FRP Machinery
FRP machines are specialized equipment designed for the production of fiber-reinforced plastic (FRP) composites. These machines facilitate the process of combining resin with fiber reinforcements, such as glass, carbon, or aramid fibers, to create strong, durable, and lightweight composite materials. These machines vary in complexity and function, catering to different stages of the composite manufacturing process, including impregnation, molding, curing, and trimming. They are essential tools in industries where high-performance materials are required, such as automotive, aerospace, marine, and construction.

Composite Sheet Production
Review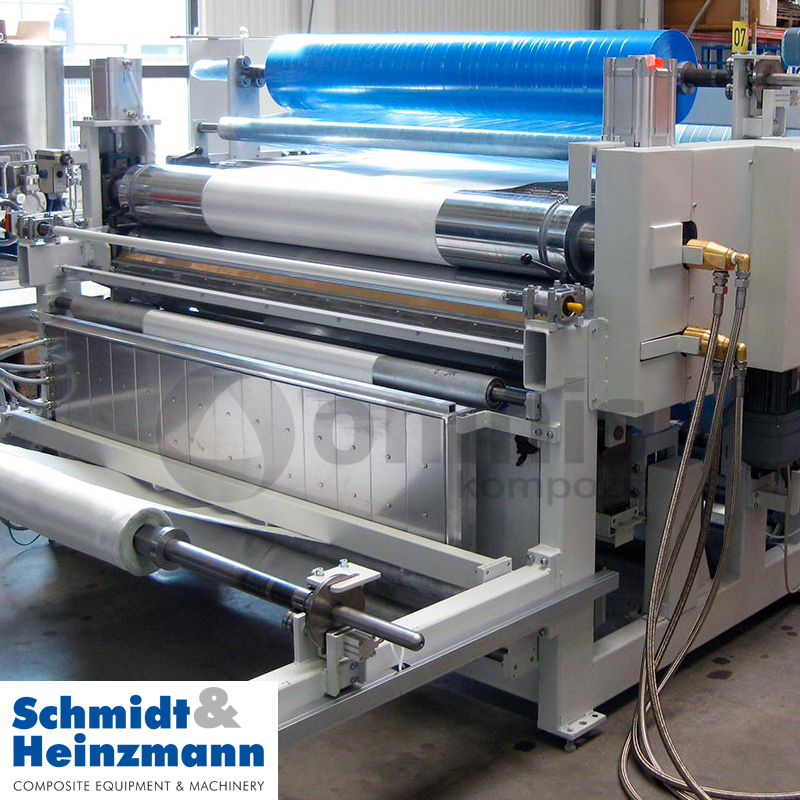
Thermosetting Prepreg Machines
Review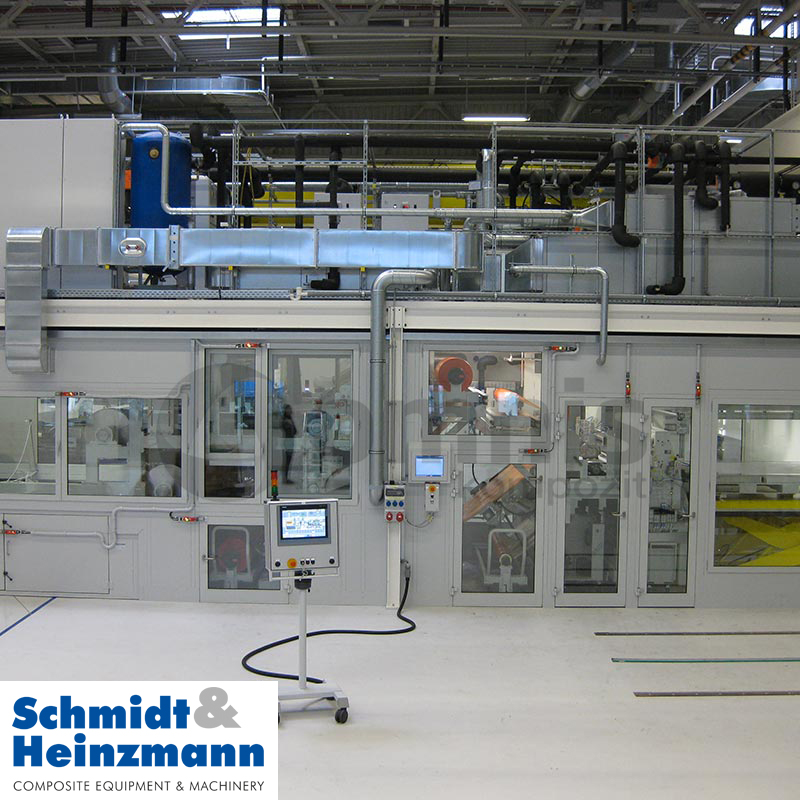
Thermoplastic Prepreg Machines
Review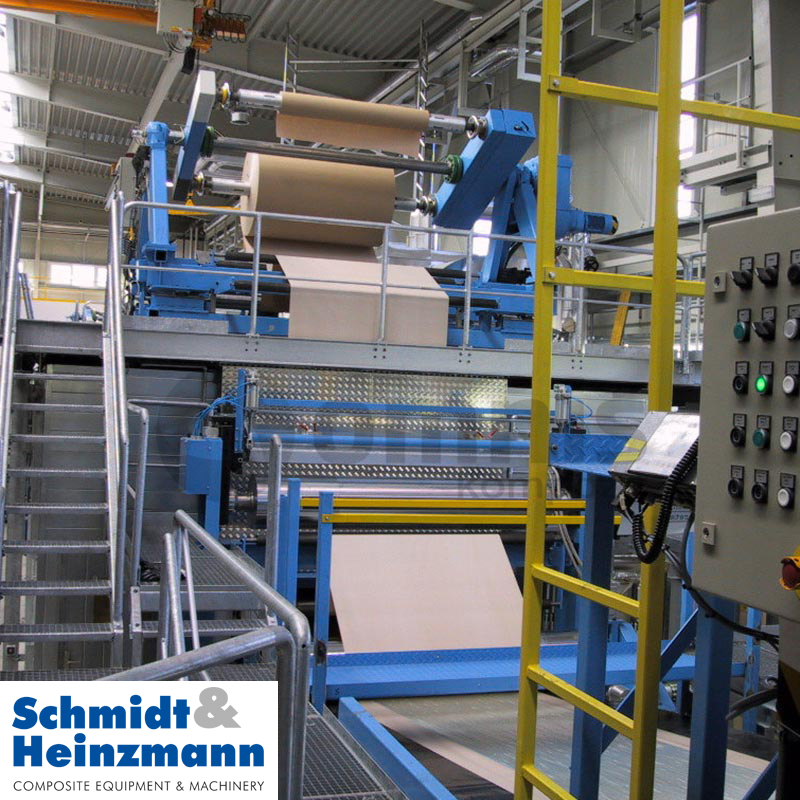
Prepreg Strip Production Lines
Review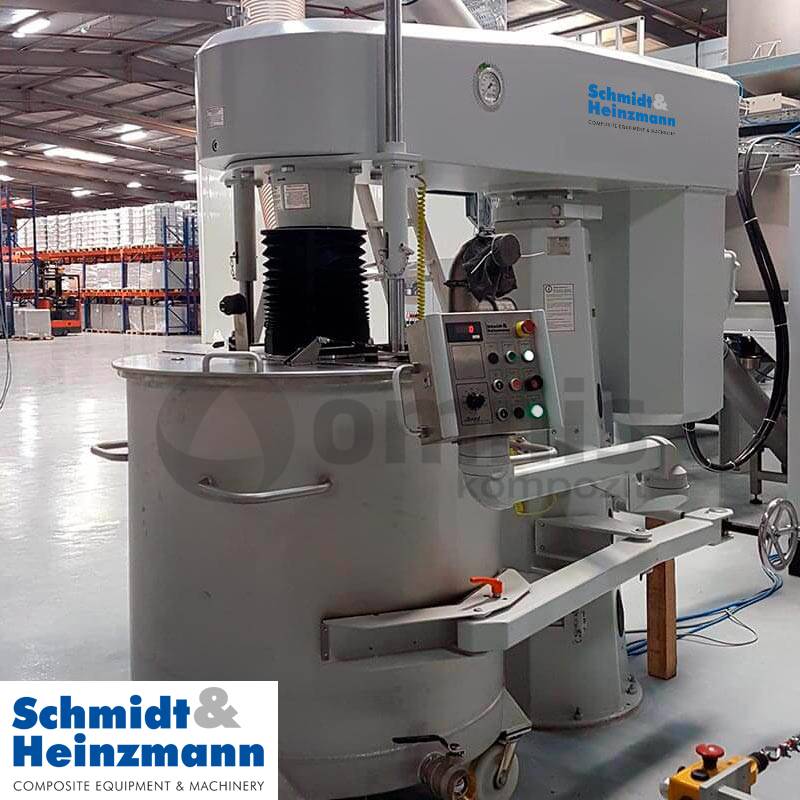
Material Preparation for SMC
Review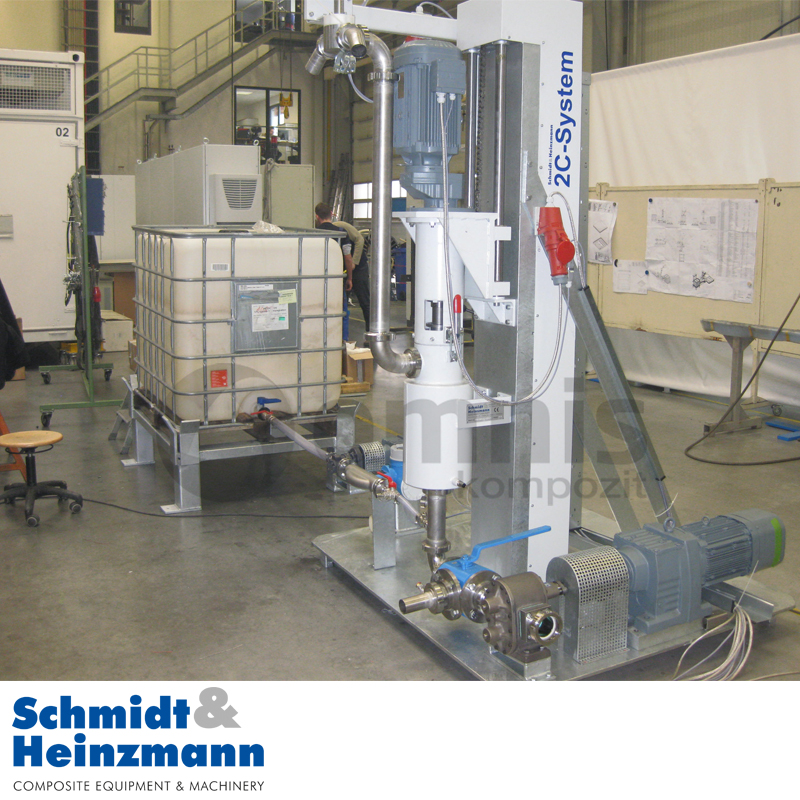
Pumping, Dosing and Mixing Systems (PDK) for SMC
Review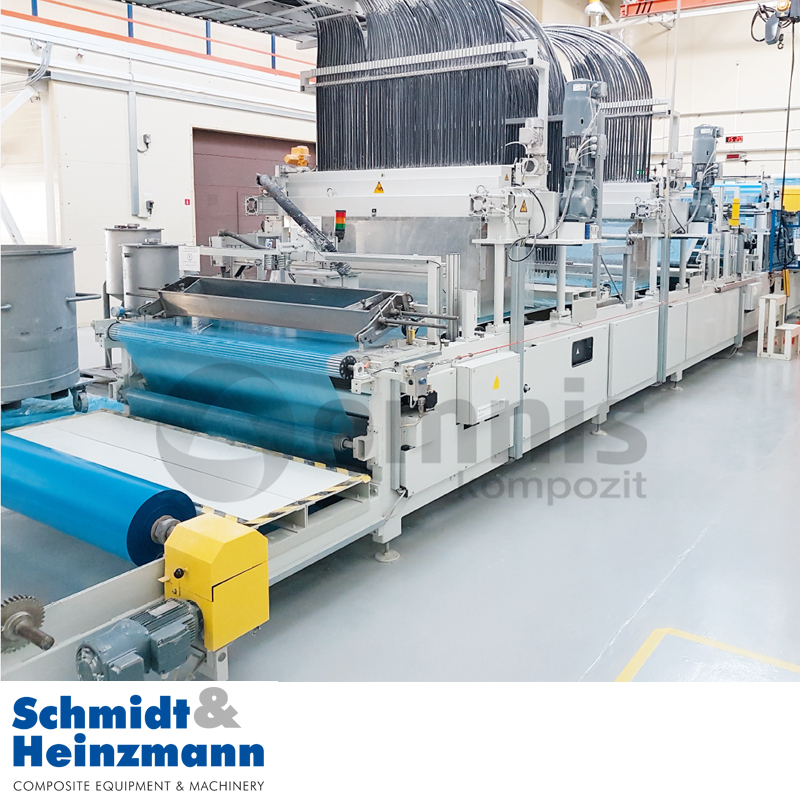
