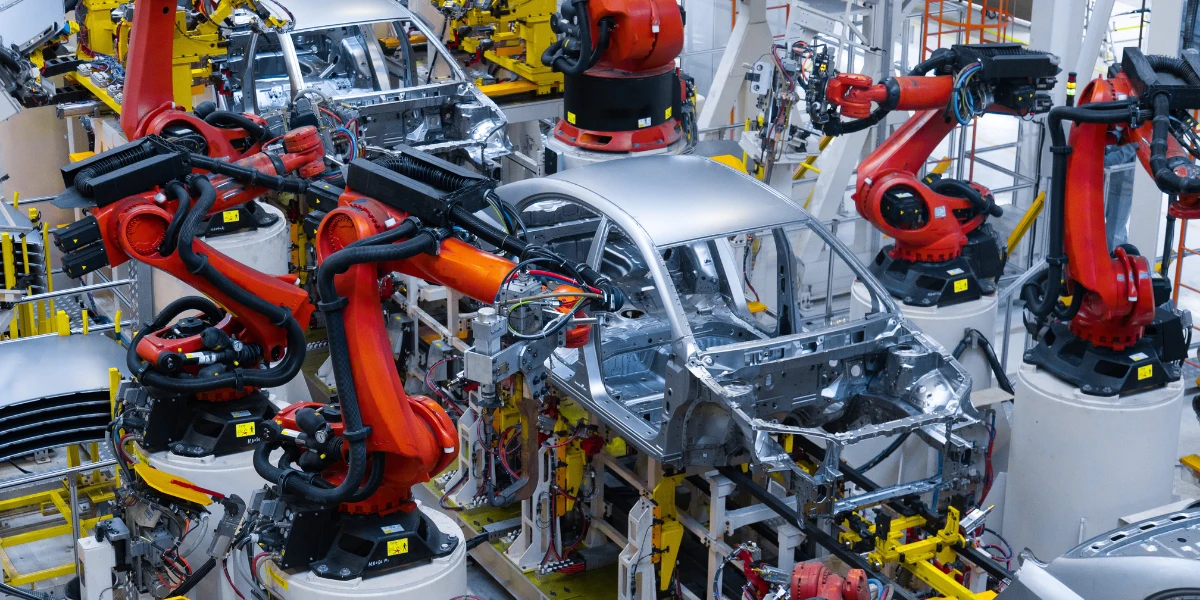
- Blog
- 7 Feb 2025
The Role of Composite Materials in Automotive Industry
Composite materials have revolutionized many industries, and the automotive sector is no exception. Composites in automotive manufacturing are widely used due to their lightweight nature, strength, and design flexibility. These advanced materials play a critical role in improving vehicle performance, safety, and sustainability. In this blog, we will explore what composite materials are, their benefits, key applications, and challenges in the automotive industry.
What Are Composite Materials in Automotive Industry?
Composite materials are engineered substances made by combining two or more different materials, typically a fiber reinforcement (like carbon or glass fibers) and a matrix (such as resin). The result is a material with enhanced properties that surpass those of its individual components.
In the automotive industry, composite materials are used to build parts that need to be strong, durable, and lightweight. These materials are commonly found in both structural and non-structural components of vehicles. Some of the most popular types of composite materials in automotive applications include carbon fiber reinforced polymer (CFRP), glass fiber reinforced polymer (GFRP), and natural fiber composites.
Benefits of Composite Materials in Automotive Manufacturing
The use of composite materials in automotive industry offers several advantages compared to traditional metals like steel and aluminum. These benefits include:
Lightweight Properties and Fuel Efficiency
One of the primary reasons for using composite materials in automotive industry is their lightweight nature. Composites can be up to 50% lighter than steel while maintaining similar strength levels. This reduction in weight directly improves fuel efficiency, as lighter vehicles require less energy to move.
For example, using carbon fiber composites in car bodies can reduce vehicle weight, leading to better mileage and lower carbon emissions. As a result, manufacturers can meet strict fuel efficiency regulations while maintaining high performance.
Enhanced Durability and Safety
Composite materials in automotive industry also enhance vehicle safety and durability. These materials can absorb energy effectively during collisions, helping to protect passengers.
In addition to impact resistance, composites resist corrosion better than metals, making them ideal for long-term use in harsh environments. This durability reduces maintenance costs and extends the vehicle’s lifespan.
Sustainability and Environmental Impact
The environmental benefits of composite materials in automotive industry are significant. Since composites contribute to fuel efficiency, they help lower greenhouse gas emissions. Additionally, some modern composites use recycled fibers or bio-based resins, further reducing the environmental footprint.
The lightweight properties of composites also reduce the need for excessive raw material extraction, making them a sustainable choice for manufacturers focused on eco-friendly production practices.
Applications of Composite Materials in the Automotive Industry
Composite materials are used in a wide range of automotive applications, both for functional and aesthetic purposes. Here are some of the most common areas where composites are used:
Exterior Components
Many composite materials in automotive industry are used for exterior parts due to their ability to withstand harsh weather and mechanical stress. Some examples include:
- Bumpers and fenders
- Hoods and trunk lids
- Body panels and side skirts
These components benefit from the lightweight and corrosion-resistant properties of composites, contributing to better vehicle performance and longevity.
Interior Components
In the interior of vehicles, composite materials in automotive industry provide both functional and aesthetic advantages. Some common uses include:
- Dashboard panels
- Seat structures
- Door panels
The ability to mold composites into complex shapes allows for modern, ergonomic interior designs while maintaining durability.
Structural and Performance Parts
Structural components made from composite materials in automotive industry contribute to vehicle safety and performance. These include:
- Chassis and subframes
- Suspension components
- Brake systems
High-performance vehicles, in particular, benefit from carbon fiber composites due to their exceptional strength-to-weight ratio, improving both speed and handling.
Challenges in the Use of Composite Materials
Despite the numerous benefits, there are some challenges associated with using composite materials in automotive industry:
- Cost: Advanced composites like carbon fiber can be expensive compared to traditional metals.
- Composite Manufacturing Processes: Producing high-quality composite components often requires specialized composite manufacturing processes that can be complex and costly.
- Recycling Limitations: Some composite materials, especially thermoset-based ones, are difficult to recycle.
However, ongoing research is focused on developing cost-effective and recyclable composite options to overcome these challenges.
To sum up, composite materials in automotive industry have transformed the way vehicles are designed and manufactured. Their lightweight nature, durability, and sustainability make them a top choice for modern vehicle production. Although challenges like cost and recycling remain, innovations in composite manufacturing processes continue to drive the industry forward.
As automotive technology evolves, composite materials will play an even greater role in enhancing vehicle efficiency, safety, and sustainability. By embracing these advanced materials, the industry can achieve superior performance while contributing to a greener future.