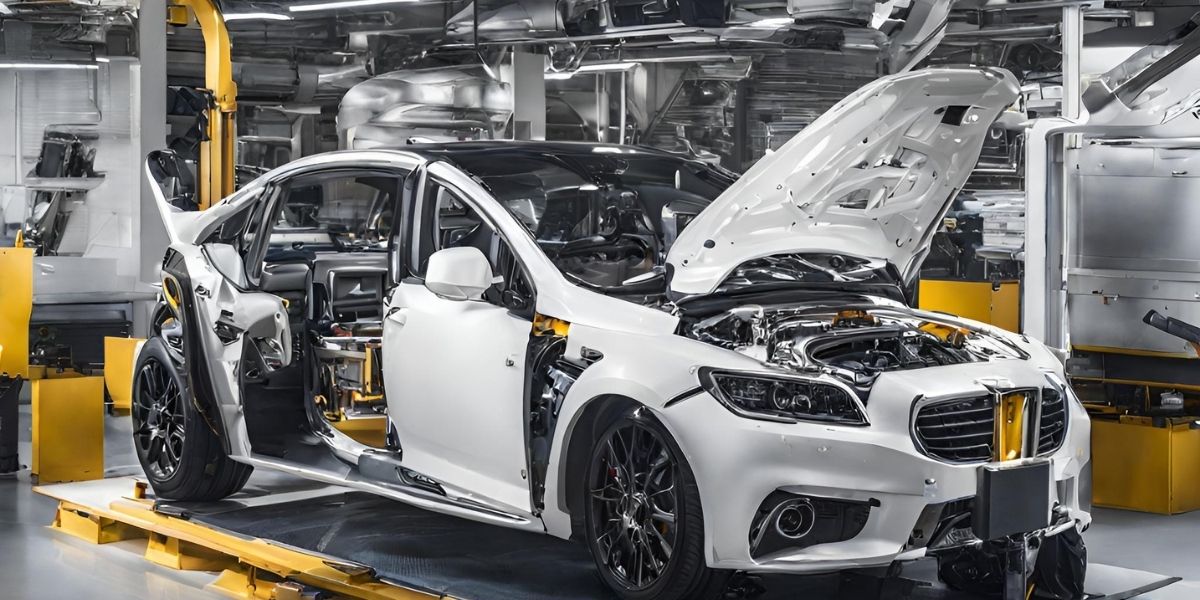
- Technical Bulletin
- 25 Oct 2023
Poliya Products Used in Automotive Composite Applications
Composite products are used extensively in the automotive industry thanks to their ease of production, smooth appearance and technical capabilities. However, there are many different poly products used in composite applications in the automotive industry. You can find more information about these products in the rest of the article.
Hand Lay Application
Hand lay-up, which is one of the preferred methods due to its wide design options and low initial investment cost, is frequently used for single and large surfaces. The more traditional method of hand lay-up is usually used for low-volume part production. After the mold release agent is applied, poly products are applied and then the glass fiber polyester is applied with a brush or wool roller. As it is a labor-intensive production model, the production capacity of this method varies.
Gelcoat Selection
The most important criterion in gelcoat selection is to determine whether the material meets the needs of the sector in which it will be used. For example, if a body part is to be produced for a transportation vehicle, the choice of gelcoat type depends on whether the part will be repainted after production. The reason for considering this criterion is to ensure that the poliya product is resistant to harsh weather conditions and to ensure that the product adapts to the conditions of the geography in which it will be used.
Lamination
For lamination used in more vertical GRP work, the danger of flowing must be taken into account. At this point, Poliya products such as Polipol 3469-TA-LSE, which are developed especially for production models that are more dependent on human labor, such as hand laying, are preferred. The main objectives of this choice:
- Improving the production environment in terms of human health,
- The product has low styrene emission and rate,
- Thanks to its hybrid structure, it is specially designed for applications with a large surface area and preferably for applications where easier fiber wetting is required.
High HDT
The HDT test, which tests the self-protection rate of the material under high temperature and up to which temperature values it can withstand, is important for the automotive industry. It is essential to use materials that can withstand the heat generated by the combination of air temperature, the temperature of the parts in the vehicle and the speed. In this context, Polipol-344-TA-LSE, one of the frequently used Poliya products, has been produced exactly for this purpose and both mechanical strength and high HDT properties have been approved by the tests conducted by laboratories. This is a Poliya product:
- Formulation that reduces styrene evaporation,
- High mechanical and thermal capacity,
- Easy and good fiber wetting properties,
- Non-flowing structure on vertical surfaces
- It is one of the most frequently used products due to its features such as not allowing regional heating that may arise from resin agglomeration.
Resin Infusion Application
The method of wetting the resin placed dry in the mold with vacuum pressure is called infusion. This application is particularly common in applications such as marine and turbine blades. In the automotive industry, where flat and wide parts are produced, resin infusion is sometimes preferred. In this method, it is as important to use the right consumables as it is to choose the appropriate resin and fiber. Although it cannot be automated in the production phase, the flexibility it provides in terms of mold geometry and size scaling makes it particularly suitable for the production of parts that are planned to be produced in small quantities.
RTM- Resin Transfer Molding
In the RTM Resin Transfer Molding method, two different molds are applied to two different surfaces to obtain a smooth product on both sides. Fibers and other reinforcements suitable for this method are placed between the female and male molds designed for RTM and the mold is closed. Many Poliya products such as Polipol 3382, the high-performance Polijel 213 and Polijel 215 can be used in RTM applications. RTM is a much more serialized method than methods such as hand lay-up and spray-up, but production can be made even more serialized by adding heating and cooling systems to the molds. Low tolerance, less need for labor, reduced styrene emission and high productivity are the advantages of the RTM method, while high mold cost is a disadvantage of RTM. This disadvantage is eliminated in scenarios where the demand for the product is finalized or where it is decided to produce similar products.
RTM ZERO System
When Polipol 321-ZERO and its complementary Polipol 3387-ZERO products are used, the zero pull chain is completed. Poliya 3387-ZERO product starts this chain with its zero shrinkage molded polyester structure and Polipol 3387-ZERO product provides the dimensional standard with a very low linear shrinkage rate without sacrificing mechanical properties. Another advantage of Polipol 3387-ZERO is that it is a polyester that can give a very high surface quality. Thanks to its unique DCPD formula, unlike other DCPD based polyesters, it is suitable for mass production and reduces volumetric shrinkage to theoretically zero.
Color Composites
In some sectors, such as the automotive industry, there is the production of parts that will not be painted afterwards. In such products where aesthetics are at the forefront, gelcoat color and performance are important. Polijel Colored Gelcoat and Polipigment pastes from Poliya products provide advantages for the manufacturer with their reproducibility in terms of color standard and quality. Apart from these advantages, Poliya products can be designed in customizable colors according to the user’s request in UV resistance, hardener system and many other important criteria.
In this article, we have touched upon which poly products can be used in composite applications in the automotive industry, where the part is of critical importance, and which techniques are used during the production phase.