Breather Fabric
Breather fabric, an essential component (consumeable) in the composite manufacturing industry, is ingeniously designed to facilitate uniform air flow and ensure optimal resin distribution during the vacuum bagging and infusion process. This innovative material, characterized by its unique structure, allows for the escape of excess air and volatiles, thereby preventing defects and ensuring a high-quality finish on composite products. When choosing the right product, manufacturers and craftsmen can confidently expect a material that significantly enhances the efficiency and effectiveness of their vacuum bagging operations. It’s essential role in composite manufacturing cannot be overstated, making it an indispensable tool for achieving superior results.
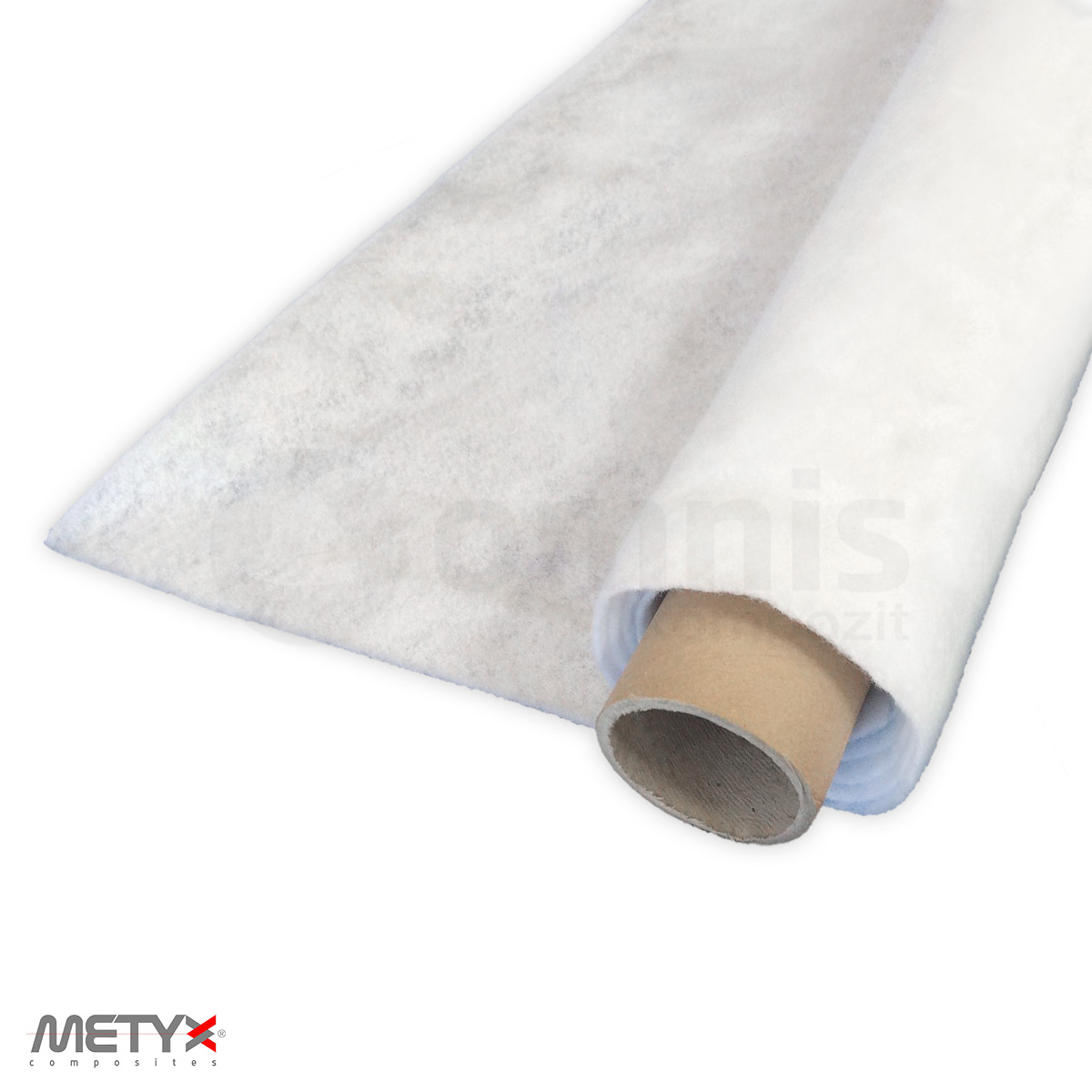
Vacuum Seal
ReviewHow does breather fabric work in vacuum bagging processes?
In the sophisticated realm of vacuum bagging, breather fabric plays a crucial role by acting as a conduit for excess air and volatiles to escape from the laminate. Its function is twofold: it aids in creating an even vacuum pressure across the workpiece and facilitates the optimal flow and curing of resin. By doing so, it ensures that air pockets and resin-rich areas are minimized, leading to a uniform and flawlessly consolidated composite structure. This enhances the integrity and mechanical properties of the final product, making it a key player in the success of vacuum bagging processes.
What are the main functions of breather fabric in composite manufacturing?
In composite manufacturing, this type of fabric serves several vital functions. Primarily, it ensures the even distribution of vacuum pressure, which is essential for the removal of excess resin and air, preventing the formation of voids and ensuring a compact laminate. Additionally, it absorbs excess resin, preventing defects and contributing to a high-quality surface finish. Its role in facilitating the efficient use of materials and enhancing the mechanical properties of the final product makes it an ideal asset in composite manufacturing processes.