SMC Production Lines
Review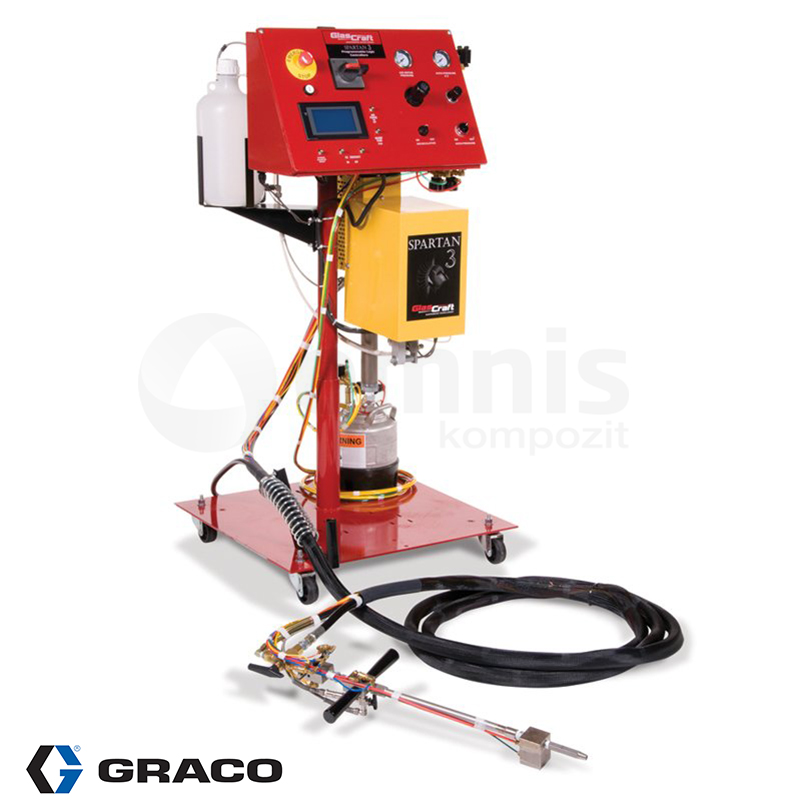
Graco RTM Machines
Review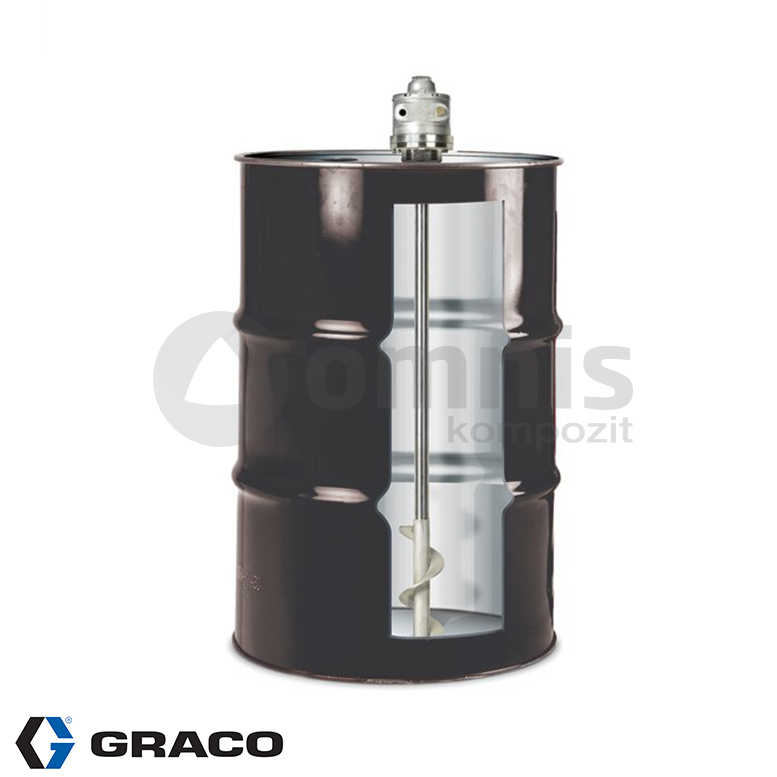
Graco Helix Resin Mixer
Review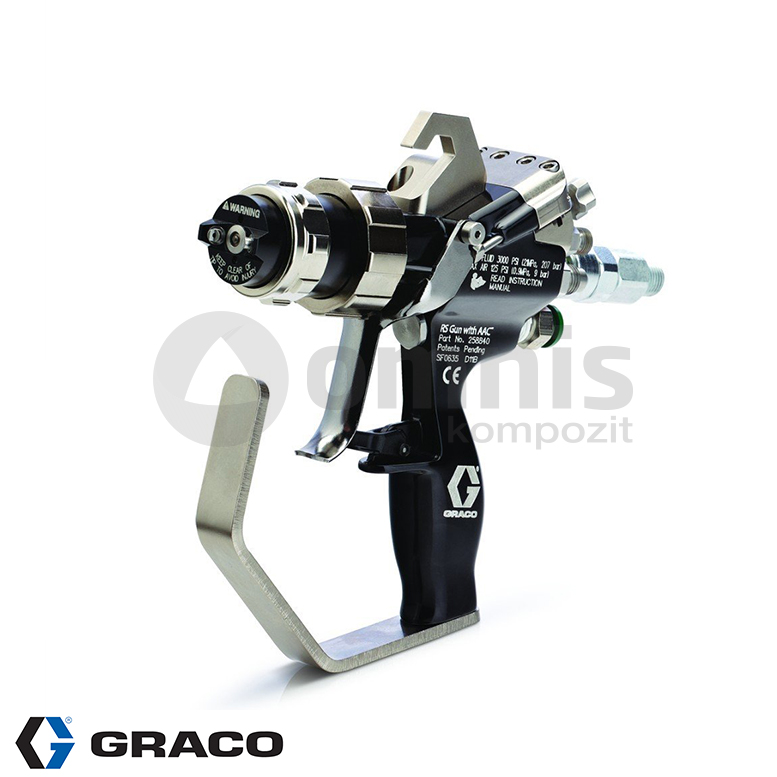
Graco RS Gelcoat Spray Gun
Review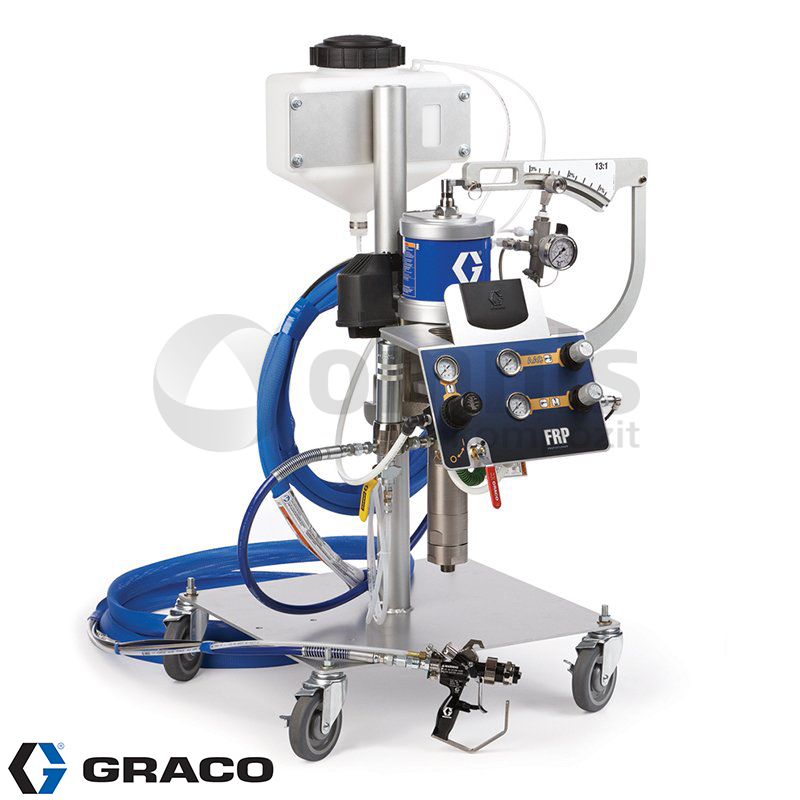
Graco Gelcoat Sprayer
Review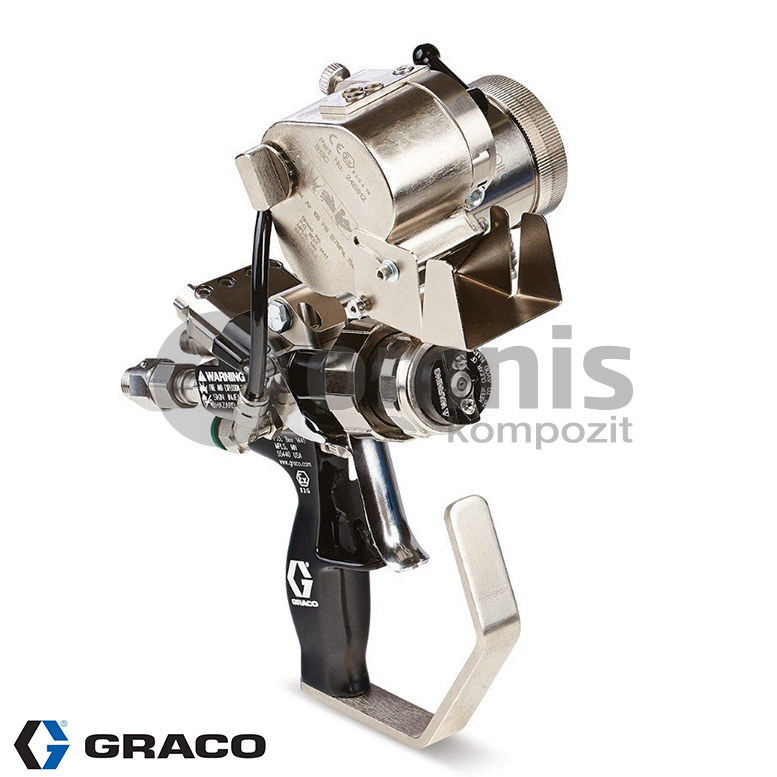
Graco RS Fiber Trimming Gun
Review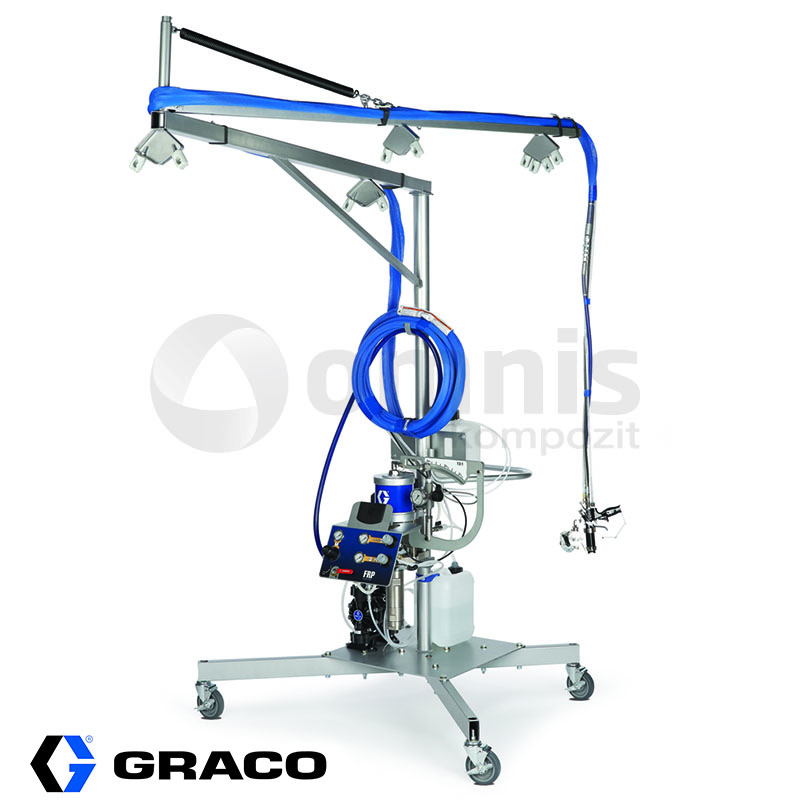
Graco Clipper Sprayer
ReviewHow do FRP machines work in composite material production?
