Infusion Mesh
An infusion mesh, also known as flow mesh, is a specially designed material used in the vacuum infusion process of composite manufacturing. It is typically laid on top of the fiber reinforcement within the mold and under the vacuum bag. The primary function of an infusion mesh is to facilitate the even and efficient distribution of resin across the entire lay-up during the infusion process. Made from materials such as nylon or polyester, these meshes have an open structure that allows resin to flow freely through them while minimizing the potential for air entrapment and ensuring that the resin fully saturates the fiber reinforcement. The use of infusion mesh is crucial in achieving high-quality composite parts with consistent resin distribution and optimal mechanical properties.
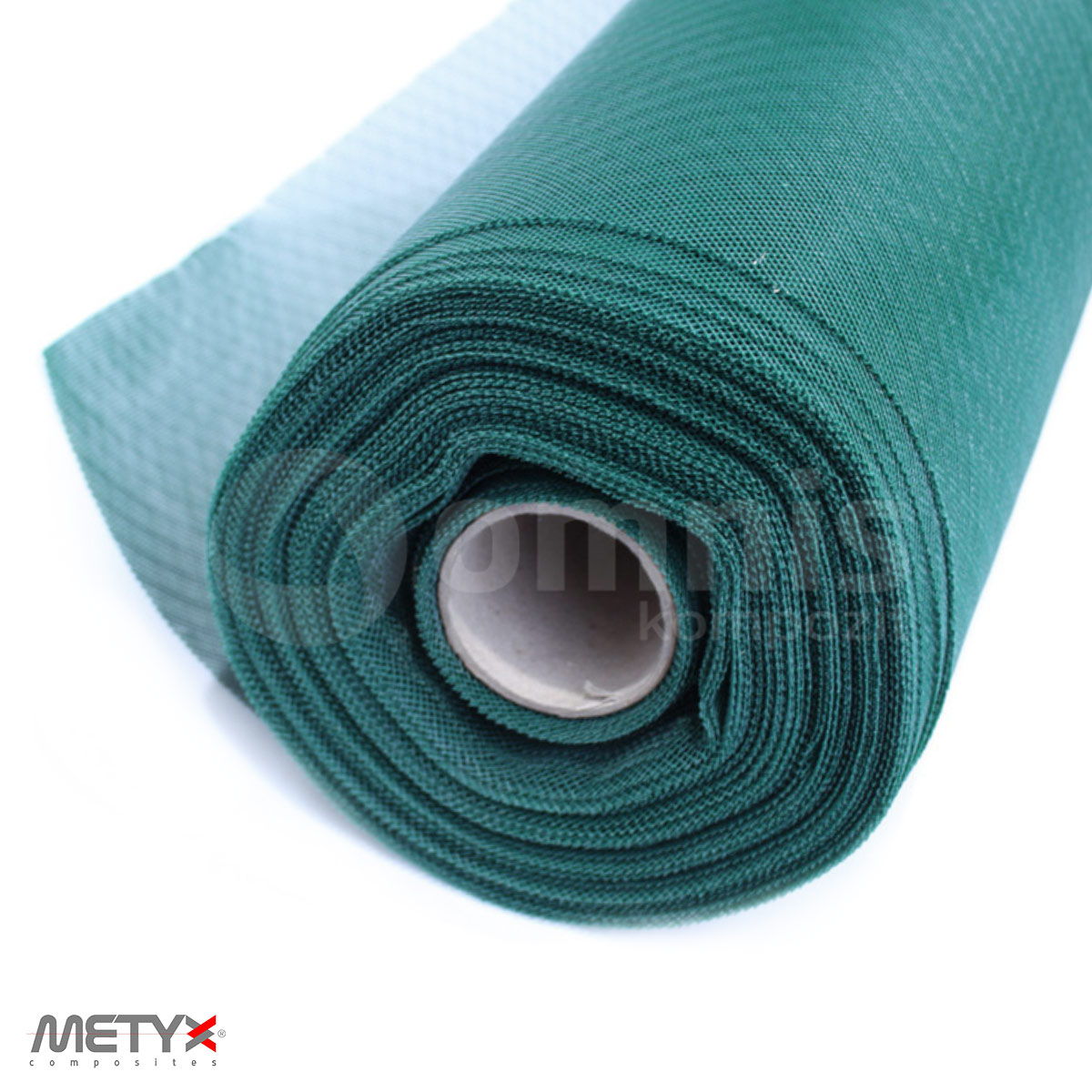
Flow Mesh
ReviewHow Does an Infusion Mesh Work in the Vacuum Infusion Process?
