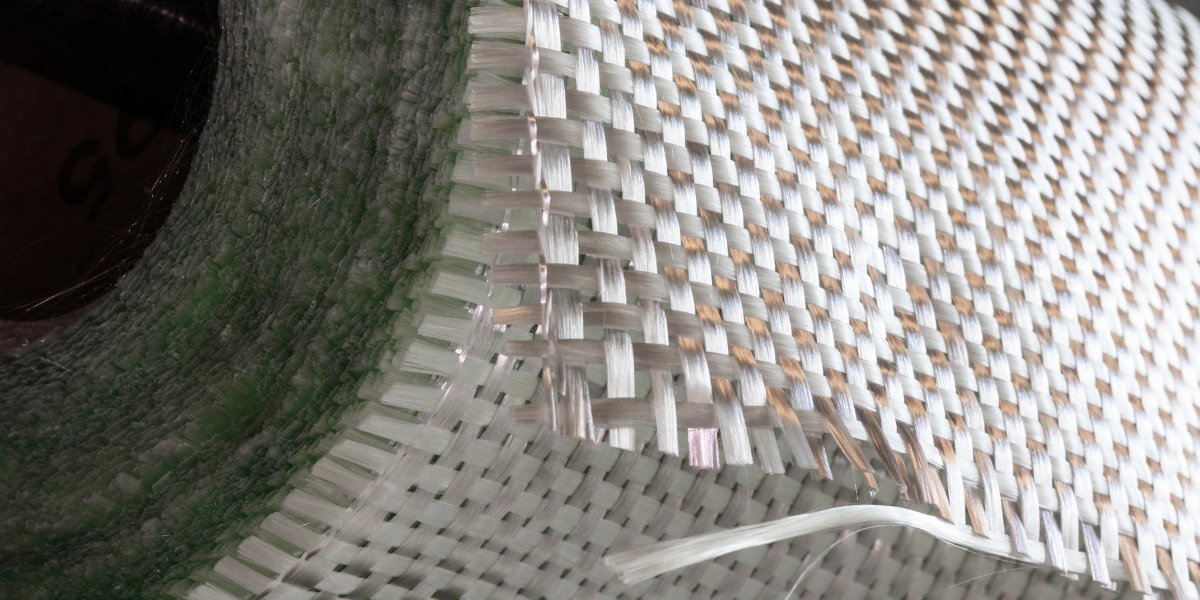
- Blog
- 14 Feb 2025
A Guide to the Classification of Composite Materials
Composite materials are essential in modern industries due to their superior strength, lightweight properties, and versatility. They consist of two or more distinct components, typically a matrix and a reinforcement, that work together to create a stronger, more durable material. Understanding the classification of composite materials helps industries choose the right type for their specific applications, whether it’s aerospace, construction, or automotive engineering.
This guide explores the various categories of composite materials based on matrix type, reinforcement type, and advanced classifications to help you understand their unique benefits.
What is the Classification of Composite Materials?
The classification of composite materials is based on the composition and structure of the components involved. They are primarily categorized by:
- Matrix Type: The material that binds the reinforcement together.
- Reinforcement Type: The structure of the reinforcing phase within the composite.
- Advanced Types: Combinations of standard composites or nanoscale enhancements.
These categories help industries select the most suitable materials for their specific requirements, whether for structural support, thermal resistance, or weight reduction.
Classification of Composite Materials Based on Matrix Type
The matrix material plays a critical role in binding the reinforcement together and protecting it from environmental damage. Here are the primary types:
Polymer Matrix Composites (PMC)
Polymer Matrix Composites (PMC) are the most widely used composite materials, consisting of a polymer resin as the matrix combined with fibers like glass, carbon, or aramid. They are commonly used in composite in construction for applications like reinforcing concrete, roofing panels, and insulation due to their lightweight and corrosion-resistant properties.
PMCs are preferred for industries needing lightweight yet strong materials, such as the automotive and sports equipment sectors.
Metal Matrix Composites (MMC)
Metal Matrix Composites (MMC) use metals like aluminum, magnesium, or titanium as the matrix material. Reinforced with ceramic or metal fibers, they offer enhanced thermal resistance and strength, making them ideal for aerospace and automotive applications.
MMC materials are often used where heat resistance and high mechanical strength are critical, such as in engine components and brake systems.
Ceramic Matrix Composites (CMC)
Ceramic Matrix Composites (CMC) consist of ceramic materials reinforced with ceramic fibers. They offer exceptional heat and corrosion resistance, making them ideal for extreme environments like aerospace and defense sectors.