Can breather fabric be used with all types of resin systems?
Breather fabric is remarkably versatile and compatible with a wide range of resin systems used in composite manufacturing. Its design allows it to function effectively across various resin types, including epoxy, polyester, and vinylester, ensuring the efficient removal of excess air and volatiles during the curing process. This compatibility enhances the flexibility of manufacturing processes, allowing producers to achieve excellent results with different materials. When selecting breather fabric, it is crucial to consider the specific requirements of the resin system to ensure optimal performance and outcomes.
How do I choose the right breather fabric for my application?
Selecting the right product involves considering several key factors, including the type of resin system, the complexity of the mold, and the desired finish of the composite product. It is important to choose a breather fabric that matches the thermal and chemical resistance required for the specific application. Additionally, the fabric’s porosity and permeability should be suited to the vacuum bagging process to ensure efficient air removal and resin flow. Consulting with experts or suppliers can provide valuable guidance in making an informed choice that meets the unique needs of your application.
Is breather fabric reusable or disposable?
Breather fabric is primarily designed as a disposable material, intended for single use to ensure the highest level of efficiency and cleanliness in composite manufacturing processes. Using fresh breather fabric for each project guarantees optimal air flow and resin absorption, contributing to the quality and integrity of the final product. While some high-grade fabrics may offer limited reusability under specific conditions, it is generally recommended to use new fabric for each application to maintain the best possible outcomes.
How does breather fabric contribute to the quality of the final composite product?
Breather fabric plays a pivotal role in enhancing the quality of the final composite product by ensuring uniform compaction and resin distribution throughout the laminate. Its ability to effectively remove trapped air and volatiles during the curing process results in a denser, more uniform material with fewer defects such as voids or dry spots. This contributes to improved structural integrity and surface finish, ultimately leading to a superior composite product that meets stringent quality standards.
Can breather fabric be used in high-temperature curing processes?
This type of fabric is engineered to withstand various curing temperatures, making it suitable for high-temperature curing processes commonly used in composite manufacturing. High-performance breather fabrics are specifically designed to maintain their structural integrity and functionality under elevated temperatures, ensuring effective air and volatile removal without degrading. When selecting fabric for high-temperature applications, it is crucial to ensure that it is rated for the specific temperature range of the curing process to achieve optimal results.
What are the differences between breather fabric and other vacuum bagging materials?
It distinguishes itself from other vacuum bagging materials through its unique ability to allow air and volatiles to pass through while absorbing excess resin. Unlike vacuum bag films that create the sealed environment or release films that prevent the laminate from sticking to the bag, this type of fabric ensures uniform pressure distribution and facilitates resin flow. Its specific function and material properties make it a crucial component in the vacuum bagging process, complementing other materials to achieve a high-quality composite product.
How do you properly install breather fabric in a vacuum bagging setup?
Proper installation of breather fabric in a vacuum bagging setup is key to its effectiveness. It should be strategically placed over the entire surface of the laminate within the vacuum bag, ensuring no areas are left uncovered to achieve uniform pressure and resin distribution. The fabric must not block any vacuum ports or resin infusion lines, allowing for efficient removal of air and resin flow. Careful placement and securing of the fabric can prevent wrinkles or folds that might impede its functionality, ensuring a successful vacuum bagging process.
What are the key considerations for storing breather fabric?
Storing breather fabric properly is essential to maintain its quality and functionality. It should be kept in a clean, dry environment to prevent contamination or moisture absorption, which could affect its performance. The fabric should be stored flat or neatly rolled, avoiding creases or folds that could impair its uniformity. Additionally, it is important to protect the fabric from direct sunlight and extreme temperatures to preserve its structural integrity and performance capabilities.
Are there different types of breather fabrics for specific applications?
Yes, there are various types designed to meet the diverse needs of specific applications in composite manufacturing. These fabrics differ in their grammage g/m2, porosity, permeability, and thermal resistance, making them suitable for different resin systems and curing processes. High-temperature breather fabrics are available for applications requiring elevated curing temperatures, while fabrics with different weights and thicknesses are designed to accommodate varying degrees of resin absorption and pressure distribution. Selecting the appropriate type of fabric is crucial for achieving the desired outcomes in any given application.
How does breather fabric affect the overall vacuum pressure and compaction?
It plays a critical role in optimizing the overall vacuum pressure and compaction of the laminate during the vacuum bagging process. By ensuring the even distribution of vacuum pressure across the entire surface of the workpiece, it helps achieve uniform compaction and resin flow. This results in a denser, more consistent laminate structure with improved mechanical properties. The fabric’s ability to facilitate air and volatile removal further enhances the compaction process, contributing to the quality and integrity of the final composite product.
Can breather fabric be cut or shaped to fit specific molds or parts?
It is designed to be easily cut or shaped to fit the contours of specific molds or parts, allowing for versatile use in composite manufacturing. Its flexibility and adaptability make it an ideal choice for projects with complex geometries or intricate designs. Properly fitting the breather fabric ensures that vacuum pressure is uniformly distributed and that resin flow is optimized, leading to a successful and efficient manufacturing process.