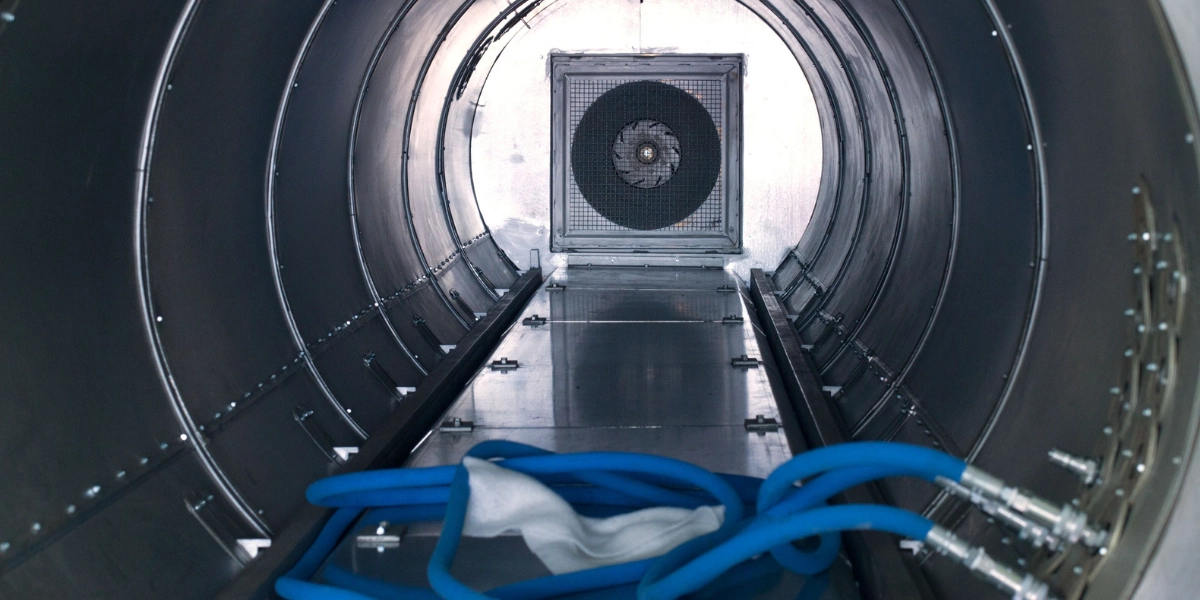
- Blog
- 6 May 2025
Why Out of Autoclave Composite Manufacturing Matters
In recent years, out of autoclave composite manufacturing has emerged as a game-changer in the world of advanced materials. This innovative process offers a more cost-effective and flexible alternative to traditional composite production methods, which often require high-pressure composite autoclave systems. By using controlled heat and pressure outside of an autoclave, manufacturers can achieve high-performance results without the need for expensive and bulky equipment. As industries continue to seek lighter, stronger, and more sustainable materials, the demand for efficient solutions like the prepreg production process and advanced vacuum equipment is rapidly increasing. Whether in aerospace, automotive, or industrial design, this method is helping companies optimize performance while reducing production costs and environmental impact.
What Is Out of Autoclave Composite Manufacturing?
Out of autoclave composite manufacturing (often shortened as OoA) is a method used to produce high-performance composite parts without the use of a traditional autoclave. Instead of relying on high-pressure systems, this process uses controlled heat and vacuum pressure to cure composite materials like prepregs (pre-impregnated fiber reinforcements). The result is a strong, lightweight product that meets demanding structural standards.
This method typically involves placing the prepreg material into a mold, sealing it with a vacuum bag, and curing it in an oven using carefully regulated temperature cycles. During the cure, vacuum equipment removes trapped air and excess resin, ensuring a compact and consistent laminate. While traditional composite autoclave processes offer excellent results, they are expensive, energy-intensive, and limited by part size. OoA manufacturing overcomes these issues by allowing for larger parts and more flexible production setups.
The prepreg production process plays a key role here, as the quality of the prepreg directly affects the final product’s strength, surface finish, and durability. When combined with advanced vacuum systems, out of autoclave methods can deliver composite components that rival autoclave-made parts in performance — at a lower cost and with more scalable production options.
Key Benefits of Out of Autoclave Composite Manufacturing
One of the biggest advantages of out of autoclave composite manufacturing is its ability to produce high-quality composite parts without the need for expensive autoclaves. This significantly reduces both capital investment and operational costs, making it an attractive option for companies looking to scale production or enter the composites market more affordably.
