Concrete Systems
Concrete additives are essential components that are added to the concrete mix to enhance its properties and performance. These additives can significantly improve the workability, strength, durability, and resistance of concrete to environmental conditions. By incorporating concrete additives into the mix, constructors can tailor the concrete to meet specific requirements of various construction projects. Whether it's accelerating the curing process, increasing tensile strength, or reducing water content without compromising the workability, concrete additives offer a versatile solution to many challenges faced in the construction industry. Their use not only optimizes the construction process but also contributes to the longevity and sustainability of the structures built.
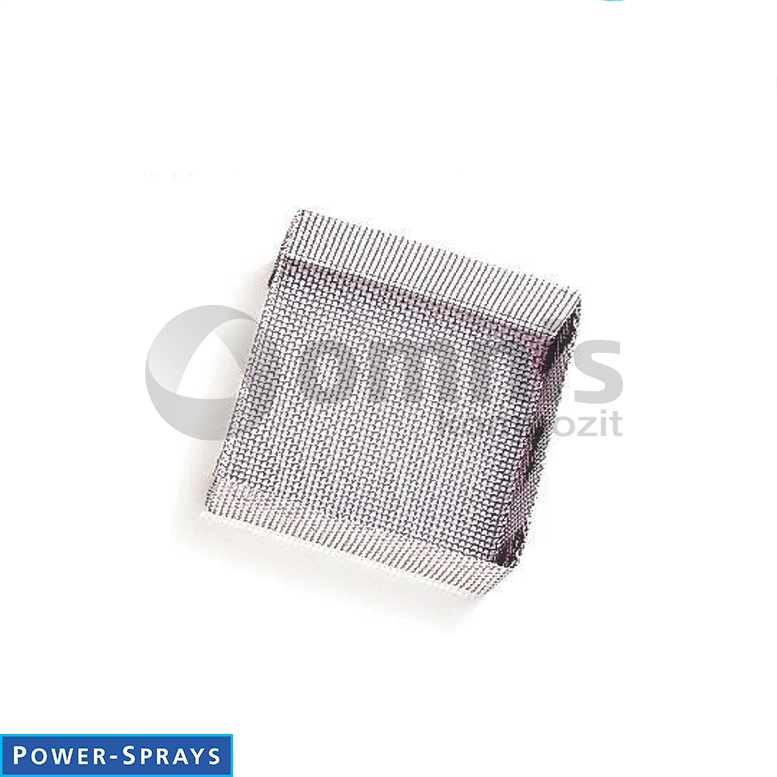
Fiber Ratio Test Basket
Review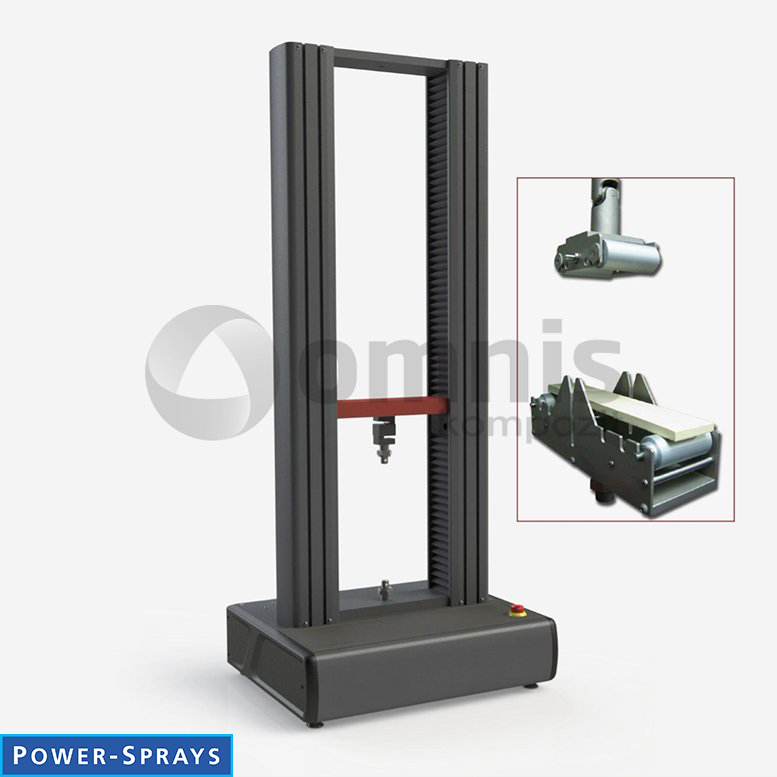
GRC Flexure Test
Review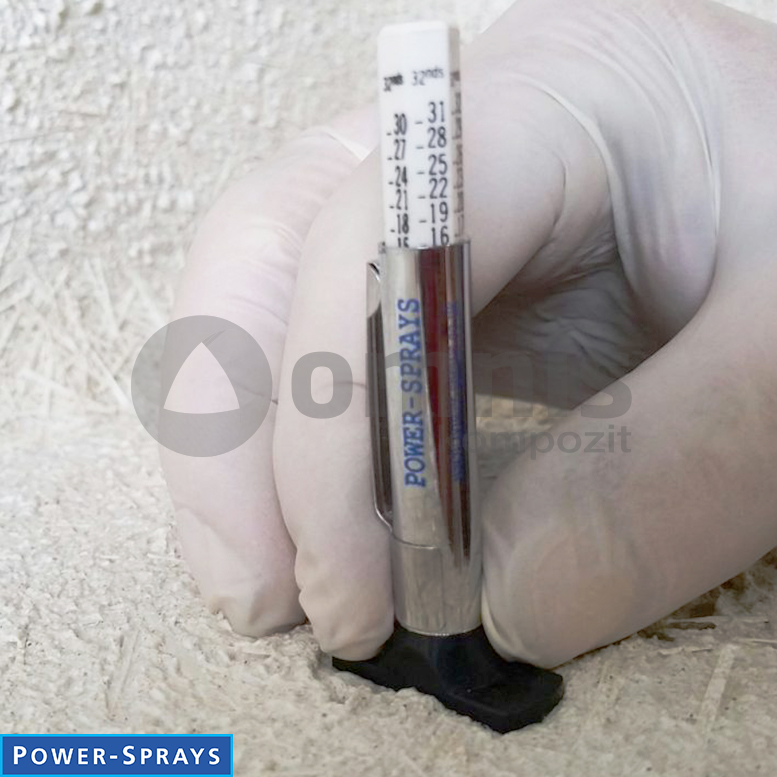
Thickness Measuring Pen
Review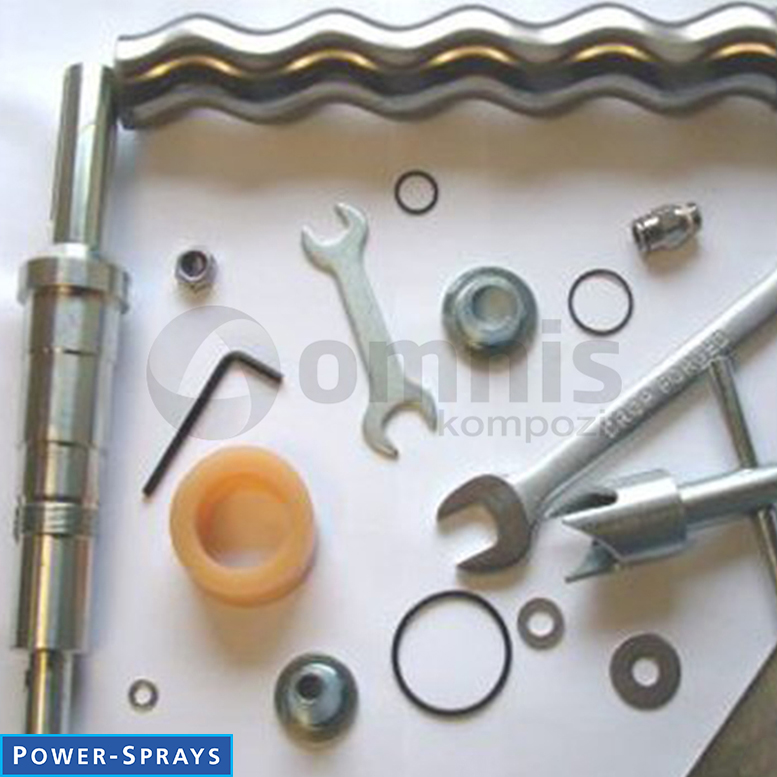
GRC Spare Parts
Review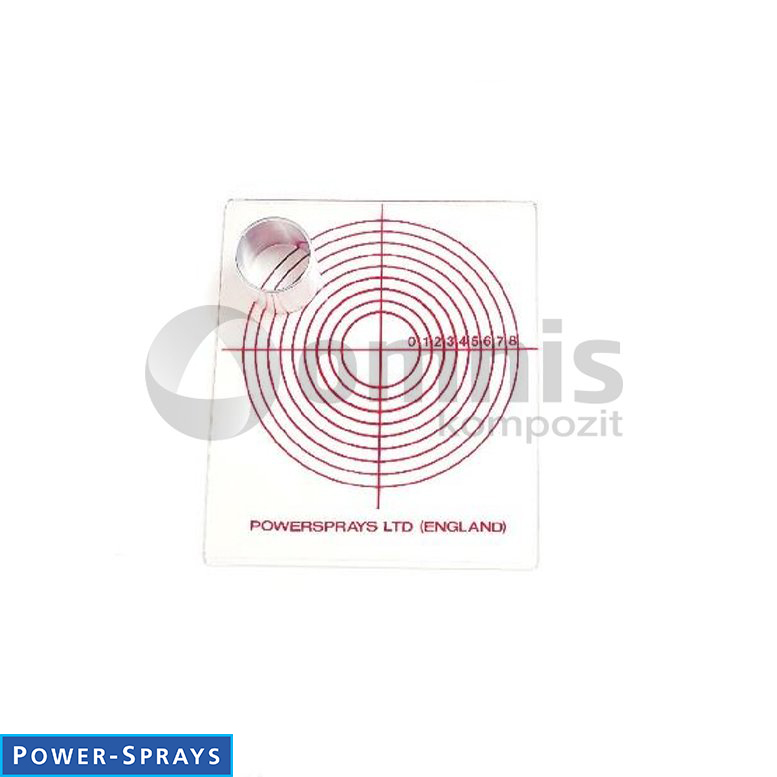
Pour Test Kit
Review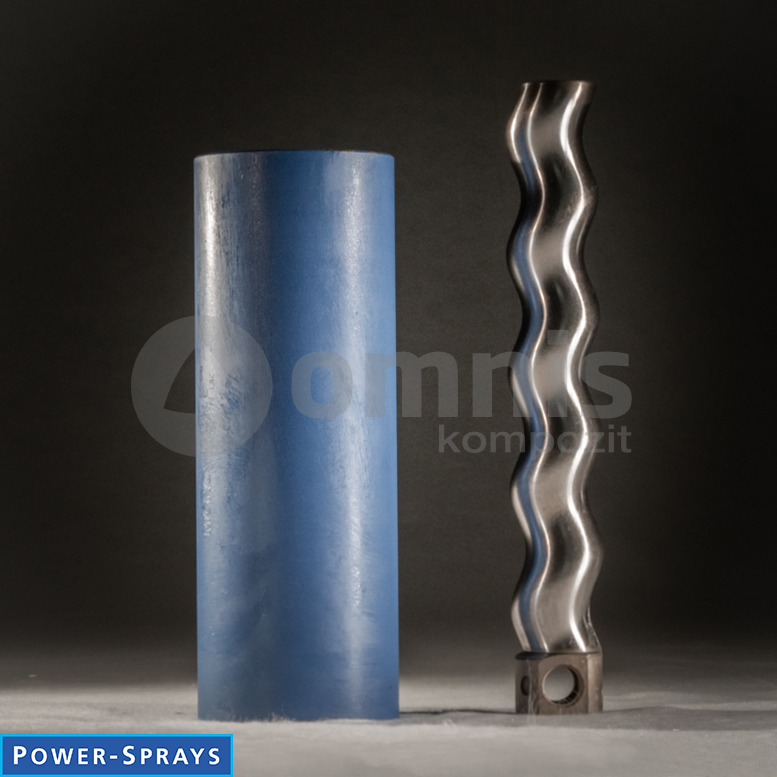
