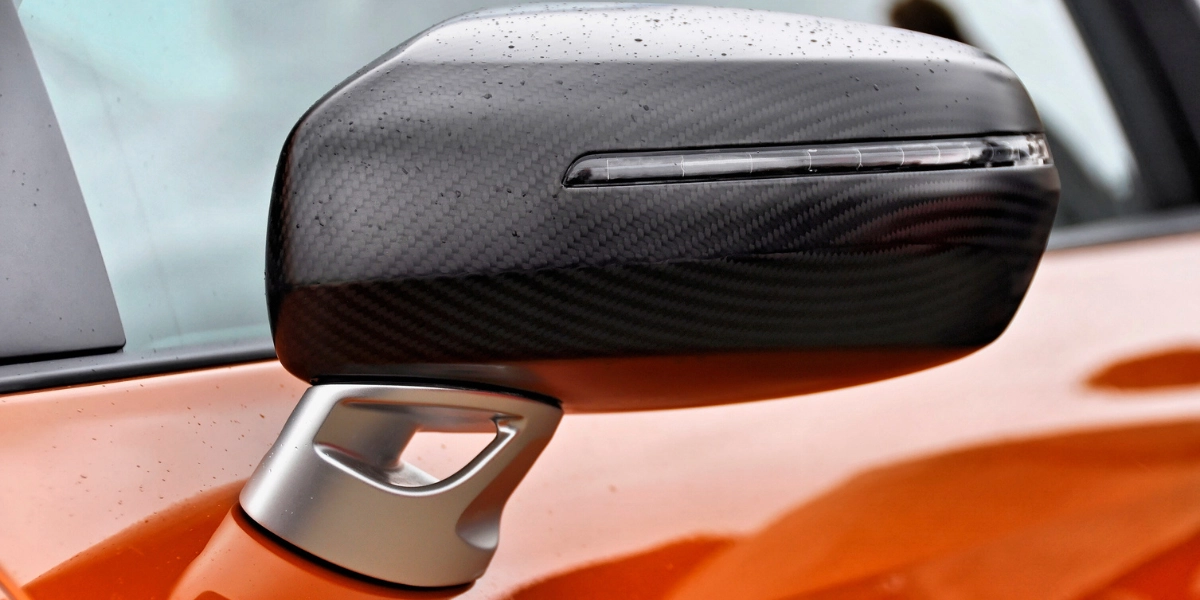
- Blog
- 23 May 2025
What is Composite Tooling?
In today’s advanced manufacturing world, making strong and lightweight parts is more important than ever. Composite tooling plays a key role in this process, especially when working with materials like carbon fiber and fiberglass. These special tools, such as molds and patterns, are used to shape composite parts with high precision and repeatability. They are essential in industries like aerospace, automotive, and wind energy, where performance and durability matter most. As composite manufacturing processes continue to evolve, understanding the role and types of composite tooling helps engineers, technicians, and product designers choose the best solutions for their needs.
Understanding Composite Tooling
Composite tooling refers to the specialized molds, fixtures, and forms used to create composite parts. These tools help shape materials like carbon fiber or glass fiber into strong, lightweight components. The quality of the tooling directly affects the final product’s surface finish, strength, and dimensional accuracy. For this reason, selecting the right tooling is a critical step in the prepreg production process, where layers of resin-impregnated fabric are laid into the mold and then cured.
In composite part production, the tooling must withstand high pressure and temperature, especially when using a composite autoclave, which applies heat and pressure to cure the material. This makes it essential for the tooling to be durable, thermally stable, and precisely designed to match the part geometry.
Because composite materials are sensitive to how they are shaped and cured, tooling must also ensure uniform distribution of heat and resin flow. Whether it’s for making a prototype or full-scale production, understanding the role of composite tooling helps improve quality and reduce costs.