FRP machines work in composite material production by automating the process of impregnating the reinforcing fibers with a polymer resin, shaping the composite to the desired form, and curing it to solidify the material. The specific operation depends on the type of machine and the manufacturing process being used, such as pultrusion, filament winding, or resin transfer molding (RTM). These machines ensure precise control over the resin-to-fiber ratio, uniform distribution of the resin, and consistent application of heat and pressure, resulting in high-quality FRP composites with optimal mechanical properties.
What types of FRP machines are available?
Various types of machines are available, each designed for specific composite manufacturing processes. Key types include:
- Pultrusion machines, which continuously pull fibers through a resin bath and a heated die to create constant cross-section profiles.
- Filament winding machines, which wind resin-impregnated fibers around a rotating mandrel to produce cylindrical or complex shapes.
- Resin transfer molding (RTM) machines, which inject resin into a closed mold containing the fiber reinforcement.
- Gel coat spraying machines, used for applying the outer protective and decorative layer on composite products.
- Chopper gun machines, which chop and spray fiberglass and resin simultaneously for open mold processes.
These machines cater to different production needs and composite material specifications.
How do I choose the right FRP machine for my manufacturing needs?
Choosing the right machine for your manufacturing needs involves evaluating several factors, including the type of composite products you intend to produce, the volume of production, the materials used, and the desired properties of the final product. Consider the specific manufacturing process that best suits your product requirements, such as pultrusion for linear profiles or filament winding for cylindrical items. Assess the machine’s capacity, speed, automation level, and compatibility with your materials. Consulting with machine manufacturers or suppliers can provide valuable insights and recommendations based on your specific production goals and constraints.