Rotor Stator Sets
Review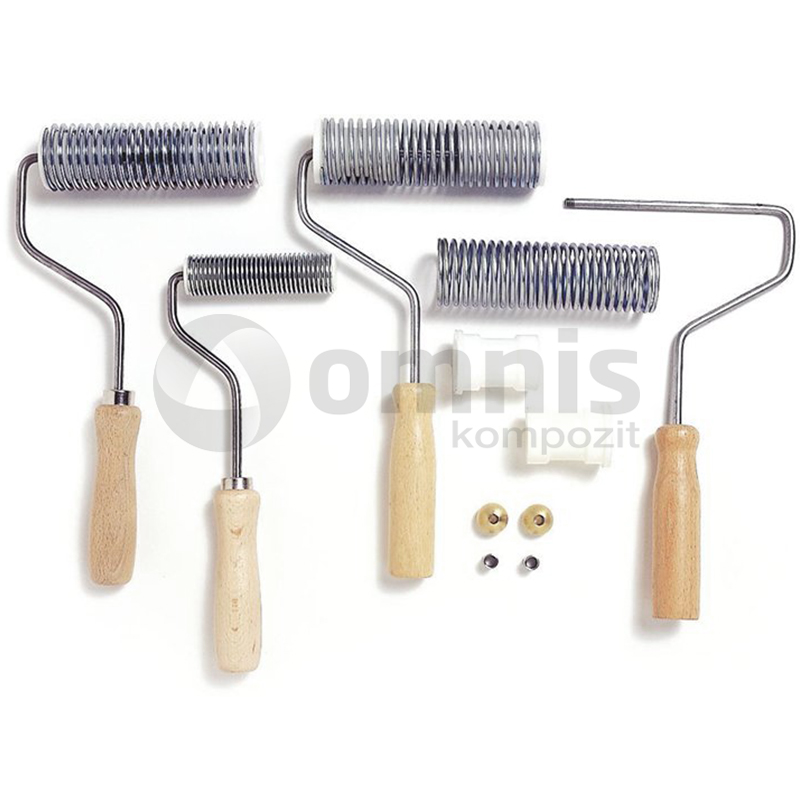
GRC Rolls
Review
Power Sprays Forklift Mounted Bucket Carrier
Review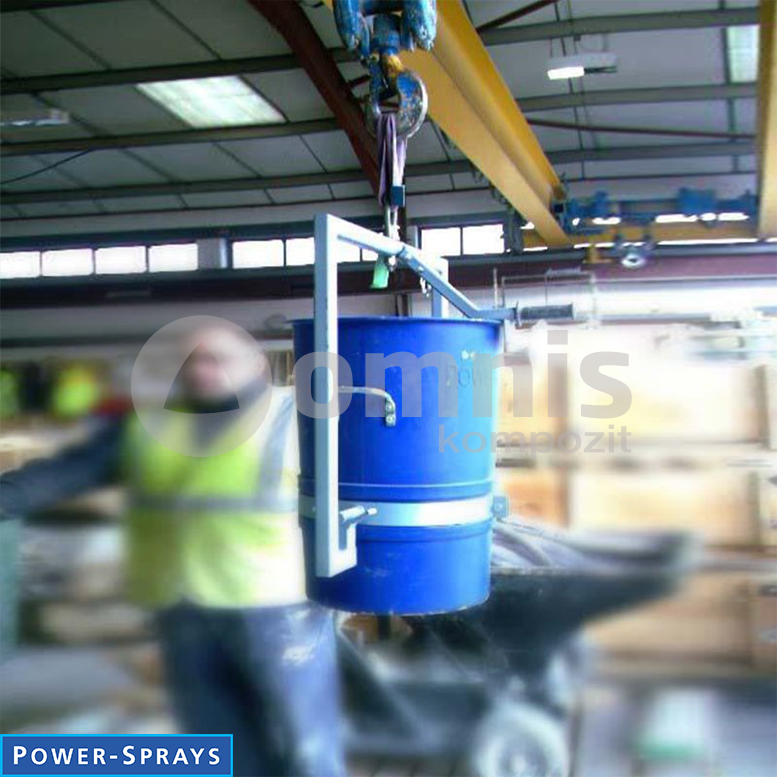
Power Sprays Crane Mounted Bucket Carrier
Review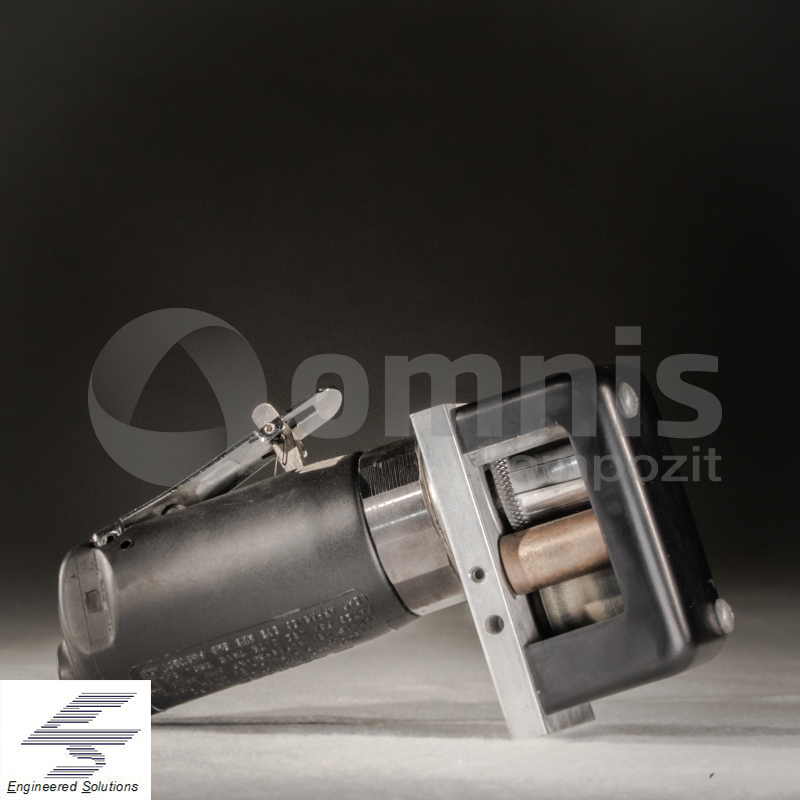
Portable Glass Fiber Trimming Machine
Review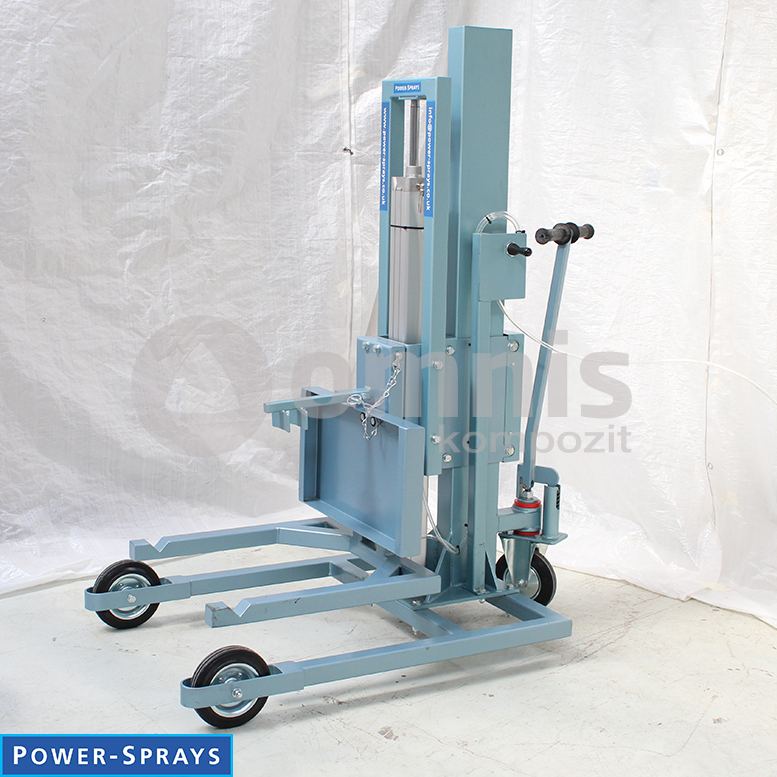
Power Sprays Wheeled Pneumatic Bucket Carrier