In the vacuum infusion process, the infusion mesh works by creating a pathway for the resin to flow over and through the fiber reinforcement layer. Once the vacuum is applied and resin is introduced into the mold, the mesh channels the resin throughout the mold, ensuring it reaches all areas of the fiber reinforcement. This is especially important in large or complex molds where resin might otherwise not distribute evenly. The mesh’s open structure allows for quick and efficient resin flow under vacuum pressure, significantly reducing the risk of dry spots and ensuring that the resin thoroughly saturates the fibers. This controlled resin flow is key to producing composites with uniform properties and strength.
What are the Main Benefits of Using an Infusion Mesh in Composite Manufacturing?
The main benefits of using an infusion mesh in composite manufacturing include:
- Improved Resin Distribution: Ensures even resin flow across the entire lay-up, crucial for large or complex shapes.
- Reduced Air Entrapment: Minimizes the risk of voids and air pockets, which can compromise the composite’s structural integrity.
- Enhanced Mechanical Properties: Achieves consistent resin-to-fiber ratios, enhancing the strength, stiffness, and durability of the composite part.
- Increased Manufacturing Efficiency: Speeds up the infusion process by facilitating faster resin flow, reducing production times.
- Versatility: Compatible with various resin systems and composite manufacturing processes, offering flexibility in production.
Can It be Used with All Types of Resin Systems?
Yes, it can be used with a wide range of resin systems, including epoxy, polyester, and vinyl ester resins, which are commonly used in composite manufacturing. The mesh’s material is selected to be chemically compatible with these resin types, ensuring that it does not interfere with the curing process or the final properties of the composite. However, it’s important to choose an infusion mesh with an appropriate structure and porosity for the specific viscosity of the resin system being used, as this can affect the resin flow rate and the overall efficiency of the infusion process.
How Do You Select the Right Type of Infusion Mesh for a Specific Project?
Selecting the right type of infusion mesh for a specific project involves considering several factors:
- Resin Type and Viscosity: Ensure the mesh is compatible with the resin system and can facilitate its flow properties.
- Mold Size and Complexity: Choose a mesh with the appropriate flow characteristics for the mold’s dimensions and intricacy.
- Fiber Reinforcement: Consider the type and arrangement of the fiber reinforcement to ensure the mesh promotes optimal resin saturation.
- Desired Composite Properties: Select a mesh that contributes to achieving the targeted mechanical and physical properties of the final composite part.
Consulting with material suppliers and conducting preliminary tests with different meshes can help identify the best option for a given project.
What Role Does the Infusion Mesh Play in Ensuring Uniform Resin Distribution?
It plays a crucial role in ensuring uniform resin distribution throughout the composite lay-up. Its structured yet porous nature creates channels that guide the resin across the entire surface of the mold, even in areas that are distant from the resin inlet points. By facilitating the flow of resin to all parts of the fiber reinforcement, the mesh helps prevent dry spots and ensures that every fiber is properly saturated. This uniform distribution of resin is essential for achieving composites with consistent mechanical properties, optimal strength, and durability. Without an infusion mesh, it would be challenging to ensure such even resin coverage, especially in complex molds or with large-scale parts.
How Does the Infusion Mesh Affect the Overall Quality of the Composite Part?
It significantly affects the overall quality of the composite part by promoting a thorough and even distribution of resin throughout the fiber reinforcement. This uniform resin infusion ensures that the final composite material exhibits consistent mechanical properties across the entire part, with minimal voids or weak points. By reducing the likelihood of air entrapment and ensuring optimal fiber saturation, the mesh contributes to the production of stronger, more reliable composite parts. Furthermore, the ability of the infusion mesh to facilitate a controlled and efficient resin flow process helps manufacturers achieve higher-quality outcomes with reduced waste and improved manufacturing efficiency.