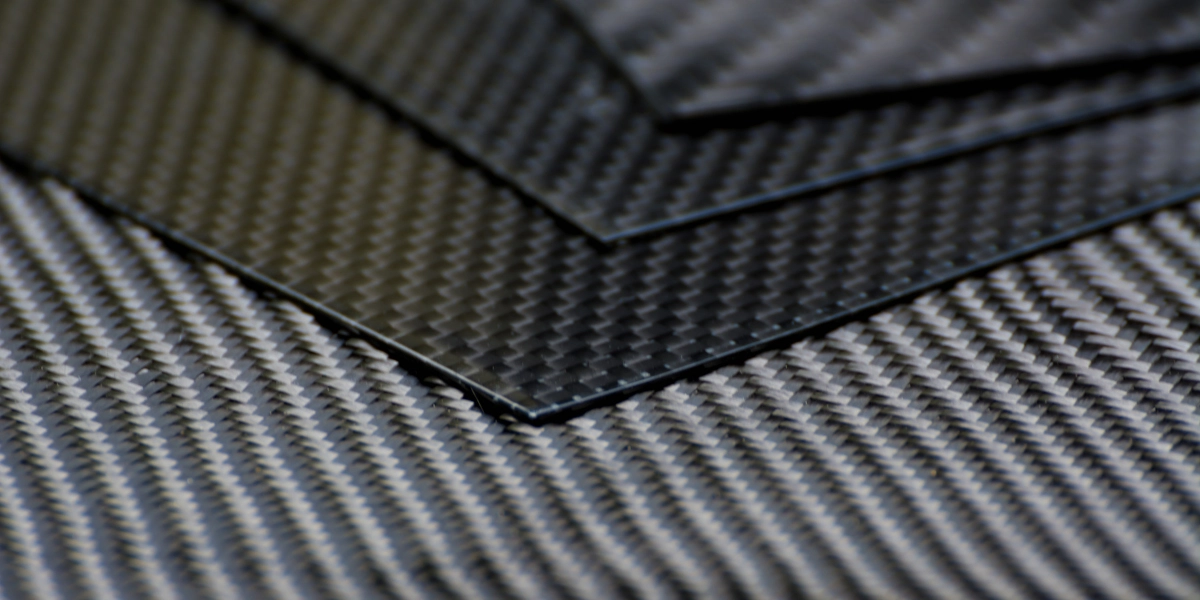
- Blog
- 10 Jul 2025
What is Composite Density and How is it Measured?
Composite materials are used in many fields due to their lightweight structure and high strength. One important physical property that helps define their performance is composite density—the mass of a composite material per unit volume. This value gives insight into how a material will behave under load, during movement, or in various environmental conditions. It also plays a key role in determining material efficiency and suitability for specific applications. In addition, composite density is closely related to the thermal properties of composite materials, especially when temperature stability and heat resistance are required. Understanding density is essential for accurate material selection, reliable design, and long-term durability.
Introduction to Composite Density
Composite density is a basic but important property that defines how much mass a composite material contains in a given volume. It is not a fixed value, as it depends on the densities and volume ratios of the matrix and reinforcement materials used in the structure. In fiber-reinforced composites, for example, the density will vary depending on whether glass, carbon, or aramid fibers are used, and how much of each is present. Since composite materials are designed for specific mechanical, thermal, or structural needs, their density plays a key role in predicting overall performance. It also provides a reference point when comparing different materials during composite testing processes.
Factors That Influence Composite Density
Composite density is influenced by a range of factors that come from both the material composition and the manufacturing process. The first major factor is the type of matrix and reinforcement used. Each material has its own inherent density—for example, epoxy resins are typically lighter than polyester resins, and carbon fibers are lighter but stronger than glass fibers. When these are combined, the proportion of each (known as volume fraction) directly affects the final density. A higher fiber volume fraction usually leads to a denser and stronger composite, but also increases weight.
Another important factor is the distribution and orientation of the fibers. In unidirectional composites, where fibers are aligned in a single direction, density may differ from that in woven or randomly oriented structures due to differences in packing efficiency. The presence of voids, air pockets, or incomplete wetting between the matrix and fibers during manufacturing can reduce density and negatively impact performance. Process parameters such as pressure, temperature, and curing time can influence the occurrence of these defects.
Additives and fillers—used to improve fire resistance, conductivity, or surface finish—also contribute to density. Even small amounts can cause measurable changes, especially in high-precision applications. In hybrid composites, where different types of reinforcements or matrices are used together, the density becomes a weighted result of all components involved. These systems require more complex calculations and careful material selection to ensure the desired balance between weight and performance is achieved.
How Is Composite Density Measured?
The density of a composite material can be determined in two main ways: through theoretical calculation and experimental testing. Each method has its own purpose and level of accuracy. Theoretical methods are useful in the design stage to estimate density based on known values, while experimental methods provide real results after the material is produced. Comparing both helps evaluate manufacturing quality and material performance.
Theoretical Density Calculation (Rule of Mixtures)
The most common way to estimate composite density theoretically is by using the Rule of Mixtures. This method calculates the expected density based on the individual densities and volume fractions of the matrix and reinforcement materials. The formula is:
ρc = ρf × Vf + ρm × Vm
Where:
- ρc = composite density
- ρf = fiber density
- Vf = fiber volume fraction
- ρm = matrix density
- Vm = matrix volume fraction
This calculation assumes perfect bonding and no voids in the material. While it is helpful for early-stage material selection and design, real-world deviations during manufacturing can lead to differences between theoretical and actual values.
Experimental Methods
Experimental measurement provides the actual density of a manufactured composite. One common method is the Archimedes principle, where the specimen is weighed in air and in a liquid (usually water) to calculate its volume, and then its density. This technique is simple, low-cost, and widely used for solid composites.
Another method is pycnometry, which uses a gas or liquid displacement approach for more accurate volume measurements, especially useful for porous materials. Advanced techniques like X-ray computed tomography (CT) can also reveal internal structure and voids, offering precise insights not only into density but also into the quality of the composite.
Comparison Between Theoretical and Actual Density
The difference between theoretical and actual density reveals important details about the composite’s quality. If the actual density is lower than the theoretical value, it may indicate the presence of voids, poor fiber wetting, or manufacturing defects. On the other hand, if the values are very close, it suggests that the material has been well-processed with minimal air gaps and accurate material proportions. This comparison is often part of composite testing, especially in applications where mechanical performance and reliability are critical.
Importance of Density in Composite Design
Density plays a critical role in composite design, as it directly affects the weight, strength-to-weight ratio, and overall performance of the final product. In structural applications, selecting a composite with the right density helps achieve optimal mechanical properties without unnecessary weight. For example, in aerospace or automotive components, lower density materials are preferred to reduce energy consumption and improve efficiency, while still maintaining structural integrity. In contrast, certain applications may require higher density for added durability or impact resistance.
Composite density also influences thermal conductivity, vibration behavior, and ease of processing. During the design phase, density must be carefully balanced with other properties like stiffness, strength, and cost. In the case of hybrid composites, where multiple materials are combined, managing density becomes even more important to ensure uniform performance and avoid stress concentrations. As a result, understanding and controlling composite density is essential for reliable, efficient, and application-specific material design.