Review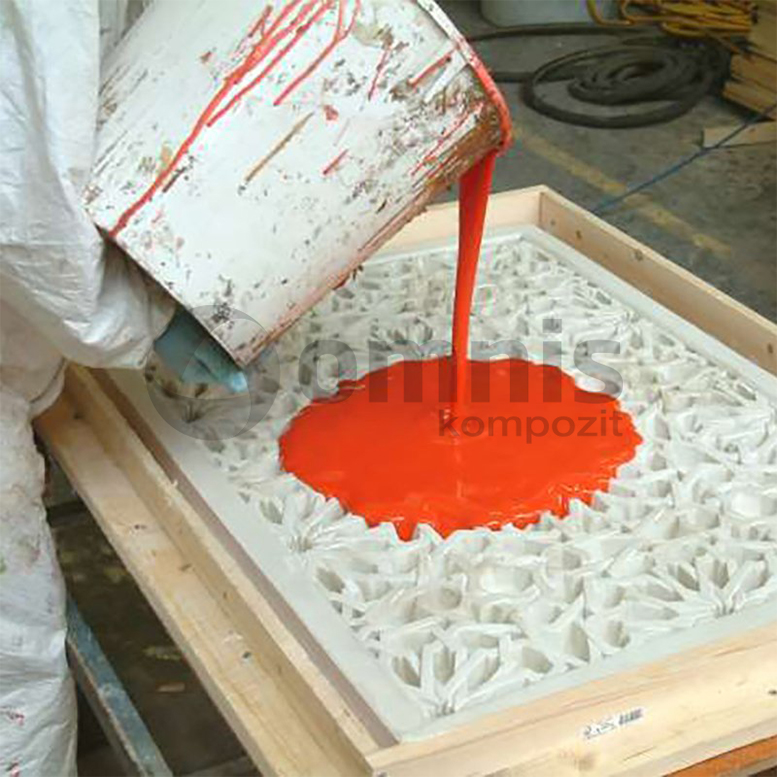
GRC Flexible Mold
Review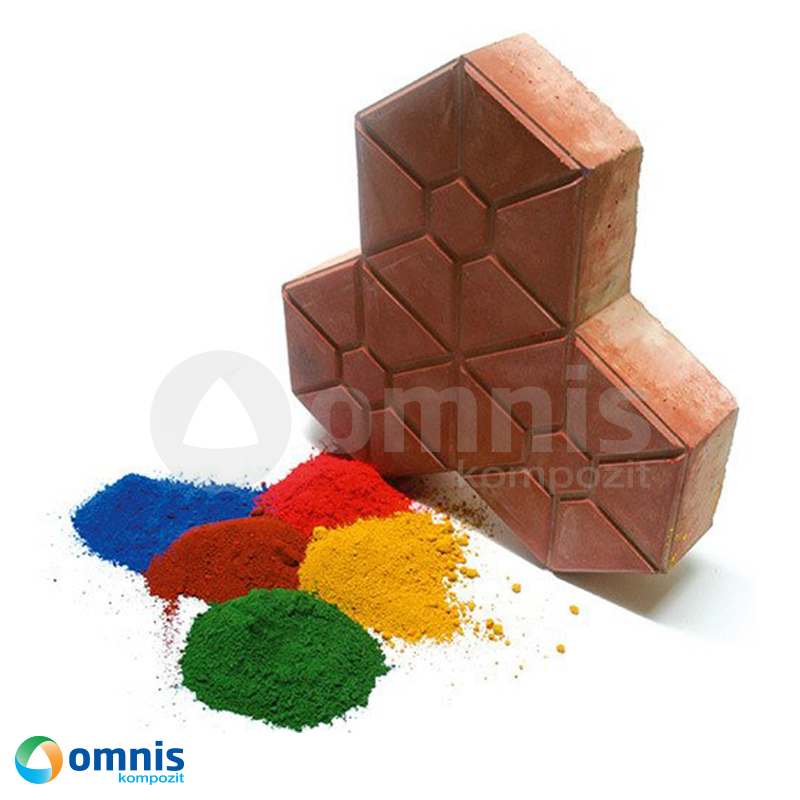
Powder Pigment
Review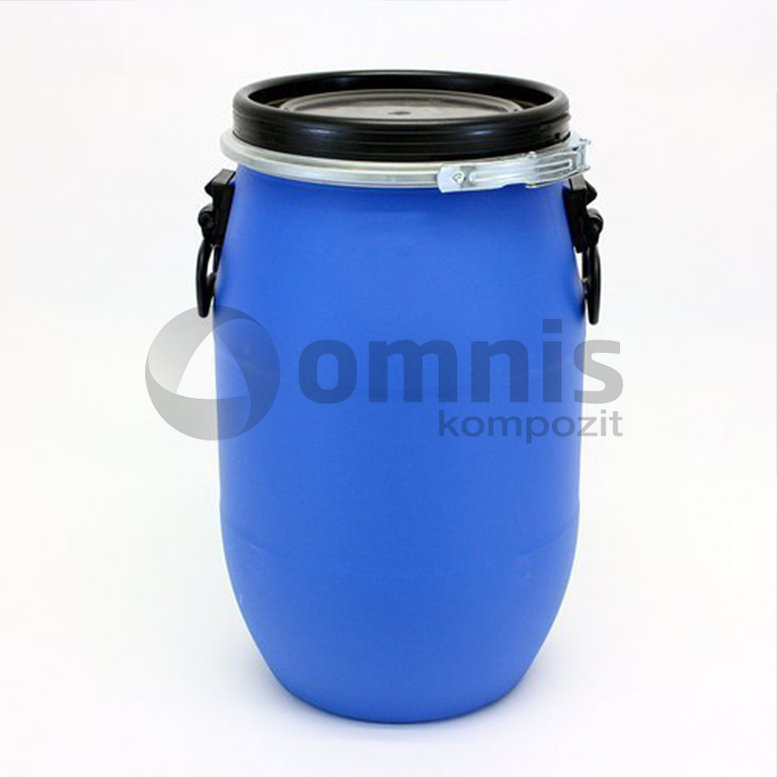
Acrylic Polymer
Review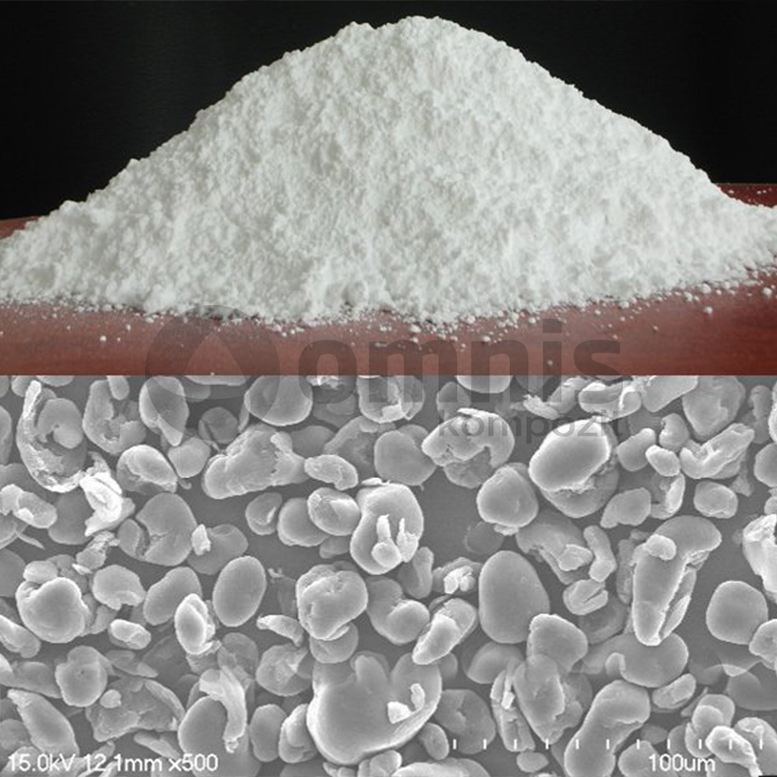
Powder Polymer
Review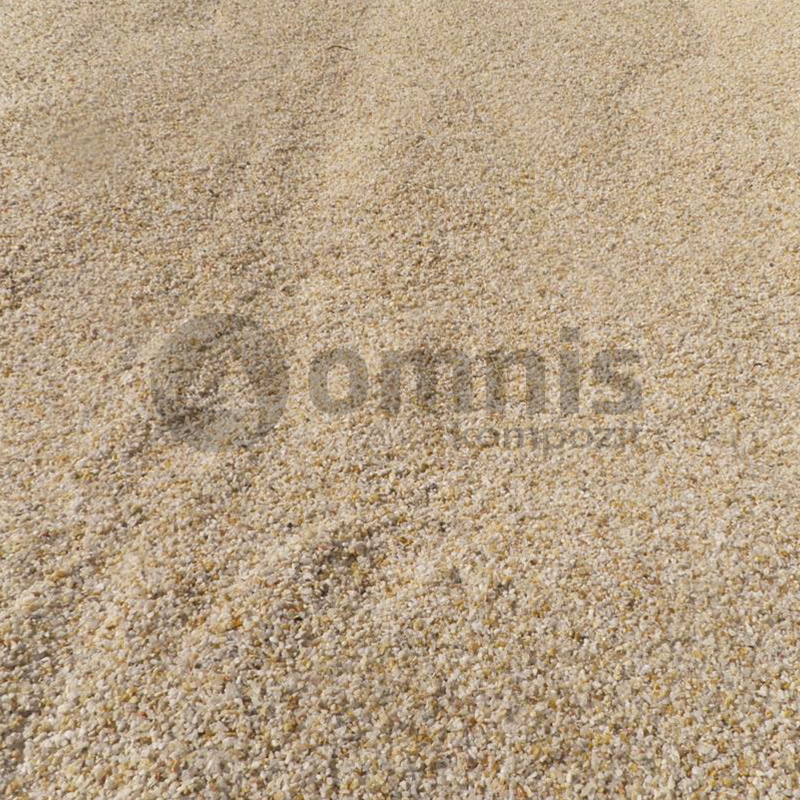
Silica Sand AFS 30-35
Review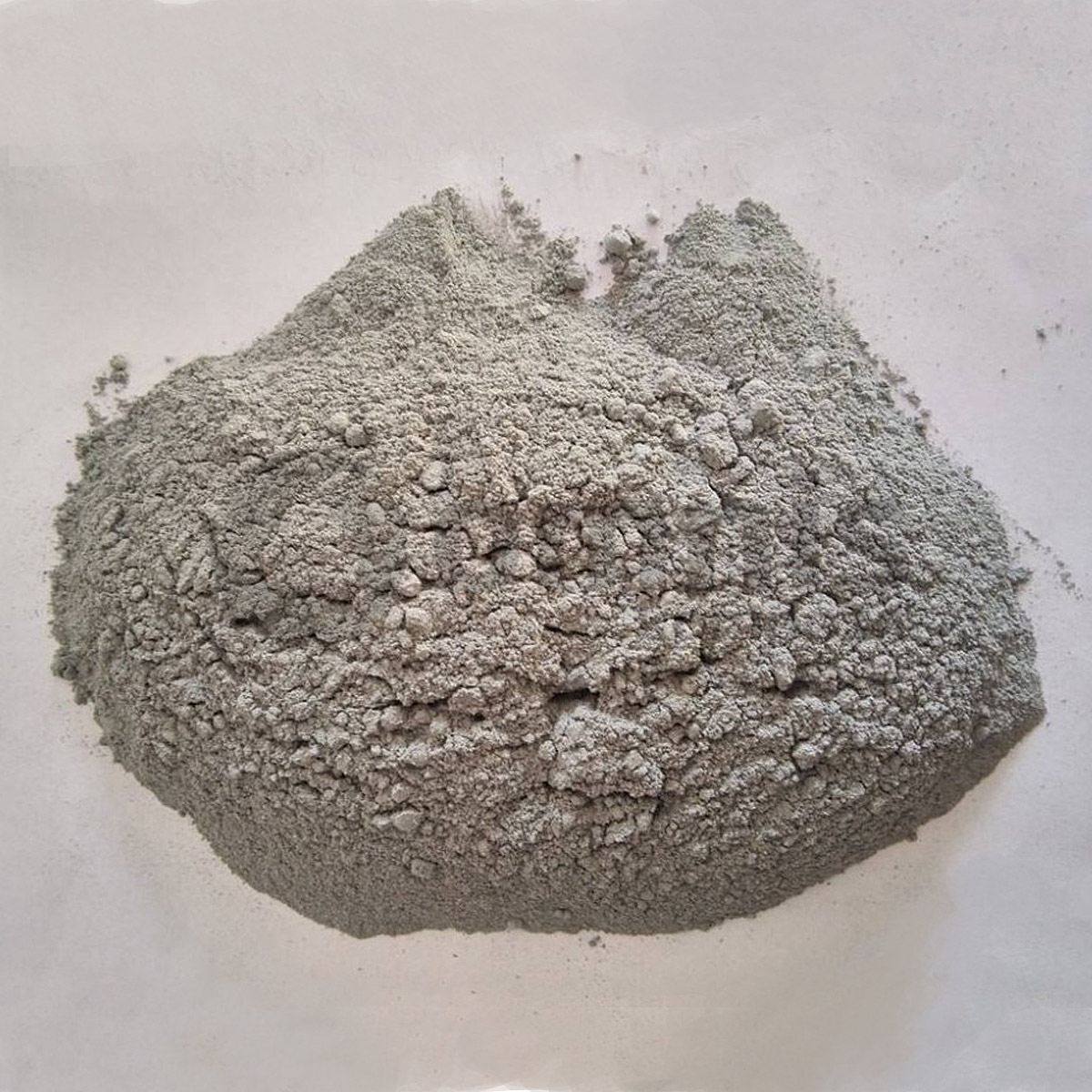
Micro Silica-Silica Ash-Fume