Types of Composite Tooling
Composite tooling comes in different forms depending on the stage of production and the desired part quality. Choosing the right type of tooling depends on factors like budget, production volume, and the specific composite manufacturing processes being used. Below are the main categories of tooling used in the industry.
Soft Tooling (e.g., Prototype Molds)
Soft tooling is typically made from low-cost materials such as foam, wood, or low-temperature resins. It is mainly used for prototypes, short-run parts, or design validation. These tools are faster and cheaper to produce, making them ideal when a quick turnaround is needed. However, soft tooling is not designed for high-pressure or high-temperature environments and may wear out after a few uses.
This type of tooling is often used during early testing stages before moving on to hard tooling for full production. It’s also helpful for checking part fit, making design changes, or preparing for resin transfer molding, where the shape of the mold plays a key role in resin flow.
Hard Tooling (e.g., Production-Grade Molds)
Hard tooling is used for large-scale or long-term production. These molds are made from strong, durable materials like metal or high-temperature composite blocks. They are designed to handle repeated exposure to heat, pressure, and chemicals, often in a composite autoclave environment.
Because hard tooling can produce hundreds or even thousands of consistent parts, it is a preferred choice for industries like aerospace, where precision and repeatability are critical. While hard tooling has a higher initial cost, it offers long-term savings through improved efficiency and part quality.
Reusable vs. Disposable Tooling
Composite tooling can also be divided into reusable and disposable categories. Reusable tooling is designed to last for many cycles, offering cost efficiency over time. It is most commonly used with hard tooling materials. Disposable tooling, on the other hand, is typically used once and then discarded. It is useful for complex shapes, one-off builds, or parts that are hard to remove from traditional molds.
Disposable tooling can save time on mold release and cleaning steps, especially in projects with tight deadlines. However, it may not offer the same accuracy and surface finish as reusable options. Understanding when to use each type helps optimize time, budget, and part performance.
Benefits of Composite Tooling
Composite tooling offers several important advantages, especially for industries that need strong, lightweight, and high-precision parts. One of the biggest benefits is design flexibility. Composite tools can be shaped into almost any form, which allows engineers and designers to create complex geometries that are difficult to achieve with metal tools.
Another key benefit is weight. Compared to traditional metal tooling, composite tools are much lighter, which makes them easier to handle, transport, and install. This is especially helpful in large-scale applications like wind turbine blades or aircraft panels, where the molds themselves can be very large.
Durability is also a strong point. High-quality composite tools can handle repeated cycles of heating and cooling, making them suitable for curing processes such as resin transfer molding. They also resist corrosion and do not rust like metal tools, reducing maintenance needs over time.
When used properly, composite tooling improves surface finish, reduces part defects, and lowers material waste. This leads to faster production and better part quality, making it a cost-effective choice for both small and large-scale manufacturing. Whether you’re working with hand lay-up, vacuum bagging, or prepreg production processes, composite tooling helps ensure consistent, reliable results.
Challenges and Limitations
While composite tooling offers many advantages, it also comes with certain challenges. One of the main issues is the high upfront cost for hard tooling. Producing durable molds with precise tolerances takes time and skilled labor, which may not be ideal for low-volume runs.
Another limitation is the sensitivity of composite materials to temperature and pressure. If the tooling is not properly designed or maintained, it can cause defects in the final part. Also, some tooling materials may degrade over time when exposed to repeated thermal cycles in a composite autoclave.
Repairing damaged composite tools can be complex, and in some cases, complete replacement may be necessary. That’s why proper design, usage, and storage are key to maximizing tool life and maintaining part quality.
Composite tooling is a powerful solution in modern manufacturing, especially when precision, durability, and lightweight performance are essential. By understanding the types, benefits, and limitations of this technology, engineers and manufacturers can make better decisions for their projects. Whether it’s for prototypes or full-scale production, investing in the right composite tooling helps improve efficiency, reduce waste, and ensure consistent part quality across different composite manufacturing processes.