Can FRP machines be used for both small-scale and industrial-scale production?
Yes, these machines can be used for both small-scale and industrial-scale production. Manufacturers offer a wide range of machines designed to accommodate different production volumes and requirements. Smaller, manual or semi-automatic machines are suitable for low-volume, custom, or prototype production, while larger, fully automated systems are designed for high-volume, industrial-scale manufacturing. The scalability and versatility of machines make them suitable for businesses of all sizes, from startup composite workshops to large manufacturing plants.
What are the main advantages of using FRP machines in composite manufacturing?
The main advantages of using machines in composite manufacturing include increased production efficiency, consistent product quality, reduced labor costs, and enhanced safety. machines automate critical steps in the composite production process, ensuring precise control over material ratios, uniform distribution of resin, and accurate shaping and curing. This automation results in higher throughput, minimal material waste, and consistent mechanical properties across production batches. Additionally, the use of machines reduces the need for manual labor, lowering production costs and minimizing the risk of workplace injuries associated with handling materials and equipment.
How do FRP machines differ from other composite manufacturing equipment?
FRP machines differ from other composite manufacturing equipment in their specific design and functionality tailored to the production of fiber-reinforced plastics. While general composite manufacturing equipment may include a broad range of machinery for processing various composite materials, machines are specialized for handling the unique requirements of FRP composites, such as impregnating fibers with resin, precise control of fiber orientation, and curing composites under controlled conditions. This specialization allows for more efficient and higher-quality production of FRP products compared to using more generic composite manufacturing equipment.
What materials can be processed with FRP machines?
These type of machines can process a wide range of materials, including various types of resins (such as polyester, vinyl ester, and epoxy) and fiber reinforcements (such as glass, carbon, and aramid fibers). These machines are designed to handle different forms of fibers, including rovings, mats, and woven fabrics, allowing for the production of composites with diverse properties and applications. The versatility of FRP machines in processing different materials makes them invaluable in creating customized composite solutions for specific industry needs.
How does the use of FRP machines impact the quality of the final composite product?
The use of machines significantly impacts the quality of the final composite product by ensuring uniform material distribution, precise control over the resin-to-fiber ratio, and consistent application of heat and pressure during curing. This results in FRP composites with optimal mechanical properties, including strength, stiffness, and durability. The automated processes reduce the likelihood of human error and material wastage, leading to higher-quality products with fewer defects. Consequently, FRP machines play a crucial role in achieving the desired performance and reliability of composite materials.
Can FRP machines be customized for specific production requirements?
Yes, FRP machines can be customized for specific production requirements to accommodate unique product designs, materials, and manufacturing processes. Manufacturers of FRP machines often offer customization options, such as adjustable molds, programmable controls, and modular systems that can be tailored to specific production needs. Customization allows for greater flexibility in composite manufacturing, enabling producers to optimize their operations for efficiency, quality, and product differentiation. Working closely with machine suppliers can ensure that the equipment is precisely configured to meet the unique demands of your manufacturing process.
What maintenance is required for FRP machines?
Maintenance required for FRP machines typically includes regular cleaning, lubrication of moving parts, inspection for wear and tear, and calibration of control systems. Preventive maintenance schedules should be established to ensure the machines operate efficiently and to minimize downtime. This may involve checking for resin buildup, ensuring proper alignment of components, and replacing worn or damaged parts. Adhering to the manufacturer’s maintenance recommendations and using trained personnel for servicing can help maintain the performance and longevity of FRP machines.
How energy-efficient are FRP machines?
The energy efficiency of FRP machines varies depending on their design, age, and the specific manufacturing process they support. Modern FRP machines are increasingly designed with energy efficiency in mind, incorporating features such as variable speed drives, energy-saving heating elements, and automated control systems that minimize energy consumption. Manufacturers are focusing on reducing the environmental impact of composite production by optimizing machine operations and materials processing. Selecting energy-efficient FRP machines can contribute to lower operational costs and a reduced carbon footprint for composite manufacturers.