Review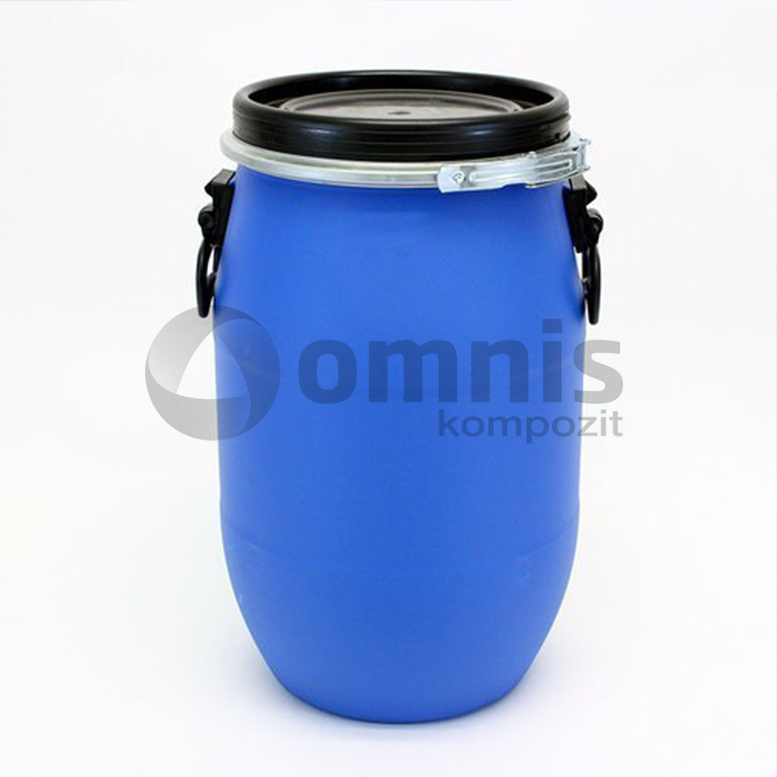
Mold Release Agent for Concrete Applications
Review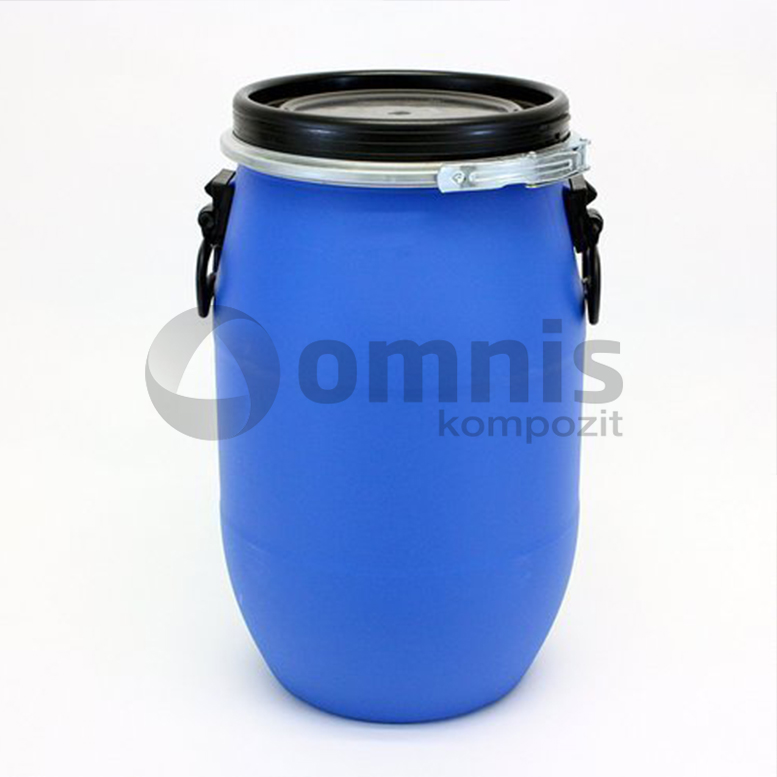
Concrete Plasticizer
Review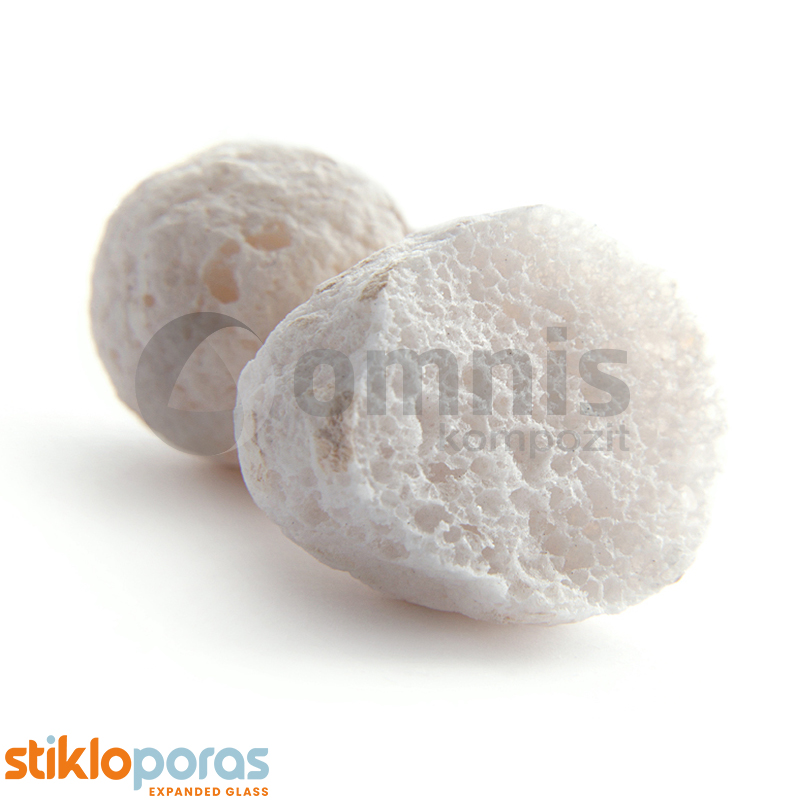
Stikloporas Expanded Glass
Review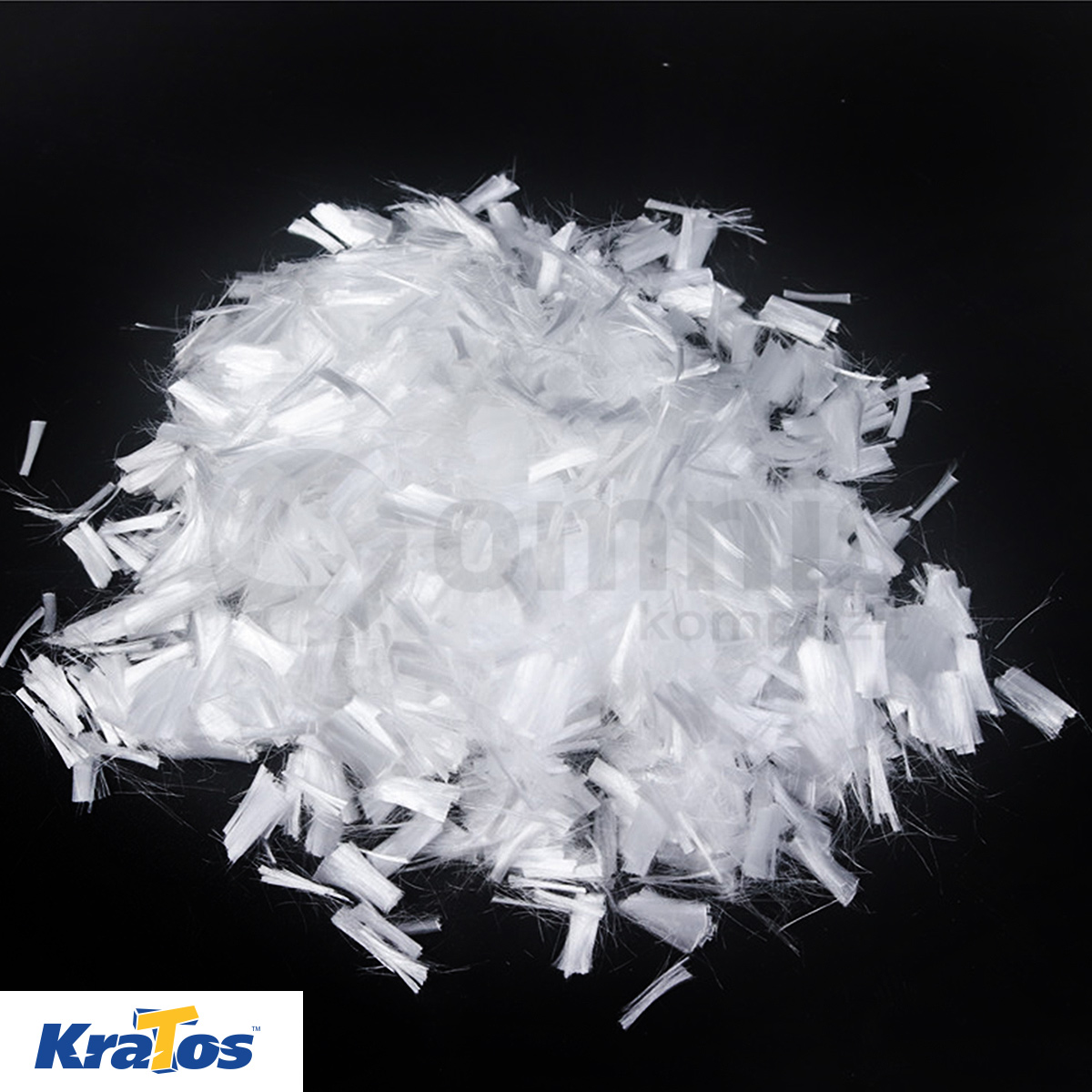
Micro Synthetic Polymer Based Fiber
Review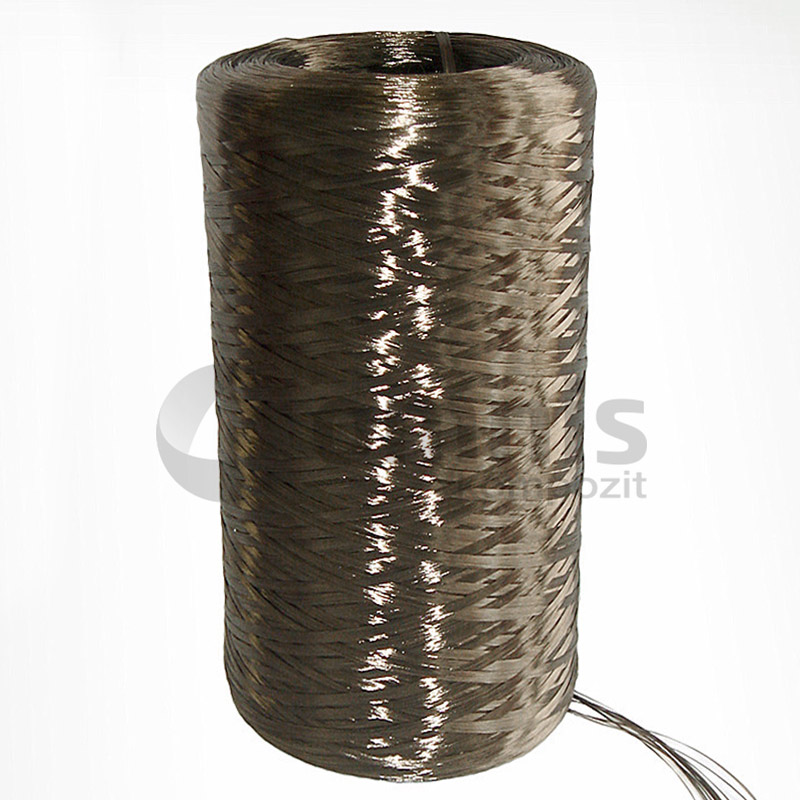
Basalt Single End Roving
