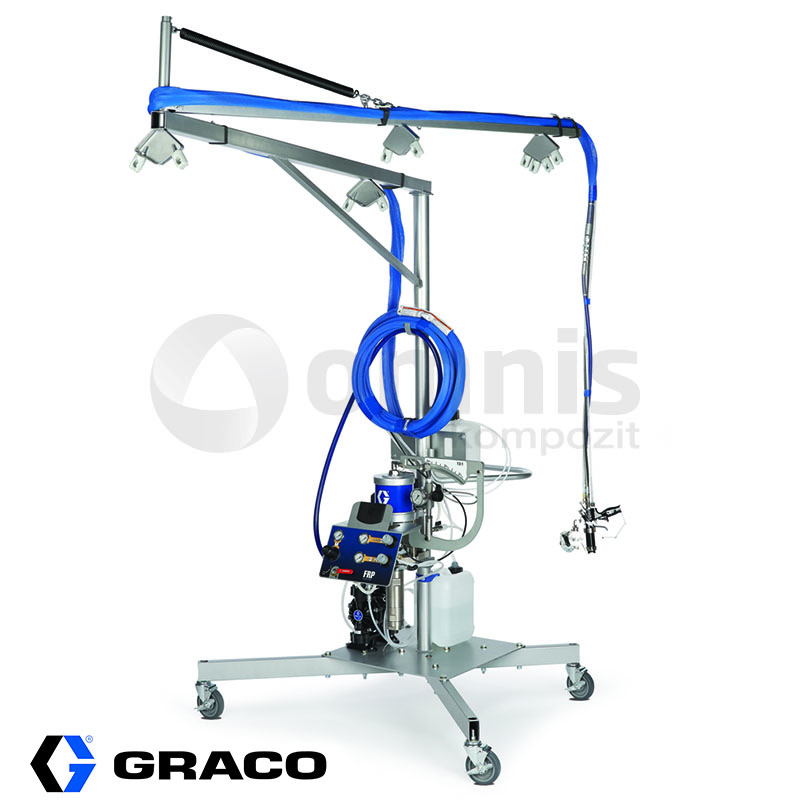
Graco Clipper Sprayer
ReviewHow Do Composite Machines Differ from Other Manufacturing Equipment?
Composite machines differ from other manufacturing equipment in their specialized design and functionality, specifically tailored to handle the unique challenges of composite material production. Unlike conventional manufacturing machinery, which often processes a single material through mechanical or thermal means, composite machines manage multiple materials simultaneously—such as fibers and resins—requiring precise control over their interaction, alignment, and curing processes. These machines typically incorporate advanced technologies to accurately mix, lay, infuse, and cure composite materials under controlled conditions, ensuring the high quality and performance of the final product. This specialization makes composite machines distinct in their capability to produce complex materials that meet stringent industry standards.
What Types of Composite Machines are Commonly Used in the Industry?
The industry commonly uses several types of composite machines, each suited to different manufacturing processes and material requirements. Key examples include:
- Filament winding machines, for creating cylindrical or spherical shapes by winding resin-impregnated fibers.
- Pultrusion machines, which pull fibers through a resin bath and then a heated die to create continuous profiles.
- Resin transfer molding (RTM) equipment, for injecting resin into a closed mold containing fiber layups.
- Autoclaves and ovens, used for curing composites under heat and pressure.
- Lay-up and infusion equipment, for manually or automatically placing fibers and applying resin before curing.
These machines offer the versatility and precision needed to produce a wide range of composite materials for various applications.
Can Composite Machines be Used for Both Thermoset and Thermoplastic Composites?
Yes, composite machines can be adapted or specifically designed to process both thermoset and thermoplastic composites. The key difference lies in the curing and processing temperatures, as well as the handling of the materials. Thermoset composites require curing through a chemical reaction that is irreversible, often necessitating equipment capable of applying heat and pressure. In contrast, thermoplastic composites are melted and shaped under heat, then cooled to solidify, requiring machines that can accurately control temperature and cooling rates. By adjusting parameters and using appropriate molds and processing technologies, manufacturers can use composite machines flexibly to produce a wide range of composite materials tailored to specific application requirements.