Another key benefit is flexibility in production. Since this method does not rely on large pressure vessels, manufacturers can produce larger or more complex shapes without being limited by autoclave size. This opens up new possibilities for industries like aerospace, automotive, and renewable energy, where lightweight, strong parts are essential.
In terms of energy efficiency, OoA processes consume less power compared to autoclave systems, which need high pressure and heat. This contributes to a lower environmental footprint and aligns with the growing focus on sustainable manufacturing practices.
Also, out of autoclave composite manufacturing makes maintenance and setup simpler. It requires less infrastructure, fewer specialized staff, and offers shorter cycle times in some applications. This can help speed up time to market while still ensuring consistency and reliability in part quality.
Industries Benefiting from Out of Autoclave Technology
Out of autoclave composite manufacturing is being adopted by a wide range of industries that need strong, lightweight materials without the high costs and limitations of autoclave systems. One of the primary sectors leading the way is aerospace. Aircraft manufacturers use this method to produce non-critical structural parts such as fairings, access panels, and interior components. These parts still require excellent mechanical properties and dimensional stability — both of which out of autoclave methods can provide.
In the automotive industry, where reducing vehicle weight is essential for improving fuel efficiency and performance, OoA technology supports the production of custom body panels, structural reinforcements, and even EV battery enclosures. It allows manufacturers to deliver durable and efficient parts without relying on the slower, more expensive composite autoclave approach.
Wind energy and marine industries also benefit. Wind turbine blades and boat hulls often involve large, curved structures that are difficult or impossible to fit in a traditional autoclave. OoA manufacturing allows for more freedom in design and scaling, thanks to flexible tooling and simplified prepreg production process steps.
As the technology continues to evolve, we’re also seeing healthcare, sports, and industrial machinery use this method to create custom, high-strength composite parts quickly and affordably — demonstrating how adaptable and impactful out of autoclave solutions can be across many fields.
Challenges and Considerations in Adopting Out of Autoclave Methods
While out of autoclave composite manufacturing offers many advantages, it’s important to understand the challenges that can come with switching to or implementing this process. One of the main concerns is process control. Without the uniform pressure of a composite autoclave, achieving consistent fiber compaction and void-free laminates requires precise handling of materials, tools, and cure cycles.
Another key factor is the quality of materials, especially prepregs. Since the process relies heavily on resin flow and air evacuation during curing, the prepreg production process must be tightly controlled. Low-quality prepregs or improper storage can lead to weak bonding, surface defects, or uneven curing, all of which can compromise the part’s performance.
Also, to get the best results, manufacturers must use advanced vacuum equipment and ensure proper vacuum bagging techniques. Even a small leak or wrinkle in the vacuum bag can lead to trapped air or inconsistent curing, affecting structural integrity.
There are also design limitations to consider. While out of autoclave methods are great for medium to large parts and non-critical structures, some highly loaded components may still require autoclave-level consolidation and strength. For this reason, engineers need to carefully evaluate whether OoA meets the performance requirements of each application.
Adopting out of autoclave methods involves a learning curve, but with the right equipment, materials, and expertise, it’s a powerful solution for modern composite manufacturing.
The Future of Out of Autoclave Composite Manufacturing
The future of out of autoclave composite manufacturing looks promising as demand grows for lighter, more efficient materials across multiple industries. With ongoing advancements in prepreg technology, resin systems, and oven-based cure processes, OoA methods are closing the performance gap with autoclave-made parts — and in many cases, even surpassing them in terms of cost-effectiveness and scalability.
As manufacturers invest more in automation and digital monitoring tools, out of autoclave processes will become even more consistent and easier to control. Integrated sensors, real-time feedback systems, and smarter vacuum equipment are already helping reduce human error and improve part quality. These innovations are making it easier for companies to adopt OoA methods without compromising on reliability or strength.
Sustainability is another driver. OoA technology supports lower energy use, less waste, and smaller production footprints — making it attractive to companies focused on eco-friendly manufacturing. Combined with more efficient prepreg production processes and recyclable resin systems, it aligns well with future global sustainability goals.
Looking ahead, we can expect wider use of OoA in space exploration, e-mobility, and infrastructure — sectors where performance, weight, and cost matter most. As knowledge and access to the technology grow, out of autoclave composite manufacturing is set to become a standard in advanced composite production, not just an alternative.