Review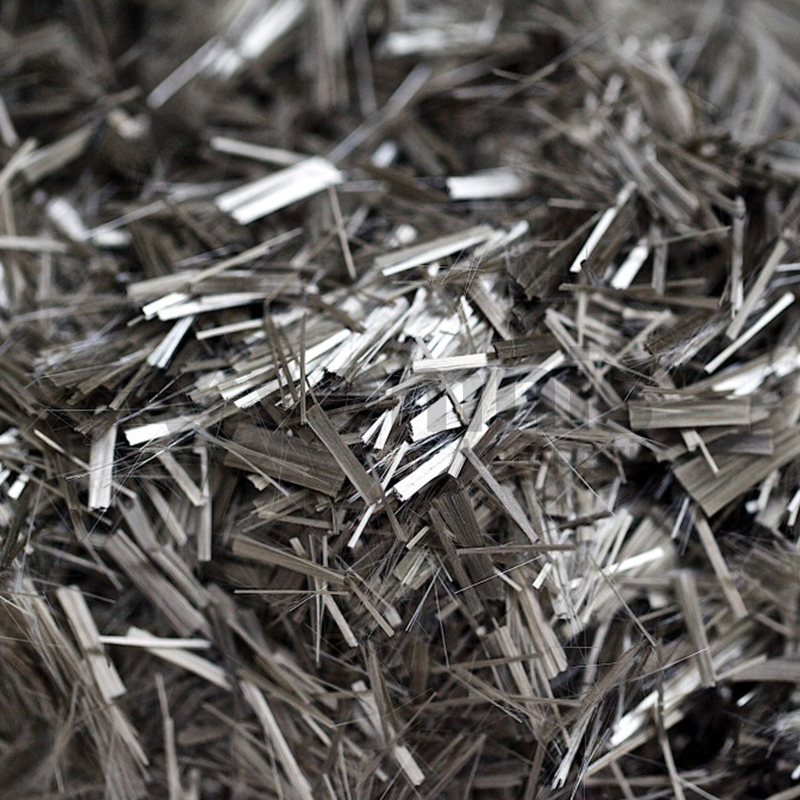
Basalt Fiber Trimming
Review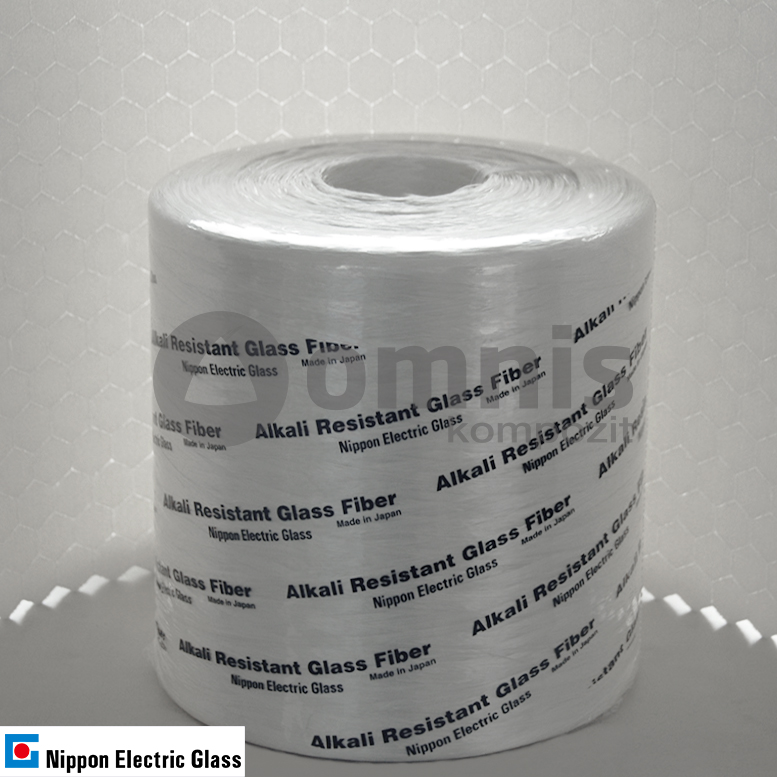
AR Glass Fiber Roving with High ZrO₂ Ratio
Review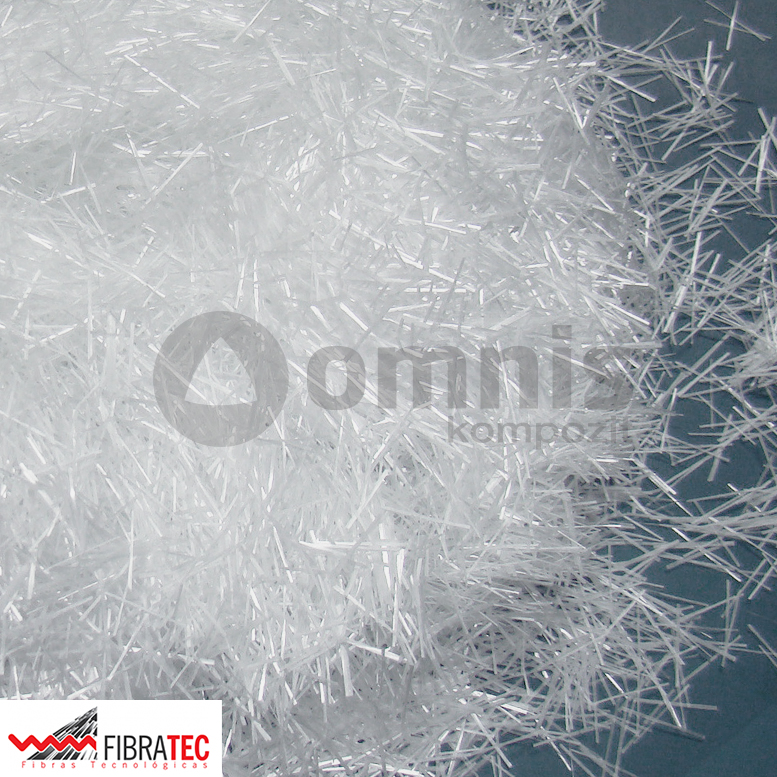
FibraTec V12 Trimming AR Glass Fiber
Review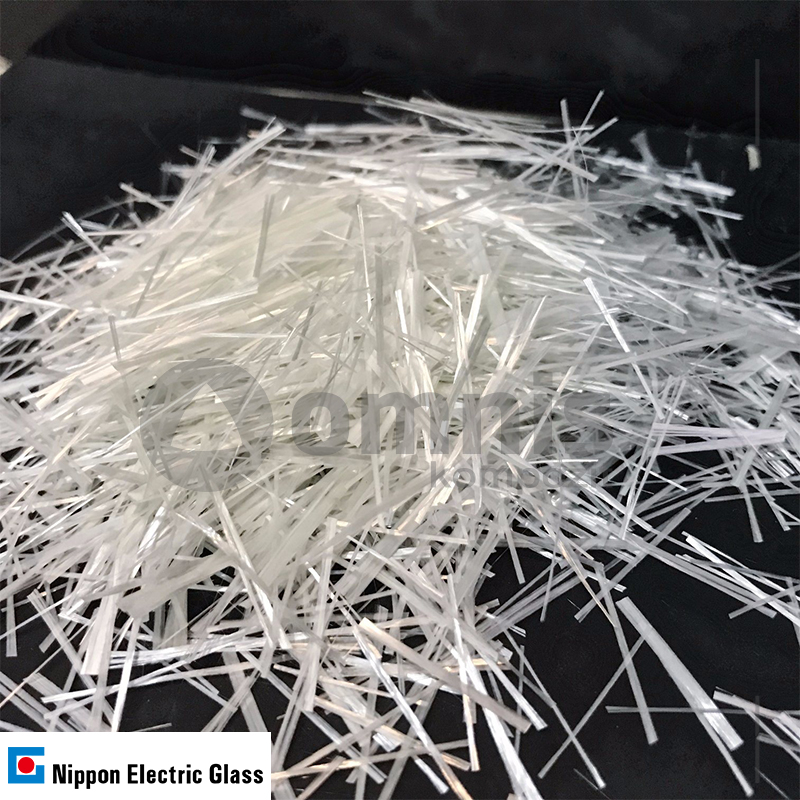
High ZrO₂ Ratio AR Glass Fiber Trimming
ReviewWhat is Glass Reinforced Concrete (GRC) and how is it used?