CMC materials are commonly found in jet engines, heat shields, and industrial furnaces due to their high thermal stability.
Classification of Composite Materials Based on Reinforcement Type
Reinforcement provides additional strength and stiffness to the matrix material. Here’s how composite materials are classified based on reinforcement type:
Fiber-Reinforced Composites
Fiber-reinforced composites (FRC) consist of strong fibers, such as glass, carbon, or aramid, embedded in a matrix material like polymer, metal, or ceramic. These fibers act as the primary load carriers, while the matrix binds them together, ensuring stress distribution and protection from environmental factors. Glass fibers offer cost-effectiveness and impact resistance, carbon fibers provide exceptional stiffness and lightweight strength, while aramid fibers, like Kevlar, excel in impact absorption and flexibility.
A key application of fiber-reinforced composites is FRP reinforcement (Fiber-Reinforced Polymer) in construction. FRP materials, commonly used for strengthening concrete structures like bridges, tunnels, and columns, are favored for their high strength-to-weight ratio, corrosion resistance, and long-term durability. Unlike steel reinforcements, FRP does not rust or weaken over time, making it ideal for harsh environments and reducing maintenance costs while extending the lifespan of infrastructure.
Particulate Reinforced Composites
Particulate reinforced composites are materials where small particles, such as ceramics, metal oxides, or carbides, are uniformly dispersed within a matrix material like polymer, metal, or ceramic. These particles help enhance properties such as hardness, wear resistance, and compressive strength. The even distribution of particles throughout the matrix allows for consistent performance, making these composites ideal for applications requiring uniform load distribution and surface protection.
A common use of particulate reinforced composites is in wear-resistant coatings, brake pads, and cutting tools, where high durability and resistance to friction are essential. They offer a cost-effective alternative to fiber-reinforced composites for moderate load-bearing applications, as they provide excellent mechanical strength while being easier to manufacture. Their balance of affordability, strength, and wear resistance makes them popular in both the automotive and industrial sectors.
Structural Composites
Structural composites are advanced materials that combine multiple layers of composites or core materials to create strong, load-bearing structures. They are typically designed with a core material, such as foam or honeycomb, sandwiched between two thin, stiff composite face sheets. This layered structure enhances mechanical properties by distributing loads evenly across the material while maintaining a low weight. The combination of core and face materials results in excellent stiffness, impact resistance, and structural integrity, making them ideal for demanding applications.
A common example of structural composites is sandwich panels, widely used in the aerospace and marine industries. In aerospace, they are utilized for aircraft floors, fuselage sections, and wings, where both strength and weight reduction are critical for fuel efficiency and performance. In marine applications, they are often used in boat hulls and decks due to their ability to resist water absorption while offering excellent durability. Their balance of lightweight strength and design flexibility makes them suitable for large-scale components where long-term durability and performance are essential.
Advanced Classification of Composite Materials
Modern technologies have led to the development of advanced composite materials with enhanced properties. These materials are tailored for specialized applications where traditional composites may fall short.
Hybrid Composites
Hybrid composites combine two or more types of fibers, such as carbon and glass fibers, in a single matrix material. This results in a balance of properties, like improved impact resistance and cost efficiency.
They are often used in automotive components, sports equipment, and protective gear where a blend of performance and affordability is required.
Nano-Composites
Nano-composites involve the integration of nanoscale particles into the matrix, enhancing strength, thermal stability, and electrical conductivity.
These materials are commonly used in aerospace coatings, medical implants, and electronic components due to their enhanced mechanical and functional properties.
How to Choose the Right Classification of Composite Materials for Your Needs
Selecting the right classification of composite materials depends on the specific requirements of your project. Here are some factors to consider:
- Strength and Weight Requirements: For lightweight applications like aerospace, fiber-reinforced composites are ideal.
- Thermal Resistance: For high-heat environments, ceramic matrix composites offer superior performance.
- Corrosion Resistance: FRP reinforcement is excellent for outdoor structural applications, such as bridges and marine platforms.
- Cost Efficiency: Polymer matrix composites often balance cost and performance effectively.
When working with composite materials, using the correct vacuum consumables during the manufacturing process is crucial. These tools, including vacuum bags and release films, ensure proper resin flow and air removal during composite curing, leading to higher-quality results.
By understanding the classification of composite materials and their diverse applications, industries can make informed decisions, improving performance, sustainability, and long-term cost efficiency.