How Do They Contribute to the Quality of Composite Materials?
They contribute significantly to the quality of composite materials by ensuring precise control over the manufacturing process. This includes accurate dosing and mixing of resin systems, consistent alignment and tensioning of fibers, and uniform pressure and heat during curing. These controlled conditions are crucial for achieving optimal fiber-resin interaction, eliminating voids, and ensuring the composite material’s structural integrity and mechanical properties. Advanced composite machines also allow for repeatability and consistency across production runs, further enhancing product quality. By leveraging the capabilities of these machines, manufacturers can produce composite materials that meet high standards of strength, durability, and performance.
What are the Key Considerations When Selecting a Composite Machine for a Specific Application?
When selecting a composite machine for a specific application, key considerations include:
- Material compatibility: Ensuring the machine can process the types of fibers and resins used in your composites.
- Process type: Matching the machine to the composite manufacturing process (e.g., filament winding, pultrusion) that best suits your product requirements.
- Production volume: Choosing a machine that can handle your required production scale, from prototype to high-volume manufacturing.
- Precision and control: Selecting equipment that offers the control needed for the quality and consistency of your composites.
- Flexibility: Considering whether the machine can adapt to future product changes or different composite materials.
- Cost-effectiveness: Balancing the initial investment against the machine’s efficiency, maintenance costs, and potential to reduce labor and waste.
Understanding these factors will guide you in selecting a composite machine that aligns with your production goals and quality standards.
Can Composite Machines be Customized for Unique Production Requirements?
Yes, they can be extensively customized to meet unique production requirements. This customization enables manufacturers to tailor the machinery to the specific needs of their composite materials and products. Modifications can include the size and shape of the equipment, the incorporation of specialized components for handling different types of fibers and resins, and adjustments to the processing parameters like temperature, pressure, and curing times. Custom features may also be added to facilitate specific manufacturing processes such as lay-up, filament winding, pultrusion, or resin transfer molding. By working closely with equipment suppliers, manufacturers can ensure that their composite machines are perfectly aligned with their production goals, material specifications, and quality standards, ultimately enhancing efficiency, product quality, and operational flexibility.
How Do Automation and Control Systems Enhance the Performance of Composite Machines?
Automation and control systems significantly enhance the performance of composite machines by improving precision, consistency, and efficiency. These systems allow for precise control over critical parameters such as temperature, pressure, resin flow rates, and fiber alignment, which are essential for producing high-quality composite materials. Automation reduces the likelihood of human error and ensures that each production cycle is consistent with the last, leading to uniformity across batches. Additionally, automated control systems can adjust processing parameters in real-time based on sensor feedback, optimizing the manufacturing process for different materials and designs. This level of control and automation not only increases production throughput but also reduces waste and operational costs, making the manufacturing process more sustainable and cost-effective.
How Does the Maintenance of Composite Machines Affect Their Longevity and Performance?
Regular maintenance of composite machines is crucial for ensuring their longevity and optimal performance. Proper upkeep helps prevent breakdowns and malfunctions that can cause production downtime and affect product quality. Maintenance routines typically include cleaning, lubricating moving parts, checking and tightening connections, and replacing worn or damaged components. Additionally, regular inspections can identify potential issues before they lead to significant problems, allowing for preventative measures to be taken. Adhering to a scheduled maintenance plan can also extend the life of the machinery by reducing wear and tear on critical components. Ultimately, well-maintained composite machines operate more efficiently, produce higher quality materials, and have a longer service life, contributing to the overall productivity and profitability of the manufacturing operation.
Can They Handle High-Volume Production Efficiently?
They are designed to handle high-volume production efficiently, provided they are correctly configured and maintained. These machines are equipped with features that support continuous operation, such as automated feeding systems, high-capacity molds, and quick curing technologies. The use of automation and control systems further enhances their ability to produce large quantities of composite materials with minimal human intervention, ensuring consistent quality and reducing production times. For manufacturers aiming to scale up their production, investing in the right composite machines with the capacity to meet their volume requirements is crucial. By choosing machines designed for high-volume production and implementing efficient workflow processes, manufacturers can achieve significant increases in output without compromising the quality of the composite materials produced.