Glass Reinforced Concrete (GRC) is a composite material made by combining cement, fine aggregates, water, chemical admixtures, and alkali-resistant (AR) glass fibers. GRC is renowned for its versatility, durability, and lightweight properties, making it an ideal choice for a wide range of architectural and decorative applications. It is commonly used in facade panels, architectural cladding, landscaping elements, and ornamental features. The inclusion of glass fibers enhances the strength and durability of the concrete, allowing for thinner, lighter panels without sacrificing structural integrity. GRC material opens up new possibilities for innovative designs in construction, providing an efficient and aesthetically pleasing alternative to traditional concrete and masonry.
How do concrete additives improve the properties of concrete?
Concrete additives play a pivotal role in enhancing the properties of concrete, making it more suitable for a variety of construction applications. These additives can improve the workability of fresh concrete, making it easier to mix, place, and finish. They also enhance the strength and durability of hardened concrete, increasing its resistance to wear, chemical attack, and environmental damage. Additives such as accelerators and retarders can modify the setting time to suit specific project needs, while others like air-entraining agents improve frost resistance. By carefully selecting and dosing concrete additives, constructors can achieve desired concrete properties, ensuring the longevity and performance of the structure.
What are the benefits of using GRC material in construction?
The benefits of using GRC material in construction are manifold. GRC offers exceptional strength and durability while being significantly lighter than traditional concrete, reducing the load on structures and enabling more ambitious architectural designs. Its adaptability to various shapes and textures allows for creative freedom in facade and decorative elements. GRC is also resistant to weathering, corrosion, and fire, ensuring long-term performance with minimal maintenance. Additionally, the energy-efficient production process and potential for recycling contribute to its sustainability profile. By incorporating GRC material, construction projects can achieve a balance between aesthetic appeal, structural integrity, and environmental responsibility.
How do plasticizers work in concrete?
Plasticizers in concrete work by reducing the water content needed to achieve a certain level of workability, thereby increasing the concrete’s strength and durability without compromising its flowability. These additives achieve this by dispersing the particles within the cement, improving its packing efficiency and allowing for smoother consolidation. The use of plasticizers is particularly beneficial in high-strength and high-performance concrete applications, where maintaining workability while reducing the water-to-cement ratio is crucial. By facilitating the production of more cohesive and less permeable concrete, plasticizers contribute to the longevity and resilience of concrete structures.
What role do acrylic polymers play in concrete additives?
Acrylic polymers serve as an important component in concrete additives, enhancing the concrete’s physical properties and performance. When added to the mix, these polymers form a flexible, cohesive film that binds the concrete components together, improving its tensile strength, adhesion, and resistance to water and chemicals. Acrylic polymers are particularly useful in applications requiring improved durability and finish, such as overlays, repair mortars, and decorative coatings. Their ability to enhance the concrete’s resistance to environmental stressors makes them an invaluable tool in extending the lifespan and aesthetics of concrete structures.
Can concrete additives be used in all types of concrete mixes?
Concrete additives can be used in virtually all types of concrete mixes, provided they are selected and dosed appropriately for the specific application. The compatibility of additives with the concrete components, desired properties, and environmental conditions must be carefully considered to ensure optimal performance. Whether it’s for high-strength structural concrete, lightweight architectural elements, or durable pavement, there is a wide range of additives designed to meet the unique requirements of different concrete mixes. Consulting with material specialists and adhering to manufacturer guidelines is crucial in maximizing the benefits of concrete additives in any project.
What are the environmental impacts of using concrete additives?
The environmental impacts of using concrete additives vary depending on the type of additive and its application. Many modern additives are designed with sustainability in mind, aiming to reduce the carbon footprint of concrete production by enhancing the material’s performance and longevity. For instance, additives that reduce the water-cement ratio can lower energy consumption and CO2 emissions associated with cement production. However, some additives may contain chemicals that require careful handling and disposal to prevent potential environmental harm. The selection of eco-friendly and responsibly sourced additives is key to minimizing the environmental impact of concrete construction.
How do GRC materials compare to traditional concrete in terms of strength?
GRC materials offer superior strength compared to traditional concrete, primarily due to the incorporation of alkali-resistant glass fibers. These fibers provide reinforcement within the concrete matrix, significantly enhancing its tensile and flexural strength. This allows GRC to achieve higher performance with thinner and lighter sections, making it an ideal choice for a wide range of applications where traditional concrete’s weight and bulkiness are limiting factors. The enhanced strength of GRC materials not only supports innovative architectural designs but also contributes to the durability and longevity of the structures.
What are the most common types of concrete additives and their uses?
The most common types of concrete additives include plasticizers, which improve workability; superplasticizers, for high workability without increasing water content; accelerators, which speed up the curing process; retarders, to delay setting time; air-entraining agents, which improve frost resistance; and fibers, which enhance tensile strength and crack resistance. Each type of additive is designed to address specific challenges in concrete construction, enabling customized solutions for enhanced performance, durability, and aesthetic appeal of concrete structures.
How can GRC material contribute to sustainable construction practices?
GRC material contributes to sustainable construction practices through its lightweight nature, reducing the overall load on structures and enabling more efficient use of materials. Its durability and resistance to environmental factors minimize the need for maintenance and replacement, extending the lifespan of buildings and reducing waste. Additionally, the production of GRC typically requires less energy and raw materials compared to traditional concrete, further lowering its environmental impact. By incorporating GRC into construction projects, developers can achieve not only innovative and aesthetically pleasing designs but also environmentally responsible outcomes.
What precautions should be taken when using concrete additives?
When using concrete additives, it’s important to follow safety guidelines and manufacturer instructions to ensure proper handling and application. Precautions include wearing appropriate personal protective equipment, avoiding direct contact with skin and eyes, and ensuring adequate ventilation when mixing and applying additives. It’s also crucial to accurately measure and mix additives to avoid compromising the concrete’s properties. Consulting with experts and conducting trial mixes can help optimize the performance of concrete additives while maintaining safety and environmental standards.
How does the addition of plasticizers affect the curing time of concrete?
The addition of plasticizers does not directly affect the curing time of concrete. Their primary function is to improve workability and reduce the water-cement ratio without impacting the setting time. However, the overall curing process may be indirectly influenced by the improved density and homogeneity of the concrete mix, which can enhance hydration efficiency and potentially lead to a more uniform and effective curing. It’s essential to monitor the concrete’s behavior with plasticizers and adjust curing practices as needed to ensure optimal strength development and durability.
Can acrylic polymers be used in outdoor concrete applications?
Yes, acrylic polymers can be used in outdoor concrete applications. They are particularly valued for their ability to improve the concrete’s durability, water resistance, and aesthetic finish, making them suitable for outdoor environments. Acrylic polymers enhance the concrete’s resistance to UV radiation, temperature fluctuations, and moisture, which are critical factors in outdoor applications. Whether used in decorative overlays, protective coatings, or repair mortars, acrylic polymers contribute to the longevity and visual appeal of outdoor concrete structures, ensuring they withstand the elements effectively.